How 3D Simulation Impacts Design Early on in the Process
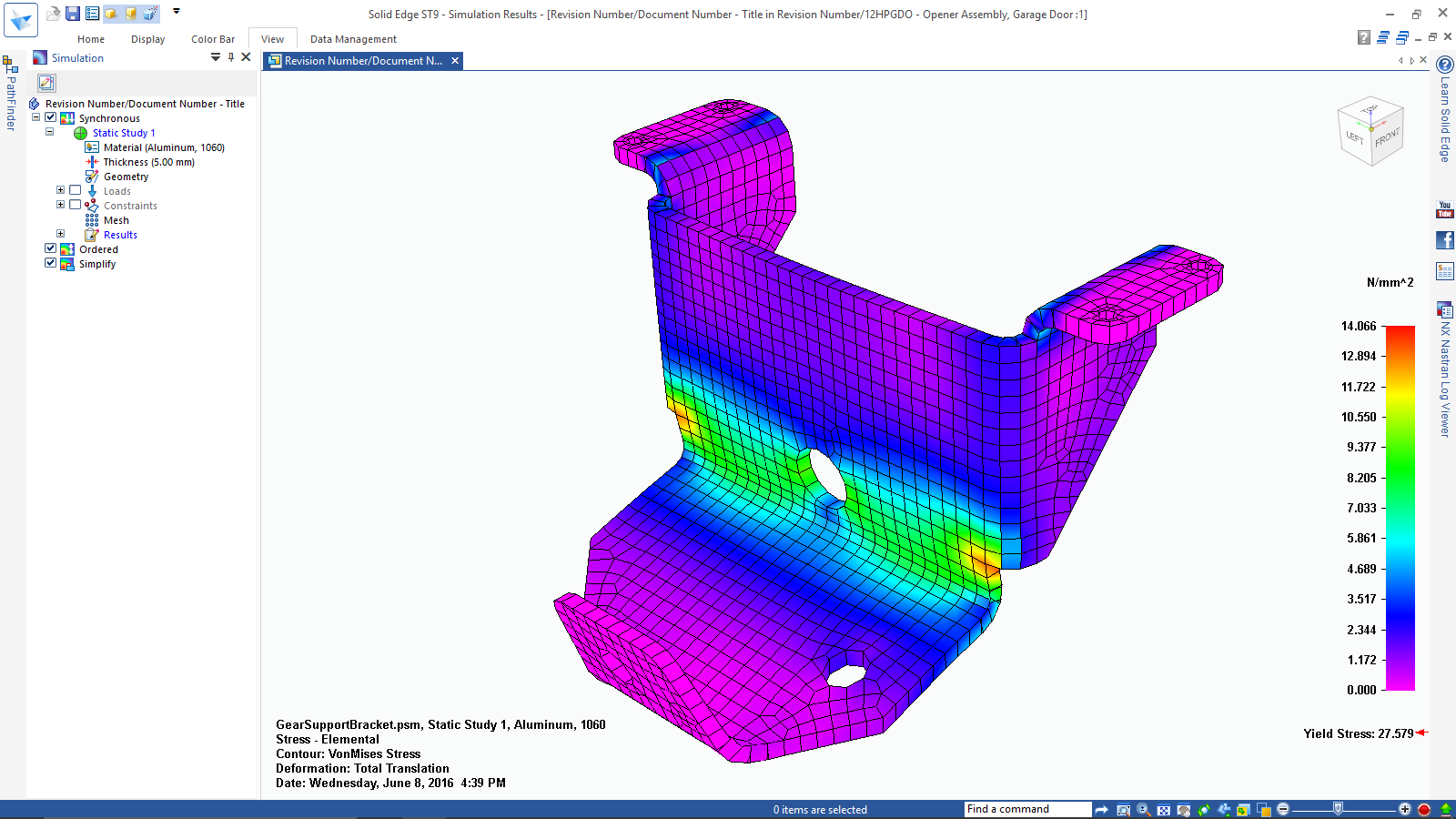
Innovating and bringing new products to the market can be negatively impacted in a micro managed environment with highly constrained and detailed product schedules. This hurts the product development process.
The problem is that many companies treat product development as if it is a repetitive process with predictable outcomes, which might be true in the actual manufacturing process—but not when a product designer has to develop something new and innovative that will perform optimally in the real world due to the many unknowns when creating, developing and testing a new concept.
More resources can actually mean less innovation
Many companies decide to maximize their usage of resources already in place in developing new products, but the law of diminishing returns comes into play—higher number of feedback loops in the team slow down decision making. Also, there is no leeway or slack available to compensate for delays. Ultimately, this is at the expense of innovation.
As the number of tasks increase it becomes even more difficult to find the bottlenecks. The result is that information is simply lost and people do not have the time to explore every possibility, so invariably there is a backlog of tasks and projects forcing people to take shortcuts. Even after building in extra capacity, executives want to leverage current resources to the maximum to justify the investment but this does not necessarily increase innovation.
There are however a few ways to overcome this state of affairs:
- Align the tasks and objectives across the organization
- Increase resources while also allowing more open collaboration between teams
- Reduce the number of initiatives
- Allow greater visibility into the backlog of tasks
Innovation comes from iterating more, and failing earlier
By following the guidelines above, people have more time to find the potential failures in a product and explore alternative product design solutions, resulting in more innovation—experimenting and analyzing can reveal what works and what fails. Failures that are caught early on in the process result in a design that will perform better and cost less to repair and service.
Simply put, more failure leads to more innovation.
For product developers, having the freedom to brainstorm, experiment and try different ideas is very important in order to innovate. Discovering which concepts fail and which succeed through frequent collaboration and rapid feedback loops is important, because it eliminates the bad ideas early on and helps the team to focus on what works.
Finding out that a jet engine will lose thrust under specific atmospheric conditions, or learning through a crash test which areas of a design are unsafe, or discovering what wind forces a 100 story building can withstand are important aspects to know very early on. Unfortunately, product development teams are often under pressure to get it right the first time.
Without time to experiment, product teams avoid risk
When product teams have to make sure they are successful from the beginning, they usually choose the path of least resistance and low risk. As a result, there is little improvement or innovation in the product being developed due to a lack of incentive to find the innovative solution. Additionally, when product development stage gates are inflexible and scheduled without any slack with dependency on the successful completion of the previous stage, many resources are committed and aligned making the costs to respond to new product specifications or changes very expensive.
While project milestones are achieved, there is a lot of risk and cost associated to solving or improving any issues that come along the way. As a result of such product development processes, bad ideas stay in until a critical situation is discovered, making it expensive to fix. So, the focus should be learning where the team got it wrong first, and then brainstorming quickly to come up with new ideas and solutions to explore through a highly collaborative and iterative product development process.
Simulation earlier in design results in superior products
Finding points of failure very early on helps in the awareness, collaboration and execution of actions needed to innovate. This is where simulation is critical to having a better understanding of the points of failure in a design in order to improve it. Trying to get the design right the first time, and relying on simulations and prototyping only to validate complete designs, results in critical issues much later, when they are more difficult and more expensive to fix. Taking more time to iterate in early design stages, instead of delaying time-to-market, can actually speed time-to-market, by moving these changes earlier in the design cycle, when they can be fixed more easily. In addition, adopting an iterative approach—using real time simulation and prototyping, executed frequently—will result in finding more errors and points of failure, and bring superior products to market.
The bottom line is that focusing on getting a product design right the first time automatically encourages the adoption of the least risky solution. Meanwhile, product simulation software allows a designer take some risk by executing multiple alternatives to find the best performing product confidently.
Embrace failure as a data point
It should be clear now that any experiment that results in failure is not necessarily a failed experiment. It’s an opportunity to learn. It’s another data point of information that can be shared and with input from stakeholders, results in more ideas and information that the innovator was not able to get earlier. All the new information resulting from the process of additional experimentation and feedback loops can be analyzed and used in the next set of experiments to push the limits of the design by exploring more innovative solutions.
This step by step risk taking results in product designs that outperform in the real world. Simulation software is at the core of the innovation process when used in such a manner.
The development of the SpaceX program is one example of a breakthrough in innovation as the team knew they were going to fail along the way but used software tools, which included product lifecycle management (PLM) applications from Siemens PLM Software to manage the risk at each stage of the design development. This great video clearly shows the iterative steps:
With advanced tools such as simulation software, companies can innovate, collaborate and develop better products at a lower cost and in less time.
Tarun Tejpal
Improving the way customers use 3D & Enterprise Software on the Cloud | IoT | AR + VR
https://www.linkedin.com/in/tejpal
@TTejpal
Editor’s note: You can try out Solid Edge’s built-in finite element analysis (FEA) tools, which allow design engineers to digitally validate part and assembly designs within the Solid Edge environment, as part of our free trial.
Comments