Industrial Robot Simulation Software for Offline Programming
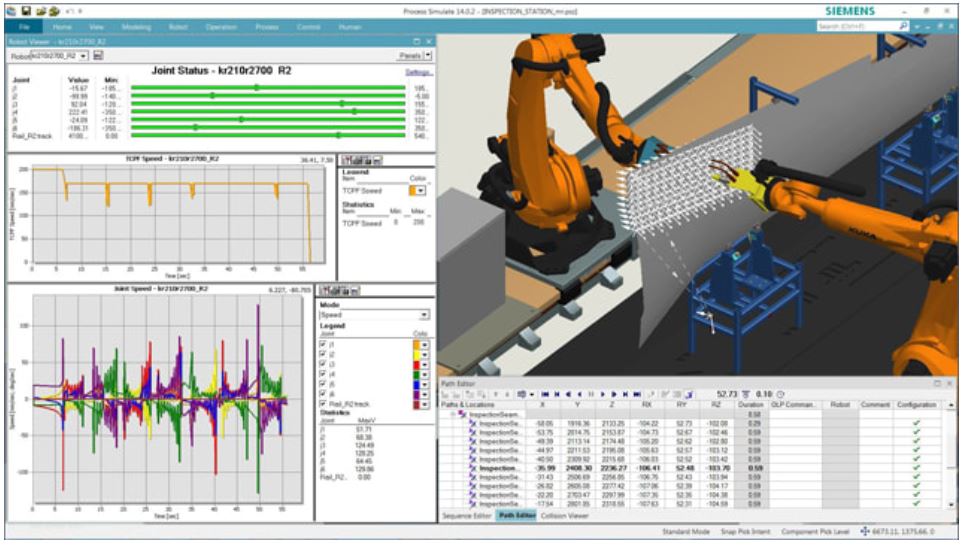
The digital publication, Engineering.com, recently published a story featuring the What, Why and How of Industrial Robot Simulation Software for Offline Programming, in which Siemens’ Senior Marketing Manager, Mike Rouman, was able to weigh on the use of robot simulation software and describe the key capabilities in Siemens Process Simulate.
We’ve captured a few of Mike’s important comments in this blog. To read the complete story, follow this link to Engineering.com.
When using simulation software to program a robot, it’s important to remember that no simulation will accurately represent what will really happen when you run the program with the real robot. The movement of cables and hoses is not simulated by most software environments, so it’s possible that the programmed motion may snag or stretch cables, causing failure.
“I think that dynamics and physics modeling will also help make simulations more accurate,” said Rouman. “We have started to do some of that in the design of machines in our software, but in terms of simulation, I still think there’s some ground to cover. If you think about when a robot moves at high speed with a high payload, when it stops, it’s not going to just stop. It’s going to settle and there’ll be some movement and so on. With those kinds of fine adjustments and things, we have to make some assumptions. I think that in the future we won’t have to make so many assumptions. We’ll be able to more closely match what the real robot will do.”
One factor that contributes to better simulation is a shift from time-based simulation to event-based simulation. “In the past, simulation developers would have to sort of guess the amount of time a given event would take,” explained Rouman. “But that’s not really how these robotics systems work. They work in an event-based mode, and if we can simulate the system the way it’s actually operating on the floor by having these events starting and stopping and coordinating with one another, we’ll also achieve a higher level of accuracy between the simulation and the real world execution of that program model on the shop floor.”
Siemens Process Simulate
If you’re familiar with robotic simulation software from Siemens, you may already be familiar with Robcad, the company’s legacy OLP tool. According to Rouman, Robcad is still supported and in use today. Process Simulate, however, is the newer product. In addition, Siemens NX has capability for robotic machining.
One of the features of Process Simulate is that it can connect to Siemens Teamcenter, a PLM data repository. This allows users to tie their robot simulation into the entire product lifecycle management system, along with other types of manufacturing data, including designs and processes. However, this connection is not required to run Process Simulate for robot simulation and programming.
According to Rouman, when choosing a simulation solution that includes OLP, it’s important to look for dedicated process tools. “For example, if someone is looking to do spraying or painting with a robot and they want to use a general-purpose tool, they may struggle,” said Rouman. “If they find a solution that has dedicated tools for that particular process, they’re likely to have a much higher rate of success.” Process Simulate, for example, enables users to set parameters of a spray tool within the software, and deposition of the spray is shown graphically in the simulation.
Cost
Process Simulate is currently available as a perpetual license, with options for single seats, seats shared across a network, or other deployments. According to Rouman, some customers prefer subscription-based software-as-a-service (SaaS) access, which is available in some cases.