A day of Heavy Equipment NVH Testing activities
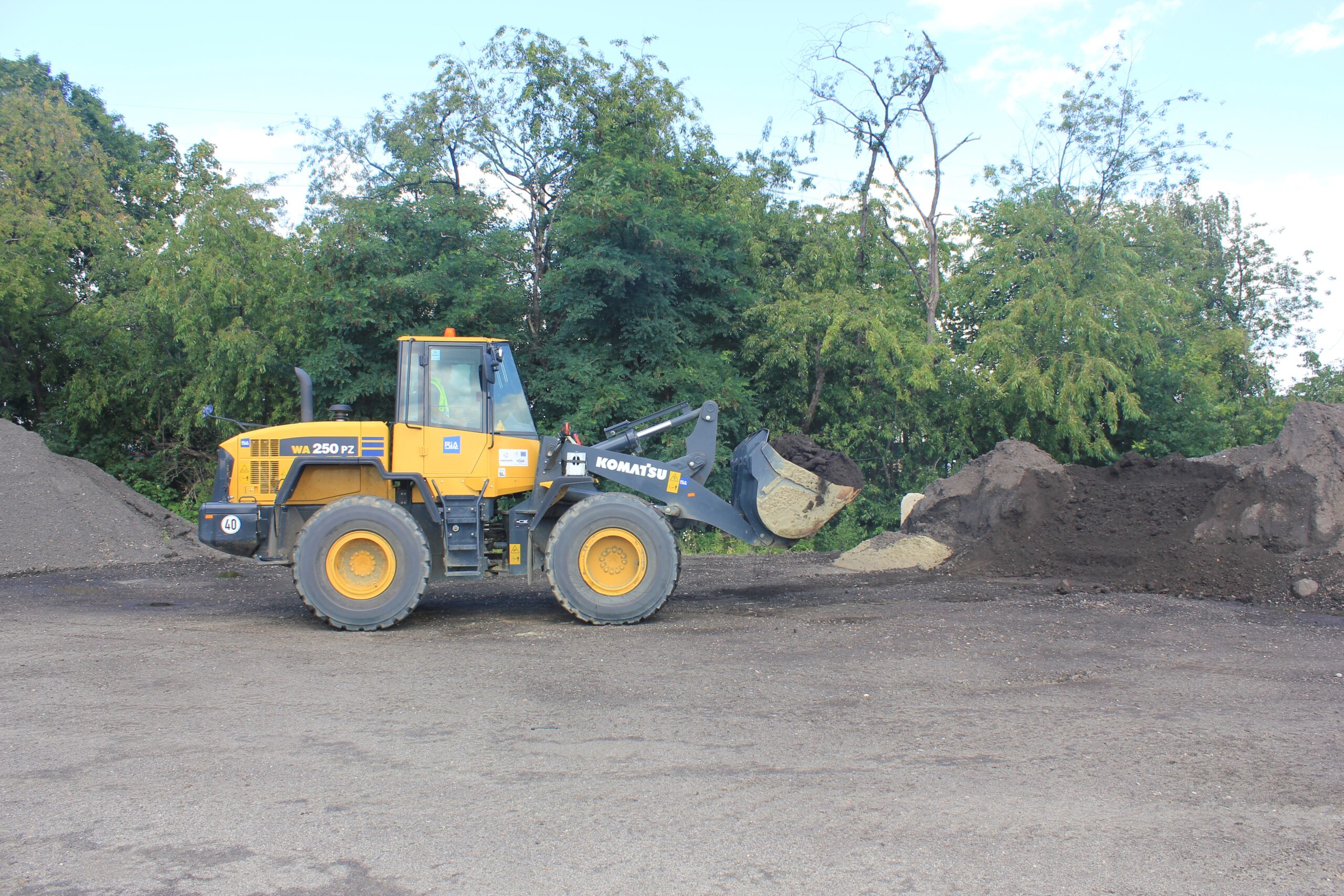
Past years, the heavy equipment market has been growing world-wide. Most importantly in rapidly emerging economies, agriculture and construction machines play a crucial role in economic growth. However, like most industries, also this one is going through rapid changes which impact the development of those machines. What are the main concerns of those teams? Let’s discuss some of the heavy equipment NVH testing challenges in this blog.
Environment impact, globalization and…very demanding customers
The worldwide push towards green sustainable economies, is highly impacting heavy equipment development. For instance, many governments are putting noise and emission regulations in place. The manufacturers need to consider it at the start of their development process in order to avoid last minute troubleshooting actions to comply with these regulations.
But this is insufficient. Globalization and increasing customer demand, pushes manufacturers to develop better machines. They do not only comply with regulations, but further differentiate with respect to customer comfort.
Today I want to talk about the noise, vibration and harshness (NVH) testing activities that are important in the development cycle of these machines. I invite you for a tour of a recent NVH testing activity I dove into. The goal was to experience these testing challenges and their importance in the final machine project.
Note: The wheel-loader and the test area were courtesy of VDAB Opleidingscentrum (Belgium).
The machine is there…what should I test?
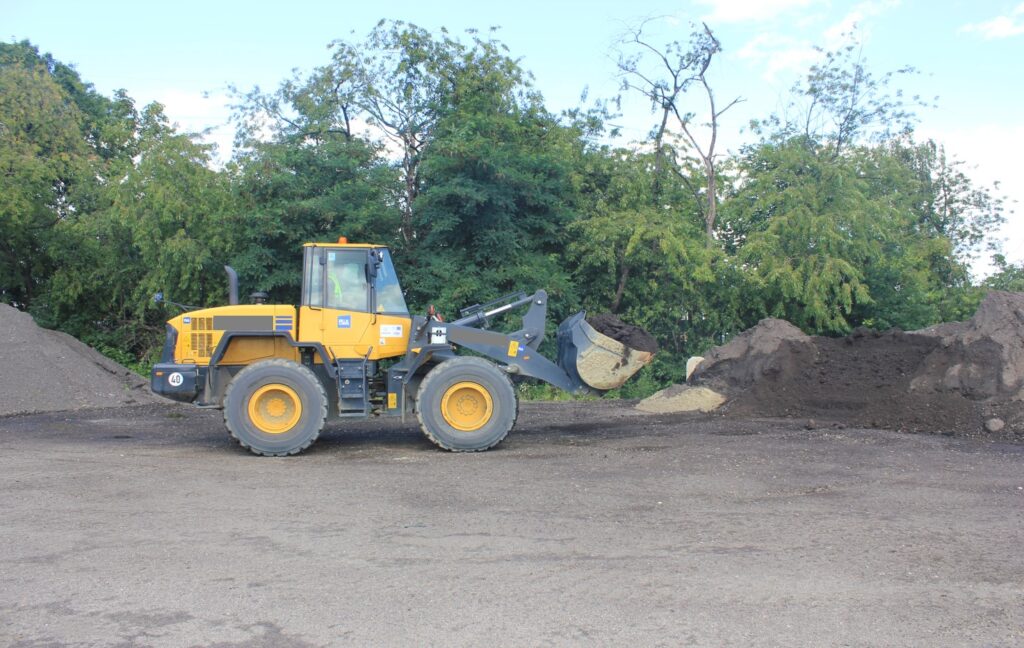
Last summer I went with my colleague to a test field in order to acquire some data in a wheel-loader. We wanted to understand what is the NVH behavior and how this was impacting the operator inside the cabin.
It’s clear that a full NVH testing schedule of such machine would take several days to be completed. We selected a simplified schedule where we could acquire and process data for the following applications:
- Human body vibration
- Operational NVH analysis
- Cabin sound quality analysis
- Sound source localization using array of microphones
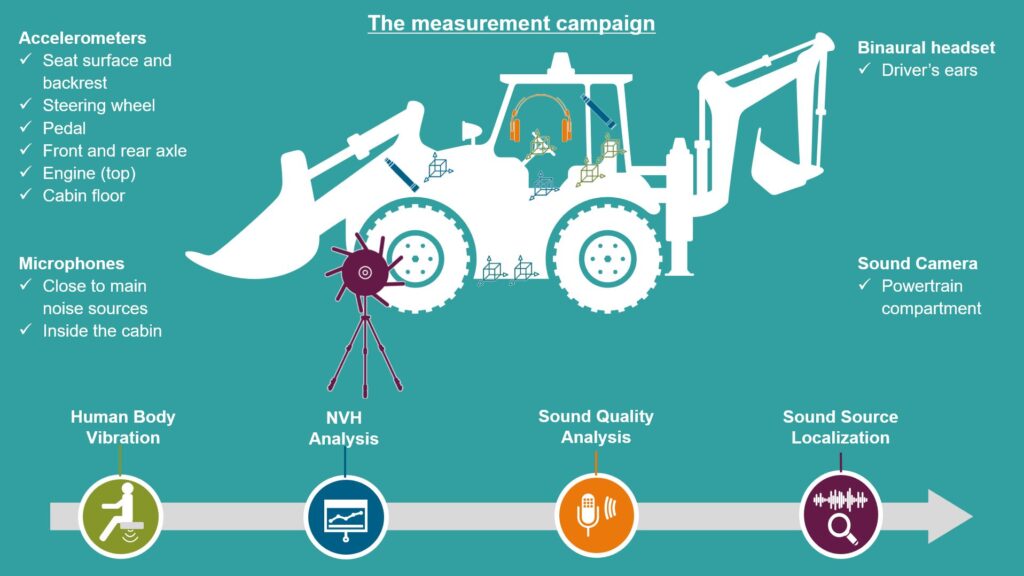
As illustrated in the info-graphic above, we’ve used accelerometers, microphones, binaural headset and an array of microphones. The idea was to identify the main NVH sources around the powertrain and their levels of inside the cabin.
Note: Measurements to check the machine reliability (durability / structural testing) will not be included in this blogpost.
Human body vibration
We selected this topic as it’s an important aspect for the operator comfort during the machine operation. Long duration exposure to high vibrations on hand at steering wheel, or whole body through the seat or floor can at worst case cause health issues for the operator. This is one of the reasons international standards and local regulations are in place. Performing those measurements is not only a must to check if compliant. They are also interesting just as a measure of the vibration comfort of the machine.
In order to access these levels, we have followed the instructions in the ISO standards below:
- ISO 2631: Whole-body vibration
- ISO 5349: Hand-arm vibration
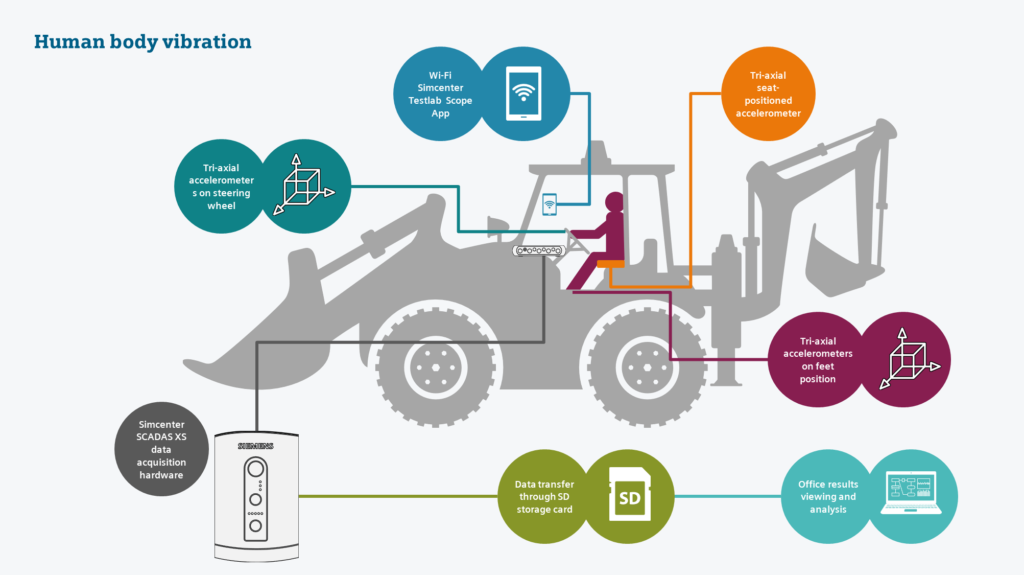
Besides the level of vibration, two other elements play a key role to quantify how discomforting those are for human operation. First of all, the frequency; certain frequencies are more damaging as those lie in the frequency range of the natural frequencies of the human body. Secondly, the direction of the vibration plays a key role too.
How to measure these vibrations?
The measurement, consisted of tri-axial accelerometers, each connected to the Simcenter SCADAS XS. Data processing with the Simcenter Testlab software further filters the data with different human-body vibration weighting filters. The next step is the calculation of RMS levels and in the end combination the 3 directions into single vibration values. The standard describes different calculation methods to access the final vibration levels.
Not to our surprise, all vibration levels were below the limits. We could confirm that this machine was in conformity with human body vibration regulations.
We were expecting vibration levels below the limits as this is a released machine. However, the comfort level of the machine can also be verified throughout Human body vibration analysis. Therefore, those measurements are also of interest for machine manufacturers to perform benchmarking or target setting for instance. In a world with increasing competition and increasing customer comfort expectations, taking human body vibration comfort into account early in development becomes a must.
Another important assessment is the interior and exterior sound power levels (not included in this test activity). These tests follow ISO standards (ISO 6393 / 6394 / 6395 / 6396). Depending of the type of machine, different standards apply. Key is that each of those measurements are fully supported as well within the Simcenter solution. Even efficient one-man operated test, that combine both interior and exterior sound power measurements are supported.
Operational NVH analysis
In most cases, meeting regulations or even more ambitious NVH targets, requires more in-dept engineering and design iterations. First aspect is the assessment of more operational NVH data with different sensors spread over the machine. This allows more detailed troubleshooting.
So, this is exactly what we did. We decided to instrument accelerometers and microphones close to the main NVH sources in the powertrain compartment (source side). On the other side we also instrument it inside the cabin (receiver side). The operator did controlled accelerations from idle to maximum engine speed and data was measured both in ascending (run-up) and descending (cost-down) speed.
Excitations from sources such as the engine and transmission can lead to acoustic or vibration discomfort. To investigate those, both the sources, as well as the insulation of cabin is of extreme importance. This pragmatic approach allows to analyze and compare those signals together.
In our test we decided to check which are the main noise and vibration sources in the machine operating conditions and check if they were affecting the cabin comfort.
Is the cabin insulated enough?
We found that the cabin insulation was very well for vibrations coming from the powertrain. However, noise was not being isolated equally well for all important engine operating conditions.
In this example, the instrumentation was quite simple and straightforward; we used classical ICP microphones and accelerometers. In many cases it can be important to add quite a lot of different sensors. Imagine for instance if you need to measure hydraulic pressures to corelate them with NVH; displacements of components using for instance string pots, rotational speed of actuators or the powertrain, vehicle speed and location using GPS to link NVH events to the location of the machine, machine state conditions available on the CAN-BUS to be linked to NVH, etc. These are all very common things to effectively troubleshoot for different NVH aspects. All above scenarios are supported with the Simcenter SCADAS hardware. With the very same hardware family, any multi-physics signals data acquisition can be addressed covering many measurements and data streams all within one synchronized data set.
Although the level inside the cabin was surely at acceptable level, there was room for further improvements. Should we completely dismiss that or further investigate it? I don’t need to say that we went for the second option and decide to extend our analysis.
Sound quality analysis
In order to investigate the impact of engine noise on cabin Sound Quality, we used data recorded with our Simcenter Binaural Headset. This sensor allows to record the data completely as perceived by the operator, as it measures the noise at both left and right ear driver’s position. Being able to assess exactly how the sound is perceived, allows to focus specifically on the Quality of the sound; recorded data can be fully replayed identically to how it sounded in the cabin. Since the perceived quality of the machine, including sound quality, becomes an increasing decision criterion for the end users, more and more these measurements become crucial.
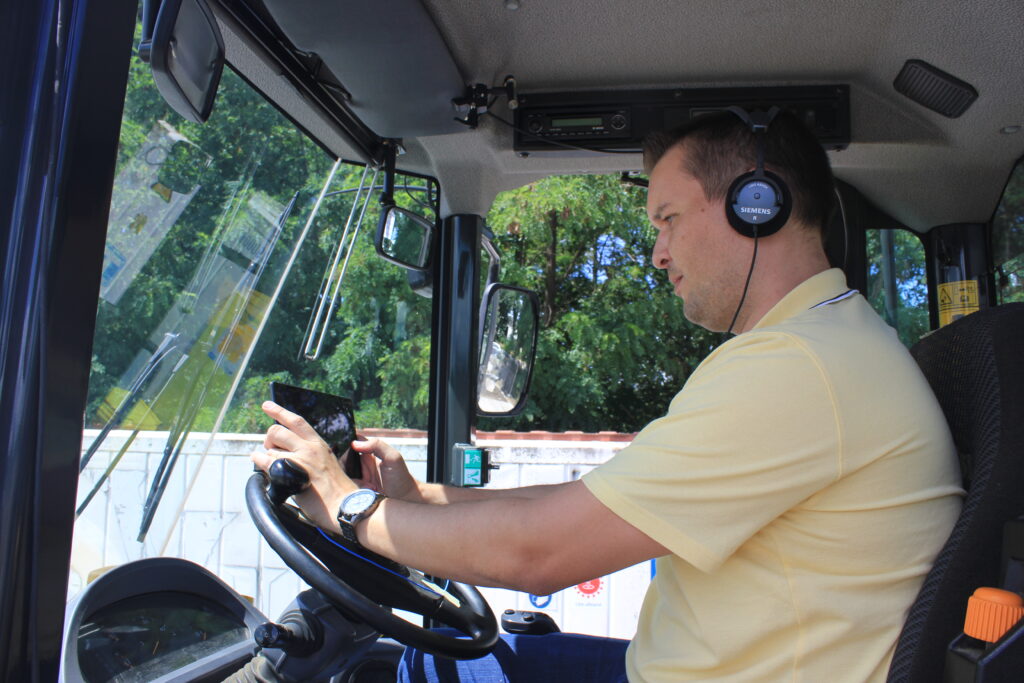
Sound quality analysis allows us to better understand the sound and how that will be perceived by the end-user. It involves usage of the so-called psychoacoustics metrics in combination with audio replay & filtering capabilities.
When performing the quality analysis, I used filters during binaural replay. We try many different filters, but we definitely agreed that on the total sound quality perception the engine firing orders (specially order 12) had a large effect on it. Reducing or even completely removing this order while doing the replay, highly increased the quality. The ability of executing these “what-if” analysis using filtering capabilities is another positive point of executing sound quality analysis during the development process of these machines.
What could be done to improve the Sound Quality?
Although we all agreed that reducing the engine fire order inside the cabin, would be a great quality improvement, the next question of course is how this could be achieved. For those more in-depth analysis it all goes back to what is called the source-transfer-receive principle. Some examples of what could be done next are:
- Focus further on the powertrain itself, the source, for instance using the sound source localization techniques.
- Investigate the airborne / structural transfer paths from the powertrain to the cabin.
- For lower frequencies, such as the engine firing orders, this may require looking at the structural properties and mode shapes of the machine, using experimental modal analysis. For mid to high frequent noise, which is usually more airborne radiated, it may be required to understand if there are leaks in the cabin, for instance using sound source localization techniques.
- To capture the complete picture of how the complete process, from engine excitation all the way to interior noise, Simcenter Testlab Transfer Path Analysis is the path forward, which maps the complete process from source towards receiver.
To illustrate some of the above, we had a closer look in the powertrain compartment side (source location). As different noise sources like engine, intake, exhaust and fan are located very close to each other, we wanted to use sound source localization techniques to understand better the noise scenario.
Sound Source Localization
Sound source localization techniques are available in the market since long time and represent a powerful way of assessing noise problems.
We used Simcenter Sound Camera, which is a digital microphone array consisting of lots of microphones (as low-frequency noise was the target, we used the configuration with long arms with total of 117 microphones). As the array has digital microphones, we didn’t have to use any Simcenter SCADAS frontend. We positioned it pointed to the powertrain compartment to capture the sound during a ramp-up in static condition.
On top of the default beamforming, Simcenter Testlab counts with additional processing methods. As beamforming does not supply accurate results in low frequencies, and we do face lots of low frequent powertrain noise, those additional processing is crucial here. We choose Bayesian focusing technique that present good results in low and high frequencies.

What these nice holograms can tell me?
The results (one localization hologram per 1/3 octave band) shows exactly which component is most noisy for each octave band. As expected, in the frequency range we have used to investigate the noise inside the cabin, the engine is responsible for most of the sound (around 500 Hz).
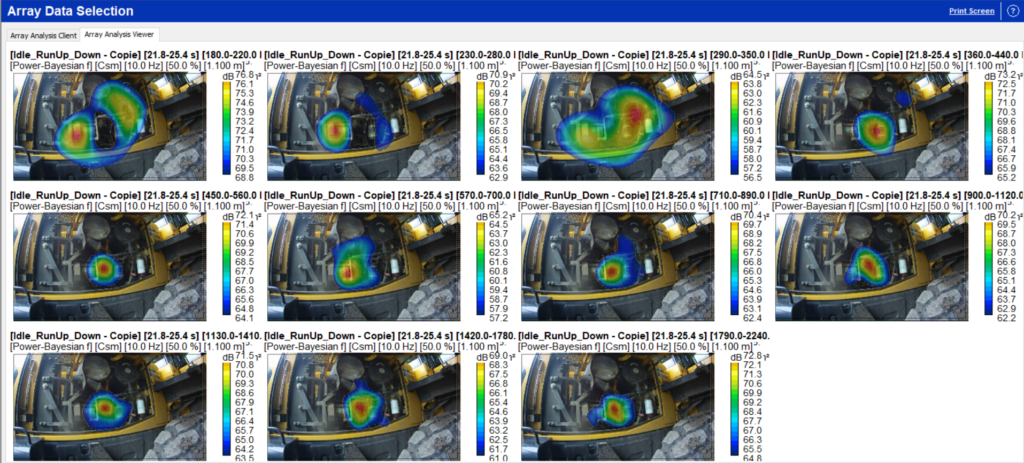
Now, there are two ways to move forward, try to change the engine, which is very unlikely to do. So more logically would be to assess further if the transfer to the cabin cannot be further optimized. A next step would be for instance to go with Sound Camera inside the cabin for identification of where the sound leaks into the cabin. Another great option is to add a near-field microphone close to the engine and combine it with the Sound Camera into one single measurement. In Simcenter Testlab, the user can analyze the sound map within the cabin, coherent with this microphone close to the engine; identify where the engine noise leaks into the vehicle. But this, will be for another measurement campaign.
The end of an enjoyable Heavy Equipment NVH testing day
That was the end of our testing activities with that wheel loader. It was impressive the amount of analysis we could do with a simplified setup and how we could link the different applications. We could prove the importance of using multi-physics testing systems allowing to execute different analysis in a single test data stream. This bring efficiency to the development process and makes sure that end-user will have a pleasant experience while operating their machines. We did a lot in one day, but at the same time many other activities could follow with the same tools. These activities have all one common goal: further optimize or improve the NVH comfort.
Are you interest in deep dive into these and other Heavy Equipment Testing activities? If yes, I invite you to watch our upcoming live webinar “Maximize cabin comfort of heavy equipment with vibro-acoustics simulation and testing”.