Change Lineage, Item Disposition and Inventory Management
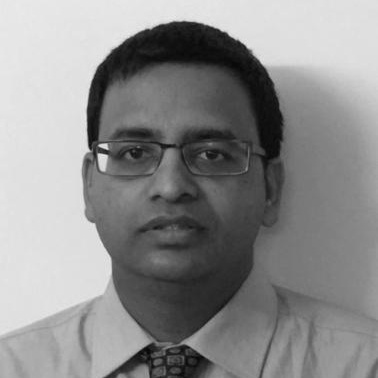
For an exclusive, inside look at Teamcenter change management, register for this webinar, “Strategies to Streamline Product Innovation with Engineering Change Management.”
Managing and tracking change lineage is a critical component of product change management. If your PLM process management and execution strategy doesn’t effectively account for change lineage, you may be missing some key advantages to managing change inside PLM.
Amitabh Verma has explored how you can leverage your change management process to enable part reuse and how you can deploy change management to get more from your PLM investment. Now let’s talk about how a PLM strategy that leverages change lineage and item disposition can help with better inventory management.
Let’s start by looking at the definition of lineage.
Lineage: A sequence of species each of which is considered to have evolved from its predecessor.
Human Lineage
You get the gist, but we will talk about more mundane things – the evolution of components, parts and assemblies.
I would like to talk about some change management capabilities in Teamcenter which facilitate the management of inventory and supply chains – change lineage and item disposition.
Change Lineage
Change lineage tracks the evolution of impacted items to solution items via a relation between solution items and their corresponding impacted items. Change lineage ensures that the impact of change is well understood by downstream users and systems – manufacturing, purchasing, inventory management and others.The information is also available for audits.
Change lineage can be used to represent different types of product “evolutions” such as the:
- Revision of a part
- Replacement of one part with one part
- Replacement of multiple parts with one part
- Replacement of one part with multiple parts
- Replacement of multiple parts with multiple parts
Item Disposition
Item disposition allows the users to specify the disposition of impacted items being revised or replaced as part of the change. Default dispositions are:
- Use As Is: Keep the parts in production
- Scrap: Do not use the remaining parts
- Rework: Modify the part, and use the modified parts going forward
- Other
Customers can configure additional values for item disposition as per the requirements and relevance for their business.
Bringing it all together
While change lineage maps the superseded items to the superseding items, item disposition provides guidelines for inventory management of superseded items. The decision to use the existing inventory delays the benefits to be derived from superseding items but it prevents write off of existing inventory as scrap. Rework offers the middle ground in case the superseded item can be reworked to conform to the requirements of the superseding item. Item disposition also helps the purchasing and procurement departments to develop a sourcing strategy for the superseding item.
Item disposition facilitates communication between engineering and manufacturing/procurement. Manufacturing provides guidelines and feedback to design engineers to improve manufacturability of products by being part of the design review. Design engineers provide suggestions on the sourcing strategy and item disposition to manufacturing and procurement. Best-in-class organizations ensure such communication by having a formal closed loop change management process which is enabled by commercial PLM software. CMII is an industry standard which provides robust guidelines on closed loop change management processes.
Deployment of PLM software can help an organization move towards closed loop change management but as Aberdeen’s research has shown, best-in-class also ensures that not only do the departments talk to each other but “the real advantage” comes in when the supporting systems are interoperable and connected.
How does your organization communicate engineering changes to downstream departments and what challenges do you face with the interoperation of different IT systems? We would love to hear about your experiences and work together to solve them.
About the Author
Amitabh Verma is a Product Manager with over 15 year of experience implementing and developing PLM solutions. He is currently responsible for Teamcenter Change Management. His areas of interests include Integrated product development and Change management in Automotive, Aerospace and Process industries