How can Medical Device companies avoid manufacturing errors? With Closed-loop manufacturing!
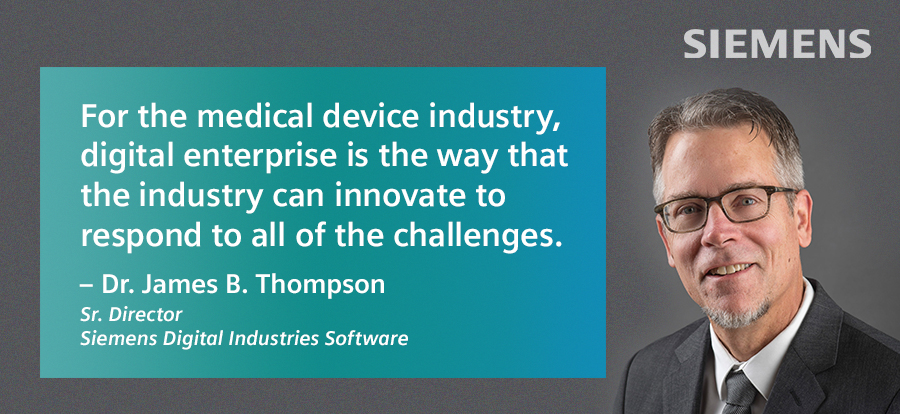
In traditional manufacturing processes, there is a tendency to rely on increasing quality inspections. In the medical device industry, an error on the shop floor can cost people’s lives and safety.
Thus, medical manufacturers demand a more holistic and systematic approach to fully address a product’s risks and minimize errors. Closed-loop manufacturing is a key element of this approach.
In this episode, we focus on closed-loop manufacturing and how it increases efficiency in resource usage and data flow throughout the production line, which is aimed at increasing the quality of product and production efficiency. Closed-loop manufacturing is critical in the medical device industry – an industry that works under a strict regulatory framework.
Let’s discover the benefits that come with digitalizing the manufacturing floor and deep dive into the concept of closed-loop manufacturing and how it relates to the digital enterprise and the digital twin impact it is having on the medical device industry.
[00:10] Bettina Pruemper: Hello, everyone, and welcome back to The Voice Of Smart Digital Manufacturing; a 10-part industry podcast dedicated to the industries of tomorrow and how they can be enablers of fundamental innovation and disruption; a place that brings the promises to allow today’s listeners to meet tomorrow’s innovation. I’m Bettina Pruemper, and I’m your host with Siemens Global Marketing. Before we start, let me remind you of our last Medical Device and Diagnostic episode where we not only talked about leveraging the digital infrastructure to accelerate growth in the MD&D industry, but we also discussed how Siemens digital infrastructure is the key to unleash advancements and innovation in the medical device industry. If you missed that episode, I recommend you to go back and listen to it.
[00:57] Bettina Pruemper: Today, in our last episode, we will again focus on the Medical Device and Diagnostic industry. This time, we will clarify why closed-loop manufacturing critical for the MD&D industry is. Throughout our podcast series, we’ve been talking about the digital manufacturing enterprise and the processes and systems innovations that are unavoidable for medical device manufacturers. For this episode, we will discuss closed-loop manufacturing capabilities, so-called CLM, which create a collaborative feedback loop to improve cost, time, and quality of manufacturing processes. By saying this, I’m pleased to welcome back today’s special guest, Dr. James B. Thompson. He is Senior Director for Industry Strategy, Medical Device and Pharmaceutical at Siemens Digital Industries Software. Hi, James. Thanks for joining us again.
[01:52] James B. Thompson: Hi, Bettina. Glad to be here again.
[01:55] Bettina Pruemper: Before we start, could you tell our listeners why you’re so passionate about the MD&D industry? And maybe also, in general, what fascinates you about working at Siemens?
[02:06] James B. Thompson: Well, I’ve invested a lot in the medical device industry. I’ve been focused on working in and around the industry for the last 17, 18 years of my career here at Siemens. And it’s been a very interesting journey to see the industry evolve in the use of our software. And that maybe gets to what my role is. I’m in an Industry Strategy group here at Siemens, and I’m responsible for our global business strategy for both the medical device and the pharmaceutical industries. I’ve been working in the engineering software industry for most of my career, over 30 years. I’ve been involved in leadership roles, as well as doing some engineering work early in my career.
[02:53] Bettina Pruemper: Well, James, in our previous episode, we not only talked extensively about new restrictive regulations and supply chain changes but also about the COVID-19 pandemic disruptions in the medical device market. But this is just the tip of the iceberg where COVID-19 highlighted the challenges underlying the medical device industry processes and systems that bring the innovation products to market. So, why is the digital enterprise a must-have for medical companies to deliver innovation to the market?
[03:26] James B. Thompson: Well, first, I like the tip of the iceberg analogy that you mentioned. And here, COVID is really just a bit of an example — a very unfortunate example — of the challenges that the healthcare industry and the medical device industry, in particular, were already facing. As we’ve seen through COVID, there’s a large elderly population around the world that is already dealing with diseases and costly care challenges, especially for chronic diseases that are preconditions, in particular, for severe reactions to COVID. And what we see globally is a widely varying healthcare system with regard to accessibility and affordability of diagnosis and treatments. COVID pointed out that that system is further challenged by global supply chains and manufacturing networks that have some vulnerabilities that COVID exposed. So, in some ways, what COVID showed us is that we’re already actually dealing with some global healthcare crises such as diabetes or cardiovascular disease that, in some ways, were pandemics themselves. But let me get back to the part of your question, which was, why digital enterprise? For the medical device industry, digital enterprise is the way that the industry can innovate to respond to all of these challenges. Digital enterprise will allow medical device companies to deal with all of this complexity of designing and manufacturing their products in such a way that it actually matches the very different and varied global needs for delivery of healthcare, associated with those medical devices so that they’re more affordable and more accessible not only in western countries like the US and Europe but around the world in more remote places like in Africa or India where they can’t afford the high cost of healthcare. Also, the digital enterprise will allow for more localized and distributed global manufacturing that deals with these newly recognized challenges and vulnerabilities in the global supply chains. So, another aspect that I think is important, too, for digital enterprises is if we look to the future, that it can serve as a platform for new kinds of innovations for healthcare, diagnosis, and treatment. Things like personalized medicine that leverage technologies such as additive manufacturing which can allow medical device makers and healthcare providers to create customized devices and treatments, and also can serve as a platform for collaboration to exchange patient data between healthcare providers and medical device experts to make sure that patients are receiving the best care possible.
[06:25] Bettina Pruemper: Wow! Impressive responsibility. I mean, the medical industry really is in the spotlight with so many challenges to face, James. We know that with greater complexity comes the greater probability to commit errors in manufacturing. And, I mean, a serious error that leads to adverse events can result in product recalls. So, how can medical companies avoid errors and have an integrated overview of manufacturing processes?
[06:53] James B. Thompson: Let’s first look at how medical device companies are trying to solve this problem today. Using current traditional manufacturing processes, even the best ones, there’s a tendency to rely on increased quality inspections, and this typically is just not good enough to adequately reduce the risk of errors, and ultimately, the possibility of a recall associated with an adverse event that would be caused by some sort of an error on the shop floor. The bottom line is that you can’t inspect quality and reliability into our product. Rather, you need a more holistic approach, a systematic approach to fully address the risks and to really address the needs on the shop floor to achieve high quality. With our digital enterprise approach, we have a more holistic and systemic method to deal with this challenge and to achieve an integrated product and production lifecycle. Part of that systemic and holistic approach is this idea of a digital twin within your digital enterprise. And what the digital twin is, is it’s a digital model of various aspects of the manufacturing and process as well as the product. So, we create these digital data models of the risks and requirements. We create digital models to define the way in which the assembly of devices comes together or formulated processes bring elements of the medical device together. And we combine all this together to model and simulate the production processes, and in effect, create a virtual reality that allows us to work out quality errors — as well as manufacturing efficiency optimization — virtually before these manufacturing processes hit the shop floor.
[09:00] Bettina Pruemper: This is so futuristic. And that’s exactly when the closed-loop manufacturing comes in. Could you explain to our listeners a little more about why the closed-loop manufacturing is so critical for medical manufacturers? And what do they need in order to implement it?
[09:17] James B. Thompson: Yeah, it is futuristic, Bettina. But also, it’s very realistic. And it’s possible to do this today. Let me explain. So, first of all, we support innovation with this digital enterprise approach that we’ve been talking about. And in doing so, it doesn’t mean that a miracle happens. Rather, it means establishing a foundation for continuous improvement and change. So, you can take this overall approach in incremental steps. And a key element of the overall approach here is closed-loop manufacturing. And that comes along with this digital enterprise approach. And it’s the advanced preparation, and even anticipation that there’s going to be a need for constant improvement and change that is driven by closed-loop feedback. And this closed-loop feedback comes from a couple of different sources. It can come from shop-floor quality control measurements that happen in real-time, that can lead to immediate adjustments of some of the manufacturing control parameters, and immediately have an impact on the production quality. But another way that the feedback comes into play is that these feedbacks may identify the need for more significant changes, possibly in the product design itself that leads to a higher quality product, or maybe even a new way to manufacture the product in which a new manufacturing process is introduced on the shop floor.
[11:04] Bettina Pruemper: That’s incredible. Welcome to the fourth industrial revolution. This really can bring medical companies to the next level. But why don’t we see it implemented universally?
[11:16] James B. Thompson: That’s a good question. Planning, and implementing a digital enterprise and closed-loop manufacturing as transformational technologies, takes time. We’re already working with many companies who are on this journey. And in particular, today, our Op Center solutions, which are the most widely used in the medical device industry for digital manufacturing is the typical starting point. But there’s certainly much more to do. To many of our existing customers, what that means is more effective utilization of this idea of digital twins. And we see particular value in this going forward as we address this COVID issue that we talked about earlier in being able to support more resilient global manufacturing networks, so that if another problem like a pandemic or some other black swan event occurs, that the healthcare supply chain is less disrupted. And for many other customers, maybe new customers, especially smaller or midsize enterprises, what they have is the benefit of our many years of experience already working with other — typically larger — customers. And they can now leverage the knowledge and experience that we’ve gained to be able to implement our solutions in a more streamlined way, in effect to realize the value of this digital enterprise approach in a more cost-efficient way and more quickly.
[12:53] Bettina Pruemper: Wow! That’s absolutely great, James. Unfortunately, this was the last episode of our podcast series. So, thank you, James, for joining today’s discussion.
[13:03] James B. Thompson: Thank you, Bettina. It’s been a pleasure to be part of the podcast series.
[13:07] Bettina Pruemper: It has been a great journey to see how Siemens imagines the industry of the future, and talking to these extraordinary visionaries who are really inspiring for all of us. So, thanks to all the speakers we talked to over the last few months. And most importantly, thanks to our listeners for joining us in this incredible adventure. For any further information, visit us online at siemens.com, and use the Contact section to reach out to us. This was The Voice Of Smart Digital Manufacturing, and our team will be happy to help you with any further questions.
What You’ll Learn in this Episode:
- The role of digital enterprise in the medical device industry (04:40)
- How digital enterprise helps reduce the risk of errors in medical device manufacturing (06:33)
- What is meant by digital twins (07:46)
- The benefits of closed-loop manufacturing in the medical device industry (09:05)
Connect with James B. Thompson:
Connect with Bettina Pruemper:
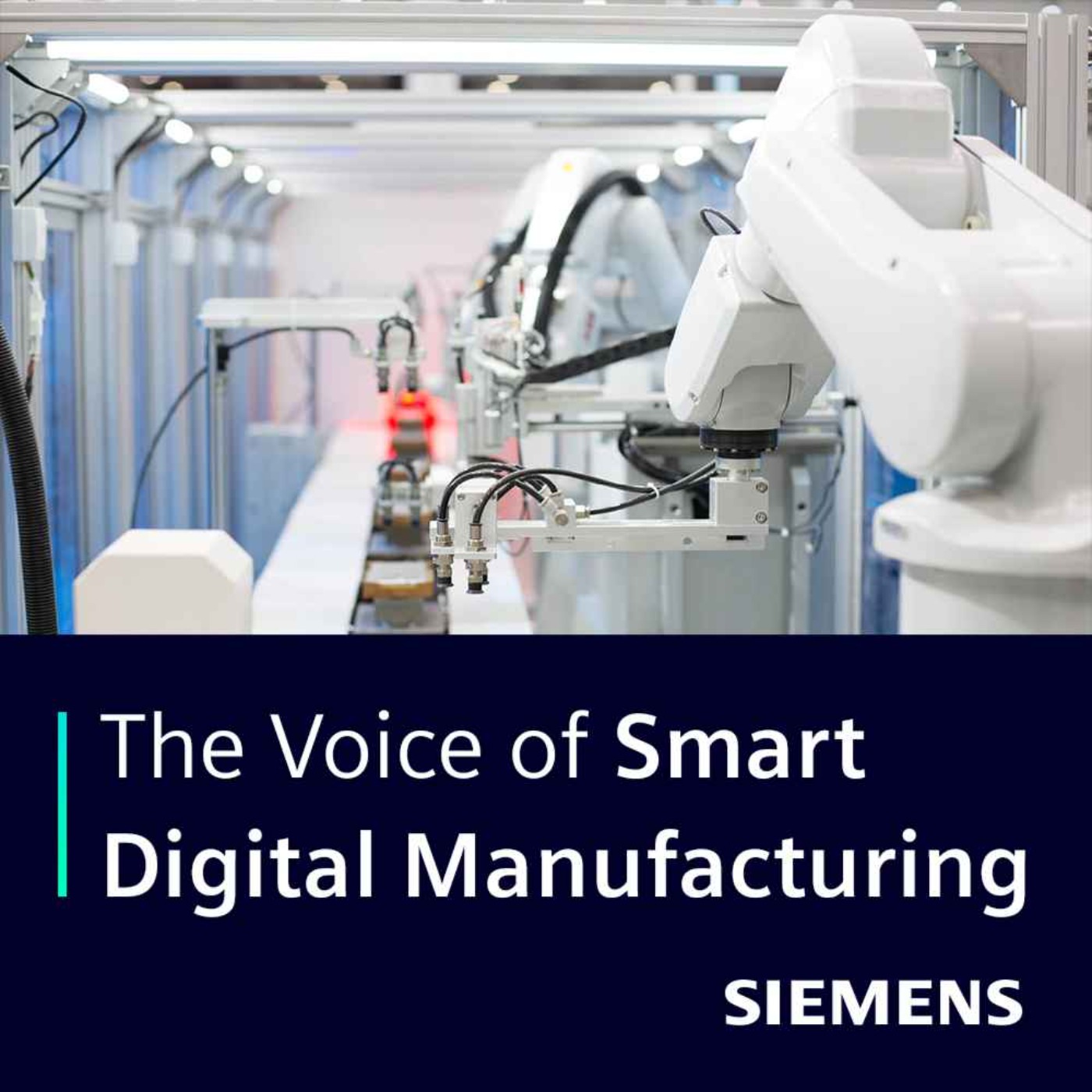
The Voice of Smart Digital Manufacturing Podcast
The Voice of Smart Digital Manufacturing is a podcast dedicated to the industries of tomorrow. Throughout 10 episodes, we will invite industry experts to share their experiences on how Siemens enables industry manufacturers – from Medical to Electronics – to become leaders, by leveraging the digital infrastructure to accelerate growth and innovation to market while lowering the cost. This series will shine a light on the road ahead for industries that are willing to embrace change brought on by digital transformation. Hosted on Acast. See acast.com/privacy for more information.