Interview with Dick Gebhard, father of Resilient Modeling Strategy
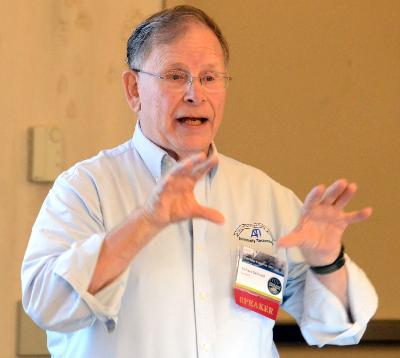
I first met Dick Gebhard at a Solid Edge University event. I knew right away that he would be a one-of-a-kind sort of acquaintance. It turned out that the presentation he was giving (on his new Resilient Modeling strategy) and the presentation I was giving (on the best ways to use Synchronous Technology) overlapped quite a bit, so we spent some time talking about this. I actually went back to my room that night and updated my presentation to include some of Dick’s ideas.
To really get the full effect here, you have to realize that Dick has a great sense of humor about things. I have never laughed so much when putting together one of these interviews. He describes himself variously as a “progressive, pragmatic, curmudgeon” and his company as “…a one man band with a trained duck…” Yeah, you have to read the whole thing to see that in context.
This article turned out much longer than my target (more than twice as long, in fact), but I just couldn’t cut any of the technical or historical content or the great gags. No matter how you look at him, Gebhard is a classic.
Let’s listen in on the conversation I had with him a couple of Fridays ago…
I haven’t heard from you for a while, what are you up to?
The reason you haven’t heard from me is that – Resilient Modeling Strategy – is going great so I’m coming up with a sequel.
Be careful – in the movies, the sequel isn’t always better than the first. Are you going to call the sequel
“Resilient Modeling Strategy II”
Matt you’re a great straight man; this interview is going well. I will admit I considered “Resilient Modeling Strategy II” as well as “Resilient Modeling Strategy – the rest of the story” but I settled on “Resilient Assembly Strategy” or “RAS” for short.
First of all I need to give you a status report on the original Resilient Modeling Strategy (RMS). It’s been online in its present form for about 7 months. I am pleased with how the activity has been steadily increasing. In the last 7 months I had 15,484 page views, 2,597 new visits to the site and 1,040 return visits to the site. Here is some of the visitor activity just this morning: Michigan, Seattle, China, UK, Some-place-I-can’t-pronounce, and Finland. I have been surprised at the amount of international activity.
But the most important thing is that Resilient Modeling Strategy is being mentioned in blogs by bloggers such as yourself, Evan Yares, Jennifer Herron, Scott Wertel, and a whole bunch in Asia that I would need a translator to read. I’m getting a lot of referrals and there is no negative feedback. So it’s obviously a subject of interest. In summary it’s going along nicely. Keep in mind nothing in Resilient Modeling is new, its purpose is to bring CAD best practices all together in a universal CAD neutral format.
Finally let’s talk about the sequel: Resilient Assembly Strategy or RAS. Are you familiar with Skeleton Modeling?
Yes, it is a popular technique to manage inter-part relationships. I believe ProE and Inventor have included it in their training collaterals.
Resilient Assembly Strategy (RAS) is not about part modeling, Resilient Modeling Strategy (RMS) handles that by organizing the feature tree and grouping the features. Resilient Assembly Strategy (RAS) expands on the skeleton model concept to manage the work flow as well as the interpart relationships that result from a “Top Down” design.
If you look at product design from a product structure point of view, you have a team of people such as engineers, designers, detailers and analysts all working on the same assembly. They want the design process to move smoothly and in parallel. The interaction and dependencies between parts prevents the design process from proceeding as desired. Rather than solving the logistic and communication problems, often a bigger bottleneck is created by assigning the design to just one author.
Resilient Assembly Strategy is about using virtual models (models that don’t appear in the parts list) such as skeleton, shape and morph models to capture the critical assembly keypoints as early as possible in the design process so that the model you’re working on isn’t holding up someone else.
We also want to utilize our resources so that the power users are doing the core group of each model and then turn it over to detailers, who complete the model. The core of a RMS model is actually stand-alone from a functionality standpoint, it has all the assembly hooks, and everything else. The power users are doing what they do best, and the detailers are learning how the process works. The detailers are working with the power user who started the model so there’s a natural apprentice relationship. And because each model is being brought to its core first, and then after all the cores are done, brought to the detailing phase, the final assembly looks like a dynamic progress report.
In summary, Resilient Assembly Strategy allows you to use your design team much more effectively and streamlines the design process
So Resilient Modeling allows you to divide the model to virtually eliminate these nasty parent-child relationships that make the model uneditable but at the same time you’re subdividing the model by skill level. You are the master designer, but because it’s a known format, you can turn the work over to someone else and move on to the next important task.
That’s exactly right, but there is more. Another RAS Concept is the use of “morph” models. Morph models are models created early in the design as a primitive solid model focusing on keypoints. The model then morphs as the design matures into the final model or often more than one model.
I am sure you know what a car steering knuckle is, imagine we have one of those. Now think of it as 3 parts: a top plate, a bearing carrier, and a bottom plate. The steering knuckle is a critical component because it affects toe-in, bump steer, camber, caster etc. It’s a rigid three part assembly when you get done, but it only has 5 critical attach points.
Think of a Formula 1 car with wishbone suspension. Two wishbones, one connecting to the top plate of the steering knuckle, and the other to the bottom plate. The steering knuckle also transfers the road forces to the suspension through a push / pull rod, supports the wheel bearings, and provides the linkage for the steering. To make matters worse it is 100% un-sprung weight but can easily be a failure point if it isn’t strong enough. Race car suspension requires a lot of design and the steering knuckle is a keystone suspension part.
So, the idea is that we start with a “morph” model. Think of this as four spheres and a cylinder. The cylinder is where you attach the wheel, and the wheel just goes around, thus the cylinder. The spheres are the attach points for the upper and lower wishbone, steering, and suspension.
I place these 5 things as surfaces into my “morph” model. Once I’ve got these joined together as temporary solid and placed it in the assembly, the steering knuckle is out of the critical path. The surface entities in the “morph” model are like placeholders for the critical points for the assembly, but everyone can work on whatever else they need to work on because those important relationships are already established.
Morph models sound cool and the name certainly is descriptive. Do “morph” models replace multi-body Parts?
When we have a group of parts that have a lot of interaction, RAS starts a multibody part with a skeleton and a “morph” part. As the design progresses, the “morph” part evolves and splits into the final parts while maintaining constant assembly keypoints to avoid disrupting the design team.
Resilient Assembly Strategy also has a very interesting approach to multi-body publishing. Each body is grouped – but we’re grouping parts not features now. The first part group in the multi-body part is a skeleton model.
For each part, the rules are very simple. You can link to the skeleton, but you can’t link to another part. For example: in a multi-body part, suppressing a part group named “bracket” will not result in any errors because there are no links between groups
I can now publish a multi-body part by “copying and deleting” with each part retaining its complete feature tree. For example – to publish a multi-body part with 4 bodies plus the skeleton, you would copy the multi-body part 4 times. For each copy – rename it with its final part name and delete or suppress the other 3 bodies but not the skeleton.
How do you handle products that rely on their “skin” for appearance or performance?
For this we have a virtual model called a shape model. The “morph” model established critical joints between parts in the assembly early on so it is out of the critical path. The Shape model does the same thing with the outer shape of the assembly. It’s completely independent of the final part, but exists in the assembly, often only as surfaces. Its content varies depending on the product type.
For instance – In an airplane, the shape model is everything. It is a design project on its own. The shape is tested in wind tunnels and everything is analyzed before you even start the detail design. You don’t design an airplane rib by rib.
Visualize a kitchen mixer – it has a motor, gears, switches etc enclosed with a shell. The shell must be pleasing to the eye but the functional parts provide rigid constraints (I can’t bend the armature to make the motor fit the shell).
The shape model is usually a continuous single surface. Eventually some of the functional parts are going to mount to the surface or use the surface to define their visible faces. Regardless of how many parts you have in your assembly, you’ve always got the shape model to copy surfaces from.
All of these virtual models have inter-part links during the design phase of the project. This is ok, as long as you delete every one of them before you release the product. Matt – You’re chuckling because you’ve obviously encountered this before.
Yeah, when I was writing a lot of best practice for another CAD product, many, many users were so terrified of in-context design that required users to remove all relations at the end of the project. The problem was that some relations can’t be edited out, they can only be made into a bit of a dead-end feature in the middle of a live-feature tree.
So that gives you a very crude overview of Resilient Assembly Strategy. I think it’s going to be as useful as RMS. If you are an experienced designer, everything I said will resonate. RAS pulls together and builds some structure around some of the best practice techniques for building models. As with RMS, There’s nothing revolutionary here at all, but what are the consequences of not doing it?
Why is this project CAD Neutral rather than aligning with a CAD vendor?
Best practices are an industry problem that doesn’t need to be solved by creating another proprietary solution. By being CAD neutral these best practices remain universal rather than being exploited by a CAD vender to blackmail users into switching to their product.
The present epidemic of irresponsible solid modeling stems from the fact that the majority of CAD users either learned CAD by discovery or by attending a training that focused on learning a particular CAD interface. The repertoire of CAD functions hasn’t changed much since 1992 because as issues developed, the CAD developers often solved them by adding “super features” or exception functionality to their interface.
The principles of Resilient Modeling and Assembly are universal and only need to be learned once. The features and functionality or RMS and RAS are common to all feature based CAD systems. Having said that, direct modeling environments such as Creo, Fusion, or Synchronous Technology have the potential to enhance the Resilient Modeling process particularly in the “core group”, but their use is CAD program specific.
CAD vendors can still support CAD neutral Resilient Modeling by adding optional functionality for RMS rules checking and by streamlining the “grouping process”.
What is it that gives you such insight into the problems of solid modeling?
Matt – I’m not charismatic, articulate, or blessed with great insight. I have been described by Michael Hadley my coconspirator on this project as a “progressive, pragmatic curmudgeon”.
Since 1985, I have sold, trained and supported 3D CAD:
· CADkey – 1985 to 1998
· Pro/E – 1992-1999
· Solid Edge – 1999 to 2014
In 1993 Jack Napoli, (my mentor at PTC) described my company to the PTC management as follows:
“Assembly Technology is a one man band with a trained duck, and I think the duck is leased.”
For 30 years I’ve done everything, sales, training, and support for 3D CAD in Arizona. I’ve seen it all – I’ve been involved in an incredible number of political as well as technical issues in the Arizona CAD community. It’s ironic that examples of worst practices are much more prevalent than examples of best practices. If you see enough bad practices, even the most thick headed with finally see the light, and the world will declare he’s blessed with insight. So don’t confuse repetition and brute force with insight.
The good news is that I have learned some things from this project:
· I usually always spell “quarantine” right,
· I would be considered illiterate without a spell checker
· The idea of a benevolent CAD vendor is absurd
· Editing an interview can make anyone seem articulate
So how are you turning this into money? Consulting? Training?
Matt, you’re old enough to remember the phrase “That’s the $64,000 question”, right? Of course when that phrase was first used in the 50’s, $64,000 was like a million today.
Unfortunately for me, I did too good a job on the Resilient Modeling website because it is stand alone. CAD users can watch 7 videos (45min max) and they get it. Resilient Assembly Strategy continues my quest for CAD neutral best practices by attacking productivity and assembly issues.
The kind of things I am doing really don’t inspire CAD vendors because they can’t see a direct link it to revenue and I have the same problem. This is exactly why after 25 years of main stream use, so many basic solid modeling issues remain unresolved. I have faith that if my “Resilient” project content has value to the solid modeling community, I will be eventually be rewarded. How it will happen isn’t clear yet, but since I am president of the company (Assembly Technology Inc) I don’t have to justify my projects to management.
When will this be ready for “Prime Time”?
This is my plan for 2015 Q1:
· Add an overview of Resilient Assemblies to the Resilient Modeling website.
· Finalize the RMS and RAS material into an onsite presentation format
· I will first present it at a local (Phoenix) Solid Edge user group meeting
· I will then Beta test it at select local Solid Works and ProE companies
After the beta testing, If I still think the content has value, Michael Hadley or myself (Richard Gebhard) will be available for onsite one day audits or presentations.
Comments