How Simulation Solves Some of Today’s Top Product Development Challenges
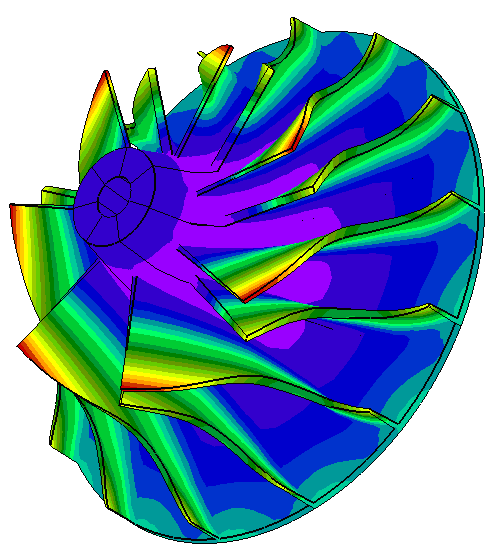
Developing products is not easy. Schedules are tight, products have gotten more complex, and even development environments are more complex. Contributing to environment complexity, typically a variety of design tools are used. In a recent Tech-Clarity’s study, companies reported using an average of 3.6 different CAD tools, with 84% of companies using two or more.
With all this complexity, it is not surprising that companies report numerous product development challenges. As part of our research efforts for our study, Addressing the Bottlenecks of FEA Simulation we asked survey respondents to select their top 3 challenges. Figure 1 shows the results:
Figure 1 – Top Product Development Challenges When not addressed, these challenges can be quite costly for a business. They can lead to expensive delays and extra costs due to errors, scrap and rework.
Responding to frequent design changes is the top reported challenge. Stopping to respond to changes disrupts the workflow of new projects, taking away from efforts that could be spent on innovation. This hurts efficiency and can put release dates at risk. Errors, new ideas, and changes to requirements are among the many reasons engineering change orders (ECOs) are initiated. However, product complexity means it’s easy to make mistakes or overlook other areas of the design that might be impacted by the change. With better insight throughout the design phase, many changes could be avoided.
Product complexity makes it very difficult to verify requirements have been met and predict final product behavior. To make it easier, engineers need better ways of validating requirements and obtaining insight into how a product will behave in a real world environment. When they cannot do this validation, problems are found much later in the development cycle, when they are much more difficult to fix. During later stages, the design is mostly finalized so even small changes can have a big impact on the rest of the design. Consequently, solutions to the problem are often limited to what is fastest and easiest, not what’s best. This can drive up cost and hurt quality. Imagine the time and cost savings if engineers could find some of these problems earlier.
Also, as our most experienced engineers approach retirement, we are losing a lot of expertise. Plus, the complexity of development environments, make it very difficult to share best practices. This becomes especially problematic when looking to optimize products or identify over-engineered areas of the design. Engineers need better methods to balances requirements to meet customer expectations for quality, performance, and cost. With better insight into the impact of trade-offs, engineers could design better, more competitive products. In many cases products are over-engineered to ensure quality such as adding extra material to increase strength. However, it is hard to know if the extra material helps or just drives up material costs and adds weight. Identifying over-engineered areas can save money, but it is difficult without guidance.
In my previous post, I described how we identified Top Performing companies to identify best practices. Table 1 shows the performance metrics used to define Top Performing companies.
Table 1 – Defining Top Performers
Figure 2 shows how Top Performing companies address the challenges outlined in Figure 1.These strategies are more likely to be adopted by Top Performers than their peers, indicating they contribute to success.
Figure 2 – Top Product Development Strategies Used by Top Performers
From Figure 2 you can see that Top Performers are very focused on evaluating product performance and behavior as early as possible. By analyzing behavior early, they have a better understanding of how products will behave and therefore, they are empowered to make better design decisions. Also, they can validate requirements as the design evolves, avoiding changes later due to missed requirements. Early analysis also puts them in a better position to optimize the design and analyze trade-offs. The analysis also leads to better insight to identify over engineered areas. The result is more competitive products that are more likely to meet revenue and profitability goals.
Top Performers also evaluate many design iterations at the concept stage, before moving on to detailed design. Because of this, they start with a more optimal concept, which helps them minimize some of the risk of new designs.
In addition to optimization, Top Performers also focus on finding problems during design, before the testing phase. By finding problems earlier in the design cycle, they are much easier to fix.
Simulation tools are key to enabling these strategies, especially as products become more complex. By using analysis tools, you can simulate performance in real world environments. This provides a better understanding of product behavior that will lead to more informed design decisions. The tools also make the process of evaluating multiple criteria simultaneously much easier. You can also evaluate many iterations in far less time making optimization that much easier.
For more insights and findings from the study, you can download the complete report here (free of charge, registration required).