Check out what accurate cost estimation is making possible
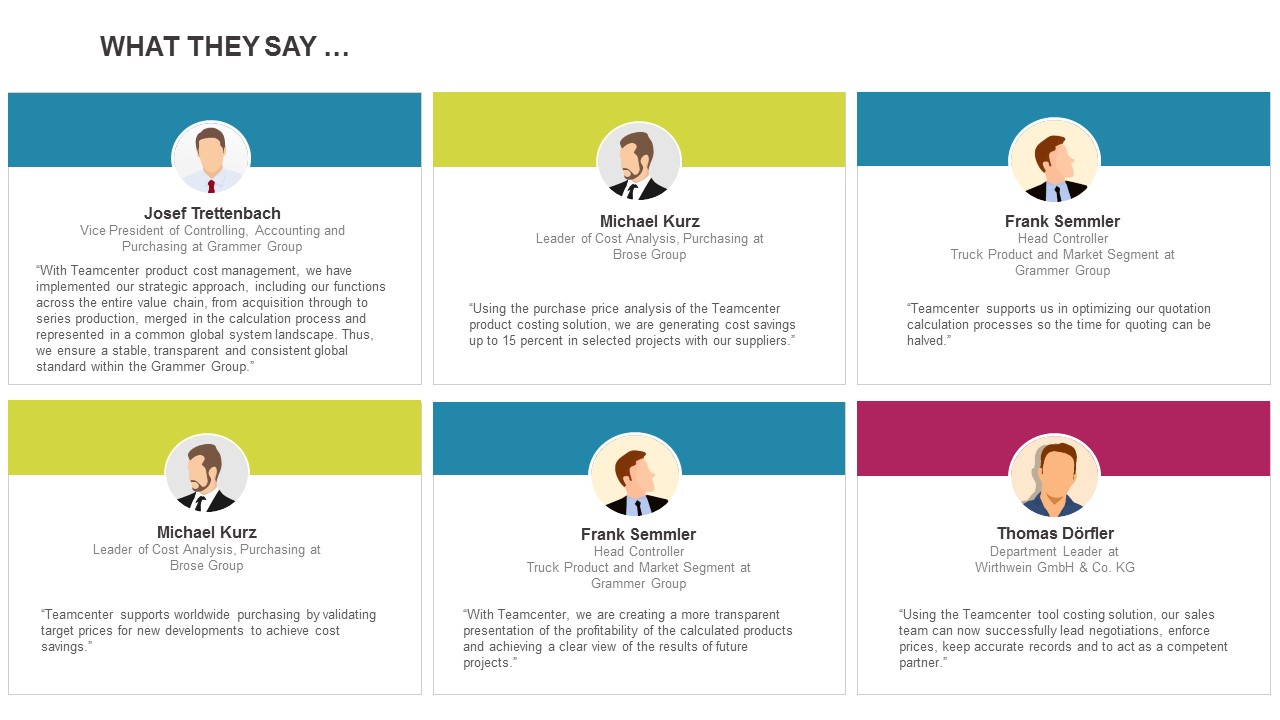
Every day, a cost estimator must deal with questions regarding costs, such as how can costs be reliably predicted before process engineering has started, what assumptions the quote should be based on, or how should these figures be adjusted to take into account changes in product, process or market conditions.
The following 3 minutes case studies video explore some high-profile companies that have managed to sustain their product and tool cost optimization efforts and keep expenses under control. The challenges faced by these organizations and the steps they took may provide some inspiration for successful long-term cost management within your own organization.
These case studies are merely summaries of the changes that these high-profile brands made to their product and tool cost estimation process. What can be seen from these brief accounts though, is if a company doesn’t have standardized calculation methods, it is impossible to systematically track and optimize product and tool costs. Different information technology (IT) structures and lack of standardization of the storage systems can make it difficult to analyze the costs, especially in global projects. The preparation of cost calculations with different versions of spreadsheet software are meant to deal with nonstandard calculations. (These are only a few challenges these companies had to deal with.) The best-in-class cost estimation software, Teamcenter Product Cost Management, provides an enterprise-wide platform for managing calculations, and thus provides the basis for standardized costing methods, models for fact-based calculations and transparency into cost drivers.
Read the full case studies on Brose and Wirthwein.
Cost estimation with Teamcenter Product Cost Management