What’s new in Teamcenter Product Cost Management
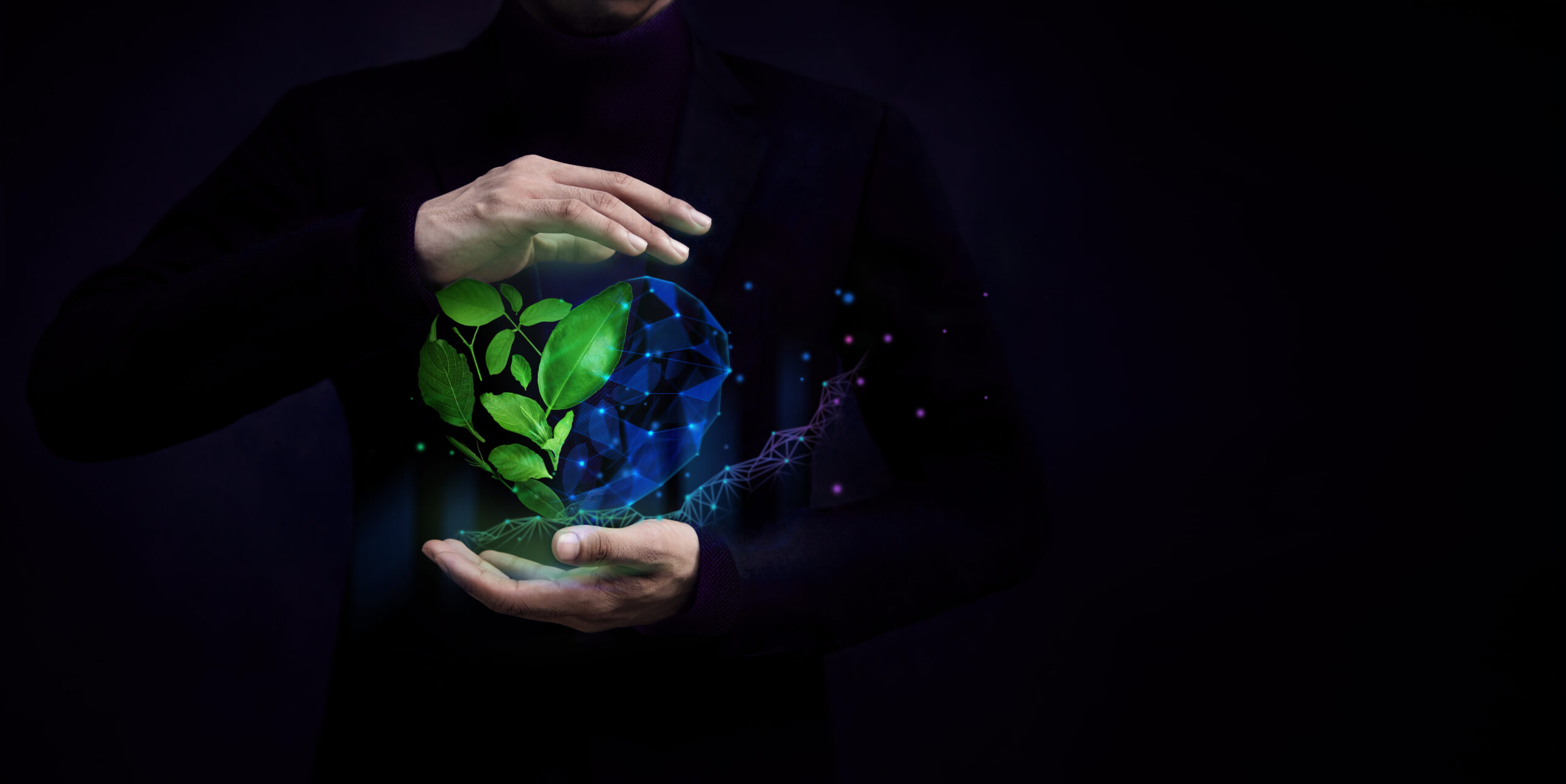
As always, this release is packed with a large variety of enhancements and innovations which help you to run your cost and CO2e emission calculations smoothly. In this blog post, I am going to walk you through the highlights of Teamcenter Product Cost Management version 9.6.
Improve your product cost calculation with the automated analysis in the 3D viewer and extraction of additional geometry parameters
The new capabilities in the core calculation and foundation area allow users to extract manufacturing dependent parameters automatically by linking a 3D-file to the calculation. This will reduce the number of steps required to get to a detailed calculation. Additional parameters available in stamping geometries can be easily synchronized with part cost calculations. Further enhancements in the 3D viewer are showing product and manufacturing information, selecting a different background color and much more. These not only increase end-user productivity and improve data quality, but also empower end users to work more efficiently.
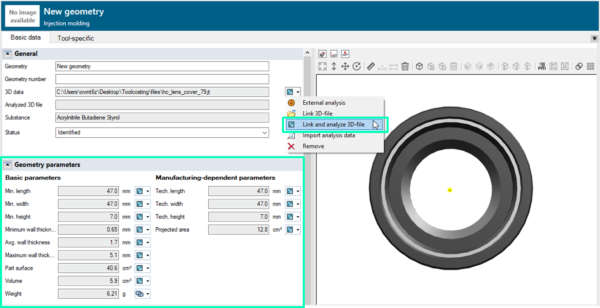
We provide enhancements in the cost engineering (should costing for purchased parts) area, so users can perform costing based on up-to-date data and consistent methods to achieve transparent, comparable product costs.
More flexibility for should cost calculations with the extended technology cost model
We have increased the usability that allows users to work directly with technology cost models without opening Excel files. Easy execution of the technology cost model by extending the trigger to all configured properties instead of only the material classification properties like it was in previous versions.
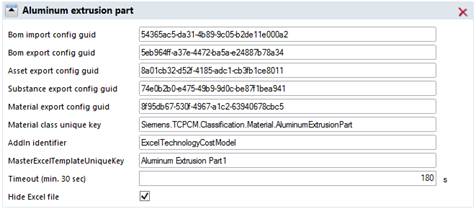
Maximize the value of your cost and carbon footprint calculations with new reference data
Cost engineers can perform timely and precise should-costing with newly added machines to support additional manufacturing technologies. These are new machines in the classes cylindrical grinding, lapping, sliding headstock lathes, and stamping. In addition, we updated the energy, technology, and cost data of ~170 machines to deliver reliable data for an accurate cost calculation.
Within the production sites area, we updated the energy prices and interest rates which offers users the possibility to leverage more accurate cost data within the scope of a purchased part price analysis.
Procurement can make the best decisions possible during negotiations with updated material prices and overhead rates (MPOR) to meet the latest price development. Therefore, regional data for EMEA, AMERICA and APAC have been added to the global average price data. ~8,200 MPOR-specific substances extend the product scope. This substance extension enables cost engineers to use the mass calculator for 99% of the materials, and 50% of the materials can now be used also directly in the cycle time calculator.
To provide access to the most up to date CO2e emission data for materials and energies, Siemens Digital Industries Software announced in September 2022 its collaboration with sustamize GmbH, a leading ClimateTech company providing professional technology, data and software solutions enabling companies to measure, optimize and manage CO2 emissions. This supports the calculation of the product carbon footprint and scope 3 emissions (for purchased parts and external services) with the capability to add additional category data sets based on demand. sustamize’ technology enables automated product carbon footprint management with one of the world’s largest CO2e database and intelligent algorithms, so the Product Footprint Engine is based on scientifically researched data enriched with more than 20 years of industry know-how and validated according to ISO 14048 by DEKRA.
With this new release, we provide updated material and energy data. The material data includes ferrous metals and alloys, nonferrous alloys and plastics and polymers. The energy data includes energy mixes for 52 countries and 4 regions. Further we deliver data for the cost factors oil and gas.
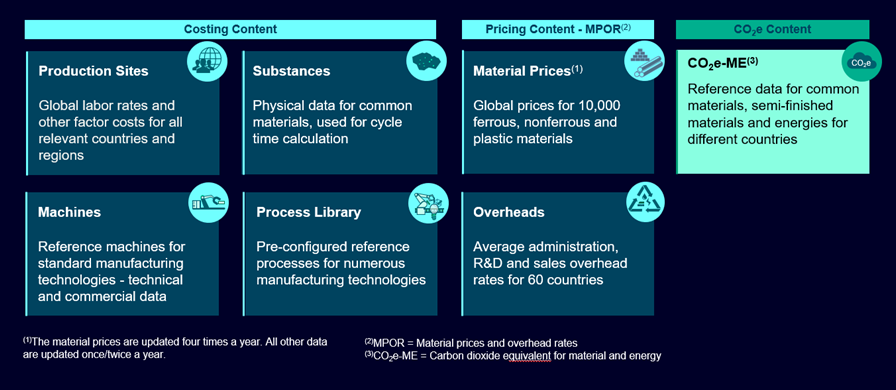
We provide enhancements in the Quotation and Profitability Calculation area, so users can perform accurate proposals and win projects with the desired economic success.
More precise quotes by supporting increase rates for materials in multi-year lifetime calculation
With the new version, extensions for the lifetime calculation are available. The calculation accuracy for manufacturing costs during the product lifetime will be increased by supporting work center activity rates which are changing over time.
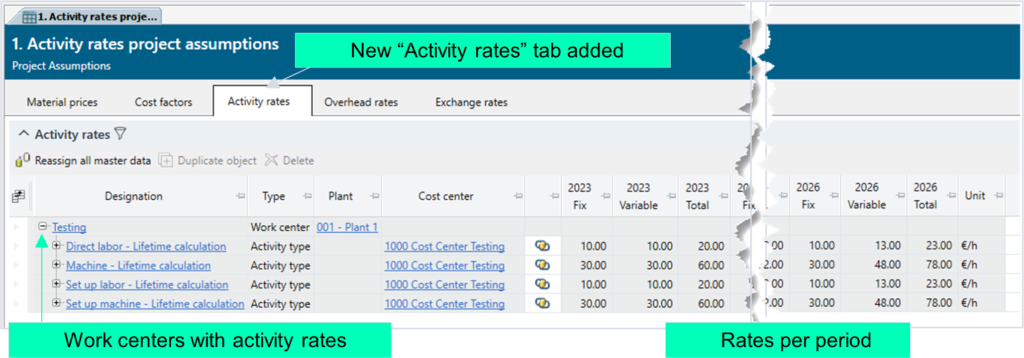
Easily calculate product sales prices based on cost calculations
The Pricing Calculator for Quotations is targeted for sales users who need to create pricing calculations as a response to request for quotation from their customers. Often sales users need to create copies of cost calculations or export cost breakdown into spreadsheets. While cost estimators continue to make changes on costs after the copies have been created or cost breakdowns have been exported. So, it becomes cumbersome to keep costing and pricing synchronized. Failure to react on cost changes often leads to loss of profit for companies.
With the Pricing Calculator for Quotations sales users can easily create a pricing calculation based on an existing costing calculation. Pricing calculations are used to add profit on top of costing calculations that are based on real production prices and are created by cost estimators. Pricing calculations are exported as cost breakdowns and used in negotiations with customers. After a cost calculation was updated, the sales user can synchronize any changes from the cost calculation into the pricing calculation. The new capability can document and visualize all updates made between cost and price calculations. This makes it possible for sales users to do their job faster and reduce the risk of losing profit.
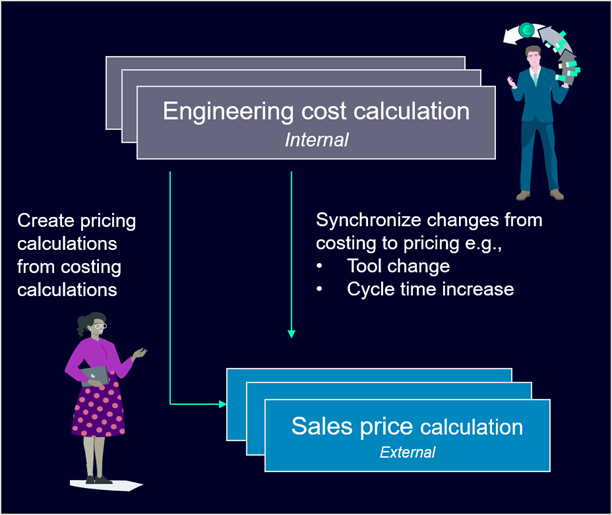
Further, the master data in Teamcenter Product Cost Management used within price calculations leads to increased price consistency in customer negotiations.
Project and profitability incomes can be synchronized with price calculations and the costs can be synced with cost calculations. This solves for example the use case where a machine is purchased for a different price than it is sold to customers.
Further improvements in Teamcenter Product Cost Management
In this chapter we summarize further enhancements such as:
- User interface and usability enhancements in the full text search and information messages for external steps
- In the calculation core foundation, the following enhancements are available:
- Users can see a new dialog when selecting a qualification cost factor.
- New user validation with “not contains” and “not contains field operators” can be set up
- In the cost engineering area improvements within the injection molding cycle time calculator are available
- In Teamcenter Tool Costing the user experience of the NX Feature2Cost module has been enhanced
Interested in more Teamcenter Product Cost Management details?
To get more details on the improvements mentioned in this blog post have a look at Teamcenter Product Cost Management version 9.6 (for registered customers only) and check out the other product cost management blogs.