Commissioning Your Plant Material Flow: Part II – Virtual Commissioning
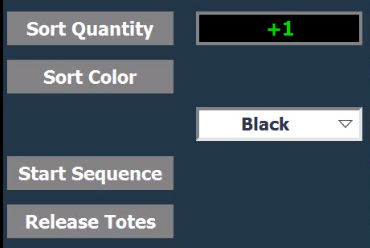
By Noam Ribon, Senior Consultant, Siemens PLM Software
In my first blog, I suggested that Tecnomatix Plant Simulation software is a foundational component of the broader Production Digital Twin architecture. I felt it was an essential building block in understanding why Digital Twins are important, and what are their required characteristics, in order for them to fulfil their purpose.
In this blog, we will dive into one of the hottest topics of the Production Digital Twin: Virtual Commissioning of your Plant Material Flow. For an overview on Virtual Commissioning, please check out our earlier blog. Without further ado, let’s get right into it.
Virtual Commissioning Setup
As the diagram depicts, what is being tested, is how well our controls strategy, control sequence, and Human-Machine Interface (HMI), will work in our production environment.
The left block lists the 3 control components tested: the PLC program itself, the HMI routine, and, the HMI layout.
The central block represents the hardware that would control the equipment in Production. Virtual Commissioning can be performed with Hardware in the Loop (HiL), Software in the Loop (SiL – for example a virtual PLC, such as Siemens PLCSIMAdvanced, or a virtual HMI) or a combination of HiL and SiL. We see a growing use of SiL, all the way to a completely virtual setup.
The block on the right, is for the equipment, as represented by the Digital Twin. The Digital Twin is what transforms Commissioning into Virtual Commissioning. A closer look at the blue box at the center of the right block (duplicated below) make it clear why the Digital Twin must have the characteristics we discussed in Part I of this blog series.
Connecting HiL or SiL to the Digital Twin
In general, connectivity to the HiL/SiL is achieved through an integrated OPC UA interface. When Siemens SiL is in the loop, connectivity can also be achieved through shared memory, avoiding the OPC UA server intermediary.
Mapping of the signals, (‘tags’ in controls nomenclature) is then applied, such that tags have their corresponding items or objects in the Digital Twin. Below are examples of PLC input tags, as organized in the Siemens TIA Portal application: a network view, and a data block view. Underneath those two images is an example of the mapping of these tags to objects of the Digital Twin: the mapping list, and one corresponding digital Twin object, in our case, a photoeye.
Virtual Commissioning in Action (video)
In this case we wanted to test the addition of a sorting and diversion functionality, specifically whether buttons and displays added to the HMI, and the logic behind them, would perform as expected when controlling production on the floor. We used a virtual HMI, a virtual PLC (SiL), and the Plant Simulation Digital Twin. We used Siemens TIA Portal to program the PLC. You can see the Physical Twin briefly at the start of the video.
In essence, we added logic that would identify a number of totes and specific color required, and allow a request to divert them from the circulating loop to the conveyor at the bottom of the movie (‘Start Sequence’ button). Once the totes are diverted, and after being emptied at the assembly station, a second HMI button (‘Release Totes’) would be pressed to release the empty totes and send them back to circulation.
In our movie, the buttons are activated, and the Digital Twin visually indicates that the PLC program is working as expected.
Practical Advice
So now we are ready to practice Virtual Commissioning. To help with your first model, I thought I would share some practical advice.
To start, model the Digital Twin so it reflects your physical production. The difference with Virtual Commissioning would be, that instead of Plant Simulation deciding on the logic of the simulation, the PLC, connected through OPC UA, for example, will control the model’s behavior.
Driving the model with a PLC means that Plant Simulation receives its triggers from the PLC (Output), and sends its objects status to the PLC tags (Input):
Output: A model driven by the Plant Simulation engine, might allow a container on a conveyor as soon as it becomes available. A PLC driven model will check if a User-defined Attribute is equal ‘true’ before allowing the container on the conveyor. The ‘true’ (1) or ‘false’ (0) state of the User-defined Attribute is determined by the PLC Output.
Input: A PLC Input is set to 1 or 0 by the status of the Digital Twin representation of its physical twin object, for example a photoeye. A PLC connected to Plant Simulation will receive the Plant Simulation photoeye object status (blocked = 1 or clear = 0). For example, when a container passes across the photoeye, thus blocking it and setting its status to 1, Plant Simulation will change the value of the corresponding PLC tag to 1.
In Summary
As I wrote in Part 1, Plant Simulation software creates behavioral and visual Digital Twins in an efficient and productive manner. Through its object orientation, hierarchy and inheritance these models remain clear, concise and predictable throughout a product’s life cycle.
In this blog, I leveraged that capability of creating an accurate Digital Twin to test control programs that are intended to run the ‘Physical Twin’ on the production floor.
It is not hard to imagine how that same Digital Twin can be leveraged to hone MES (Manufacturing Execution Screens) routines in a similar way, using the Digital Twin to play various production scenarios.
Perhaps even more exciting is the new world opening up with MindSphere Apps, reading in IIoT and continuously calibrating the Digital Twin to reflect in near real time the behavior of its Physical Twin.
Having the Digital Twin calibrated with IIoT from a MindSphere App, reflecting, for example, changes sensed in equipment today, will allow me to anticipate how my production will run tomorrow taking into account the impact of the changes I sensed. Assume, just for this discussion, that the changes will gradually cause a gradual drop from 99.99% efficiency to 99.5%, over the next 5 days. The calibrated Plant Simulation Digital Twin will be able predict that today based on the IIoT just received.
In a world where the only margin of play remaining to one-up the competition may be by maintaining efficiency at 99.99%, such observations today, can help me engineer the corrective steps, test them on the Digital Twin, and confidently make the necessary adjustments to maintain my efficiency at 99.99%, avoiding altogether the gradual, and perhaps costly drop to 99.5%.
Exciting. That perhaps deserves a blog of its own.
If you learned something and enjoyed this post, please leave a comment below.
Read part one of this blog series here.