BENTELER Automobiltechnik reduces quoting time by 40% while balancing CO₂ footprint, profit margins, and customer value
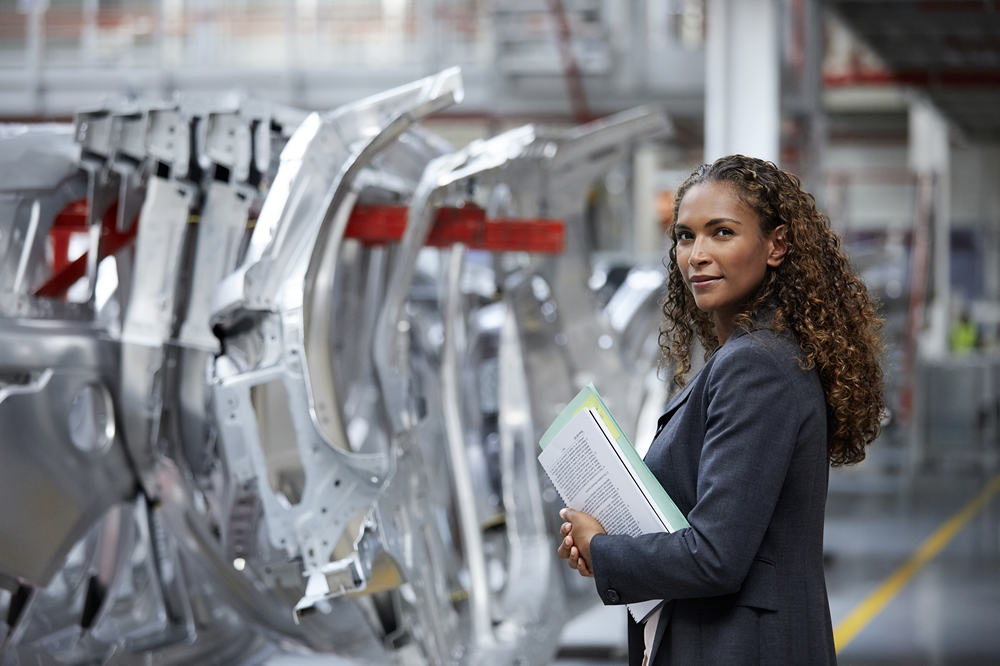
In manufacturing, the decisions managers make today can determine their companies’ future success or failure. Whether choosing the right investments, selecting the best production location, or calculating the cost of producing a product with the lowest carbon footprint, each choice holds significant weight. To navigate these complexities, managers need a clear and thorough understanding of the alternatives available and the ability to predict the impacts of each decision.
These decisions involve balancing financial performance with other considerations, such as environmental impact, operational efficiency, and risk management. Managers can only make the right choices when they compare and carefully weigh all the available alternatives. Informed decision-making relies on having access to detailed information, understanding the implications of each potential move, and simulating the outcomes to reduce uncertainty.
By using simulations and data analysis, managers can see the broader picture, assessing the short- and long-term impacts of various choices. The more detailed and accurate the information available, and the more effects that have been simulated, the more confidence managers can have in their final decisions. This kind of foresight helps organizations not only avoid pitfalls but also seize opportunities in competitive and volatile markets.
This is a great example of how BENTELER Automobiltechnik GmbH leverages the solution Teamcenter Product Cost Management for strategic decision-making early in development which is laying the foundations for success.
The automotive sector of the BENTELER Group is organized into two divisions: BENTELER Automotive Components and BENTELER Automotive Modules. As a development partner for the world’s leading automobile manufacturers, the two divisions work with around 20,000 employees in more than 20 countries to develop tailored solutions for their customers. Their product portfolio includes components and modules in areas like the chassis, body, engine, and exhaust systems, as well as future technologies such as battery storage systems for electric vehicles. The company also supports customers along the entire value chain, from product ideation through development to production and assembly. For a global manufacturing company like BENTELER, forecasts and cost analysis in financial planning and corporate management are prerequisites for evaluating new investments, project plans, and quotation submissions and their financial effects.
The pressure on original equipment manufacturers (OEMs) to reduce the carbon dioxide (CO2) emissions of their vehicles to comply with regulatory requirements has been increasing for several years. This stricter CO2 regulation for OEMs also impacts suppliers like BENTELER. The company calculates the CO2 emissions for modules and components upon customer request. BENTELER and its customers are increasingly interested in the CO2 footprint of materials and manufacturing processes to achieve their own sustainability goals. Therefore, the company combines sustainability and profitability by integrating the product’s CO2 assessment into existing structures and processes for calculating costs.
Keys takeaways from BENTELER’s success with Teamcenter Product Cost Management
- Optimize the quotation calculation processes, and reduce quoting time by 40 percent
- Analyze the impact as a trade-off between the CO2 footprint, profit margin, and customer value
- Ensures greater efficiency, as they can calculate the costs and CO2 footprint for a large number of our products along their value chain
- Model project costs which provide the best conditions for comprehensively evaluating the opportunities and risks of long-term delivery agreements or new investments