Industrial AR across the product lifecycle
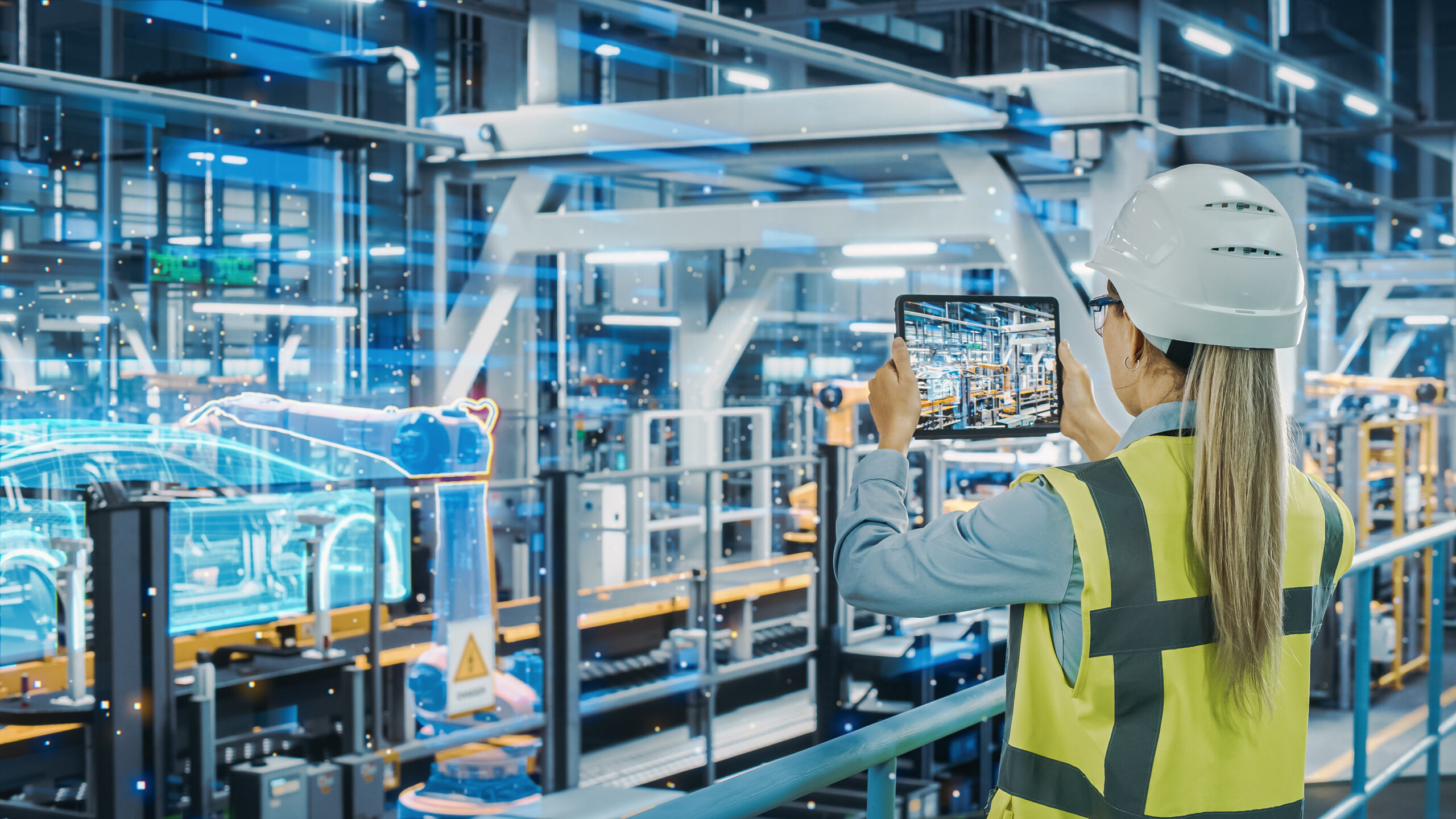
In today’s rapidly evolving industrial landscape, industrial augmented reality (AR) is emerging as a breakthrough technology, with proven use cases across the product lifecycle. From design and manufacturing to maintenance and aftersales support, industrial AR isn’t just enhancing existing processes; it’s redefining them, creating new possibilities for businesses to optimize their operations and stay competitive in an increasingly digital world.
In this blog post, we’ll explore how industrial AR is being successfully applied in three key areas: manufacturing and assembly, service and maintenance, and training and onboarding. We’ll highlight real examples of companies who have implemented industrial AR solutions from our partner, TeamViewer. And, we’ll show how industrial AR bridges the gap between the physical and digital realms, enabling workers to access critical information in real-time, collaborate with remote experts, and execute complex tasks with greater precision.
What is industrial AR?
Industrial AR is a technology that overlays digital information onto the physical world, enhancing the user’s perception and interaction with their environment in industrial settings. Unlike consumer AR applications, industrial AR is designed to improve efficiency, accuracy, and safety in manufacturing, maintenance, and training processes. It achieves this by providing real-time, context-aware information directly in the user’s field of view, often through smart glasses or mobile devices.
At its core, industrial AR combines smart object recognition, workflow digitalization, and seamless integration with existing enterprise systems. This allows workers to identify tools, parts, and machinery in real-time, access digital work instructions, and retrieve data from business systems instantly. Industrial AR also enables remote expert collaboration, allowing on-site workers to connect with off-site specialists for real-time guidance and support. These capabilities, coupled with hands-free operation through voice commands and gesture controls, make industrial AR a powerful tool for enhancing productivity, reducing errors, and improving safety across various industrial applications.
Industrial AR in action – use cases and customer results
Manufacturing and assembly
Industrial AR significantly improves accuracy and quality control in manufacturing processes. By providing visual guidance and real-time information, AR reduces assembly time and minimizes errors, leading to higher-quality products. Workers can access digital work instructions, 3D models, and component information hands-free, enhancing their efficiency and safety. Industrial AR also enables real-time quality checks, ensuring that each step of the manufacturing process meets the required standards. Here are some examples of customers that have benefitted from TeamViewer’s industrial AR solutions for manufacturing and assembly:
A leading systems provider implemented an AR solution on two assembly lines, resulting in zero errors, faster assembly, and 100% hands-free operation. The solution guides workers through assembly processes using smart glasses and integrates with external sensors for quality assurance.
A global automotive supplier utilized industrial AR to implement innovations across their global plants. This AR solution enables live sessions between experts at headquarters and technicians in remote locations, significantly reducing travel costs and improving the efficiency of innovation rollouts.
A major aircraft manufacturer deployed an AR-based inspection solution for helicopter assembly and maintenance. By using AR and smart glasses, they shortened gearbox inspection time by 40%, achieved 100% paperless documentation, and eliminated manual input errors.
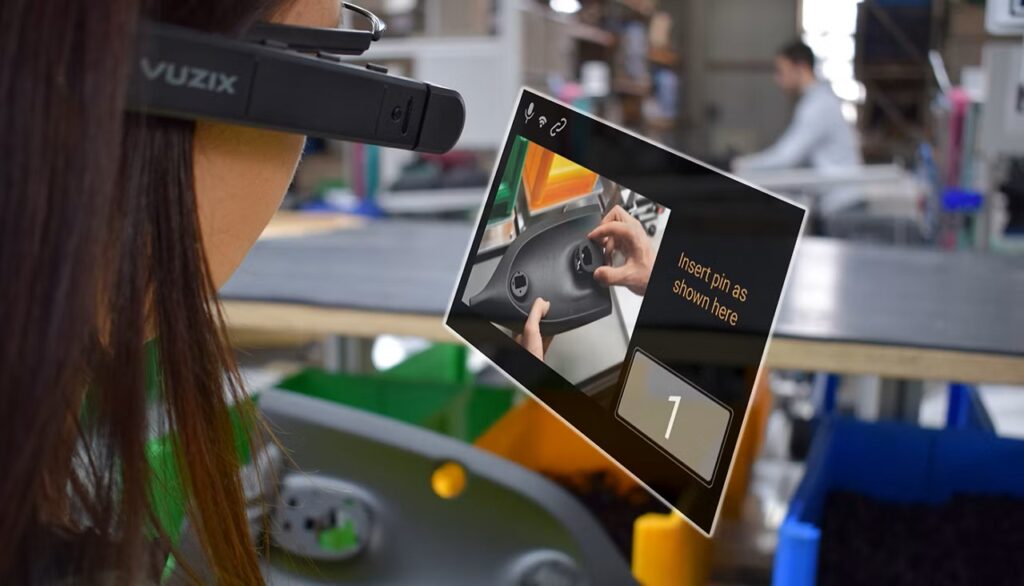
Service and maintenance
In the service and maintenance domain, industrial AR facilitates faster problem identification and resolution. Technicians can access equipment history, diagnostic data, and repair procedures in their field of view, reducing the time needed to troubleshoot issues. Remote expert collaboration allows on-site technicians to receive guidance from experienced colleagues, leading to improved first-time fix rates and reduced equipment downtime.
Real-world applications of TeamViewer’s industrial AR solutions in service and maintenance include:
A marine equipment company implemented AR for remote support in equipment maintenance. The solution enables real-time troubleshooting on ships worldwide, reducing travel costs by up to 80% and solving 85% of technical support requests during the first contact.
A multi-business chemicals corporation leveraged an AR-based solution to drastically reduce machine downtime from days to hours. By enabling remote support between plants in their technical textile division, they achieved a 50% reduction in downtime, 30% increase in productivity, and 20-30% savings in travel costs.
A power generation equipment manufacturer utilized AR for remote diagnostics and maintenance. Their AR-enabled kit allows experts to provide real-time guidance to on-site technicians, significantly improving response times and reducing the need for on-site visits.
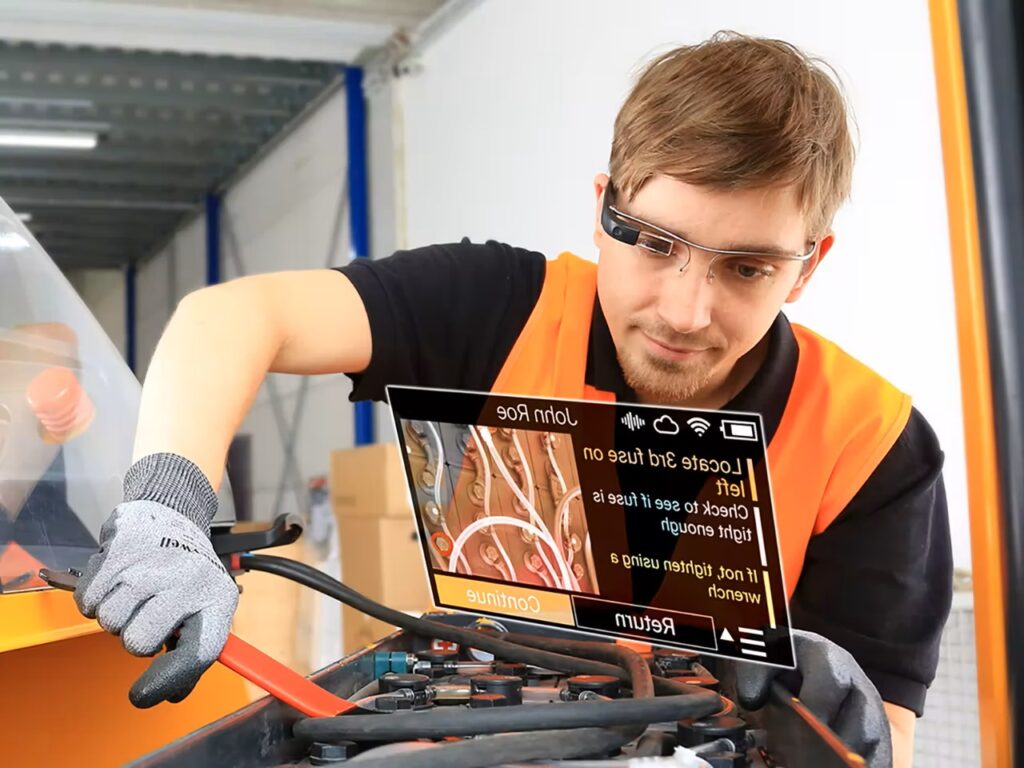
Training and onboarding
Industrial AR revolutionizes training and onboarding processes by providing immersive, interactive learning experiences. New employees can receive step-by-step guidance for complex tasks, accelerating their learning curve and reducing the time needed to achieve proficiency. AR-based training ensures consistent and standardized experiences across different locations, improving knowledge retention and transfer.
Moreover, the ability to practice procedures in a virtual environment enhances safety and reduces the risk of costly mistakes during actual operations. Successful implementations of TeamViewer’s industrial AR solutions in training and onboarding include:
A pharmaceutical company implemented AR solutions in their manufacturing processes. They use smart glasses to simplify the onboarding process, display visual instructions for complex procedures, and provide remote support, ensuring consistent quality and compliance in their GMP environment.
A global office equipment manufacturer used AR technology to enhance technician training for printer maintenance. By implementing AR and smart glasses, they reduced servicing times by an average of two hours per case nationwide, with up to five hours saved in remote areas.
A premium automotive manufacturer deployed AR-based training solutions for quality assurance in manufacturing. Using AR, they display important information on test steps and processes through smart glasses, standardizing test procedures across all plants worldwide and enabling quick deployment of new testers.
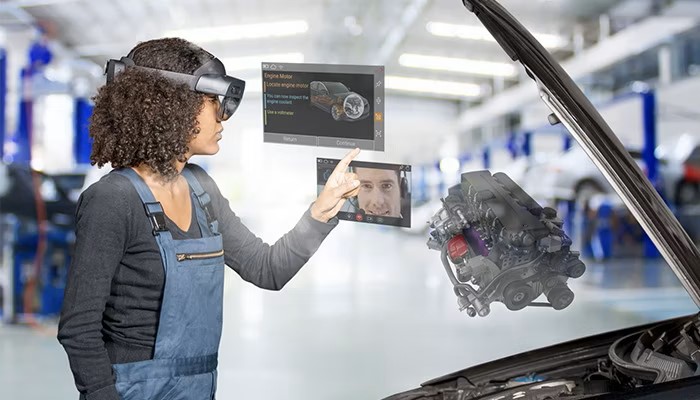
Start your industrial AR journey with Siemens and TeamViewer
Industrial AR is rapidly transforming the way businesses approach the product lifecycle. As demonstrated by the examples provided, it’s clear this technology is not just a futuristic concept but a present-day reality, delivering tangible benefits. And through our partnership with TeamViewer, a leading provider of industrial AR solutions, it’s now easier than ever for product manufacturers to implement industrial AR by reusing the digital twins of their products, managed in Teamcenter. Contact us today to learn more about how your organization can benefit from industrial AR connected to Teamcenter.
Ready to explore Teamcenter X, the leading cloud PLM?
No matter how you choose to deploy Teamcenter,
you get the same proven solutions designed to help you innovate faster.