Overcoming conflicts with Simcenter Soundbrush
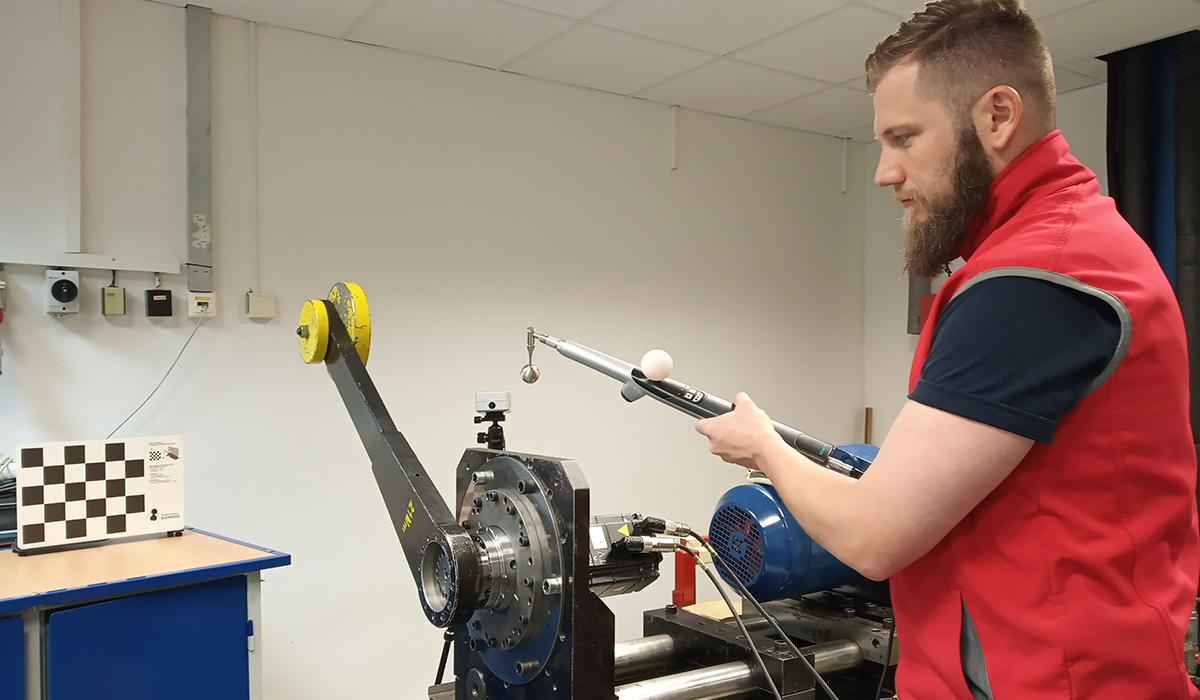
Conflicts can be very difficult and break a relationship, whether its business or personal. How do you find a resolution? The one thing I have learned about conflicts is that if you approach them wisely and rationally, they will move you further and open new horizons. Conflicts can means opportunities if handled in the right way. And what’s more, you can apply this to the corporate world as well. Here is the story of SPINEA.
Driven by the motto, “Excellence in motion,” SPINEA is a global producer of high-precision reduction gears with patented designs as well as other modules used in automated and robotized production lines. Based in Presov, Slovakia, SPINEA boasts a high-profile client list that includes world-renowned industrial robot manufacturers KUKA and ABB as well as other premier companies such as Comau, Trumpf, Doosan, Swarowski and Tetrapac. SPINEA also provides products to CERN in Switzerland, the European Organization for Nuclear Research. Customers such as CERN have high requirements and do not accept product imperfections.
Adding a new customer to this list and maintaining a good business supplier-original equipment manufacturer (OEM) relationship can be difficult. Suppliers tend to run into conflict situations that result in customer complaints. Although suppliers can produce products meeting all requirements, once the component or sub-system is integrated, issues may appear. The situation gets even more complicated when an OEM deals with several suppliers and each is convinced their product is flawless. How do you tackle these situations?
Simcenter Soundbrush: Measure and proof
SPINEA can relate to these situations. Their gear boxes were once suspected of causing noise issues. This company would bet their bottom dollar (or Euro, if you will) their components are perfect, meeting the noise level requirements and “innocent” of causing any noise issues. To ensure and justify the quality of their products, SPINEA’s team began searching for a solution to measure the noise levels and define the root cause of the issue. This is what brought them to the engineering technique called, “sound source localization.”
Sound source localization uses real-time noise measurements to identify the specific noise source. SPINEA decided to invest in Siemens Digital Industries Software’s Simcenter Soundbrush solution, which enables the development team to visualize sound intensity in 3D. This tool provides accurate and detailed identification of noise sources, including sound intensity values, sound propagation directions and sound power values during one single and simple measurement.
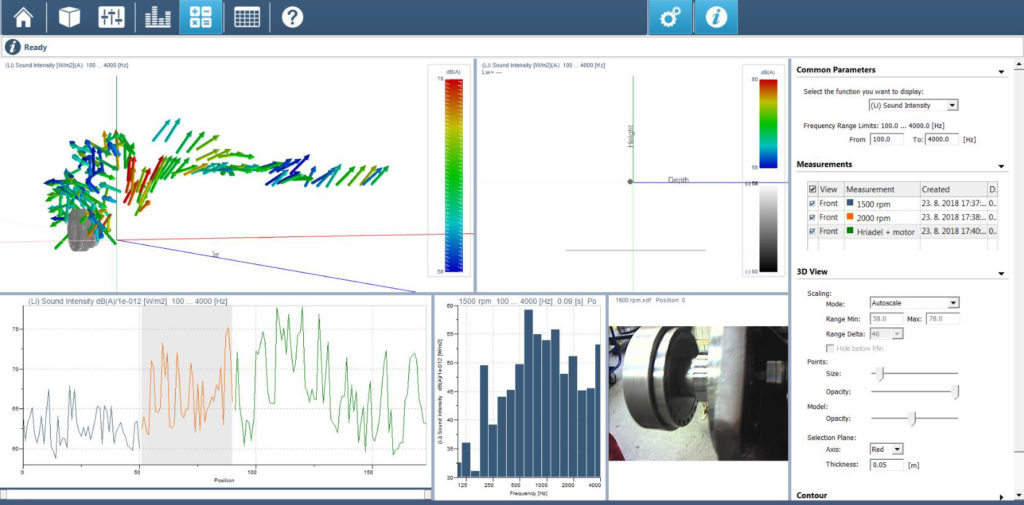
“The critical reason why we decided to deploy Simcenter Soundbrush is its capability of accurate 3D noise pressure visualization in real time and ease of use.”
Mr. Olejár, test engineer, SPINEA.
“Before, we worked with microphones, but we were lacking the capability to pinpoint exactly where the noise was coming from,” says Mr. Olejár, test engineer, SPINEA. “Is it from the gear box or from the engine? A microphone is never as precise as the Simcenter Soundbrush, which allows us to provide precise measurements when responding to complaints.” You can rely on microphones to get the sound level measurements, but not to gain the information about the directions it comes from.
Looking at the sound intensity measurements made by Simcenter Soundbrush, it was immediately clear that the SPINEA gearbox was not the one to blame for the noise issues.
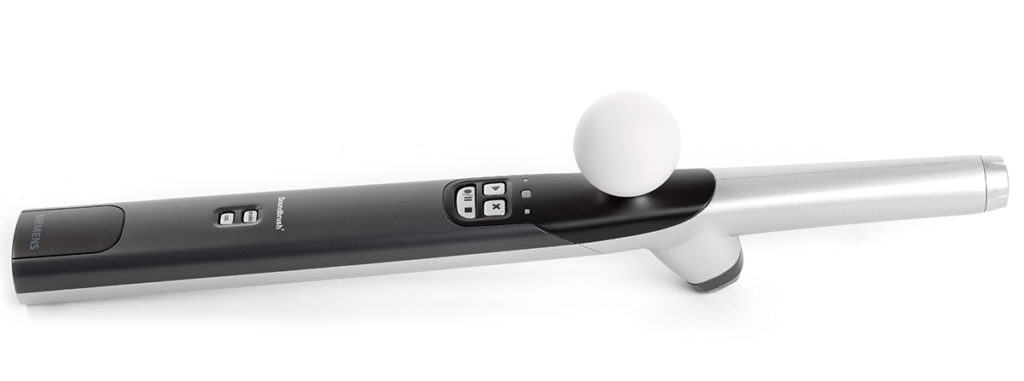
Simcenter Soundbrush is very easy to use. There is neither extensive training nor deployment periods needed. “Immediately after the training, we started with the acoustics measurements and analysis of the bearing reduction and the results were great. It was shown that our products are meeting the strict requirements for the maximum allowed noise limits,” says Mr. Olejár. “The noise field is registered by movement of the high-sensitive 3D intensity sensor, which is able to register the direction and intensity sound field around the tested bearing reduction. This is very important to filter out other unwished noise phenomenon from the motor, for example. Thanks to this capability, some of the complaints were revoked.”
“It’s much nicer to answer the complaint with an explanation that includes visualization. In this way, we spare both sides a lengthy complaint process and potential reshipping of the product.”
Mr. Olejár, test engineer, SPINEA
Simcenter Soundbrush comes together with a dedicated software program. “Simcenter Soundbrush 5 is user friendly,” says Mr. Olejár. “It guides you and offers different analysis options of the noise field according to your needs, whether you’re dealing with impulsive, fast or slowly changing noise, or if you are interested only in some specific frequencies.”
Mr. Olejár adds, “The first setup may take you some time, but once this is done, everything goes fast afterwards. The software is very intuitive, easy and fast. The possibility to identify the root cause of a problem, which we can do with Simcentere Soundbrush, is essential.”
End-of-the line testing with Simcenter Soundbrush
You remember I said that solving a conflict in a positive way will move you further? By deploying Simcenter Soundbrush, SPINEA gained new capabilities for additional end-of-the-line testing. Simcenter Soundbrush is a very compact tool, ready to measure in a couple of minutes. This enables SPINEA to quickly proceed validation noise measurements once the product is taken off the production line to ensure there are no issues and the product can be released for shipment.
Measure for future enhancements
Using Simcenter Soundbrush provides you with insightful information for future product enhancements. The test engineer collects needed data and confidently share it with the development team using a Microsoft Excel spreadsheet file. Working with standardized files accelerates the interaction between the development and test departments.
Sound source localization is a unique engineering technique to rapidly identify the root cause of any noise. For SPINEA, this technology helps the company deal with complaints using a simple to interprete 3D visual representation of the 3D sound field, test products before their release and enhance their next generation of products.