Shorten time to market through efficient manufacturing process planning
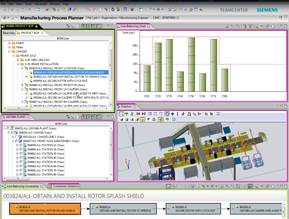
We’re all affected by the faster moving world and the changing practices and expectations that go along with it. Manufacturers are no exception. The challenges and competition they face come from diverse sources. These can include manufacturers worldwide who, for a variety of reasons, may be able to manufacture their products more inexpensively and quickly, to something as seemingly simple as customers’ expectations of receiving their product even months sooner. As a result, manufacturers are obligated to tackle these all-important issues of reducing time to market, meeting customer orders, and doing so economically.
And yet, the manufacturing field is a complex and difficult one. In the quest to get a product – like a train, plane or car – to market, there are countless issues that stretch from the initial conception and design phases, to prototyping, on to documentation and efficient manufacturing. It’s common for each phase of the process to pass through at least a couple of trial and error runs before the results are acceptable. Because of this complexity manufacturers would benefit greatly if a lot of the gross approximation and uncertainty were removed from the equation. Teamcenter Manufacturing achieves just that, by providing a unified and comprehensive method for managing manufacturing – from the early design stages, through manufacturing process planning, and ultimately execution. But it’s the outcomes resulting from these capabilities that lead to business transformations for manufacturers and quicker time to market.
For example:
- For Duqueine Group, an aerospace and defense manufacturer, a more than 50 percent reduction in time to market – from 30 months to 14 months – resulted when all technical and design data were re-located to a single repository and linked to ERP, ensuring data consistency and integrity that was always reflected in the most recent versions, with the resources on hand to meet requirements.
- For Perkins Engines, an engine manufacturer, using virtual process planning, adopted by manufacturing, engineering, operations, service and aftermarket divisions, enabled a 300 percent increase in manufacturing process planning capacity – with the ability to execute planning for more than 100 unique customer configurations. Perkins made a business decision that for all new products, Teamcenter would be the single, safe source of all information.
- For Volvo Cars, an automotive manufacturer, product developers and manufacturing engineers collaborate using the same engineering environment, enabling them to work with the latest product data. Often up to 90 percent less time is needed to produce up-to-date engineering (process) documentation since they now automatically generate it directly from the system.
- For Siemens Rail Systems, a train manufacturer, dynamic 3D simulations of complex assembly scenarios reduced error and optimized assembly, making it simpler and possible in less time.
As Sammitr Motors Manufacturingput it, “Siemens PLM Software has been instrumental in helping us streamline our complex product design, engineering and manufacturing processes. Their innovative products have drastically boosted end-to-end efficiency and helped us maintain our reputation for consistently exceeding customer expectations.”
More information about Siemens PLM Software manufacturing process planning solutions can be read here:
http://www.plm.automation.siemens.com/en_us/products/tecnomatix/manufacturing-planning/