Teamcenter Product Cost Management | What’s New?
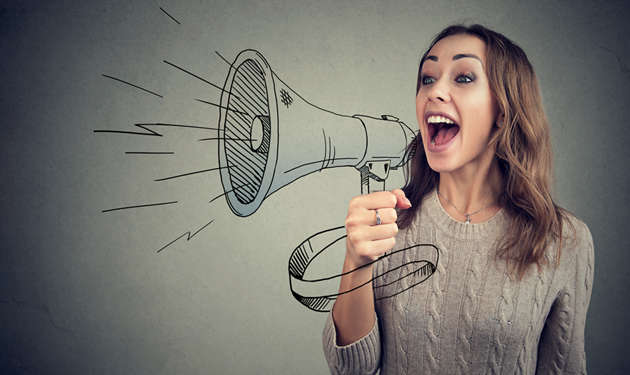
We are working to make it easy and affordable for customers to develop profitable and climate-smarter products. With Teamcenter Product Cost Management version 2406, we have further optimized our solution supporting customers in measuring, managing, and minimizing product cost and carbon emissions within their value chain. This enables them to meet margins and sustainability goals.
Use the cloud to calculate tool and transport costs and carbon footprint
To accelerate your digital transformation, we have increased the cloud-based capabilities for Teamcenter X Product Cost Management by extending the scope of the product calculations to include the cost and carbon footprint of both tools and transport. With an extended scope, you can leverage more accurate calculations quickly.
Speed up your transport cost and carbon footprint calculations
In the new version, a recommendation of the transport mode is automatically applied as default to your calculation. Further, you can automatically calculate the transport weight, which is calculated based on the part weight and package weight (Fig. 1). This reduces manual work, and you can calculate the transport cost and carbon footprint much faster.

Maximize the value of your cost and carbon footprint calculations with the new and updated reference data
Accurate data is the basis for precise calculation results. With the regularly updated benchmark data in Teamcenter Product Cost Management you know immediately where you stand compared to the competition. The quarterly main releases for our benchmark data are in February, May, August, and November (Fig. 2).
Content costing: Production site data is provided twice a year, in February and March, and includes labor costs, labor burden, floor space costs for 67 countries and 454 regions, and interest rates. In addition, labor costs data is delivered for two skill levels, labor burden for three shifts, and floor space costs are available for the office and warehouse categories. The energy prices and interest rates are updated twice a year, in May and November. The machine database is regularly extended with new machines and updated four times a year. We continuously extend our data content and provide in this new release, data for two new countries Costa Rica and Uruguay. For more information on the countries, please read the specific release letter where you can find information on the country data developments for each country and each cost factor.
Content pricing: The material prices are updated four times a year and the overhead rates once a year in August. The latest material price update includes material price data for about 10.000 material prices, 3 regions, and a world average price plus 7 semi-finished product types and 3 yearly ordering quantities for each material.
Content carbon emissions: The carbon emission data for materials and energy contains reference data for common materials, semi-finished materials, and energies, and is updated twice a year in May and November.
Your added values briefly:
- Lead timely and precise should-costing with updated global energy prices and interest rates
- Perform timely and precise should-costing with newly added machines to support additional manufacturing technologies
- Make the best decisions possible during negotiations with updated material prices to meet the latest price development
- Start easily calculating the product carbon footprint with updated CO2e material and energy data
- Leverage more accurate pre-configured manufacturing processes with the updated knowledge domain and new machines

User experience and collaboration
The new version provides significant UX innovations and improvements. We’ve updated the user interface by migrating the work center master data to the new user interface. The splash and login screen (Fig. 3) have been aligned with the UX design of the Siemens Digital Industries Software portfolio.

The “calculation basic data tab” view (Fig. 4) is now on the new user interface. This enables a new user experience for all input fields, especially unused views that can be collapsed. Further, the “calculation variant” view has been split into four views providing more focus to the user on relevant information. Warnings and errors are now visualized in the field where the validation occurs; this provides even more transparency to the user to identify potential issues directly. The “calculation validity” view is aligned with the information in the master data. The “calculation validity” describes the supply, location, and time of the calculation. The granularity of the calculation is defined in the detail view. The user can identify costs, one-time investments, and carbon footprint values, as well as the used shift model in this view.

Further, we have improved the layout settings for tables. For each tabular view, the changes you make on the collapse/expand state of the view, column order, width, and selection are saved automatically.
Flexible table editor
The beta version of the new “table editor” (Fig. 5) shows parts, materials, and manufacturing steps as structure elements of a bill-of-material (BOM). With the “table editor”, you can edit and manage a BOM and bill-of-process (BOP) structure. In the future, the “table editor” will leverage more and more features and substitute the current quick editor and BOM report. Data accessible in the “table editor” are also editable in the respective document. Some smart copy-and-paste action as well as filtering supports a good user experience.

Easy configure bulk data changes
The functionality for updating large numbers of data called „mass data change“ was renamed to „bulk data change“. The possibility to configure „bulk data changes“ enables you to store „bulk data change“ procedures which are typically often used. Leverage full-text search for „bulk data changes“ to search and open configurations and manage „bulk data change“ configurations to create, edit, and delete them.
Increased accuracy of pricing calculations
To increase the accuracy of pricing calculations you can now save updates on the pricing calculation in an intermediate state enabling rapid interactions at a later point in time. Further, you can perform more dedicated bulk mass data changes on your pricing calculations to speed up the calculation process. These improvements increase end-user productivity and data quality and empower end-users to work more efficiently.
Are you interested in learning more?
To get more details on the improvements mentioned in this blog post, look at Teamcenter Product Cost Management version 2406 (for registered customers only) and check out the other product cost management blogs.