Thermal fatigue: some hot features in Simcenter 3D Durability
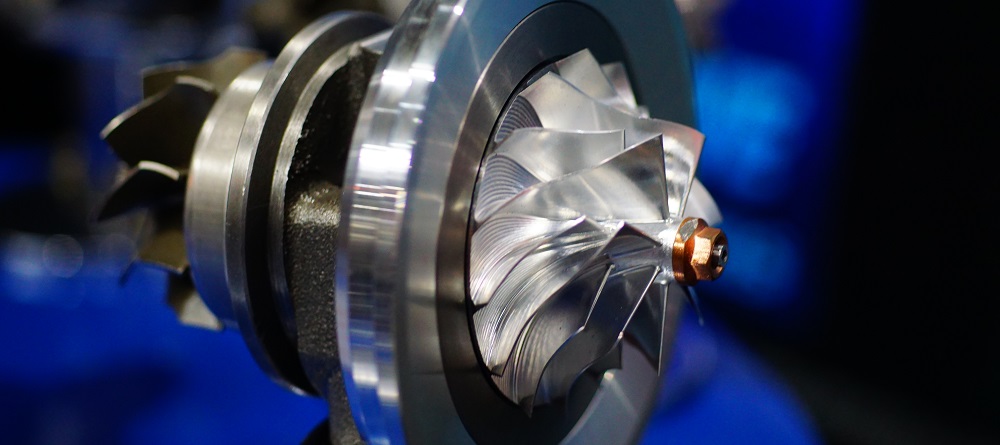
Fatigue failure, especially in safety-relevant parts, could ruin your brand name. Or it could even have hazardous financial and legal repercussions for your company if it could be held liable. So, fatigue life prediction is one of those analyses during design that can better be taken seriously. But what to do with components that are, for example, part of an engine? Or more in general, if they are close to a heat source? High and variable temperatures seriously influence material properties, and hence on fatigue! That’s where Simcenter 3D Durability for thermal fatigue can help.
First, let’s see what happens to your structure when it gets hot.
Mechanical properties change
At higher temperatures, several material characteristics change, including the stiffness – material generally becomes more flexible, and also the density – material usually expands. Therefore, for various temperatures, the same loads lead to different stresses and strains, and consequently to different thermal fatigue behavior.
But Simcenter 3D can take these phenomena into consideration. Because the Simcenter 3D multi-physics solution leverages temperature and temperature flow into FE analysis. After that, the Simcenter 3D Specialist Durability solution can directly take the transient results of this solution as an input.
Thermal fatigue behavior
At the same time, also resistance against load cycles varies with temperature. Both high-cycle fatigue data (stress-life curves) and low-cycle fatigue data (strain-life curves) are temperature-dependent.
That as well is something you can consider in Simcenter 3D. Because in the software, you can enter fatigue data at different temperature levels. When necessary, the solver automatically interpolates data for intermediate temperatures, or adapts the data at each time step if the temperature field is transient.
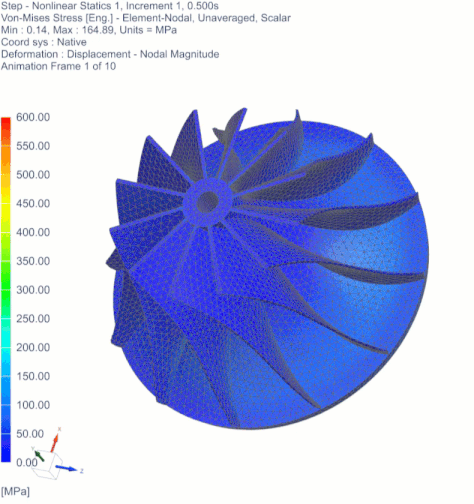
Influence on the stress-strain curves
In low-cycle fatigue methods, engineers identify damaging events along the recreated local stress-strain path. As also this behavior is temperature-dependent, material data is expected at the same temperature levels as the other fatigue data. Behavior at intermediate temperatures comes again through automatic interpolation.
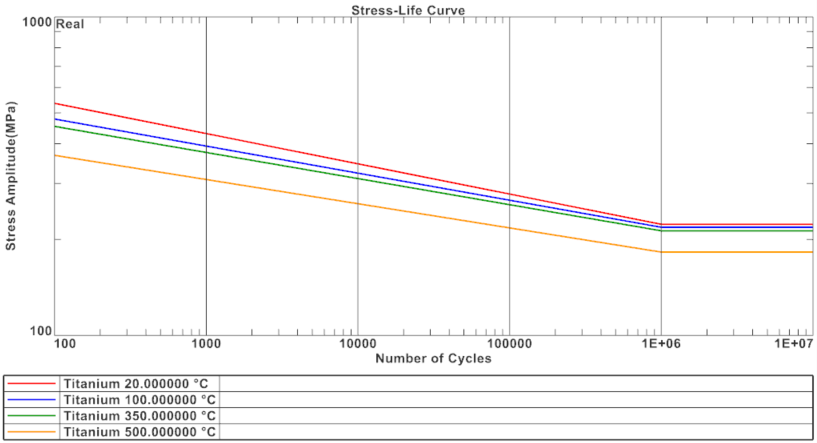
Influence on the plastic behavior
At higher temperatures, visco-plasticity will dominate the material behavior of metals. Mean stress relaxation and creep become important. Because the latter may lead to failure.
So how to combine all these effects?
How to bring these phenomena into thermal fatigue lifing analysis?
The relative importance of the different phenomena depends on the material itself (obviously), the temperature range, and the relative importance of temperature loads versus mechanical loads:
- If the temperatures still remain far from melting temperatures (rule of thumb < 50%) and the mechanical loads are dominant (think of the “cold” end of a muffler as an example), isothermal approaches are suitable, as these can sufficiently assess the influence of the temperature on the mechanical behavior and on the fatigue behavior.
- The temperature then defines whether high-cycle (stress-based) or low-cycle methods (strain-based) should be applied.
- And at high temperatures and in load cases dominated by temperature, you should consider low-cycle fatigue, visco-plasticity and creep.
Simcenter 3D includes all these use cases and their combinations, for example like high-cycle fatigue, combining high-cycle fatigue loads with varying temperatures.
Read below how to do it in practice.
Steps to setup thermal fatigue analysis in Simcenter 3D
Include fatigue data
Fatigue data in Simcenter3D are part of the material data. These can be temperature-dependent. So, the user can enter the fatigue data for several temperatures.
Temperature data
Temperature data in Simcenter 3D Specialist Durability are handled by temperature sources that are attached to the load events. For those, two different options exist:
Temperatures on groups
The user has temperature data from measurement or simple calculations defined on different parts of the structure. In this case Groups can be defined and on each group a temperature or a temperature time history is set.
If the groups would overlap, the user can decide whether to use the maximal temperature or if the software should average the temperature at those elements/nodes.
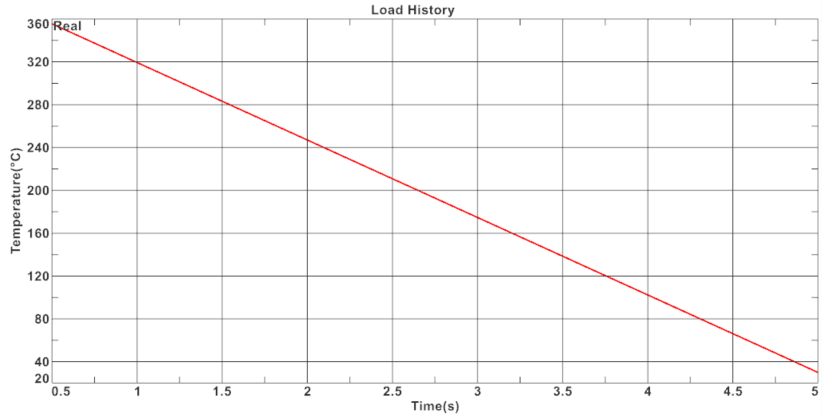
Temperatures from FE
The temperatures originate from FE results either as constant temperature field or as transient temperature data. In the latter case, the temperatures are typically aligned with the stress and strain data used in transient fatigue analysis. The transient event analysis automatically selects the correct temperature time steps in this case.
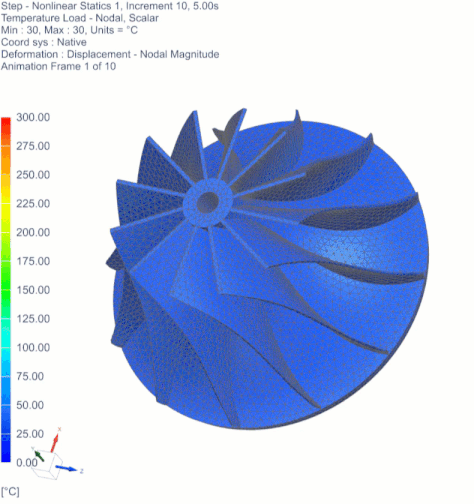
The analysis methodology
The technology has been developed in industrial research projects in strong collaboration with the University of Ljubljana, and tested in many different application cases, from simple vibration tests at different temperatures up to the simulation of thermal shocks (Heat up and cool down cycles from 20°C up to 1000°C).

The strength of the methodology is that it uses standard fatigue data at a few different temperature levels. But at the same time it can take into account the influence of temperature changes in each time step. You can read more about the methodology and several application examples in the bibliography below.
Bibliography
- Nagode, M., Hack, M., and Fajdiga, M., “High Cycle Thermo-Mechanical Fatigue: Damage Operator Approach,” Fatigue Fract. Engng. Mater. Struct. 32:505-514, 2009.
- Nagode, M., Hack, M., and Fajdiga, M., “Low Cycle Thermo-Mechanical Fatigue: Damage Operator Approach,” Fatigue Fract. Engng. Mater. Struct. 33:149-160, 2010.
- Nagode, M.; Längler, F.; Hack, M.: Damage operator based lifetime calculation under thermo-mechanical fatigue for application on Ni-resist D-5S turbine housing of turbocharger. In: Engineering Failure Analysis (2011), Nr. 18(6) S. 1565-1575
- Brokate, M., and Sprekels, J., “Hysteresis and Phase Transition,” Applied Mathematical Sciences 121, Springer, New York, 1996.
- Brokate, M., Dressler, K., and Krejci, P., “Rainflow Counting and Energy Dissipation in Elastoplasticity,” Eur. J. Mech. A/Solids 15:705-737, 1996.
- Hack, M., “Schädigungsbasierte Hysteresefilter,” D386 (Diss Univ. Kaiserslautern), Shaker Verlag, Aachen, 1998.
- Nagode, M., and Fajdiga, M., “Coupled Elastoplasticity and Viscoplasticity under Thermomechanical Loading,” Fatigue Fract. Engng. Mater. Struc. 30:510–519, 2007.
- Nagode, M., and Hack, M., “An Online Algorithm for Temperature Influenced Fatigue-Life Estimation: Stress-life Approach,” Int. J. Fatigue 26:163–171, 2004.
- Nagode, M., and Zingsheim, F., ” An Online Algorithm for Temperature Influenced Fatigue-Life Estimation: Strain-Life Approach,” Int. J. Fatigue 26:151-161, 2004.
- Nagode, M., and Fajdiga, M., “Temperature-Stress-Strain Trajectory Modelling During Thermo-Mechanical Fatigue,” Fatigue Fract. Engng. Mater. Struct. 29:175–182, 2006.
- Šeruga, D.; Nagode, M.; Hack, M.; Hansenne, E.: Thermomechanische Ermüdung – Simulation von Thermoschocks. In: NAFEMS online magazin (2011), Nr. 18, S. 79-87
- Nagode, M.; Šeruga, D.; Hack, M.; Hansenne, E.: Damage operator-based lifetime calculation under thermomechanical fatigue and creep for application on uginox F12T EN 1.4512 exhaust downpipes. In: Strain (2012), Nr. 48 (3), S. 198-207
- Šeruga, D.; Hansenne, E.; Haesen, V.; Nagode, M.: Durability prediction of EN 1.4512 exhaust mufflers under thermomechanical loading. In: International Journal of Mechanical Sciences (2014), Nr. 84, S. 199-207