Why Do We Need Multi-Body Modeling?
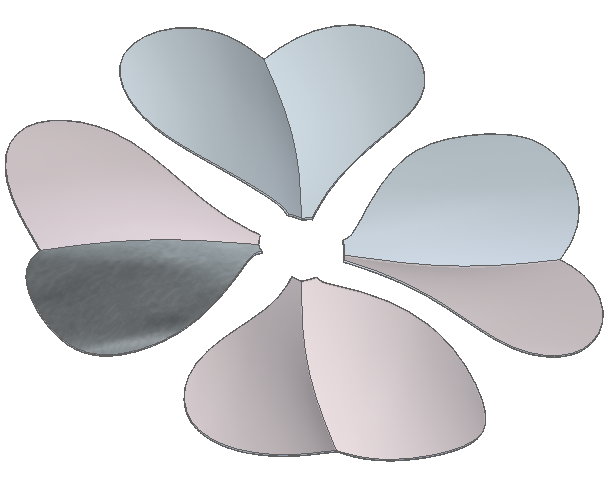
This is going to be a series of blog posts covering the topic of multi-body modeling (let’s call it MBM) in Solid Edge. It has taken me a while to get my head around this topic because it is significantly more complex than other multi-body implementations I’ve used. This first post will mainly be an overview of MBM concepts. In a second post, I’ll go through the specific tools that are involved, and how they work. In the third and final post I’ll show some actual techniques where you might use MBM methods to their best advantage.
Many “best practice” concepts for MBM are transferable between CAD packages. Best practice itself is a continuum from the most conservative, risk-averse “safety first” attitude on one extreme to high-risk, speed and ease of use centered philosophy on the other extreme. MBM best practice mostly boils down to balancing functionality you are willing to give up against a little convenience. MBMis not inherently risky, but file management, associativity, and editability can all become more complicated in MBM scenarios.
You may hear the argument that complex assemblies can be replaced with just a single part file that contains all the parts right inside it. While there are CAD software packages that are intended to work this way, Solid Edge is not one of them. Solid Edge has an assembly environment for a lot of reasons. MBM is not going to replace assemblies, but will enable you to do more with part design, enable certain functions that use tool bodies or external references, and may help you get to an assembly more quickly.
You might be thinking “multi-body modeling? I don’t need no stinking multi-body modeling.” And you might be right. Or maybe you do need it, you just don’t know it yet. To be fair, 10 years ago I was a big opponent of MBM. My argument was that you could do everything you needed to do in assemblies. I felt that MBM was just a sloppy shortcut, a lazy method, or a cheat. I still think that there are a lot of “illegitimate” uses of MBM, but I recognize some of the benefits. I recognize that the word “illegitimate” sounds pretty judgmental, but I do believe that some methods have more value than others. In the course of these blog posts I’ll lay out my reasoning, and you can make the decision for yourself which methods you will adopt and which you avoid.
Is there anything for which you absolutely must use MBM? Continuous shapes between parts is one thing that comes to mind. You design a car body as a single part. You don’t design the awkwardly shaped rear fender, then try to make the door flow smoothly into the fender. You model the entire car shape a single part, then break it into multiple bodies, then separate those bodies into individual parts. This is a common technique used in many types of design known as “master model”. We’ll get back to more detail on this later on.
Is there anything that you absolutely should not use MBM for? Generally, don’t get caught in the trap of using a multi-body part where you should use an assembly. There are several things you can’t do with MBM, such as the motion of mechanisms, BOMs, drawings, etc. I believe that if you are going to use MBM techniques for something, you need to have a plan. Your plan might be to just investigate, or experiment. Or it may be a master model approach. Or possibly you have a body you need to use as a tool to create a shape in another body, or maybe the multi-body state is a temporary state before the finished solid model.
There are many possible reasons for using MBM methods:
- Bridging between volumes that don’t touch (rim and hub)
- Toolbody (Emboss feature)
- Inseparable subassembly (captive washer on bolt)
- Overmold (toothbrush handle with multiple materials)
- Surface modeling (surfacing is inherently multi-body)
- Reusing design data from other parts (insert part copy)
- Patterns (patterning bodies is faster than patterning features)
- Master Model method (mouse shape divided into multiple buttons, covers, etc…)
These are just some of the common uses of MBM, I’m quite sure there are as many reasons for using it as there are people who use it.
Multi-body methods in Solid Edge have existed for years, but it wasn’t until ST5 (2012) that Solid Edge really went through and revamped all of their functionality. The result is that Solid Edge’s implementation of multi-body modeling has a few extra layers in it that I haven’t seen elsewhere. Solid Edge gives you more control, and when you consider that there are Ordered and Synchronous implications to multi-body modeling, there is a lot to know about Edge’s MBM methods.
In this post I hope to have whetted your appetite if you are not a current MBM user. In the next couple of posts, I’ll show more detail about what features are available that use these methods. I think you’ll find that the Solid Edge implementation offers you a lot of options that other CAD software may not. In the meantime, it would be great to hear from some of you that are already using these techniques, what sort of work you are using them for. Pix are always welcome in the comments!
Comments