Digitalization of the Design Cycle for Aerospace Suppliers
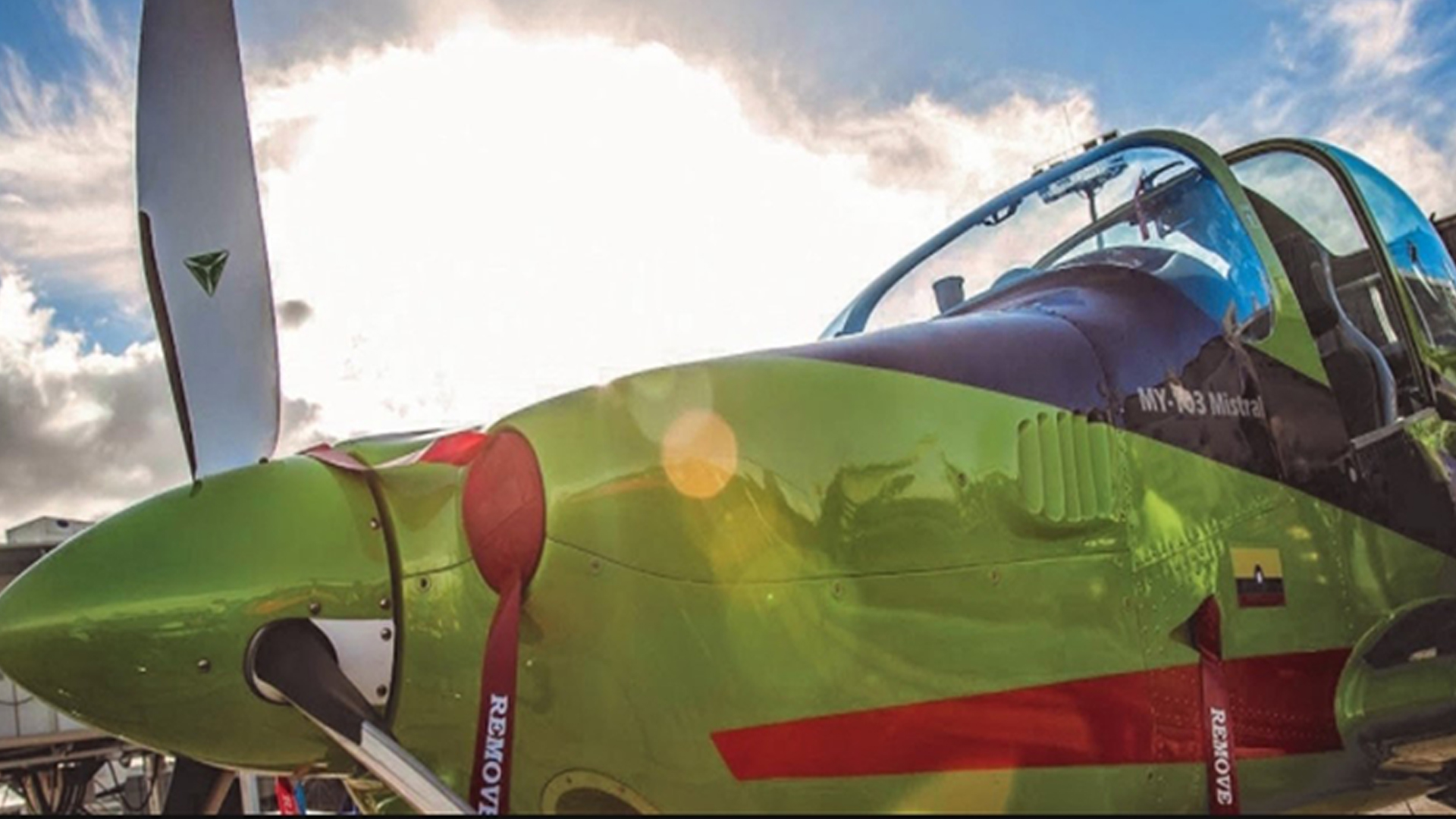
There’s little doubt about it: there is no shortage of new challenges in the aerospace industry. And those issues aren’t just for the prime contractors and tier-one suppliers. They’re trickling down. Established approaches and solutions do little to help addresses these problems. Thankfully, a range of progressive technologies can help. In this post, we’ll explore all these issues.
Challenges Abound
One of the most significant trends in the aerospace industry is the change in funding. Today, there are fewer programs. Those that are running are operating on smaller budgets. To get a piece of a program, contractors must bid more aggressively, and work under very tight schedules along with uncertain program requirements. This trend trickles down to Tier 2 and Tier 3 suppliers as well, and profits can take a hit as a result of overspending, late delivery charges, or regulatory compliance penalties.
Despite the shrinkage of programs in the industry,systems are still getting more complex. Over a decade ago, Tier 2 and Tier 3 suppliers almost exclusively won contracts for parts. But today, OEMs are outsourcing entire systems to prime contractors and that complexity is making its way down to Tier 2 and Tier 3 companies as well. These contracts require a broader engineering skillset, which can make hiring a lot more complicated and expensive.
Lastly, regulations are becoming stricter, and suppliers must comply. Since smaller companies have fewer specialists that are aware of these criteria, there is a much higher risk of error. If your designs don’t match up, it’s back to the drawing board.
Needs for Detailed Design
Changes in the industry are driving adjustments across development in the supply chain. One of those areas lies in detailed design. Ultimately, the goals for any supplier involved with these programs include:
- Developing designs that satisfy requirements, comply with regulations, meet cost constraints, and can be manufactured and delivered on time.
- Producing design documentation that downstream functional departments use in the development process.
The tactics to achieve those goals will vary from company to company. But in general, activities in this phase of development include:
- Developing mechanical designs and documentation.
- Verifying that the functional performance of the mechanical design satisfies requirements.
- Developing designs and documentation for electrical systems (harnesses)
- Verifying that the functional performance of the electrical system satisfies requirements.
Established Approach and Traditional Solutions
So what’s the established approach to getting things done in the supply chain? Manufacturers are using many different traditional solutions. Let’s run them down.
For one, documents and spreadsheets are still widespread for a variety of use cases.Engineers simulate product performance through spreadsheets and hand calculations. Requirements are defined and tracked in spreadsheets and documents. Of course, you can only predict so much with spreadsheets and documents. If the calculations are wrong, you’ve wasted a lot of time on a prototype that doesn’t work.
In this traditional approach, as engineers manage product requirements as files, different versions of this information can be spread throughout the company. This method can lead to many mistakes if there is a disagreement over which file is the correct file. In the end, you might encounter two interlocking components that don’t quite fit together.
Everyone needs to be on the same page to deliver a successful end product. With an old fashioned import-and-export system, product requirements are stored separately from the actual design files, meaning anything that deviates from the initial guidelines could go unchecked. If this one little change goes unnoticed, you may end up remaking the entire part, and you’ve lost not just time but a good bit of money as well.
Novel Approach and Progressive Solutions
We’ve run down the established approach used for some of the processes in detailed designs. What about the novel approaches and progressive technologies? One significant change is to manage requirements and designs in one system, allowing allocations between the two. Furthermore, engineers can leverage simulations and generative design tools to make better design decisions. Here are more details.
By managing both designs and requirements in one system, you have a lot less risk for human error. If the model does not conform to the guidelines at any stage of the process, engineers will immediately know and be able to make adjustments. Instead of scrambling to identify and find the right file, everything is in one place. There’s no risk of having multiple definitions of the same thing.
Instead of attempting to calculate results by hand, running simulations during the design process can prevent a lot of headaches. Of course, it’s much easier to do this when the model contains both the designs and the project requirements. When engineers conduct analyses during the design cycle, they can make better decisions before moving on to prototyping. Engineers can address potential problems early on, and there are fewer surprises at the end. Additionally, Generative Design can be used to eliminate any unnecessary weight from parts and play a significant role in saving money on materials.
With a single, unambiguous digital design definition, engineers can explore more design options with different modeling approaches, and determine which is the best fit. By exploring different modeling techniques, they can choose the method which saves the most time and money. There’s a much higher possibility of getting things right the first time. The more information and options available, the better the product.
Summary
Using digital definitions of your product throughout the entire design process will help your company avoid wasting time and materials. A digital overhaul for your organization may sound intimidating but the long-term benefits are indeed worth it. The demand for complex products will only continue to rise, and this is an investment that will help you keep up.
If this topic resonated with you, then you should consider attending our upcoming webinar on April 10th that looks further at digitalization across the entire product development process. You can register for the webinar here.
Comments