Achieving the data-driven, lights-out factory of the future
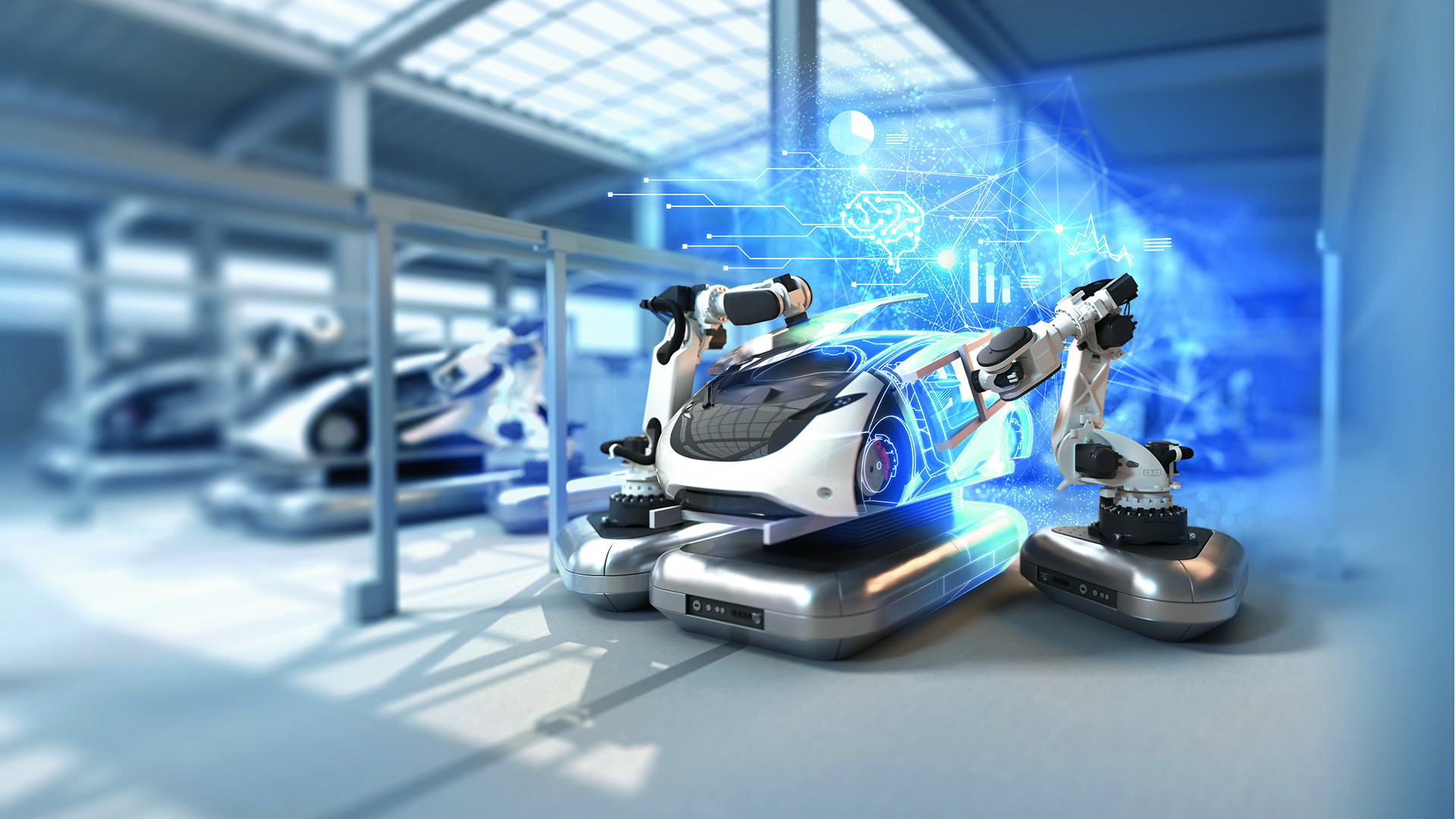
In our newly issued white paper, learn how you can reimagine factory floor operations with digital manufacturing for greater agility, resilience, and sustainability
“How do we get there from here?” When this question is asked, it often elicits two contrasting emotions: excitement and apprehension. In the question’s context, “there” has become an achievable aspiration, a happily anticipated capstone. However, if one is “here,” the path to “there” may be obscure and potentially fraught with difficulties.
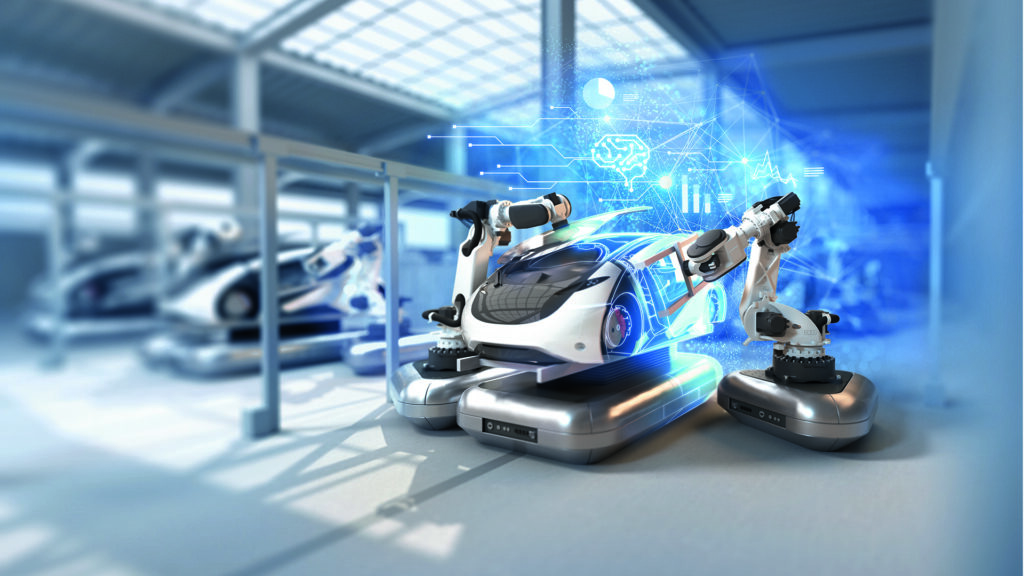
At Siemens Digital Industries Software, we sense both these emotions in those whose job it is to bring new efficiencies to their factories and to impart greater quality in their products. On the one hand, many manufacturers are inspired by the recent success of a few lights-out factories – facilities that can literally operate in the dark because there are no humans on the shop floor. Also called dark factories, these operations enjoy the high efficiencies one might expect of fully automated processes, as well as the boost in quality brought about by machine precision. The most well-known lights-out factory may be the FANUC factory in Japan, where robots are building robots and no human workers are needed onsite reportedly for a month or more. This success raises speculation that a completely self-sufficient factory may be on the horizon – a facility for which placing orders and receiving finished products comprise the only human interactions necessary. Exciting possibilities!
On the other hand, it’s hard for many manufacturers to look around an existing facility and imagine that it could one day be transformed into a factory of the future – whether lights-out or otherwise data-intensive – to reach new production efficiencies and quality of output. In some cases, bulldozing and starting from scratch may seem more realistic than transitioning the existing operation. But a step-by-step transition is precisely the achievable path forward that we at Siemens are helping our customers realize. Here is an overview of the approach we recommend for reimagining the factory floor.
Data sharing and manufacturing insights
As soon as a manufacturing company employs digital tools of any kind – from CAD/CAM, PLM and simulation systems before production through to sensors at the end of the manufacturing line – it begins to generate data, and lots of it. Today’s automotive plant might generate 20 gigabytes (or more) of data each day. Yet most companies today tap only a small percentage of this data to gain insights into what’s happening on the production floor.
Reasons for this are twofold. First, the data is unstructured. To turn big data into actionable smart data, manufacturers need it to be aggregated and contextualized. This structure connects data points with their meaning, so that digital tools can be used to detect trends and identify problem areas. Insights like areas of high downtime for a specific machine, too many operator errors, product build or supply issues, long lead times due to operator-intensive monotonous work, or an overabundance of non-value add activities become visible when manufacturing data is harnessed, organized, and evaluated.
The second reason manufacturing data is not being used to its full potential is isolation. In many factories, various departments work on systems that don’t “talk” to each other. This means, for example, that a quality issue detected in a work-in-progress (WIP) on the factory floor is difficult to connect to a variation in the properties of an incoming component or raw material that may have caused the WIP problem.
To advance toward data-driven manufacturing, digital tools may be employed to break down these data silos, one by one, so that a company gains manufacturing insights by analyzing data from multiple departments. Eventually, digital manufacturing tools will generate these insights across the manufacturing enterprise.
So, the journey to lights-out and other high-efficiency production schemes begins with something already present in your manufacturing operation: your data. If you adopt digital tools capable of organizing, sanitizing, and effectively interpreting existing data, you will have taken a big step toward tomorrow’s agile, resilient, and sustainable data-driven manufacturing.
The data-driven manufacturing culture
We have so far suggested implementation of digital tools and technologies, but tools are only as effective as your team makes them. This means overcoming a culture in which employees segregate by function and rely on tribal knowledge to get their tasks done. This culture must be replaced with an ecosystem in which sharing interpreted data across domains, by domain experts, is the norm.
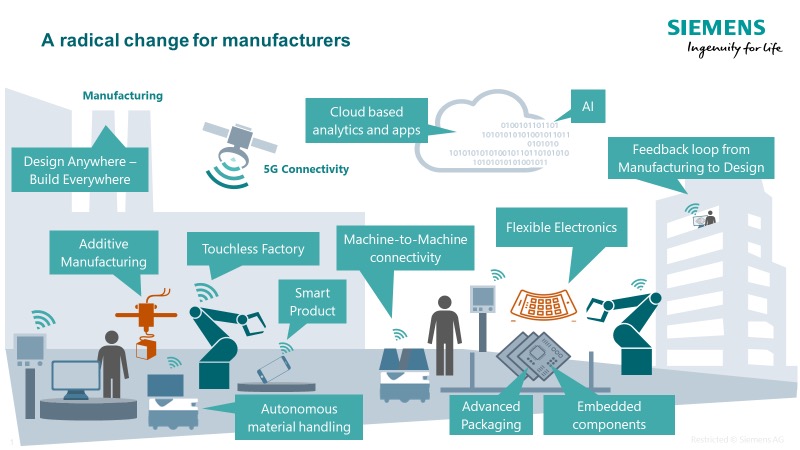
The full value of your digital investment is supported by such a cultural shift; and the inverse is true, too: your digital tools support the cultural shift. What we mean is that today’s digital systems are designed to appropriately filter and tailor shared information so that it provides role-specific access and insights. For example, while your planners need access to information from all production lines and facilities, the supervisor of a particular manufacturing floor is best served with access to planning data pertinent to that floor only. As your employees develop the habit of seeking cross-departmental insights, your digital system ensures information efficiency for these users.
By sharing interpreted data, your entire manufacturing team will be empowered to identify areas of inefficiency and their potential root causes. As the team diagnoses manufacturing processes and equipment that display a high likelihood of bottlenecks, downtime, errors and associated corrective measures, long lead times or other inefficiencies, you will now be in a position to pinpoint areas that would benefit from increased autonomy in production.
The lights-sparse approach
While a handful of manufacturing efforts lend themselves to a complete transition to the lights-out factory, more often manufacturers gain the benefits of data-driven manufacturing by converting a few processes within their facilities to run as lights-out operations. We call such manufacturing facilities “lights-sparse factories.” They intersperse lights-out operations among conventional production processes. By implementing lights-out manufacturing processes incrementally, these manufacturers gain efficiencies and quality without having to undergo a complete transformation of their factory floors.
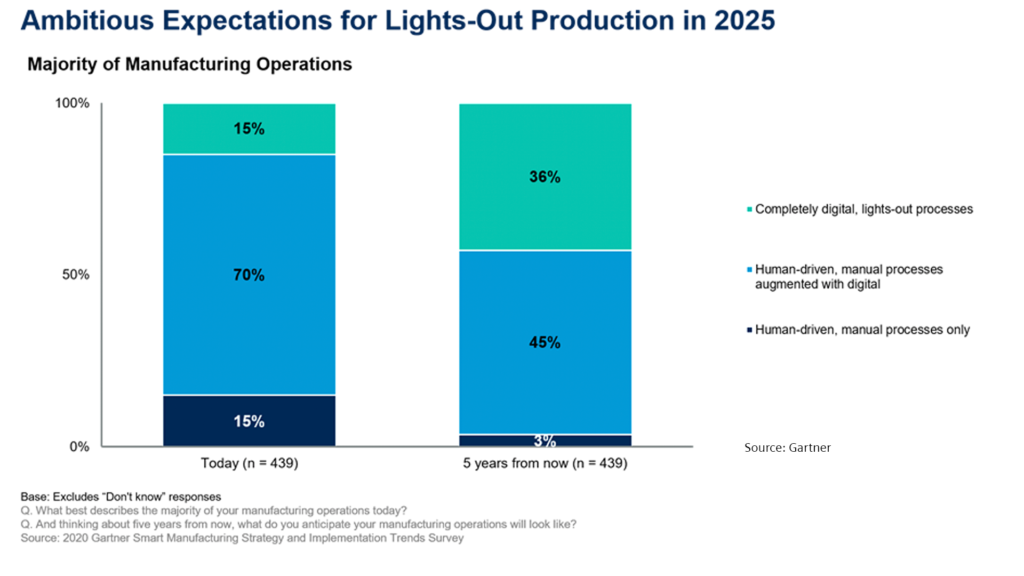
As your company uncovers opportunities to implement high-efficiency data-driven manufacturing areas within your production lines, a central tool for this implementation is the digital twin – an interactive, virtual representation of a physical product or process. As lights-sparse conversion projects are undertaken, the digital twin enables your engineers to explore alternative approaches and what-if scenarios before you take the plunge with major capital investments. Digital manufacturing tools and the digital twin are designed to replicate autonomous processes in the virtual realm, where they can be optimized prior to deployment. These processes and associated automation can be simulated, evaluated, and commissioned virtually, eliminating bugs and accelerating changeover to each new data-driven manufacturing operation.
Conclusion
Digital manufacturing tools along with the culture change to a data-driven manufacturing ethos set the stage for the next steps in your digitalization journey. First, by implementing lights-out automation in an identified manufacturing area, your facility earns designation as a “lights-sparse factory.” More importantly, you quickly realize higher efficiencies and quality in these areas. Next, your digital manufacturing tools continue to deliver new data insights and identify new opportunities for data-driven efficiency gains. Incorporating additional automation, you also enrich the facility’s digital twin, ultimately creating a closed loop of insights and improvements.
For your specific manufacturing enterprise, “there” may or may not be a full lights-out factory. But for any manufacturer, getting to new efficiencies and quality from “here” is realistic. And exciting.
—–
> Download and read now.
—–