All about operation management systems for automotive suppliers: Advanced planning
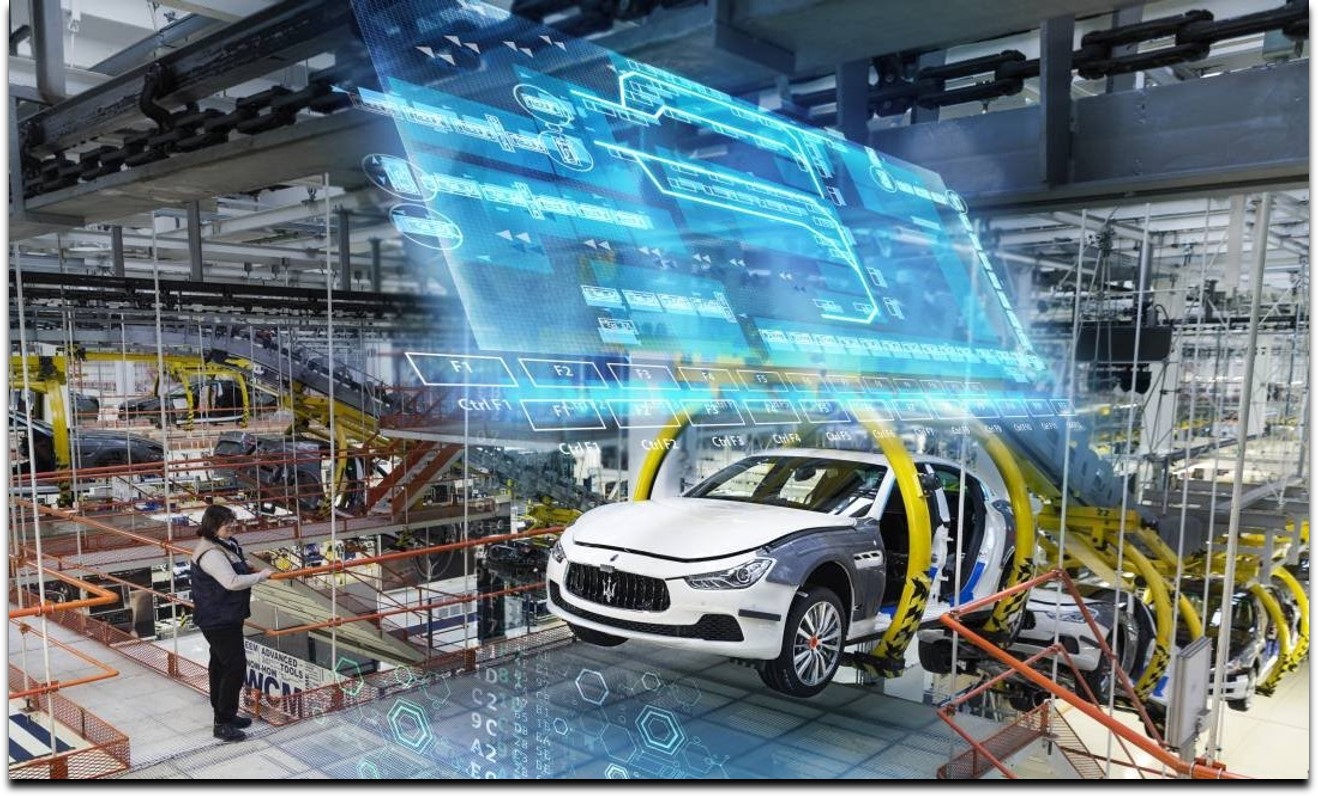
Advanced planning and scheduling software provides two halves of a whole solution.
The whole solution aims to provide better production planning and scheduling processes for auto suppliers of all types and sizes.
For simplicity and brevity, this blog will only focus on the first half: planning.
You need a plan before you can schedule
APS systems – like Opcenter Planning from Siemens – are a strategic decision-making support tool that look at the big picture of production.
Watch this webinar clip to learn how planning software works:
Planning tools consider forecast demand and stock orders to get a general direction of production.
The same tools can actively set target stock levels to meet future demand and load balance across multiple resources.
Overall, APS software can help with the production planning process by supporting major decisions to extend the workforce or resource capacity.
For more on the scheduling half of the solution, read the next blog in the series next week.
Watch the entire on-demand webinar and discover what APS software can do, how auto suppliers are using it, and learn how it compares to other solutions.
Planning and scheduling is more complex than most people know. Try this interactive planning and scheduling game for an enlightening and fun experience.
This is the fourth installment in a series of six weekly blog posts about APS software and the automotive industry.
Read last week’s blog to learn more: How do auto suppliers use APS systems?