Enhancing ETO Assembly Planning with robust change management
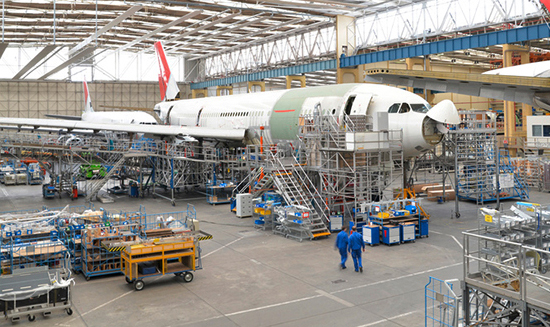
Manufacturing assembly planning in the Engineer-to-Order (ETO) industry is plagued by several challenges, including frequent engineering changes, complex workflows, tight deadlines, and rework. Unlike mass production, where processes are repeatable and predictable, ETO manufacturing—especially ETO assembly planning—requires constant change, frequent engineering revisions, and complex coordination across multiple teams.
Managing these variables is a significant challenge as it can disrupt production schedules, complicate resource allocation, and lead to costly delays.
To navigate these complexities, ETO manufacturers need a robust planning tool that streamlines change management and improves coordination among teams. A comprehensive platform that integrates engineering data with manufacturing planning ensures real-time communication of every change across all departments. This seamless flow of information helps manufacturing engineers, manufacturing planners, design engineers, quality engineers, shop floor engineers, and industrial engineers stay aligned, adapt quickly to changes, and maintain production efficiency.
In this blog, which is part of an upcoming series on ETO manufacturing assembly planning, we will first examine how integrating all stakeholders through a task-based approach can make manufacturing planning more seamless and effective in the change management process. We will explore how to navigate the ETO change process when manufacturing and assembling an aerospace component in the forthcoming blogs.
Task-based strategy for improved ETO assembly planning
Managing assembly planning during an engineering change process in Engineer-to-Order (ETO) manufacturing environment can be a cumbersome task. It requires design engineers, manufacturing engineers, manufacturing planners, industrial engineers, shop floor operators, and simulation engineers to work together seamlessly. When these roles are well-aligned, it minimizes the impact of changes on downstream activities, leading to better communication and smoother coordination. This collaborative approach helps teams handle engineering changes more effectively, keeping production on track and ensuring that what is designed, is manufactured to the highest quality standards throughout the process.
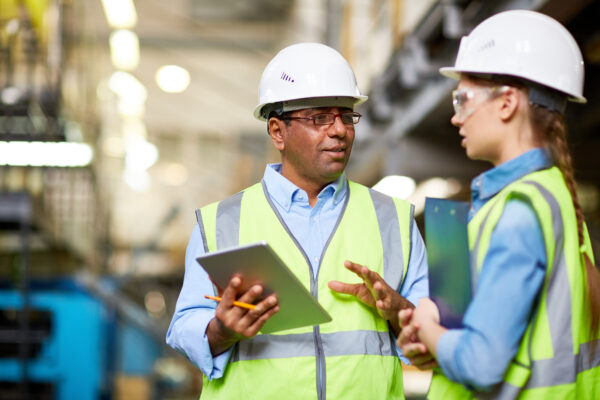
To achieve this seamless integration, each stakeholder plays a crucial part in tasks such as BOM management, process planning, work instruction authoring, and process validation, ensuring that the transition from design to manufacturing is smooth and effective.
BOM Management
When the product design and engineering team issues a change, such as a part modification, the Manufacturing Engineer must update the Manufacturing Bill of Materials (MBOM) assemblies to reflect the new Engineering Bill of Materials (EBOM) parts. This EBOM-MBOM reconciliation ensures a direct link to the design definition, providing a verified MBOM with controlled changes and traceability to design requirements. The Manufacturing Engineer is responsible for creating and updating MBOMs based on the latest EBOM and geometry, ensuring that design changes are accurately reflected in the manufacturing process.
Process Planning
After an engineering change, it’s crucial to redefine process plans based on the updated BOM. Using a standard process development framework with a Bill of Process (BOP), the Manufacturing Engineer creates a detailed plan that aligns with the new requirements. The Industrial Engineer then focuses on optimizing production efficiency by analyzing the impact of these design changes on the assembly process and the production line. This includes creating time analyses for different stations and balancing workloads to ensure the production line can handle the new requirements efficiently. Adjustments to resources and work cells help minimize downtime and maintain smooth production operations.
Process Validation
The Simulation Engineer plays a pivotal role in validating assembly plans before they reach the production floor. Using advanced connected simulation and validation tools, they create dynamic 3D simulations of the assembly process to thoroughly test and validate each step. This ensures that all components align as designed and that assembly procedures are both efficient and error-free.
The process validation is completed before authoring the work instructions (WI). Once validated, the WI are authored and released. Should the validation reveal any issues, adjustments to the process or tooling are made accordingly. By simulating the entire assembly process in a virtual environment, the Simulation Engineer leverages manufacturing process planning data to identify and resolve potential issues early, significantly reducing the risk of costly errors or rework in production.
Work Instruction Authoring
After process validation and adjustments to assembly plans, necessary changes are implemented. Configuration-driven work instructions are then created from the Bill of Process (BOP). Leveraging existing engineering and reference data, these instructions undergo controlled document revisions to ensure accuracy. Once revised, the instructions are released to shop floor operators, who review them alongside the updated BOM to ensure that component assembly is completed correctly, on time, and to the highest quality standards. Shop floor operators play a critical role in executing these revised procedures accurately, ensuring that all changes are reflected in the final product while maintaining overall production efficiency.
By integrating these roles and processes, ETO manufacturers can streamline assembly planning, even amid complex engineering changes, ensuring production remains efficient, accurate, and aligned with design intent.
Learn more
Stay tuned for our next blog, where we’ll explore how the ETO industry manages change processes—demonstrated with an aerospace component—using Teamcenter Easy Plan for MBOM management, bill of process (BOP) management, and the authoring and sharing of electronic work instructions.
In addition, explore how integrated collaboration can transform your manufacturing processes by enabling seamless process planning and simulation in a connected, collaborative environment. Sign up for the manufacturing planning trial, tailored to the ETO industry from an aerospace and defense standpoint.