Optimizing design and eliminating production problems virtually
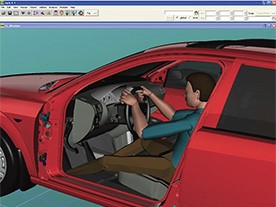
Customer success story summary: Comau
ComauFor over 60 years Italy- based Comau (Engineering, Injection Molds & Dies Business Unit) has been supplying quality engineering services and production tools mainly to the automotive industries.
Managing growing design and production complexity, from the need to reduce errors to the setting up of precise customer specifications according to strict schedules, requires absolutely flexible software solutions that are synchronized to allow the tight control of entire projects.
To deliver complex, quality products according to strict due dates, Comau aligning its production strategies product lifecycle management (PLM) software tools. These tools allow calculations and analysis in a virtual environment that fully substitutes the physical tests. Immediate feedback during the test processes, which directly and automatically affects the design work, enables the correction of errors before entering into production. Virtual processes have become indispensable to reach the market in the ever-faster times expected by customers.
Comau uses solutions from Siemens PLM Software to manage its design and production environment. Giuseppe Molina, Business Line, Chief Operating Officer, Comau explains, “Siemens PLM Software offers a range of tools to increase the integration of individuals and organizations. Using Siemens PLM Software technology, all the figures involved in product development (marketing, designer, draftsman, technicians) can use – throughout the phases of design, industrialization and production – a single digital model synchronized in a single environment.”
“What distinguishes a good vehicle is its re-elaboration and adaptation to new technologies in short times and without problems during the final phase of production,” he explains. “Besides a correct design, in fact, foreseeing a coherent assembly – one without interferences – is fundamental. Downstream interferences can decisively compromise the goodness and quality of the product. For this reason, anticipating eventual problems during the mounting or dismounting phases is an indispensable factor for a manufacturing company wanting to stay market competitive.”
“Besides NX software for design and Teamcenter software for product data management, we have implemented with success Teamcenter for lifecycle visualization, as well as Tecnomatix FactoryCAD for 3D factory layout and Tecnomatix Jack software for human modeling/simulation,” he says. “The Siemens PLM Software solutions allow a digital mockup to be created that manages all phases going from virtual assembly to process testing of models designed with heterogeneous CAD systems. Virtual assembly is less expensive and quicker in comparison with physical assembly. You have the opportunity to test that all the tolerances are respected. Not being able to foresee a little error in the mounting of the equipment can compromise the quality of a whole product.” Molina adds, “Through the use of these solutions it is possible to work in parallel across both product industrialization and design processes. Thanks to this parallel and continuous analysis, we can evaluate priorities and solve eventual problems that could arise during product development, thus assuring handmade deliverability.”
Read the complete Comau customer success story here.