Avoid design and process risks with a comprehensive quality approach
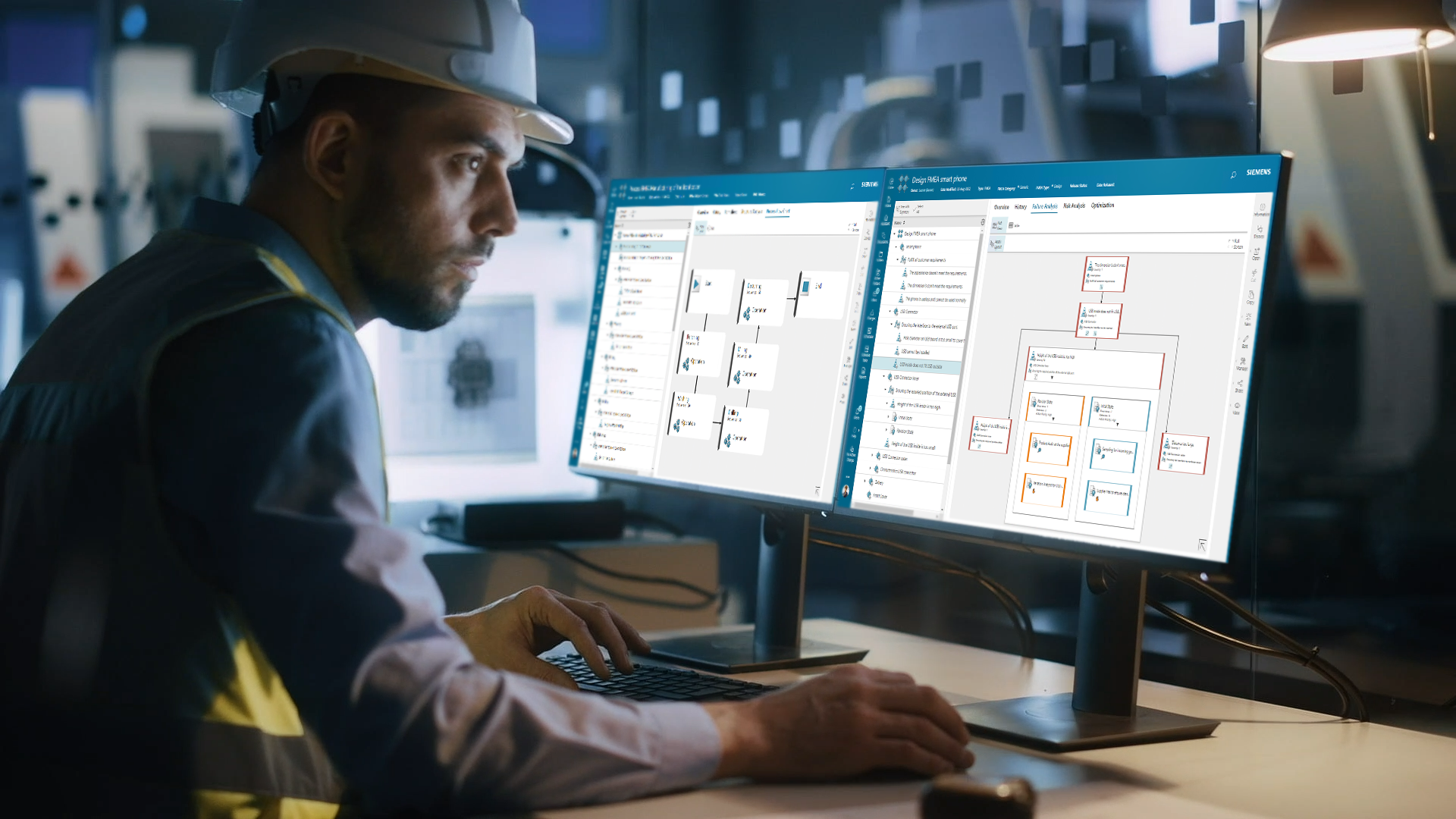
For today’s automotive industry, it is challenging yet vital to effectively assess design and process risks without a comprehensive quality approach.
How will a comprehensive quality approach help to reduce design and process risks? Stricter homologation and environmental regulations and increasing product complexity have put automotive manufacturers at greater risk for warranty issues and recalls than ever before. Making sure quality is addressed before the finished product rolls off the production line helps developers and manufacturers avoid changes in later production stages, saving money and helping produce high-quality results.
Failure mode and effects analysis (FMEA) is a critical preventive tool for effectively assessing design and process risks. Providing a powerful FMEA, a closed-loop quality solution enables developers and manufacturers to reduce both risks and costs. Quality management system (QMS) software, part of a comprehensive smart manufacturing approach, mitigates these risks with a closed-loop system that integrates product design, manufacturing, quality and the supply chain to safeguard compliance and product integrity.
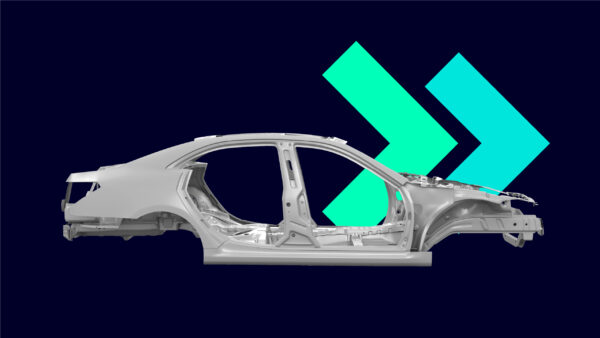
To provide a deep dive into FMEA and the value of a digital quality approach that enhances FMEA with direct access to engineering data, we asked one of our experts to offer his insights. Axel Eicker, Siemens senior product manager for Teamcenter Quality FMEA, has spent his entire career in quality management roles within the development departments of three different companies. He has focused throughout his career on modernization of FMEAs and the associated process and method optimizations. Today Axel brings his knowledge to Siemens with the goal of developing the best FMEA solution available on the market as an integrated part of product lifecycle management (PLM) and quality.
Why has it become important to detect design and process risks?
To remain competitive in the marketplace, automotive manufacturers must decrease product and operational costs while cultivating product quality. This requires a trade-off between cost and time while consistently meeting customer requirements. A new product starts its lifecycle as a requirement, so, it is fundamental to consider all customer expectations and then build quality into the design of both the product and the process. Quality requirements need to be fully addressed before the final product rolls off the production line. It helps to avoid deviations in later product phases, which can result in more expensive corrective measures and reduce the opportunity to deliver high-quality results. This practice is critical, since making the wrong or late decisions can have a severe negative impact on your business.
How does FMEA support automotive quality guidelines?
The quality standards and guidelines regulating the automotive industry require risk to be quantified and considered for all key processes and decisions. The ISO 9001:2015 does not specify a method but emphasizes the importance of risk management. IATF 16949:2016 proposes a specific method that uses FMEA as the primary identification tool. As manufacturers apply FMEA to each specific situation, it is important to understand how risk should be addressed based on standards and guidelines. There is no mandatory requirement to eliminate all design and process risks, but an expectation to identify, document and manage them.
It should also be noted that auditors investigate FMEA as one of the ways to assess how a company manages quality and failure. Furthermore, they are crucial to minimizing potential defects prior to production to achieve advanced product quality and reduced warranty claims and costs.
What roles does FMEA play throughout the entire product lifecycle?
A forward-looking approach to quality initially enables you to comprehend the needs of the customer and then builds quality into the design of both product and process. FMEA can be used to recognize possible failures beginning early in development. As a fundamental part of the quality planning process, automotive companies need to manage numerous design and process risks in their daily business activities to avoid recalls or adverse events.
An integrated FMEA solution is one of the best tools a company can use to avoid product defects and process faults. FMEA provides the toolset to recognize and moderate design and process risks in the virtual product and process structures.
The FMEA is a cross-functional methodology touching the entire product realization process, which includes both design FMEA (D-FMEA) and process FMEA (P-FMEA). D-FMEA applies an analytical method to discover potential failure when developing a new product. P-FMEA is used to discover risks in new manufacturing processes and helps make products and processes as robust as possible.
What is the value of performing FMEA within a QMS that is integrated with PLM?
FMEA has been conducted in the past using numerous manual and homegrown approaches, but today’s state of the art is FMEA software that supports failure assessment efforts within a QMS solution. This approach makes FMEA an integral tool in an end-to-end quality program.
FMEA within a QMS and PLM digital ecosystem replaces manual tracking of a disparate set of quality activities using decentralized tools across the enterprise with a centralized database housing all quality-relevant data. This digital quality approach enables our customers to support a closed-loop quality approach from design to manufacturing.
Teamcenter Quality, which is part of the Siemens Xcelerator business platform of software, hardware and services, helps you support all of the quality-relevant processes required in the overall product lifecycle. Built on top of the Teamcenter PLM backbone, Teamcenter Quality helps quality engineers use product and process information, as well as share cross-departmental workflows, so they can streamline the core quality management processes.
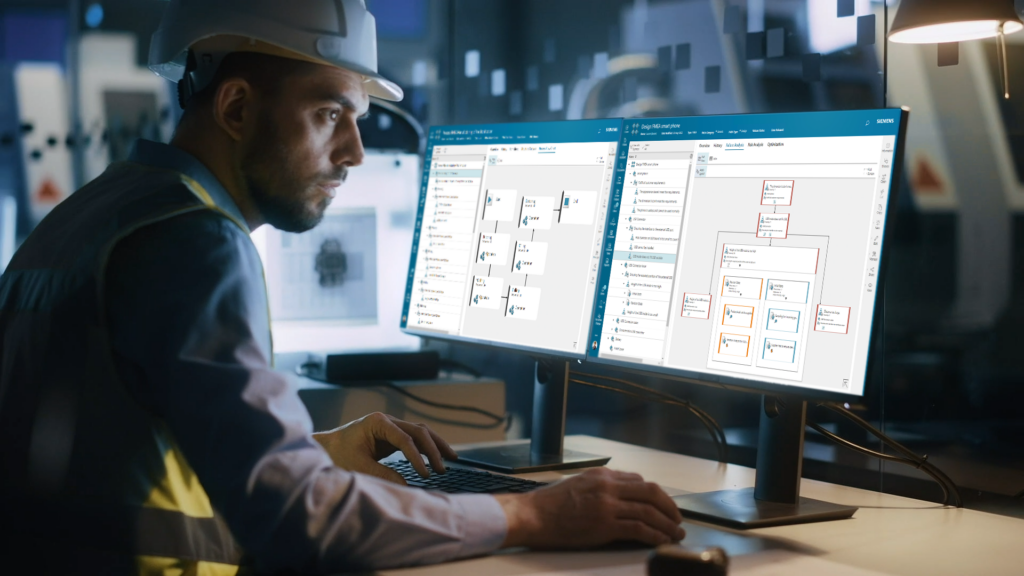
Supporting the advantages of FMEA plus a digital quality approach is a comprehensive knowledge database that can be accessed by all relevant experts. Former experience can be applied to new projects to abbreviate the development process cycle and minimize or eliminate defects at the launch of the production cycle.
With the Teamcenter collaboration platform, the value of analysis is enhanced due to the opportunity to directly access all engineering data, such as bills of materials (BOMs), bills of process (BOPs), drawings and 3D models. You can manage FMEA throughout the product lifecycle, and utilizing Teamcenter Quality FMEA allows you to support FMEA planning. People and responsibilities can be organized in a project by using the capabilities of quality project management solutions, using an action tracking and alert mechanism. Residual risks can be managed by using the control plan and closing the loop with problem-solving and change management processes.
If you had to give a brief summary, what would you say is the business case for implementing Siemens QMS solution for FMEA?
The Siemens digital quality approach enables manufacturers to access all available engineering with native PLM integration. Siemens smart manufacturing portfolio delivers a strong opportunity for digital transformation in quality management. When both OEMs and suppliers implement a comprehensive quality management solution, they realize enormous benefits, often exceeding targets with reliable and high-quality products.
Do you want to learn more?
To learn more about the FMEA, don’t miss our upcoming webinar in June, where special guest, Axel Eicker (Senior Product Manager – Teamcenter Quality FMEA) will guide us in a deeper understanding of the process and explain how Siemens solution can support quality initiatives.
In the meantime, find out more in this white paper about possible application of the Teamcenter Quality FMEA.
Axel Eicker, Siemens Senior Product Manager – Teamcenter Quality FMEA
Axel has studied production technologies at the University of Applied Sciences Cologne and quality management at the distance learning institute of the Berlin University of Applied Sciences. He started his journey inside Siemens in February 2020 as a senior product manager for Teamcenter Quality FMEA. Prior to this, he gained his professional experience of a total of 11 years in the automotive industry and in the household appliance industry. He spent his entire career in quality management roles within the development departments of three different companies. The moderation of FMEAs and the associated process and method optimizations were more or less the focus all along. Today Axel brings his knowledge to Siemens with the goal of developing the best FMEA solution.