Customer Zero in Teamcenter Quality
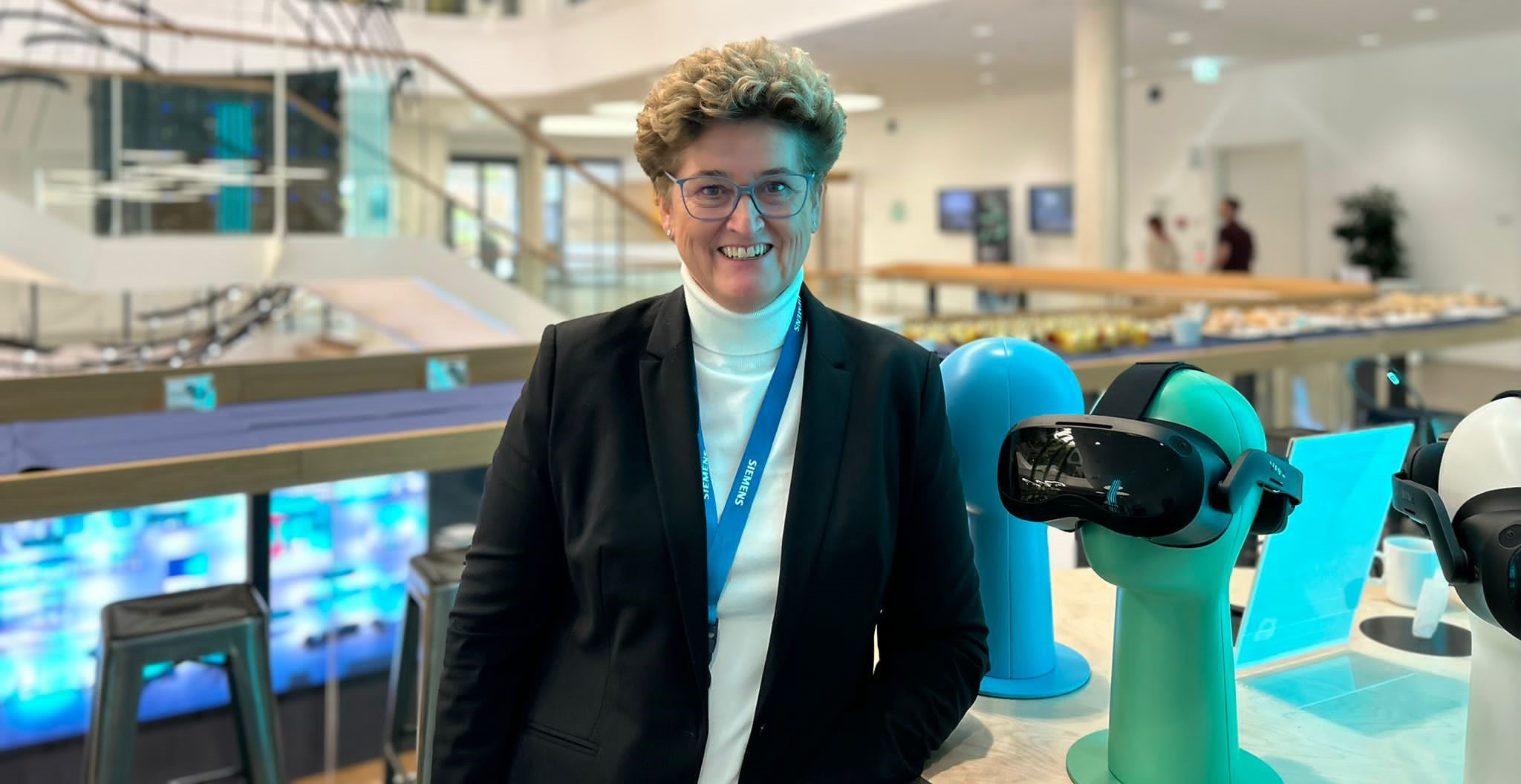
The role of Customer Zero in Teamcenter Quality
Listening to and learning from customers has always been a crucial part of how Siemens Digital Industries Software develops and refines our software solutions, ensuring that our products can rightly be described as “best-in-class.” Since we use these products in Siemens businesses, it only makes sense that we would leverage our own customer experience in this same way.
In fact, the “Customer Zero” approach is part of Siemens’ DNA. “When developing new products, we already have the whole End-2-end process in our mind. This means that we cover the whole product lifecycle from ideation, development, procurement, software development, production and beyond. Our quality principles are in the loop to mitigate potential risks to the lowest.” explains Monika Hofrichter, Global Head of Quality Management and EHS at Siemens Digital Industries.
Hofrichter recently oversaw a customer zero approach to Teamcenter Quality. Siemens AG business units integrated their standardized processes and knowledge into the software helping to verify its effectiveness and refine it to meet real needs. Here is what we learned through this experience.
How the Customer Zero approach works at Siemens
Siemens endorses the Customer Zero approach not just for our own use but also as part of a sound business strategy for any company. When a company uses its own products or services internally before releasing them to the external market, that company can evaluate and refine its offerings under real-world conditions, acting as its own first customer (thus the designation “Customer Zero”). By doing so, the company implements its own processes while identifies and resolves potential issues, gathers internal feedback, and demonstrates confidence in its products.
Hofrichter has long appreciated the value of the Customer Zero approach. Having worked in several Siemens enterprises worldwide, including IT, automotive, energy and infrastructure, she has been able to bring a unique experience in data management, process and data architecture, End-2-end process and a proven skill set to bear on Teamcenter product lifecycle management (PLM).
When she joined Siemens Digital Industries Quality Management and EHS, Hofrichter soon recognized an opportunity to incorporate innovative functionality into the product through a customer zero approach.
“When I started my role in 2017,” she recalls, “I quickly learned that we had innovated some custom features of the Teamcenter version we were using internally, and customers haven’t been aware of. Throughout my career at Siemens, I have understood that standardization is the best way to reduce costs and gain speed by optimizing processes. I immediately partnered with our Teamcenter software specialists to explore how we could incorporate our customizations into the standard Teamcenter Quality version and offer it.”
A broad approach for quality and compliance within PLM
The growing impact of increasing product and process complexity has led to a critical need for manufacturers to implement quality management system (QMS) best practices throughout the entire product lifecycle. To address this need, companies are required to redefine roles within product lifecycle management (PLM) and prioritize quality, cyber security and compliance as key objectives.
A recent CIMdata commentary highlights the importance of expanding QMS software beyond its traditional focus on manufacturing repeatability and customer complaints. By integrating QMS with digital twin PLM solutions, organizations can adapt to changing consumer patterns and evolving manufacturing practices. Applying quality and compliance management best practices to all processes becomes more effective as PLM systems enable accurate digital twins throughout the product lifecycle.
The commentary also emphasizes the benefits of seamlessly integrating PLM and QMS processes to achieve closed-loop quality and comprehensive digital twins. We invite you to read this CIMdata report “A Broad Approach to Quality and Compliance Management – A CIMdata commentary” to discover how you can bridge the gap between roles and domains within quality management.
Doing its part to build this broad approach to quality and compliance, Siemens introduced Teamcenter Quality in 2021 to expand our QMS capabilities into a complete lifecycle quality management ecosystem built on the Siemens Xcelerator business platform. By leveraging the wide portfolio of Teamcenter with combined QMS and PLM capabilities, manufacturers can achieve improved efficiency, quality, and collaboration throughout the product lifecycle.
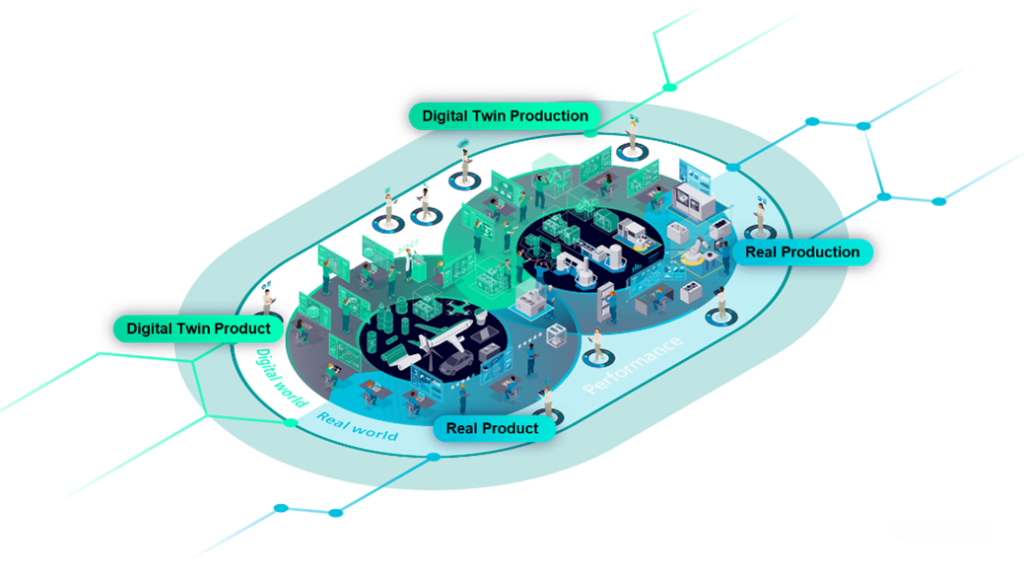
Through seamless coordination between quality processes and product development, Teamcenter ensures that quality requirements are effectively and efficiently incorporated into the product lifecycle. The software accomplishes this by facilitating improved collaboration among cross-functional teams, enabling efficient communication and information sharing. This helps to streamline decision-making processes, reduce errors, and enhance overall productivity.
Being Customer Zero on Teamcenter Quality updates
Each time the latest Teamcenter Quality version is available, Siemens starts working internally with the customer zero approach. In the recent case led by Hofrichter, the latest version of Teamcenter Quality was first made available to business units of Siemens AG in order to check the improvement of their own quality management in development, production and service over the entire product lifecycle. And of course, this deployment would also reveal ways Siemens could optimize the product.
The Siemens Customer Zero team included cross-functional experts such as product managers and internal IT architects. Experts within the business units (software, motion control, factory automation, process automation) contributed their strategic view. End users (developers, manufacturing and quality management professionals, supplier quality managers and production engineers) employed Teamcenter Quality and reported their experience. Through an iterative process, maturity reviews were conducted, functional enhancements were added to the out-of-the-box (OOTB) product, and the next version was put through its pace by the customer zero team.
According to Hofrichter, the further developments in Teamcenter Quality bring forth a range of transformative practices. One of the key aspects is the establishment of a preventive quality approach, which aims to mitigate risks along the value creation process. Another significant element is the concept of front-loading, where quality management is brought to the forefront of decision-making across all end-to-end processes. By incorporating quality considerations from the early stages, organizations can proactively guide decisions, aligning them with quality goals and standards.
Underpinning these approaches is the closed-loop approach, which emphasizes continuous improvement. By leveraging process improvement techniques and adopting iterative procedures, businesses can build on previous successes and learn from past experiences, driving ongoing optimization and innovation.
Digitalization emerges as a key driver in transforming quality management practices. By harnessing digital tools and technologies, organizations can streamline quality processes, collect and analyze real-time data, and make data-driven decisions. This digital transformation promises to revolutionize quality practices, enhancing efficiency, product quality, and customer experiences.
Overall, these developments in Quality Management are set to reshape how organizations approach quality assurance. By embracing a preventive approach, front-loading decisions, and leveraging digitalization, businesses can position themselves for success in an increasingly competitive landscape, delivering high-quality products and services that meet and exceed customer expectations.
Benefits of embracing a digital approach for quality management
Embracing a transformative approach for quality management, businesses can leverage three main benefits for improved product development.
Firstly, by gaining end-to-end process understanding, organizations can seamlessly integrate development data into the product development process. This eliminates the need for connectors, enabling real-time utilization of valuable insights and facilitating more efficient decision-making.
Secondly, the incorporation of advanced analytics and predictive modeling enhances risk management capabilities. By proactively identifying and mitigating potential issues, businesses can minimize risks, optimize resource allocation, and ensure smoother product development cycles.
Lastly, the implementation of predictive maintenance strategies brings significant advantages. By leveraging data-driven insights, organizations can optimize equipment performance, reduce downtime, and achieve cost savings through efficient maintenance planning.
How customer zero benefits Teamcenter Quality customers
Through the customer zero approach, Siemens has successfully optimized Teamcenter Quality while streamlining our own product development cycles. “We use what we sell,” Hofrichter points out. “With our customer zero approach, we have taken our own expertise in optimizing and standardizing our quality processes and incorporated it into Teamcenter Quality, thus maximizing its value for our customers and ourselves. A major advantage is that we can use the product data for the quality methods from our PLM environment at any time.”
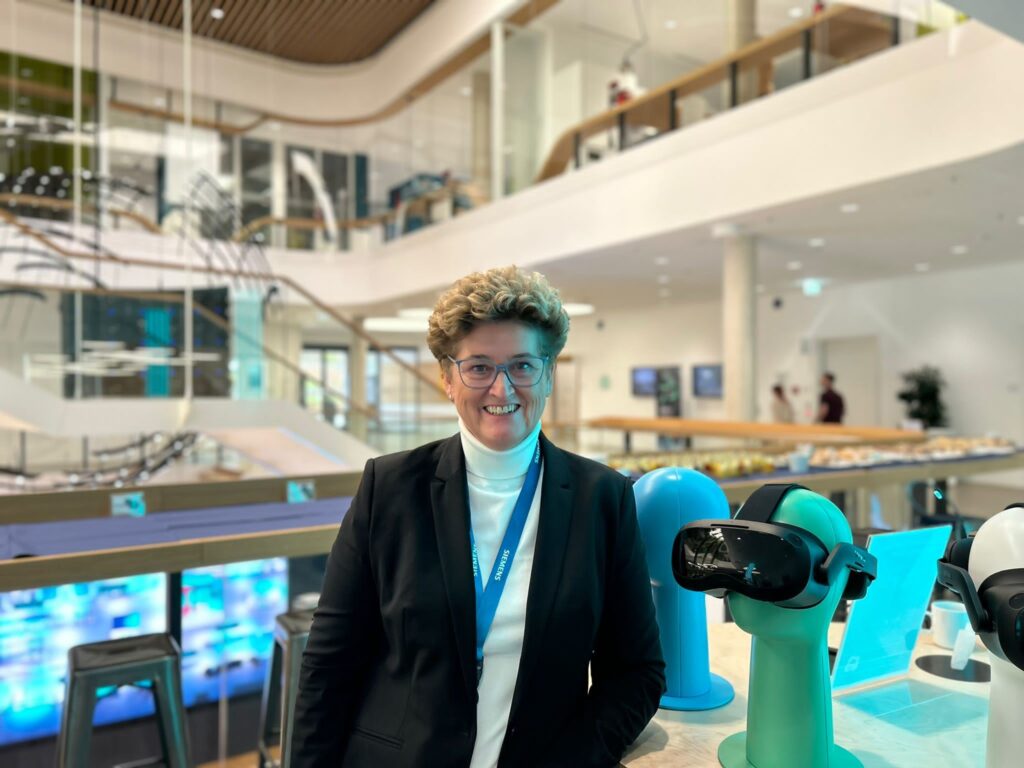
“By avoiding unnecessary customizations and adaptations,” she continues, “we significantly improve efficiency and eliminated unnecessary expenditures for ourselves and our customers. Not only does this approach help us to be faster with our software release cycles, but it also allows us to better allocate our resources, enabling us to deliver innovative solutions to our customers.”
The use of the Customer Zero approach enables Siemens to incorporate the experience of 175 years of success into its own products. It also helps uncover both minor and major issues that might not be apparent in controlled test environments. Solving these problems early can prevent customer dissatisfaction and costly post-release fixes. For these reasons, Siemens recommends the customer zero approach to the global manufacturing community. Using your product internally serves as proof of concept and shows that your company believes in its product enough to rely on it operationally. This can boost the product’s credibility and market trust when launched.
“With the Customer Zero approach,” Hofrichter concludes, “we have embraced a unified strategy where every feature or change request is integrated into a single process. By consolidating our efforts and eliminating the need for duplicated development, we have been able to achieve a faster time to market. Additionally, every customer who uses our Teamcenter solution can leverage the full power of Siemens, implementing our way of working and thinking within their company. Even small-sized companies can now benefit from our extensive experience to become more efficient with best-in-class processes.”
More innovations to come
Siemens remains committed to continuously refining our processes and creating cost-effective solutions that meet the unique needs of our customers while eliminating duplications and optimizing resource allocation.
We have exciting plans for new Teamcenter Quality features to be developed under the customer zero approach. One notable upcoming development is the implementation of generative artificial intelligence (AI) into the Teamcenter Quality modules. “This integration promises to greatly enhance the capabilities and efficiency of our quality management processes,” Hofrichter notes. Stay tuned for more updates on this groundbreaking development.
In the meantime, the current Teamcenter Quality release will help companies achieve new quality goals by:
- Ensuring consistent quality across all stages of the product lifecycle
- Minimizing defects and rework, thereby reducing costs
- Enhancing customer satisfaction through reliable and high-quality products
- Facilitating sustainable practices by efficiently managing product returns and recycling
- Improving overall efficiency and productivity through streamlined processes and better resource utilization
For more about best-in-class Teamcenter Quality, we invite you to visit our website and gain access to all our product resources.
Ready to explore Teamcenter X, the leading cloud PLM?
No matter how you choose to deploy Teamcenter,
you get the same proven solutions designed to help you innovate faster.