Why the Digital Twin is not about technology
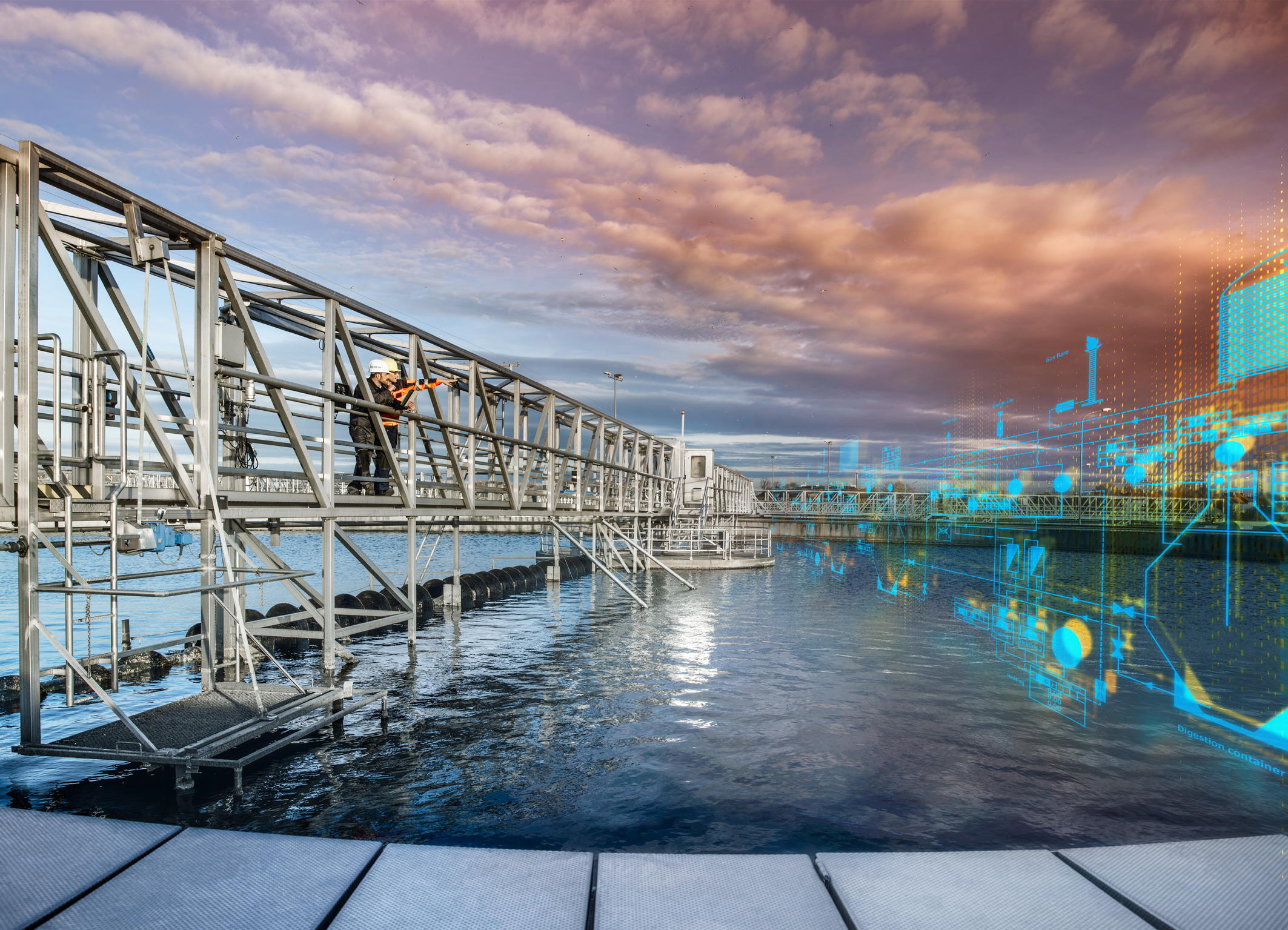
Some weeks ago a colleague approached me to represent Siemens on a panel of experts in the water industry. The topic I presented: The Digital Twin in the Water Industry. When we discussed what I would talk about in my presentation, the natural route of the conversation went down the technology path. But here’s why I think this topic isn’t as dry as it sounds… Digital Twin is not about technology, it’s about people. People and processes to be exact. Because when you connect people through effective and efficient processes, technology is just the tool that serves a higher purpose: Innovation for a better world.
Let me explain. In the water industry, like in many others, the engineering team designing and analysing a water system is often loosely connected to (if not completely disconnected from) the team of operators. This silo approach is inefficient, costly and frustrating.
The ideation phase: the creation of the digital twin
When we look at process, we can identify three main phases: ideation, realization and operation. In the ideation phase, engineers use system data (GIS, CAD, BIM) to automatically create a simulation model. This is the core of the digital twin.
A good example of where this approach has been applied successfully is this case study from Kehoe Myers and JS Pump and Fluid System Consultants. They used Simcenter Flomaster to design and analyse the water supply system serving the new Brisbane West Wellcamp Airport. They stated:
“Static and dynamic hydraulic modeling of the area’s town water supply system performed in Simcenter Flomaster assists in optimizing critical plant components. This results in lower life cycle costs and more reliable system operation”
Kehoe Myers and JS Pump and Fluid System Consultants
The realization phase: the re-use of the digital twin
Once the system is designed and optimized, it is time to build it, or to ‘commission’ it. This is what we call the realization phase. The problem is that water systems are not like cars or planes for which you can build prototypes or iron-birds. There is no room for prototypes, the system must be right from the beginning. This is where we can reuse the digital twin to create more and more value.
The hydraulic dynamic model created in the ideation phase can now be connected to the control and automation model. Both these models can be run simultaneously by means of an operator dashboard. This is what we call Virtual Commissioning. This allows you to operate the system in a completely virtual environment. Allowing you to explore its response to different conditions before it is even built. This technology also allows to create an effective operator training tool which improves the knowledge transfer between engineers and operators.
The operation phase: digital twin at work
Now, the step to reuse the digital twin in the operation phase is very small. This is because we can connect it directly to the real control and automation system. Now the digital twin can run it in real time to provide additional information to the operators. An example: the digital twin can provide information at locations where sensors are not available. This is what we call virtual or soft sensors. Another more interesting example: the digital twin can compare the simulation results with the measured data to detect malfunctioning and trigger alarms if necessary.
Since the virtual system is completely hidden behind an operator dashboard, there is no need for additional training or for operators to learn simulation tools (which sometimes can be daunting).
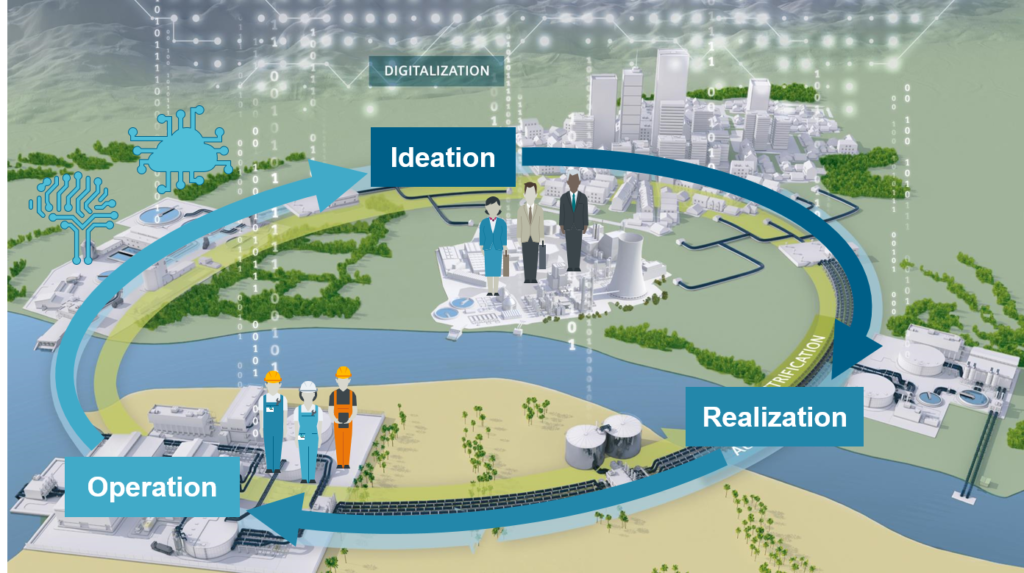
Closing the loop
The final step is to close the loop by gathering data from the real system to continuously update and improve the fidelity of the digital twin. we can do this by leveraging industrial internet of things, artificial intelligence and machine learning to automatically fine tune the digital twin.
All of this might look technical, complex, maybe even futuristic, but in reality this is something that can easily be done today. Engineers can continue to happily use simulation tools to build digital twins. Operators do not need to learn new tools, because the power of the digital twin is completely hidden behind a familiar and user friendly dashboard.
This is a technology that improves process efficiency through improved communication between engineers and operators.
I like to think that the use of the digital twin will not only make processes more efficient but it will also make our environment better and ultimately our everyday lives better.
For more information about how you can improve your workflow by incorporating a digital twin, look at this presentation on using Simcenter for Operational Excellence in Wastewater Treatment.