Siemens weighs in: Manufacturability starts with communication, and DFMA can help
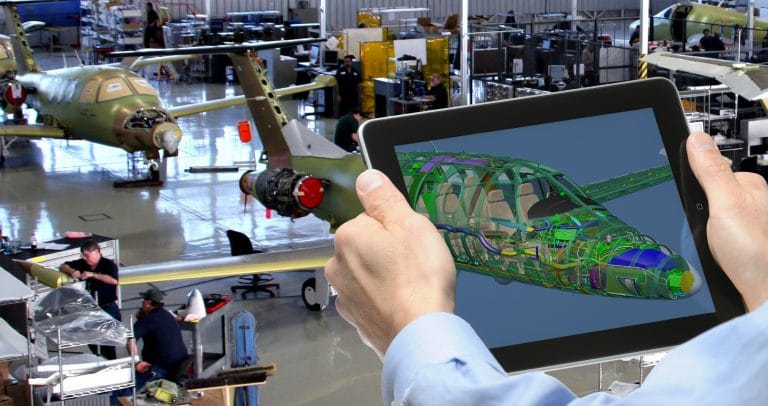
The online publication, AdvancedManufacturing.org, recently published an article about why controlling manufacturing costs and complexity start in design. Bruce Morey, contributing editor, states that,”Capturing and applying experience in a disciplined manner is vital, for both design engineers and their manufacturing counterparts.” The comprehensive story goes on in length about the need to design for manufacturing.
Mike Rouman, senior marketing manager for Siemens PLM Software, was able to weigh in on the subject and noted that advances in simulation tools and evolving standards in how information is being distributed have an impact on how designers incorporate Design for Manufacturing / Assembly (DFM/DFA). One such communications foundation is the emerging use of product manufacturing information, or PMI, attached directly to a CAD model.
Quoted from AdvancedManufacturing.org:
PMI is not a new concept. The idea is decades old and the enabling standards were developed at least 10 years ago. “What we are seeing now in our customer base is a real transition—mass adoption as people are moving to [PMI] and using a model with PMI attached across the enterprise,” he said, moving away from what he termed as drawing-centric workflows.
Why is this important for the implementation of DFMA? It provides not only a communication tool from the designer to the manufacturing process, but also allows employing other tools just as important for understanding manufacturability.
“For example, we have Monte Carlo-based techniques for setting tolerances—they can simulate thousands of variations in assembly configurations and tell you which ones will fail, where tolerances are actually too tight and how to relax them to make a cost-effective process,” he said. With PMI attached to CAD, not only can manufacturing processes like machining and fabrication be programmed, so can inspection programs and a host of other manufacturing-related processes. Other simulation tools that have come into their own are discrete event simulations, such as Tecnomatix Plant Simulation offered by Siemens.
“Approaching the problem from this perspective might not always impact design, but it could change the manufacturing process or system,” he said. By exploring options through a manufacturing simulation, fixturing could be adjusted or operations performed in a different sequence to get the lowest cost system rather than simply the lowest cost design. “Combining DFM tools with other simulation allows all those checks before you ever go into production,” he said.
CIMData comments about the importance of DFM in additive manufacturing:
So, almost 30 years after these concepts were introduced, what has been the general acceptance in industry? “I am still not seeing the level of acceptance I would expect for as long as it has been around,” said John MacKrell, chairman of CIMdata (Ann Arbor, MI). There are a few places where it is well received, such as automotive and aerospace, where either the volume or complexity of the manufacturing process makes it paramount to consider DFM in the engineering process.
“In other companies, I get mixed feelings about it; [acceptance] often depends on the engineer rather than DFM being supported] by a company process,” he said. Obviously, there is room for education. One area where DFM will be vital is additive manufacturing, MacKrell asserted. “While the basic principles of DFMA have not changed that much, additive requires both designing the part for the manufacturing process, and additive manufacturing enables things like reducing part count,” he said.
You can read the complete article online at AdvancedManufacturing.org
https://advancedmanufacturing.org/manufacturability-starts-with-communication-and-dfma-can-help/
The concept of digital twins, computerized replicas of a product and even its production system, is an emerging tool impacting Design for Manufacturing and Assembly.