Simulation Reuse: The Key to Analysis Productivity?
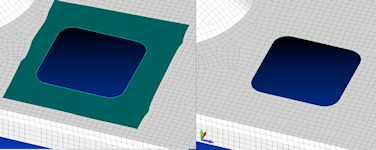
Analysis is no longer the purview of highly trained experts. For more than a decade, engineers have been able to run simulations of the models they’ve designed. Now, their simulation systems include more capabilities and tools than ever. Engineers can mesh a model. They can apply boundary conditions and loads. They can solve for several physical forces acting on their model at the same time. They can take multiple types of physics into account.
While this new age of simulation has delivered numerous benefits to engineering teams, what if they could do more faster? What if engineers don’t need to start from scratch, building every model anew. What if they don’t need to “take it from the top,” as it were, each time they run a simulation? Perhaps they don’t need to start from a clean slate sheet every time when it comes to model creation and simulation.
A Treasure Trove of Past Analyses
Engineers at most manufacturers have already created models and simulations for many of the company’s parts and products. Those models are digitally stored–digitally warehoused by some means–within the manufacturer.
That’s particularly true for companies that work in highly regulated industries–like those in the pharmaceutical, medical device, and food packaging industries—and those must document due diligence with their designs. In many cases, these companies are required to save the models and simulations that demonstrate their products have met regulatory specifications. If in a worst case scenario, someone brings a lawsuit against the company, the models and simulations come immediately into play. They stand as proof that the product was safely designed.
Beyond proof of due diligence, these simulation models and results represent more. They embody a significant of work and, in some cases, best practices that have been carefully developed over years. Additionally, these completed simulations represent work that can be built upon. The results have been accepted and are shown to be superior to any other, earlier results. They’re the final product. They already exist.
Accelerating Simulation Processes
In all of these cases, there is little need to start every simulation from scratch. Rerunning an existing simulation is a valid case. Engineers can use these simulations to build new products. Existing simulations offer a shorter path to delivering results, representing a more efficient way to work than beginning with a clean slate. Why recreate the wheel when a simulation of the wheel, representing best practices, already exists? Grab that simulation and make it your own. Many times, you only need to make a slight change to the pre-existing simulation. Then it will be perfectly suited to your needs. You may need to tweak the geometry. You may need to apply and solve for a new load case, apply a boundary condition. You may need to tweak the finite element mesh.
Opening Legacy Simulation Models
Before a completed analysis can be reused, however, it must be accessed. In many cases, accessing a simulation is more complicated than simply opening a file. Older simulation models and results might be in old, proprietary, or depreciated formats. Too often, companies may no longer even own the simulation application that was used to build the analysis model.
In the aerospace industry, for example, certain parts continue to be manufactured for years. But their designs are slightly changed as time and needs change. These design can be updated with only a few changes to the existing model. But simulation application needs access to that original model no matter its format.
Companies may keep their models and simulations in the digital archives, but they’ve certainly updated their design and simulation technologies over the years. They’ve may have moved to an entirely different CAD system or updated their system numerous times throughout the years. They may have models stored that came from any number of suppliers provided in any number of formats. The simulation application must be able to open all of them.
In order to accelerate the simulation process through reuse, engineers need simulation tools that can open analysis models in a wide range of native or neutral formats.
Changing Legacy Simulation Models
Of course, your simulation application also has to let you make changes to an existing model. That may seem straightforward, but there are many functions it needs to allow for. It’s important you be able to modify the geometry of the existing model. You have to be able to change its mesh geometry or even to change the mesh itself. You need to be able to create and modify loads and boundary conditions as well.
Remember, no need to recreate the wheel. The wheel you’re looking for probably already exists. But it also probably won’t be exactly suited to your present-day needs. Some simulation applications let you find the wheel, modify it, and run the needed simulations. Ultimately, to get the most from reusing existing simulations, engineers need simulation tools that can not only open legacy analysis models but modify them as well.
Recap
- Compared to starting from a clean slate, existing simulation models may offer a shorter path to delivering results. There are many scenarios in which a slight change to a pre-existing model is the only thing needed.
- Simulation applications need to provide access to existing models and must allow engineers to make changes to them, like tweaking geometry or applying boundary conditions.
That is my take folks. Do you have experience in leveraging legacy simulation models? Sound off in the comments and share what you’ve found.
Siemens PLM provides a range of capabilities that directly address legacy simulation workflows. For more details on how FEMAP addresses these needs, download our complimentary eBook.