Startup uses simulation to develop monocoque frame for road bikes in virtual environment
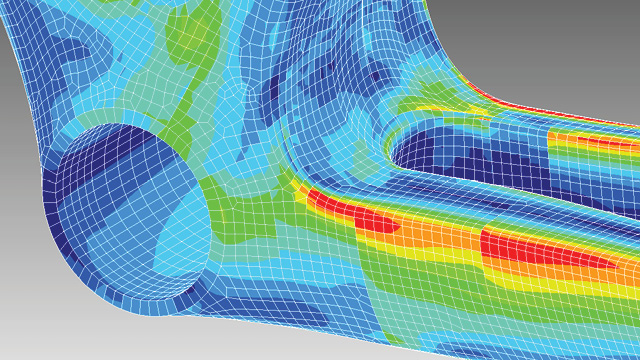
Until recently any cyclist who wanted to buy a new bicycle had two options: Either purchase one of the big brands with a monocoque frame that is available in a fixed range of sizes with performance based on stiffness by weight, or a tailor-made frame manufactured with the tube-to-tube technique. This kind of bike has tubes that are cut, welded and wrapped with carbon fiber around the joints (knots), with the inevitable drawbacks in stiffness.
Now startup EXEPT, which is based in Savona, Italy, is providing a third way. It has developed a process that combines the benefits of both traditional approaches to create tailor-made monocoque frames. The custom monocoque technique invented by EXEPT uses movable molds to cast monocoque frames without any carbon fiber discontinuity so it can be made to order for each cyclist.
EXEPT identified Femap with Simcenter Nastran as the desired solution to optimize design and prototype in a virtual environment that allows them to address the needs of their unique market. Engineers at EXEPT take advantage of the clear and intuitive visual display of Femap to better understand the model, as well as advanced reporting tools for data extraction. Accordingly, tasks such as model construction and interpretation of analysis results are intuitive, fast, and lean.
Read the full case study to find out more about how EXEPT uses Siemens PLM Software’s simulation solutions to design and analyze customized monocoque bicycle frames