Supplier Collaboration: Wake Up and Smell the Coffee!
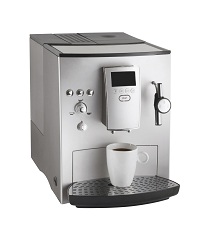

Supplier collaboration and coffee??? It must have been my early morning cup that got me thinking about this …
Remember the days when coffee makers didn’t have clocks, fancy timers, built in grinders, single serve options and come in multiple color choices?
Way back when coffee makers were simple, we either had to get creative to make it meet our needs, or buy additional items that would complement the coffee maker, a bean grinder for instance. I remember when I was a kid my dad installed a special switch in my parents’ bedroom so that he could flip on the power to the coffee maker when he woke up in the morning, having it freshly brewed by the time he was ready to leave for work. A nice example of the requirement (I want fresh coffee) driving the technology (I’ll install a switch).

Of course the desired approach to meet needs of both consumers and manufacturers today is to have requirements drive the technology. A common business requirement that I hear from manufacturers is to extend their PLM processes across the supply chain. In addition to addressing Model Based Enterprise (MBE) requirements and sharing 3D CAD files with their suppliers, manufacturers have a need to integrate their supply chain into various aspects of the product development process, including build to spec, COTS sourcing, contract manufacturing, product compliance, etc.
So, how do these requirements drive technology? And what’s the connection to supplier collaboration?
Typically, you’ll see one-off applications used to address individual use cases or a single collaboration dimension. For instance, some companies choose to use Dropbox for file sharing, but use other apps to address direct materials sourcing and supplier program management. This sounds a lot like the simple coffee maker example. Added technologies (integrations to one-off apps) are required to meet needs (extend their PLM processes across the supply chain).
It should be noted, addressing supplier collaboration requirements from both the OEM’s and the supplier’s perspective is no small task. The OEMs must take on the cumbersome challenge of shepherding their suppliers to ensure all the data and process information going out and coming in is correct. Both one- way and bi-directional supplier collaboration scenarios are important to consider.
The supplier has the challenge of keeping up with their customer’s requirements and learning their many processes and systems to stay compliant. From a supplier’s perspective, handling all the requirements and processes from one OEM can be a handful to manage. Add to that the complexity of multiple OEM interactions and you can imagine the struggle to keep everything straight.On top of all this, you have industry requirements, regulations and standards and one can easily discern that supplier integration solutions are definitely not “one size fits all.” Solutions must be easy to use and help to simplify the collaboration process for both the OEM and the supplier.
Best-in-class companies, or companies who continually meet their product cost, quality, revenue and launch date targets, agree that viewing suppliers as strategic partners in the design process is key to their success. Check out this infographic, created by analyst Aberdeen Group, to get an overview of the importance of supplier collaboration in order to improve your PLM processes.
Aberdeen Group – The Importance of Collaboration with Suppliers

As you can see from the infographic, the “Best in Class” companies who integrate their suppliers either tightly or loosely into their PLM processes have an advantage over companies that have a disconnected supply chain. Best in class companies can lower their risks by having a better chance to stay compliant with regulatory and industry directives, are more likely to understand supply chain costs and impacts early in the development process and are twice as likely to possess supply chain traceability. All of these factors are so important not only in reducing risk but also in meeting your corporate objectives. Product sustainability, for instance, is a high priority for most companies today. This article by Co.EXIST Want To Be More Sustainable? Look At Your Supply Chain points out the benefits of traceability in your supply chain, cautioning that what you don’t know can eventually hurt you.
Without dumping money, time and resources into integration projects to get supplier focused applications connected, you really don’t have a good answer to supplier collaboration (your modern coffee maker with the slick options). A single solution framework that covers multiple supplier use cases is really what’s needed here, and in the past this just didn’t exist – until now.
In my next several blog posts I will be highlighting different supplier collaboration use cases that can be addressed with Teamcenter; from design data exchange (DDE), to direct materials sourcing, supplier program management and processes like Production Part Approval Process (PPAP) and First Article of Inspection (FAI) – all using a single solution framework. Hopefully I can bring to light all of the benefits that can be realized by extending your PLM processes across your supply chain.
About the bloggers:
Kerri Doyle is a Teamcenter Product Marketing Manager for Siemens PLM Software.
Rohit Tangri is the Vice President of Teamcenter Product Management, Marketing and Business Development for Siemens PLM Software.
Comments