5 ways industrial AR transforms work
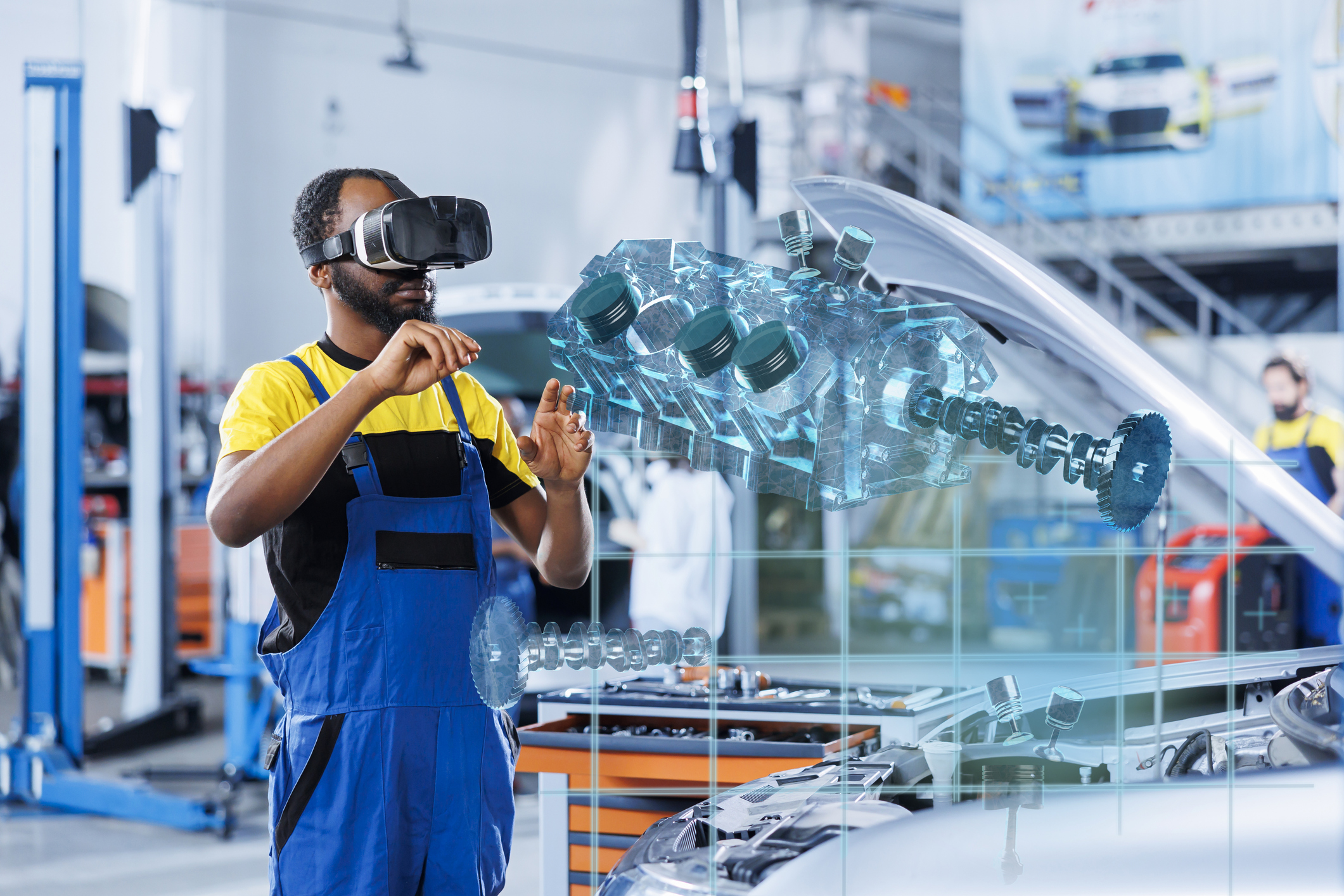
Augmented reality (AR) is going mainstream in industrial operations. This powerful technology provides frontline workers with hands-free access to vital information by projecting instructions, animations, and data directly into their field of view. Across industries, industrial AR is allowing technicians to identify issues faster, learn more efficiently, work with higher quality, maintain safety, and increase productivity.
In this blog post we’ll explore how service organizations can leverage industrial augmented reality to empower their technician workforce like never before possible. Whether your goal is reducing downtime, compressing training timeframes, ensuring procedural accuracy, maximizing workplace safety, or getting more done using the same resources, industrial AR is a technology you need to understand.
#1 – troubleshooting and repair
One of industrial AR’s biggest benefits is providing technicians with real-time access to equipment schematics, repair manuals, and step-by-step instructions overlaid directly onto the equipment they’re working on. An example of this is manufacturing technicians who use AR to identify and fix issues on complex assembly line machinery. They can view 3D models, part diagrams, and recommended repair steps, all seamlessly blended into their vision of the actual equipment. With this additional context in their field of vision, technicians can rapidly diagnose problems and have the machines up and running again, while minimizing costly downtime.
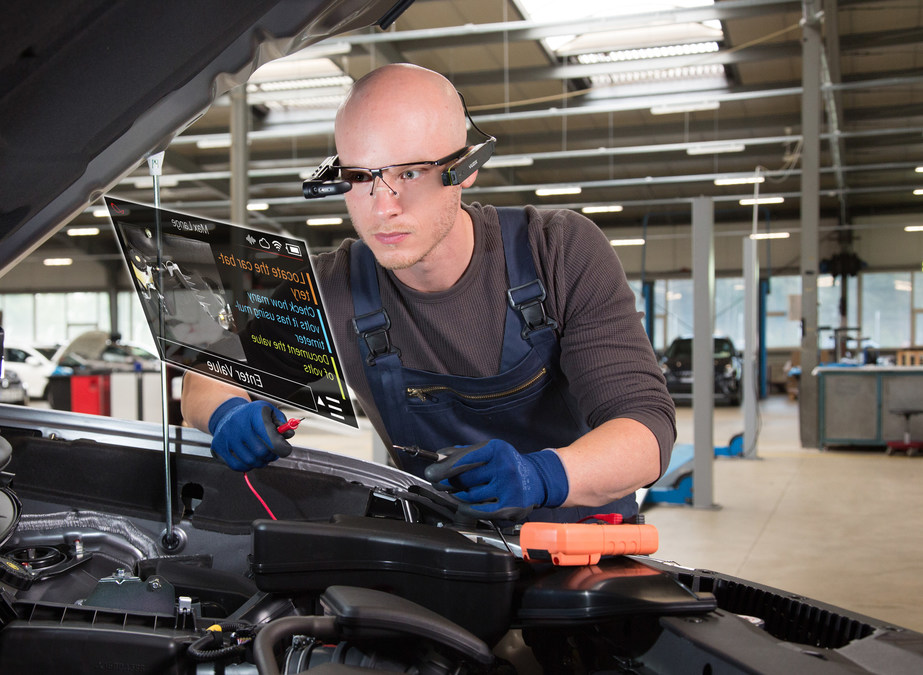
#2 – training and knowledge transfer
Industrial AR enables next-generation training by allowing technicians to practice service procedures and simulate realistic scenarios. Trainees can practice hands-on with the actual machinery while industrial AR provides guided workflows, techniques, and enables collaborative sessions with instructors, overlaying instructions and animations directly onto the workspace. An example of this can be found in some training programs for new wind turbine technicians. Industrial AR allows these trainees to learn maintenance procedures on a real turbine, using augmented reality to see tools highlighted, access manuals, and even have an instructor remotely correct and guide them. This immersive, learn-by-doing approach accelerates their development.
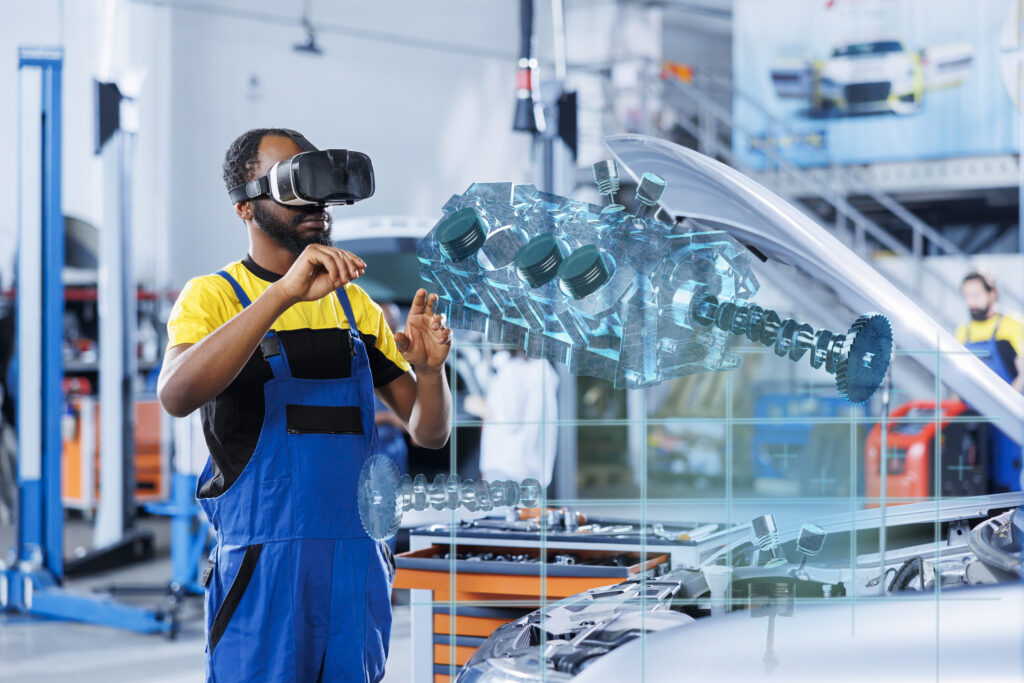
#3 – quality and precision
For many industrial maintenance tasks, ensuring quality and precision is critical to safety and proper equipment operation. Augmented reality can be helpful here, by overlaying precise guidelines, measurements, tolerances, and other data directly onto the work surface, while guiding technicians every step of the way. An example of this in practice is with aircraft maintenance. Technicians use industrial AR to visualize precise engine measurements, overlay tolerance ranges, and view detailed reassembly instructions – all while working hands-on with the actual equipment. This “extended reality” view helps them to complete maintenance tasks with exacting quality.
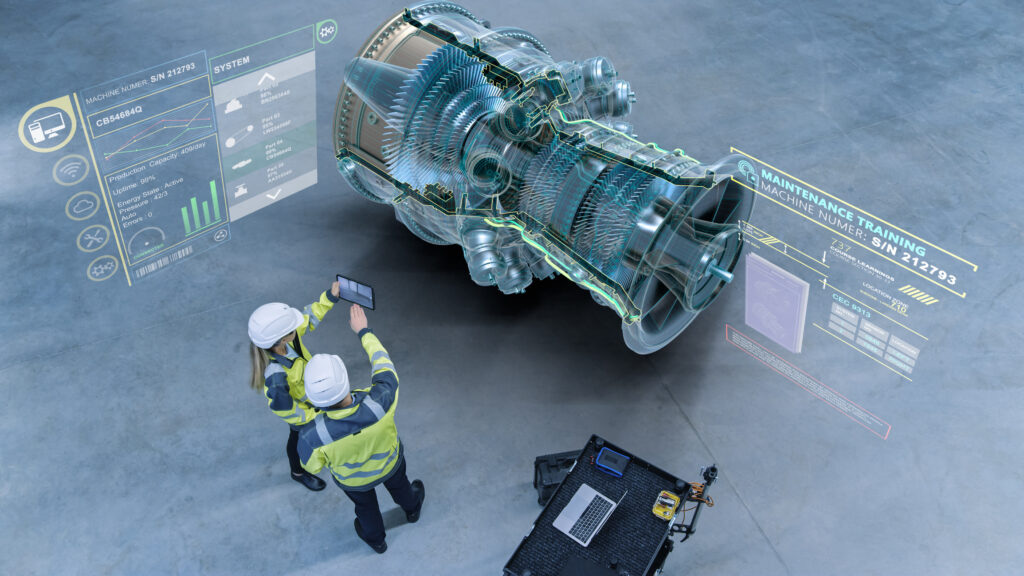
#4 – safety and compliance
Workplace safety is a top priority for service organizations and an area where industrial augmented reality can really help. By making hazards and safety protocols easily visible in the technician’s field of view, industrial AR provides a powerful way to enhance workplace safety. It can automatically detect warning signs for technicians, perform automated equipment checks, display required PPE, and provide easily accessible safety checklists. In industrial settings such as chemical processing plants, industrial AR can help ensure compliance with safety measures by displaying lockout/tagout reminders, PPE requirements, and safety inspection procedures – all superimposed onto the technician’s real view of the environment.
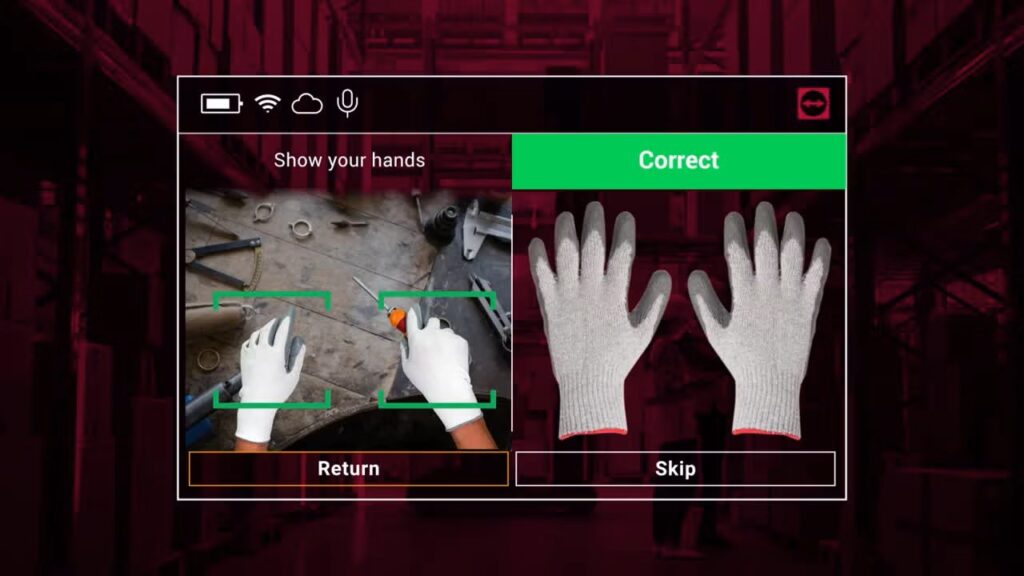
#5 – productivity and cost savings
Ultimately, the main business benefit of industrial AR is its ability to boost productivity and reduce costs through more streamlined processes and fewer errors. With industrial AR providing on-demand access to information, remote expert assistance, and precise guidance, technicians can accomplish more with the same resources. Service organizations that use industrial AR have realized significant operational improvements such as reduced service times, higher first-time fix rates, and reduced need for external contractors.
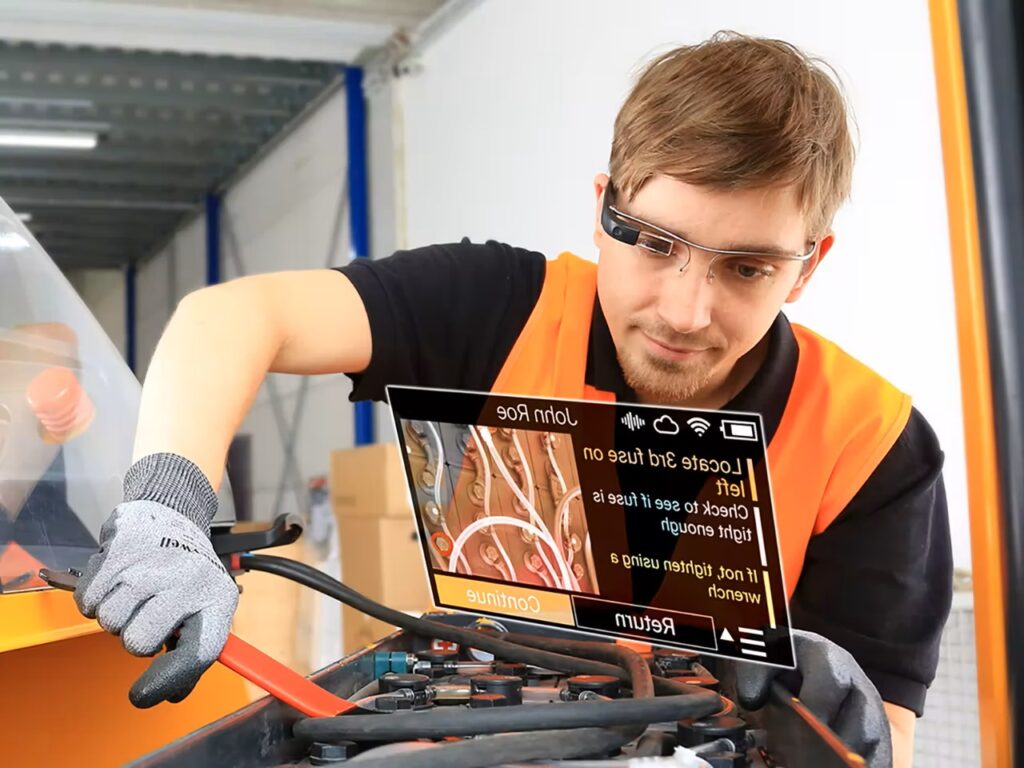
Start your industrial AR journey with Siemens and TeamViewer
These are only a handful of examples that illustrate the benefits of industrial AR for service organizations. By connecting technicians to the digital world in an intuitive, visually-augmented way, industrial AR can help service organizations to reduce repair times, improve quality and safety, accelerate training, and achieve greater productivity.
Getting started with industrial AR has never been easier. Through our partnership with TeamViewer, a leading provider of industrial AR solutions, we’re enabling customers to create AR content on Teamcenter by reusing the configurable digital representation of a product – the digital twin. Contact us today to learn more about how your organization can benefit from industrial AR connected to Teamcenter.
Ready to explore Teamcenter X, the leading cloud PLM?
No matter how you choose to deploy Teamcenter,
you get the same proven solutions designed to help you innovate faster.