Technological Innovations in The Siemens Opcenter Execution Core Family

COVID-19 is still impacting health and safety around the world. The agility of medical device manufacturers is as challenged as it has ever been. Products are becoming more complex, and companies are feeling the pressure to innovate quickly and deliver products to market faster. With increasing complexity comes increased regulations, especially in the medical device industry. To overcome today’s manufacturing challenges, organizations need a solution that will allow them to react quickly and easily at any time and for any reason.
The Voice of Smart Digital Manufacturing is a 10-part series podcast which will focus on the impact smart digital manufacturing is having and what to expect from it in the future.
In this third episode Bettina Pruemper is joined by two guests from Siemens Digital Industries Software – Martin Russell from Opcenter Execution Core Product Development, and Silvio Saouaf, Product Portfolio Manager. They’ll help us understand how Siemens is introducing new architectural innovations that are being utilized to transform manufacturing.
[00:00:10] Bettina Pruemper: Hello, everyone, and welcome back to the Voice Of Smart Digital Manufacturing – a 10-part industry podcast dedicated to the industries of tomorrow and how they can be enablers of fundamental innovation and disruption; a place that brings the promises to allow today’s listeners to meet tomorrow’s innovation. I’m Bettina Pruemper and I’m your host with Siemens Global Marketing.
[00:00:32] Bettina Pruemper: Before we start, let’s shortly recap our last episode. We focused on the medical device industry and talked to Dr. James Thompson about leveraging the digital infrastructure in order to accelerate growth in the MD&D industry. So, if you missed it, I would recommend you go back and listen to it.
[00:00:51] Bettina Pruemper: Today, in our third episode, Technological innovations in the Siemens Opcenter Execution Core family, we will focus on how Siemens digital infrastructure on the one side and technological innovations on the other side are the keys to unlock advancements and innovations to industries at any levels. And doing this, the companies can not only improve substantially the system’s performances but they can also be cost-efficiently while meeting the highest in the quality. So, by saying this, I’m pleased to introduce two special guests today: Silvio Saouaf, Product Portfolio Manager at Siemens Digital Industries Software, and Martin Russell, Startup Leader also at Siemens Digital Industries Software. Welcome, Silvio, and welcome Martin. Thanks for joining us today to talk about how digital infrastructure accelerates growth in the manufacturing industry of the future. We are happy to have you here today.
[00:01:45] Silvio Saouaf: It’s great to be here.
[00:01:47] Martin Russell: I’m happy to be here too, Bettina.
[00:01:49] Bettina Pruemper: Silvio, you have been working in the enterprise manufacturing software space for quite a long time. So before we start, could you please share a little bit about your background and role at Siemens with our listeners?
[00:02:01] Silvio Saouaf: I’ve been working in this space for over 20 years. I started as a consultant, building solutions for manufacturers, then moved into a role in technical pre-sales, spent some time as a Quality Assurance Manager. But for the last 15 years I’ve been working as a Product Manager and a Portfolio Solution Manager for the Opcenter Execution Core product family.
[00:02:22] Bettina Pruemper: Silvio, thank you for sharing these insights about you. What about you, Martin? Could you tell our listeners a little bit more about your background?
[00:02:29] Martin Russell: Sure. I’ve also been working with manufacturing software for over 20 years. With Opcenter Execution Core, I’ve had multiple roles both in services as well as product design and development. Currently, I’m the Startup Lead for Opcenter Core Execution. Until my new role, I have been leading various development efforts for the past 10 years.
[00:02:53] Bettina Pruemper: It’s quite a vast array of experience.
[00:02:56] Silvio Saouaf: Speaking for myself, I think it’s really helped shape and influence my experience in this area, allowing me to understand the many different roles and needs of our enterprise manufacturing software customers.
[00:03:09] Martin Russell: For me, it helps create a deep understanding of our products and how we can position them to solve the manufacturing challenges our customers face every day.
[00:03:18] Bettina Pruemper: I see. Speaking of the needs, Silvio, what are the challenges and needs that you see in the manufacturing space today?
[00:03:25] Silvio Saouaf: That’s a great question, Bettina. As you know, the manufacturing space really is as challenging as it’s ever been. Manufacturers are building products that are increasingly more complex while needing to innovate much more quickly and deliver new products to the market faster than ever. For some industries, such as the medical device industry, you have increased regulations that certainly add additional burdens on top of those existing challenges they have today. And they have to achieve all this while maintaining a very high level of product quality, as well as controlling or even reducing their costs. It’s a perfect storm of challenges coming together. This in turn means that manufacturers expect even more from the applications that they deploy in order to help manage their increasing manufacturing complexity.
[00:04:14] Bettina Pruemper: Wow, Silvio, that sounds like the manufacturing space is challenging enough but we were exposed to a global pandemic. So, how did COVID impact manufacturers?
[00:04:25] Silvio Saouaf: That was certainly a challenging time and continues to be a challenging time. We saw the impact COVID had on the health and safety of people but it also really challenged the agility of many manufacturers. We saw the compassion and willingness of many manufacturers as they quickly changed gears to produce products that they’d never produced before. For example, you have car manufacturers like Tesla, GM, and Ford that switched some of their production facilities from making vehicles to making these urgently needed ventilators. While this agility was greatly needed, it really did put even further stress on these manufacturers and emphasized the importance of having a strong manufacturing execution system that can allow them to quickly and easily react and adapt their manufacturing processes at any time for any reason, all while supporting the volume of data and application performance that they need to have true granular control over their manufacturing processes.
[00:05:29] Bettina Pruemper: It certainly was great to see everyone jumping in to help during the pandemic. So, Silvio, speaking of helping, what are some exciting innovations that Siemens is working on in the manufacturing space to actually help manufacturers to deal with today’s challenges?
[00:05:47] Silvio Saouaf: Thank you for the question. There’s a lot of exciting things that we’re working on and we’re very proud of at Siemens. We’re introducing a number of architectural innovations to improve the deployability, supportability, and maintainability of the Opcenter Execution Core product family. We’re also delivering some greatly enhanced application performance improvements to support the growing demands of having more granular traceability as well as increased data volumes. And with our 8.6 release, we will be delivering a brand new high-performance transaction engine.
[00:06:20] Bettina Pruemper: That definitely sounds exciting. So, can you tell us a little more about this new high-performance engine?
[00:06:26] Silvio Saouaf: The High-Performance Engine is this new transactional framework within the Opcenter Execution Core application that supports transaction processing at a significantly higher performance rate than the typical or standard transactional framework. This new framework essentially runs in parallel to the existing standard transactional framework. This means that both new and existing customers can take advantage of this new framework. For existing customers, as they upgrade to version 8.6, all their existing transactional investments are protected and carried forward – we know how important that is as customers upgrade. They will not lose anything, but they will gain the ability to leverage this new high-performance transactional framework. We will not only deliver this new framework but also a set of out-of-the-box transactions built on this new framework that customers can take advantage of immediately. And as always, we will continue to expand the catalog of these out-of-the-box transactions, but customers can easily extend them to create their own or even modify existing transactions. Our goal is to provide a solution that’s highly flexible and extensible.
[00:07:36] Bettina Pruemper: That seems like it could be valuable for all manufacturers. So, can you give us some use cases of how manufacturers could leverage this high-performance framework?
[00:07:47] Silvio Saouaf: This capability really can help manufacturers in any industry, it’s not limited to a particular industry. One industry, in particular, that would greatly benefit from this new framework is the semiconductor industry. The semiconductor industry has a great demand and need to support single-item tracking. This tracking can be at the device level or even at the individual die level. For example, some manufacturers make insulated gate bipolar transistors – or IGBTs, as they’re called for short – and they make them in lots of several thousand. Each of these IGBTs are multi-chip modules that are comprised of many, many components. Semi-manufacturers start these units of tracking for each module and also track all the activity performed against each and every IGBT, such as associating and disassociating those IGBTs from carriers, moving them, sorting them, and terminating defective devices. So, as you can imagine, that is a lot of activity that must be executed and tracked against each of these units. We have other semi-manufacturers that convert their wafers into a strip of die which are called sliders. Now, a wafer can yield tens of thousands of sliders, and each slider, again, must be tracked individually. Once again, that’s a lot of activity that must be tracked against thousands of items with really minimal to no performance impact required. In the box build industries such as electronics and some segments of the medical device industries manufacturers have to manage devices that have a bill material composed of several thousand components – quite large and significant. This can be a nightmare to manage from an assembly process but also from a repair process. Imagine receiving a defective device where you have to diagnose and troubleshoot and then repair against a list of thousands of components. And if the complexity was not enough of a challenge, these manufacturers cannot afford any system performance impact as they process these large lists of components – performance must support the process. They need a system that can provide them with the flexibility to manage this ever-increasing complexity, as I mentioned before, while delivering the speed and agility that they must have. The high-performance engine provides that flexibility and speed.
[00:10:10] Bettina Pruemper: That’s impressive. We would definitely like to learn more about it. Could you share an example with our listeners?
[00:10:17] Silvio Saouaf: We performed a comparison of the time it would take to create multiple containers, which are our units of tracking. As the number of units increases, we saw system performance continue to improve. For example, if you were to start a thousand units simultaneously, with a traditional start transaction, it would take approximately 30 seconds. But with a start transaction that’s built on the high-performance engine, starting this thousand units simultaneously only took about three seconds – that’s a 90% improvement in performance time, and that’s significant, and really will greatly benefit our complex manufacturers.
[00:10:57] Bettina Pruemper: Wow! The high-performance engine is certainly compelling innovation for any manufacturer. Thank you, Silvio, for your time.
[00:11:05] Silvio Saouaf: My pleasure.
[00:11:06] Bettina Pruemper: But there are also some more key architectural and technological innovations from Siemens to further drive customer value. Is that correct, Martin?
[00:11:17] Martin Russell: Yes, Bettina. We are currently looking at a major shift in our application architecture that will allow us to adopt a containerized model for Opcenter Execution Core and the other products that sit on top of it. When you think about our application, currently, it’s really a traditional monolithic type of architecture with multiple layers to it. And we’re now going to take that and put that into a more flexible architecture that’s within containers as we move forward. Our application has always been a traditional N-tier architecture that starts at the persistent layer with the database at the bottom and moves up through the presentation layer and our portal at the client level. For customers, this creates a really big monolithic application. We’re moving forward with an approach that will utilize the containers to allow our application deployments to be a lot more flexible to our customers. This is really important, I think, for all of our customers. Our current models that we look at involve a lift-and-shift type strategy when you adopt and attempt to look at going to the cloud. The challenge with lift and shift, in general, is you are seeing a similar type of application architecture and technology in the cloud that you would have on-premise. This really is not working that well in terms of cost savings for our customers. It still requires them to get the same prerequisite software. It requires them to get the same licensing. And so they really don’t see any gains in savings at all. A containerized approach provides a much more elastic model that is easily scalable, both on-premise and in the cloud. So, if you’re a customer and you’re looking at an infrastructure model, basically, within your own walls or in the cloud, this type of approach really works well. We leverage software packages like Docker and Kubernetes that allow us to greatly reduce the amount of time spent in supporting and servicing applications. Tasks that involve deployment, monitoring, and upgrading can be done in far less time, especially as you scale a single site and start going across the enterprise, those time savings can greatly add up. For us, this also opens the gateway for additional modularization of our applications. So, we’ve wanted to start first with containerization, and now start looking at how we can break the application up even further into more manageable pieces. Ultimately, Bettina, this all comes down to reducing the cost of ownership for our software in terms of hardware, software licensing, and operational costs. And we hope that’s of great value to our customers. How are we doing this? Well, once again, we have this monolithic architecture that’s really a vertical stack, and we’re taking each of those layers, and we’re breaking them apart and flipping that on its side into a horizontal model where each of those layers then becomes its own container. And so in that regard, the application server becomes a container, the web services become a container, the UI portal becomes a container, all the additional services become individual containers as we go along. We then look at the application in that mode and we identify common services that actually can be used and leveraged across multiple sites within the enterprise, and we take those and group those together. And so now those don’t need to scale now instead of each site having an individual copy of those, we can use one copy of those services for all of the sites across an enterprise that need to use them. This also allows us to identify the services that will be unique for each given site in an enterprise implementation, and for those then you would have an individual container. As we continue on with that approach, we also adopt a DotNet core architectural base that greatly reduces the operational system dependencies. We’re no longer tied to Windows at that point, we can reduce the cost of that OS for our customers as well. Finally, we stay and leverage standard commercial type of technologies like Docker and Kubernetes to manage and orchestrate the container deployments. This allows us to stay technology agnostic. We don’t want to be tied to one cloud technology, or one operating system technology. We really want our customers to be able to decide on which path they want to go. This is a lot of work that we’re currently working on. We’re expecting our initial releases of this in the coming year, in 2022, as we continue to roll out software next year.
[00:16:10] Bettina Pruemper: Wow, that sounds really fascinating, Martin. So, since we are all very curious, of course, only if it’s allowed, could you tell us of a real case where deployability, maintainability, and supportability have been improved?
[00:16:27] Martin Russell: Sure. We’re still very early in the process of this change in our architecture but we are already generating a lot of interest in this area. We are actually working directly with a very large customer in the medical device space to help realize their enterprise-wide global manufacturing as they shift from an on-prem model to a cloud model. This has really been beneficial to our team. The actual hands-on working with that customer is allowing us to work through a lot of the scenarios that will need to be supported, not just in the software areas and technology but also the areas of qualifying a solution for use which is critical in regulated industries.
[00:17:10] Bettina Pruemper: Interesting. Unfortunately, we are already at the end of today’s episode. So, thank you, Silvio, and thank you, Martin, for joining this discussion on technological innovations in the Siemens Opcenter Execution Core family. We are really looking forward to talking to you again in the future.
[00:17:28] Silvio Saouaf: Thank you, Bettina. And thank you for inviting us.
[00:17:30] Martin Russell: Thank you, Bettina, very much.
[00:17:32] Bettina Pruemper: Of course, and thanks to our listeners for listening to this episode. If you enjoyed it and you want to stay up to date with the latest digital industry stories, click the subscribe button and leave us a review and rating to help us spread the message of these extraordinary visionaries. We have recorded over 10 episodes, and we want to bring you more exciting content just like this. In the meantime, we will be working hard and putting together episodes for your auditory pleasure. Also, for further information, you can visit us online at siemens.com and use the contact section to reach out to us. This is the voice of Smart Digital Manufacturing. And I hope you will join us again for our next podcast episode.
In this episode, you’ll learn
- The challenges manufacturers are facing today (03:20)
- How COVID-19 impacted manufacturers (04:23)
- Solutions that Siemens have developed to help manufacturers face today’s challenges (05:38)
- How the high-performance engine in Opcenter works (06:23)
- Application containerization and its benefits (10:57)
Connect with Silvio Saouaf:
Connect with Martin Russell:
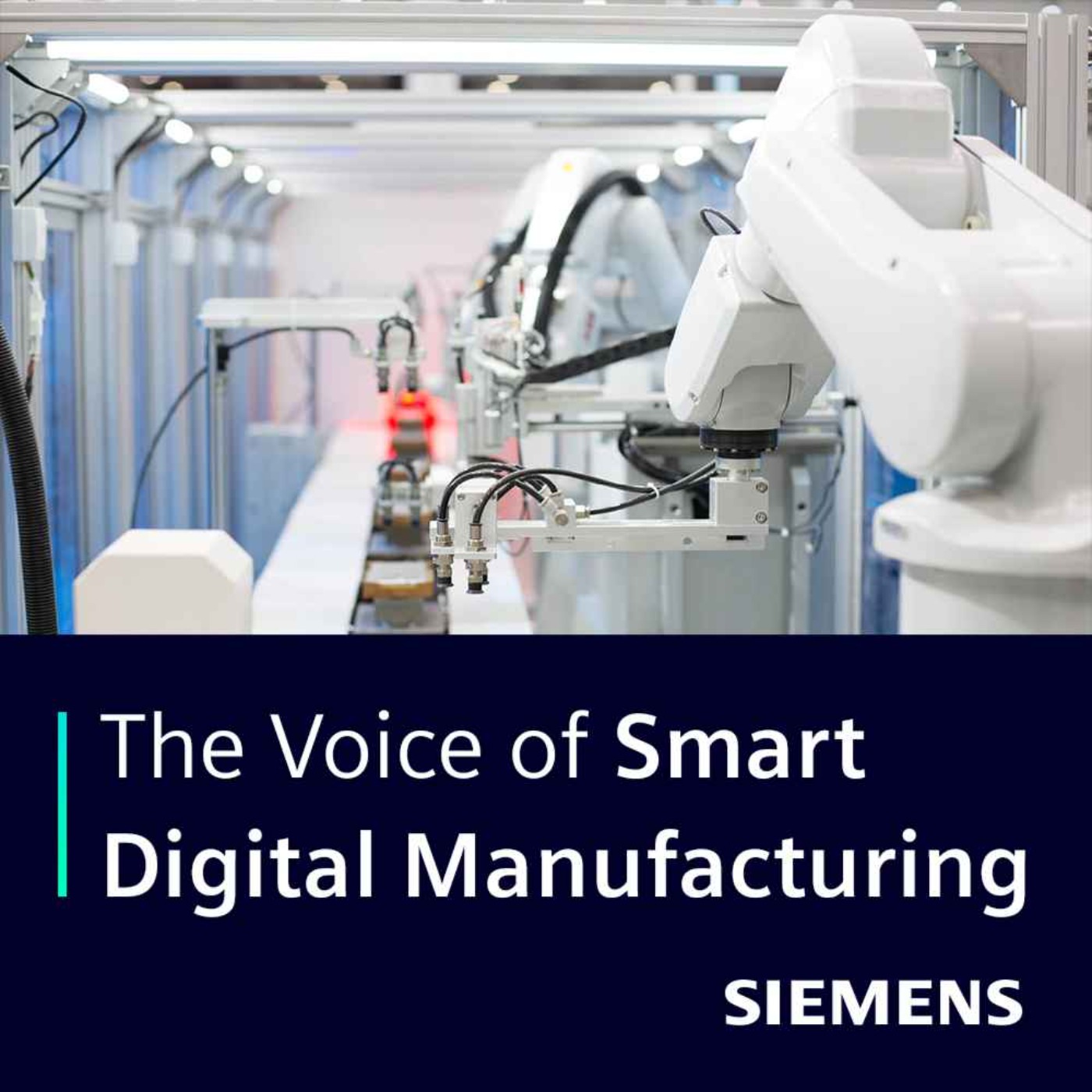
The Voice of Smart Digital Manufacturing Podcast
The Voice of Smart Digital Manufacturing is a podcast dedicated to the industries of tomorrow. Throughout 10 episodes, we will invite industry experts to share their experiences on how Siemens enables industry manufacturers – from Medical to Electronics – to become leaders, by leveraging the digital infrastructure to accelerate growth and innovation to market while lowering the cost. This series will shine a light on the road ahead for industries that are willing to embrace change brought on by digital transformation. Hosted on Acast. See acast.com/privacy for more information.