Mechanical engineering specialist uses Siemens solutions to design complex mechanical constructions

Solid Edge and Tecnomatix enable Mechtop to obtain lucrative contracts for sophisticated conveyor systems
Mechanics in motion
Based in the north of Switzerland, Mechtop AG (Mechtop) takes a pioneering approach to custom machinery and plant construction. Founded in 1995 as a machinery maintenance firm, the company now designs and builds custom steel structures, tanks and apparatus as well as pipework and conveyor systems. Mechtop’s 55 design engineers, fitters and production employees cover the entire development and manufacturing process all the way to commissioning while also providing maintenance services along each plant’s lifecycle.
Mechtop’s motto “Mechanics in Motion” not only describes its dynamic, agile and forward-looking attitude towards mechanical engineering, it also stands for the company’s sophisticated conveyor technology.
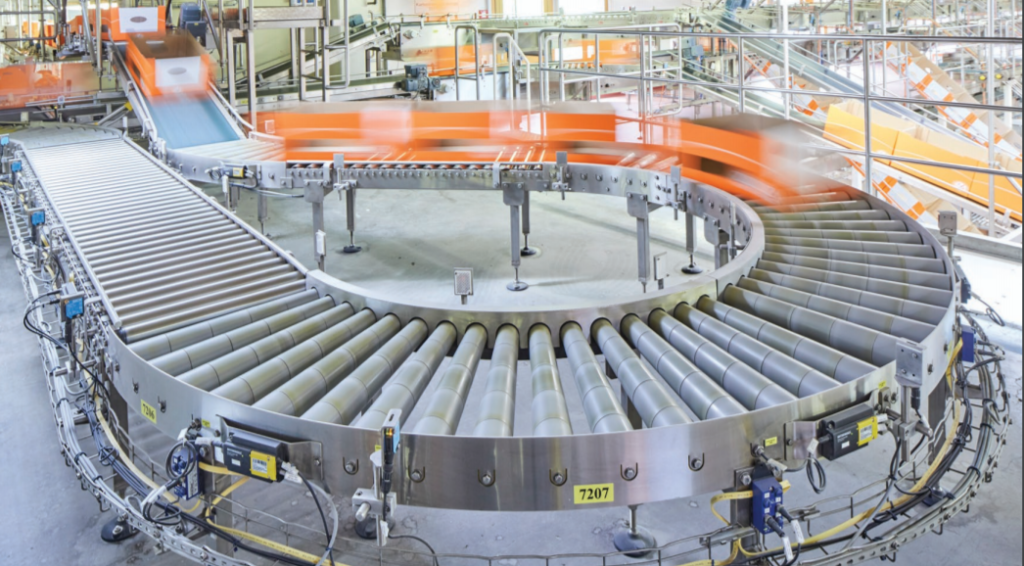
Developed over several decades by a company acquired in 2016, it has become an important pillar of Mechtop’s business. In a close dialogue with customers, eight project managers create conveyor solutions mainly for the food and beverage industry.
Solid Edge for complex plant design
For the computer-aided design (CAD) of the custom installations, Mechtop’s engineers use Solid Edge® software from Siemens Digital Industries Software. “This 3D CAD software with its supportive user interface is easy to learn; new colleagues require only minimal training,” says Jürg Bachmann, head of technology and production at Mechtop. “At the same time, it has everything we need to create and verify our large and often very complex designs, including powerful sheet metal and tubing capabilities.”
Commissioned by a major food retail chain operator, Mechtop engineers used Solid Edge to design a custom conveyor system as part of a container cleaning plant. Centered around an inline cleaning system, it includes a stacker and a destacker for the food crates as well as a buffer zone to accommodate containers that are not required immediately after cleaning. The installation is designed to clean 2,000 boxes per hour. This means that it has a throughput of one box every 1.8 seconds. It also means that a 30-minute standstill would result in an intolerable container shortage in some of the stores the following day.
In the light of these framework conditions, it came as no surprise that the customers required a proof of concept before actually awarding a $3 million contract to Mechtop. “Using Solid Edge, we can show the customer a 3D model,” says Bachmann. “To convince a customer that the plant will fulfill the requirements, it takes a digital twin of the plant, complete with its temporal behavior.”

Tecnomatix for material flow optimization
In search of the appropriate software solution, Bachmann turned to Cytrus, a Siemens Digital Industries Software solution partner with three locations in Switzerland, one each in the German, French and Italian speaking parts of the country. Cytrus suggested using Plant Simulation, a digital manufacturing solution in Siemens’ Tecnomatix® portfolio, to build digital twins of logistics systems and their processes.
Robin Vornholt is a senior consultant at Cytrus, the only Siemens Smart Expert in Switzerland for this software. He says, “Tecnomatix Plant Simulation allows users to model, simulate, explore and optimize systems and processes involving material flow. Using discrete event simulation and statistical analysis, these digital representations enable material flow and resource utilization analysis and optimization well in advance of production execution.”
After receiving a four-day training from Cytrus, three Mechtop engineers completed a simulation model of the conveyor system of the container cleaning plant. “We had to meet an extremely tight schedule,” says Bachmann. “The most challenging part was providing proof of concept for the destacker within two weeks.”
The simulation results convinced the customer that the plant as proposed by Mechtop was going to fulfill all requirements. After receiving approval, the three engineers developed the digital twin of the cleaning plant in less than two months.
Supported by the Cytrus Plant Simulation experts, they built a library of models of their conveyor components. To create the models, they imported data from Solid Edge using the JT™ data format from Siemens. They also used timing characteristics information previously stored in spreadsheets.
“Plant Simulation has an object-oriented, hierarchical structure,” says Bachmann. “Using this software makes creating 2D/3D models of complex dynamic layouts fast and intuitive.”
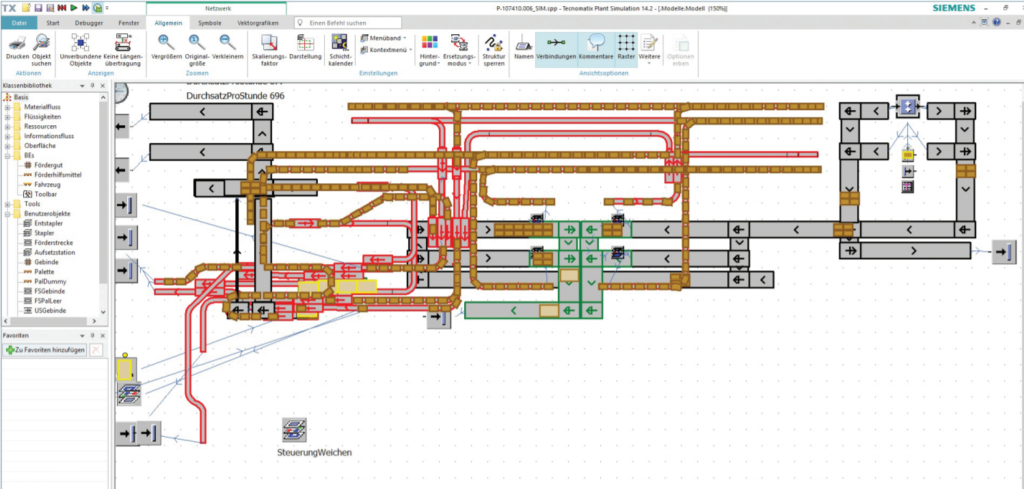
Early design validation
Plant Simulation also enables Mechtop to meaningfully illustrate the simulation results using diagrams as well as interactive 2D/3D real-time visualization. They use this capability of the software to optimize system parameters and for planning purposes. The main use of the comprehensive simulation and visualization tools in Plant Simulation, however, is in the sales process, where they enable sales to create powerful presentations using valid design information.
“Plant Simulation allows project validation in the earliest project phases,” says Bachmann. “With simulation-based material flow optimization, we can offer our customers added value and make sure their project is successful.”
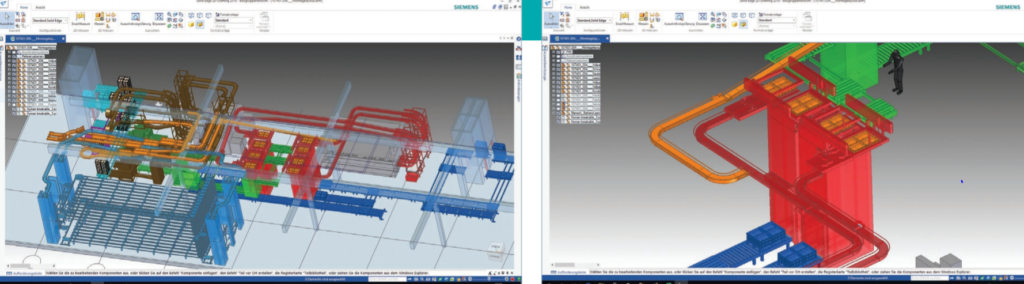