Use Engineering Simulation to Verify Product Design
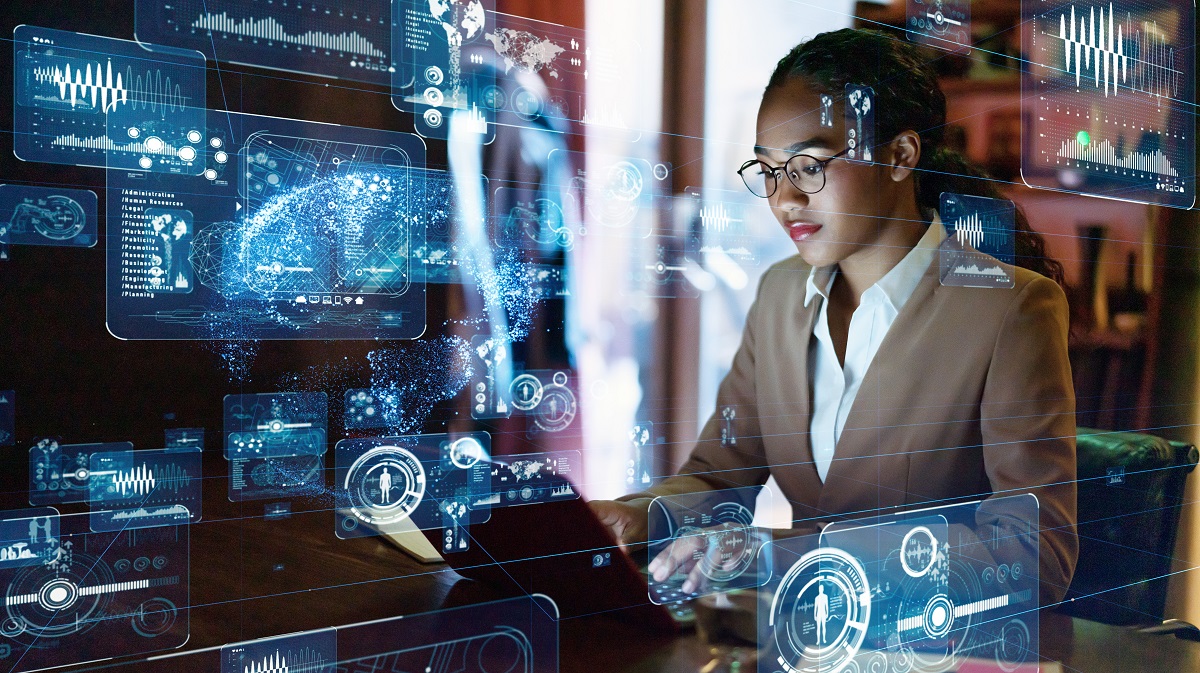
Optimizing your product design with engineering simulation
Engineering simulation for concept and design has been increasing exponentially as product complexity has continued to grow over the last three decades. Many processes have grown and evolved over this time to respond to simulation requests, and optimize the creation and reuse of these models. While 3D CAE modeling must wait for 3D CAD to be created, the 1D modeling space has moved further upstream in the design process. Many, but not all 1D modelers have also realized the value of following the Software Control Management (SCM) based development processes. But both the file-based and SCM-based processes can be improved by relating the model to the product requirement, function, or system element.
Ensuring all modeling activity is rooted in a valid request for work minimizes wasted effort and drives the ability for product design to have traceability to the models which were used to validate those designs. As we evaluate how this can impact your process efficiency, it is first prudent to share a view of the levels of maturity that we see in the marketplace:
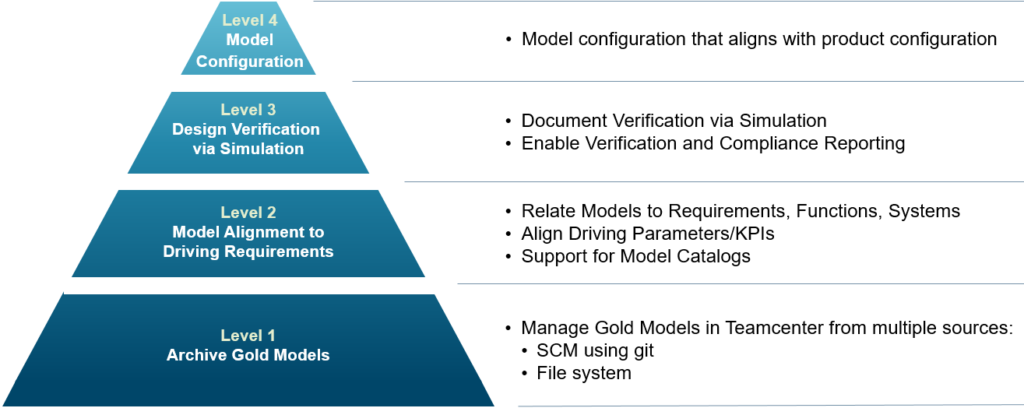
By looking at the breakdown shown in the image above, we can see that the focus is not on the actual model authoring process but on how effective that modeling activity can be related to the “reason for the model” in the first place. From a product alignment perspective, we see that there is a separation between the work-in-progress (WIP) activity for a given simulation and the product design that model is simulating.
Basic archival as the entry point
At Level 1, we recommend that the first step toward proper traceability is to make the models available within the PLM system. Even if you are not ready to relate the models to the driving product requirements, you will want to prepare for that next step by taking advantage of the archiving value of your PLM system. Whether your company is using a git-based process for model creation, or a file-based/shared-drive process Teamcenter can archive the initial version of the model and maintain updates to the model as later versions are ready.
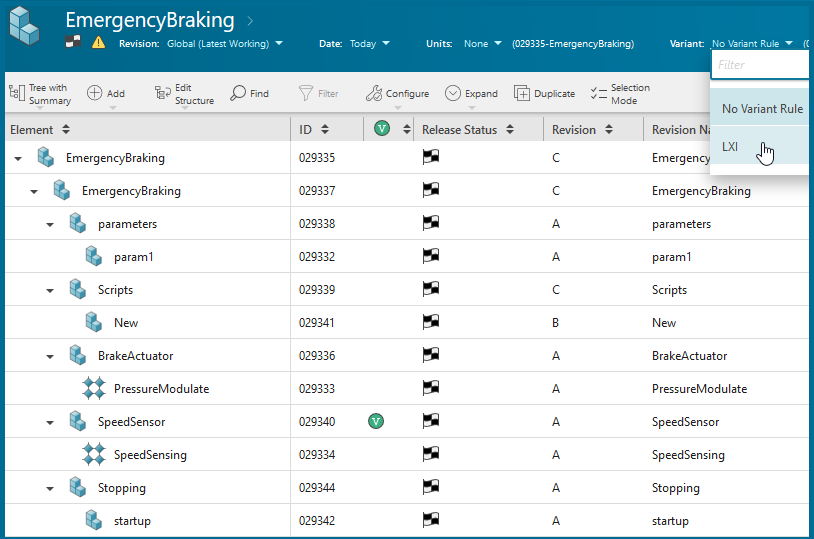
Teamcenter provides a WYSIWYG (What You See Is What You Get) folder-based display of each file in the model with version tracking. This way, both the simulation engineer and the consuming engineer can see exactly how the model will look on the file system. For companies who are still using a file-system-based approach for their models, instead of using a shared-drive system you can also use Teamcenter to provide that shared location for all of your model authors.
Building the Digital Thread for engineering simulation
When your company is ready to start managing requirements and/or functions and systems in Teamcenter, you will be able to directly relate your models to those product definitions. This provides clear traceability from the requirement, function, or system to the 1D model which is being used to simulate it.
Another layer of value here is to connect the engineering simulation model to those key parameters which are being evaluated either from the requirements or the functions/systems. This enables you to report how closely you are achieving your goals as defined by those parameters.
“Proof-of-Compliance” with verification and testing
The next level of improving your process is to track your testing and validation in Teamcenter. This is done by using the Test and Verification Management system. You can simply add the model to a test package and then execute the simulation with the Teamcenter Simulation automation. This process can initiate the test simulation directly from the test package and record the results. With this closed-loop testing process, you will have automatic proof-of-compliance because the simulation model and its results are directly related to the product definition. There are several test status reports available that show not only the goodness of the simulation and the status of the simulation and testing process against a plan.
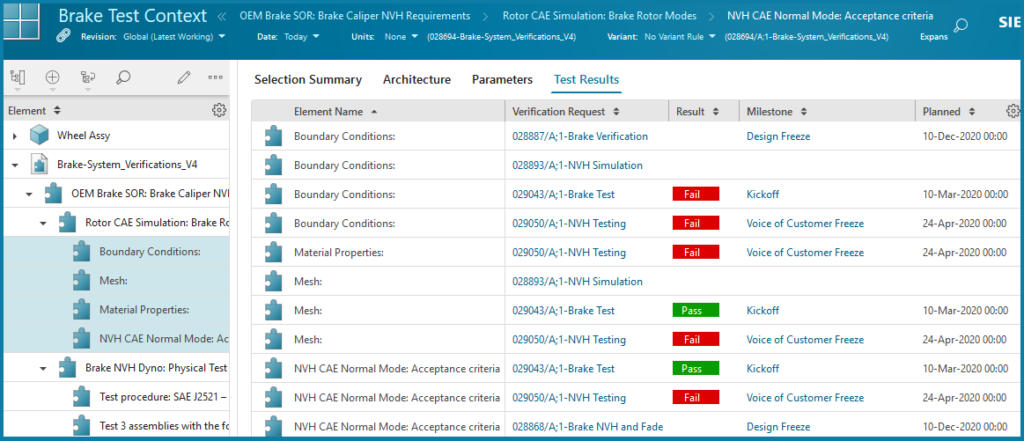
Are you ready for configuration?
Once a model is stored in Teamcenter, it can be configured so that only the right model components and the correct parameter values are associated together as a configured model. Then you can prove your designs across the multiple expected configurations your product must fulfill and have a more complete analysis for the readiness of your product.
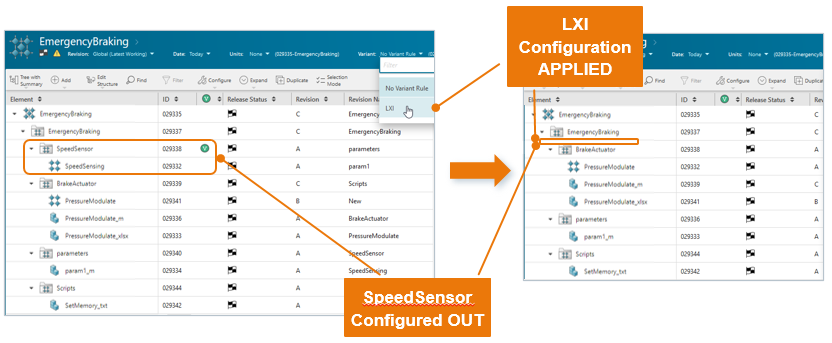
Realize your better, faster product delivery NOW!
Seeing the potential process improvement to your business is valuable. But it is just the first step in improving the functional value, innovation refresh rate, and quality of your product. The next step is evaluating honestly where you are on that process maturity level, and then taking actions to improve.
Siemens has the tools and process expertise to help you assess where you are and work with you to accelerate your business. Let us work with you to identify your next steps. Please reach out to your sales contact to learn more about this solution.
For additional information about early design simulation, model-based systems engineering (MBSE), and our simulation-based testing capabilities with Teamcenter Test and Verification Management, visit the MBSE webpage or read other MBSE blog posts.