From factory floor to designing new facilities: how Plant Simulation became part of Dexcom’s DNA
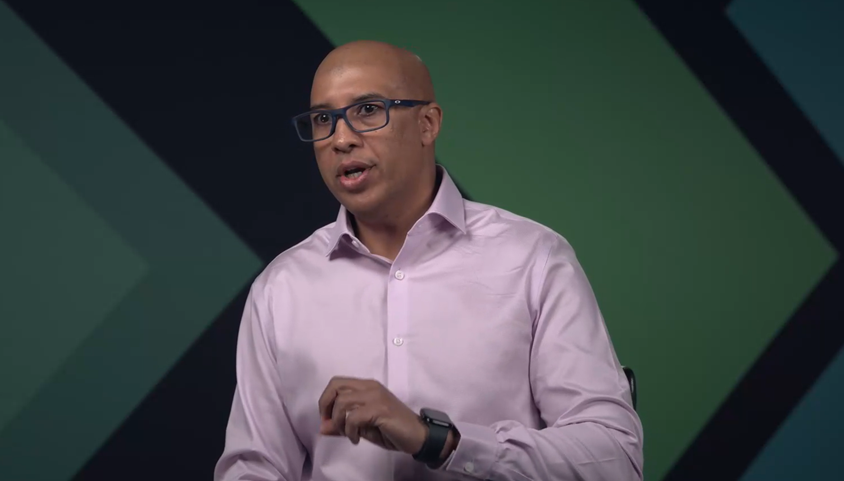
From production line to layout design, explore how a medical technology pioneer for diabetes management and continuous glucose monitoring (CGM) optimizes factory operations and boosts productivity with Siemens Plant Simulation.
Dexcom is an emerging medical technology pioneer for diabetes management headquartered in San Diego, California specializing in the development and production of continuous glucose monitoring (CGM) systems. These devices are critical for helping patients monitor their glucose levels in real-time, offering a less invasive alternative to traditional blood glucose meters. Dexcom’s newest device, Dexcom G7, effortlessly helps its users track glucose levels, allowing them to make smarter decisions about food and activity in the moment and to take better control of their diabetes. With the launch of their latest diabetes management device, Dexcom continues to push the boundaries of innovation, ensuring smaller, more effective, and user-friendly products.
In the face of rising demand for Dexcom’s innovative continuous glucose monitoring devices, the medical technology leader needed to scale their operations while maintaining efficiency, safety, and cost-effectiveness. In order to scale operations, it was paramount Dexcom keeps customer experience at the forefront to continually advance the product while ensuring affordability for broader accessibility.
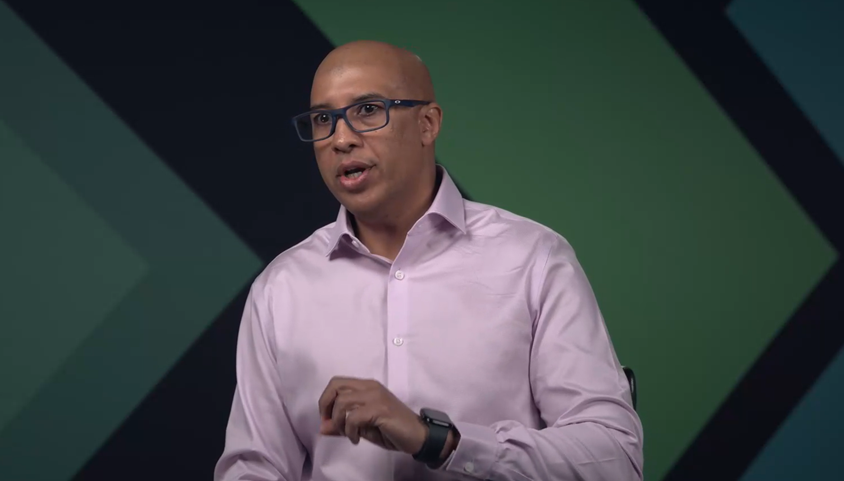
That’s why Dexcom adopted Plant Simulation. We’re making it part of the Dexcom DNA, so it supports our decision-making process. That way, it allows us to keep continuously advancing our product while we rapidly grow so we can optimize our operations, while increasing our productivity at a lower cost.”
Mohamed Elsayed, Industrial Engineering Manager – Modeling & Simulation, Dexcom
To help address these challenges, Dexcom embraced factory simulation technology, specifically Siemens Plant Simulation, to help drive quantitative decisions. The medical technology organization dedicated a specialized team to digitally replicate their factory sites to optimize production processes. By leveraging Siemens Plant Simulation, Dexcom can model, analyze, and optimize their operations in a virtual environment before making physical changes. This approach not only enhanced safety and productivity but also enabled them to maximize resource utilization, ultimately reducing costs and increasing product accessibility. As a result, Dexcom achieved a more streamlined and effective production process, better positioning themselves to meet the growing needs of their customers while driving innovation in diabetes management.
Meeting industry needs while maintaining efficiency and accessibility
With the increasing demand for its continuous glucose monitoring (CGM) devices, Dexcom needed to scale their production while maintaining prioritizing efficiency and safety. As Dexcom expanded globally, the organization needed a robust solution to optimize their operations, from plant layouts to logistics processes. To tackle these challenges, Dexcom adopted Siemens Plant Simulation, allowing them to model, simulate, visualize, and analyze their production systems and logistics processes, ensuring optimized material flow and resource utilization across all levels of plant planning.
From enhancing production line efficiencies to using the factory simulation technology for the construction of new sites, explore the different Plant Simulation use cases.
Use Case 1: Enhancing Production Line Efficiency
A most commonly known use case for Plant Simulation is leveraging the software on the factory floor. Dexcom used the factory simulation software to optimize its production lines, allowing them to model various scenarios and production flows. By simulating different layouts and workflows, they identified bottlenecks and optimized resource allocation, significantly increasing production throughput. This also enabled Dexcom to predict the impact of introducing new products on existing lines, ensuring a smooth and efficient transition.

Use Case 2: Optimizing Facility Layout and Safety
A unique use case of Dexcom’s Plant Simulation implementation was to improve the parking lot and overall safety at their facilities. By modeling current layouts and simulating various scenarios, Dexcom identified the most efficient parking configurations and traffic flows, reducing the time employees spent searching for parking spots and improving overall safety by minimizing traffic congestion. They also used the simulation to stagger employee arrivals, reducing peak-time traffic and enhancing safety.
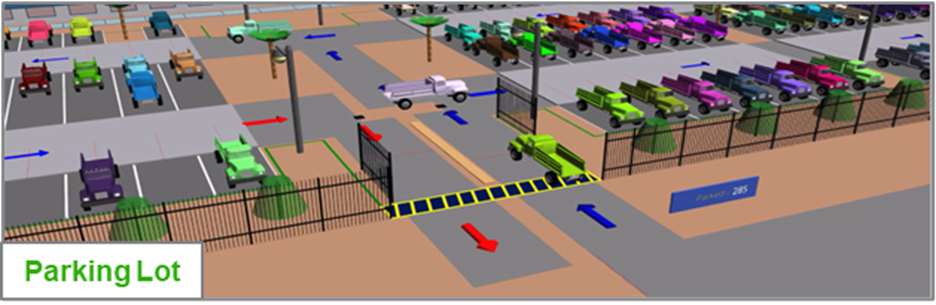
Use Case 3: Designing a New Manufacturing Site
As Dexcom continues to expand globally, the medical technology leader uses Plant Simulation for designing their factory site even before construction begins. When recently designing a new factory site, Dexcom utilized Plant Simulation to create an optimized layout. The simulation helped model emergency scenarios, such as fire drills, ensuring safe and efficient evacuation routes. This proactive approach allowed Dexcom to plan for safety and efficiency right from the design phase, reducing potential risks and ensuring compliance with safety regulations.
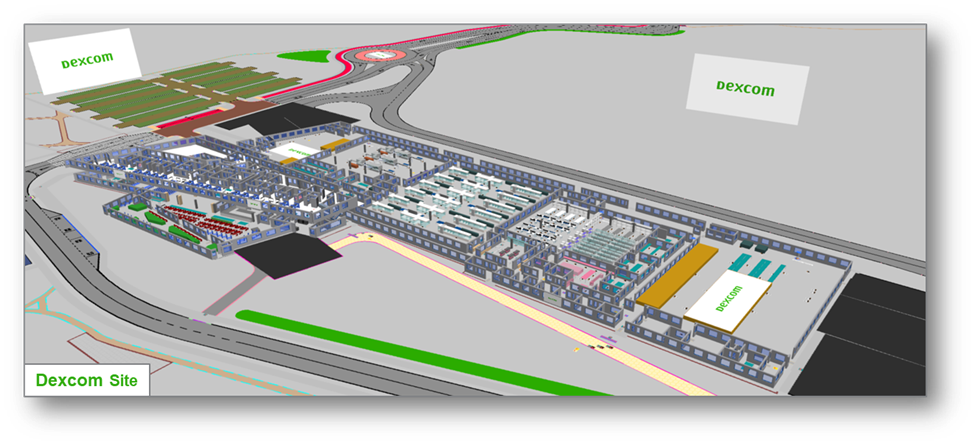
Making simulation part of the Dexcom DNA
Looking ahead, Dexcom plans to democratize factory simulation within the company, making it accessible to more employees, including those on the shop floor. The goal is to integrate simulation capabilities into everyday decision-making processes, allowing for real-time adjustments based on current resource availability and production demands. This initiative will help Dexcom continue to meet the growing demand for their products while maintaining efficiency and cost-effectiveness.
Through Siemens Plant Simulation, Dexcom has embedded a culture of continuous improvement and innovation within its operations. By leveraging simulation to optimize facility layouts, enhance safety, and streamline production, Dexcom is well-positioned to meet future challenges and continue providing life-changing products to their customers. Simulation has truly become a part of Dexcom’s DNA, driving better decision-making and supporting their mission to improve the lives of people with diabetes worldwide.