Digital Transformation for Industrial Machinery
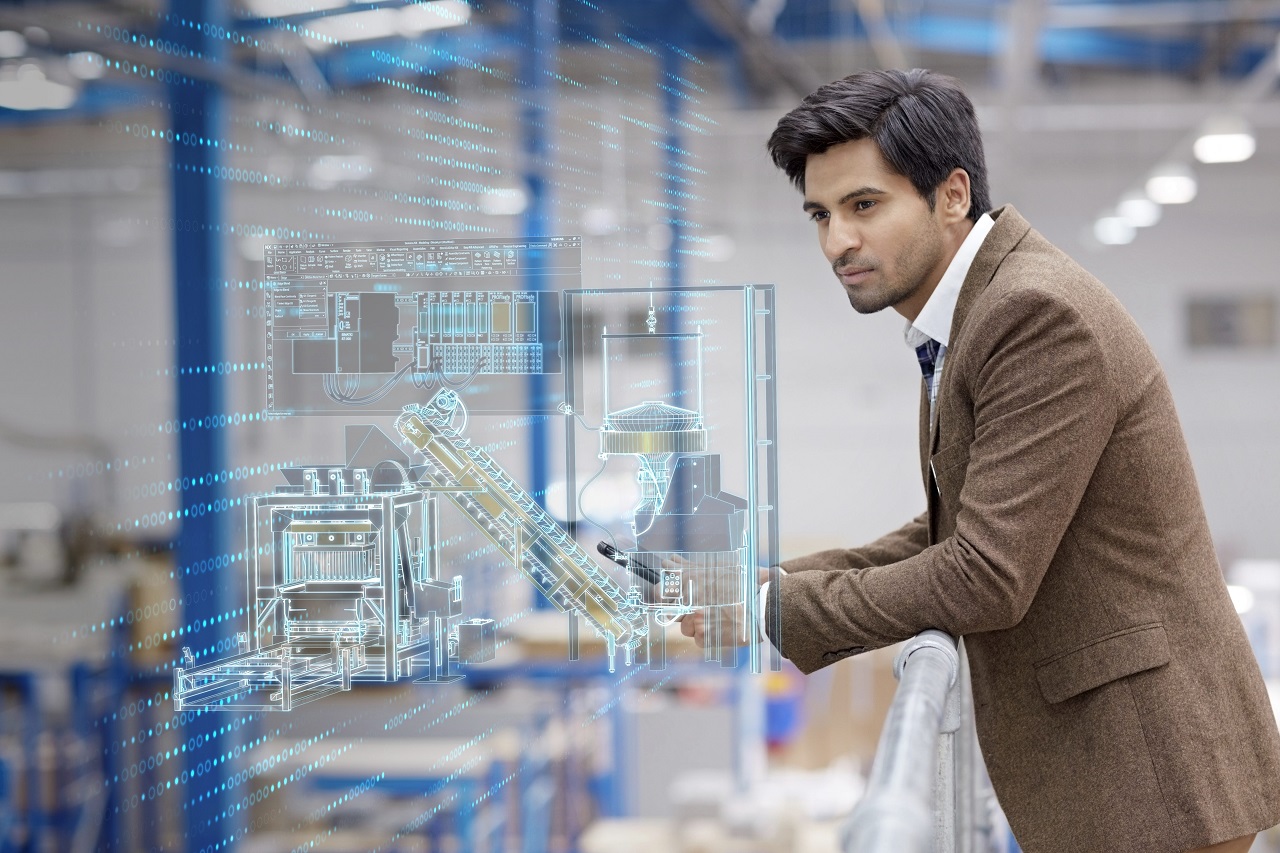
Digitalization is key to increasing the quality of manufactured products and significantly lowering production cost. In addition, it is instrumental in helping manufacturers meet their customer’s diverse customization needs. It comes as no surprise that the adoption of digitalization has accelerated in the last few years as companies seek to remain competitive.
This episode is divided into two parts. In part one, Bettina Pruemper is joined by two guests from Siemens – Ian Hadden, Solution Director for the Industrial Machinery, and Giulia Piovano, Industry Manager focusing on Machinery. They will help us understand digitization in the industrial machinery industry. We will also discuss the critical role played by data in increasing the effectiveness of automated equipment. Finally, you will learn about the digitalization solutions that are currently available and the problems they are solving.
[00:10] Bettina Pruemper: Hello, everyone, and welcome back to the Voice Of Smart Digital Manufacturing – a 10-part industry podcast dedicated to the industries of tomorrow and how they can be enablers of fundamental innovation and disruption; a place that brings the promises to allow today’s listeners to meet tomorrow’s innovation. I’m Bettina Pruemper, and I’m your host with Siemens Global Marketing.
[00:32] Bettina Pruemper: Before we start, let’s shortly recap our last episode where we talked to Oren Manor about the electronics industry. Among other things, we discussed the global pandemic and how digitalization is supporting industry manufacturers to speed up the production and innovation to market while lowering the costs. If you missed it, feel free to go back and listen to it. Today is already the fifth episode and it will be divided in two separate parts. In the first part, we will be focusing on the value that machine builders can achieve when they connect a comprehensive manufacturing operations management system into their digital transformation strategy. And in the second part, we are going to discuss a real case study. To help us explain this topic in greater detail, I’m pleased to introduce two special experts in the industrial machinery and manufacturing operations management field. First, Ian Hadden. He’s the Solution Director for the Industrial Machinery at Siemens. Ian, it’s really nice to have you here today. Before we start, could you please share a little bit about your background and your work at Siemens?
[01:37] Ian Hadden: Hi, yes. Thank you, Bettina. My name is Ian Hadden, and I’ve been with Siemens for over 10 years. My current role, as you said, is the Solution Director for the Industrial Machinery. But before that, I’ve worked with Siemens in the integration space as a Solution Architect for Teamcenter and in the Digital Manufacturing Space.
[01:55] Bettina Pruemper: Thanks, Ian. Our second expert today is Dr. Giulia Piovano. She is part of the Digital Manufacturing team and the Industry Manager for Machinery at Siemens Digital Industries Software. Giulia, could you also share a little bit about your background at Siemens?
[02:11] Giulia Piovano: Hello, Bettina. Thank you. Giulia Piovano speaking. I work at Siemens as the Industry Manager, especially focusing on Industrial Machinery, A&D, equipment, environment, and domain. I’ve been working at Siemens for nine years. And before, my role was Service Manager for A&D customers.
[02:34] Bettina Pruemper: Thanks, Giulia. We are really happy to have you both here today. Let’s get started by taking a closer look at the trends. Ian, what are the key trends that are driving the need for digitalization in the industrial machinery industry?
[02:48] Ian Hadden: When we look at the industrial machinery landscape, we continue to hear from our customers that there are several transformational trends that mark a significant turning point for machinery evolution. There’s a market shift towards personalized products and customized services and machinery companies are challenged to design and build machines that support expanding product mixes and more rapid and frequent changeovers. And because customer preference changes are more immediate, there’s added pressure to innovate quickly and compress delivery schedules.
[03:18] Bettina Pruemper: Okay, so the key trend in the industrial machinery industry is consumer-driven customization. Giulia, are you seeing any of your customers having to address this trend?
[03:29] Giulia Piovano: Oh yes, I can confirm it. This is especially true for customers performing complex manufacturing. There are different manufacturing archetypes inside the industrial machinery niche with different characteristics. Machine builders include, for example, manufacturers of the CNC motion control machines, or producers of trains, conveyors, and special-purpose machines, and this kind of stuff. Machine builders are often large enterprises with production spread among different plants, even in different countries. The production is generally engineered-to-order like. The end customer demand for highly differentiated and customized products drives OEM demand for customized machines. We could, for example, consider the case of Robopac that is a world leader in packaging. The market for packaging machines has changed significantly in recent years, and Robopac customers are requesting customized products more and more. Robopac can offer a very high number of configurations for each packaging machine, and this is one of their key differentiators. In order to be able to keep up with these market trends, they had to transform the production process to make it more flexible and capable to manage the growing requests for customized products.
[05:00] Bettina Pruemper: Giulia, you mentioned how production is now highly engineered to order a result of the demand for highly customized machines. What is Siemens’ value proposition for these needs?
[05:13] Giulia Piovano: Well, for these manufacturers, it is important to ensure the end-to-end management of manufacturing processes, including quality. This will reduce the introduction of engineering changes. The possibility to implement a central engineering feeding different production plants improves the efficiency and the harmonization of know-how among different plants. Well-structured work instructions can guide operators step by step, helping new human resources in the ramp-up phase. And the loop between engineering and manufacturing is closed thanks to the escalation of shop floor issues to design department, leading to actions and improvements. So, our customer experienced a reduction in the cost of quality warranty returns incoming goods inspection times, and also the decreasing of the engineering changing corporation to shop floor from one week to less than a day.
[06:14] Bettina Pruemper: Ian, coming back to you. We just discussed customization. To achieve the benefits, Giulia just described, there’s another aspect that machine builders should consider for their digital transformation blueprint. The need for smarter machines and also how to make this data that is collected insightful and actionable. So, what are your thoughts on this?
[06:38] Ian Hadden: Industrial components suppliers are quickly embracing IoT-enabled technology in their products. This has changed the landscape for electrical and controls automation engineers and production with, for example, the huge increase in input-output channels and new communication protocols like 5G. At the same time, there are insights to be gained from so much information that can be handled by the automation of production processes. The trend for hyper-automation requires vast amounts of data and cloud-based analytics to accelerate learning about machine behavior and performance to automate machine functions.
[07:15] Bettina Pruemper: Giulia, how does the concept of hyper-automation apply to the manufacturing operations of a customer like Robopac?
[07:2] Giulia Piovano: Together with Opcenter, Robopac also decided to implement an AGV system for the automated and intelligent handling of machines along the production process, and the warehouse management system for the digital management of logistic processes. So, all these technologies have been integrated, and they now form the core of the Robopac smart factory. And by the way, talking about smart manufacturing, I really recommend you the article, The Light-Spars Versus The Lights-Out Factory, it describes the factories where the human activities are so minimal that the facilities can operate in the dark. But going back to Robopac setup, this is the typical setup for a first end-tier supplier, where the assembly areas are frequently automated. In these lines, different parts flow one after the other with shorter time — we call this a one-piece flow process. The components to be assembled need to be available along the lines in a very coordinated way in order to satisfy the faster time and minimize the inventory rate or material waste. For these manufacturers, due to limited capacity of the lines, it is crucial to optimize the usage of machines to verify if customer’s due date can be respected and to check the impact of unforeseen production events.
[08:58] Bettina Pruemper: Giulia, in regard to optimizing machine utilization, what can Siemens offer to these customers?
[09:06] Giulia Piovano: Opcenter has the elements to support one-piece flow processes including automated lines with, for example, features like a process interlock. The data can be automatically collected from the machines or scanned with barcodes readers. Kanban capability guarantees the availability of components along the lines. And thanks to the scheduling module, it is possible to optimize the usage of the plant resources, reduce the inventory of the lead time, and rescheduling in case of disruption.
[09:38] Bettina Pruemper: So far in this discussion, we have talked about increased customization which leads to an increase in complexity. This has then led to a unique situation when it comes to global competition. So, it can be perceived as a barrier to some but I think also as an opportunity depending on who embraces digitalization. So, Ian, how do you perceive the state of global competition within the industrial machinery industry today?
[10:09] Ian Hadden: Well, global competition has always existed. But now the competition is coming from more flexible, agile startup companies that start from the basis of machine learning and are not linked with existing complex business processes and legacy customer engagements. In many cases, the aging workforce in many parts of the world has forced employers to replace experience with machine learning, and many machinery companies may not survive this transition.
[10:37] Giulia Piovano: Talking about machinery, a large portion of the market is composed of small-medium companies. Indeed, the work is often organized in job shops by job functions such as welding, machining, finishing, and so on. Job shops like small-medium companies in other industries have specific characteristics, both on business and on the organizational side. They usually have a small number of employees – less than 1000 – and annual revenue less than $1 billion. Therefore, they could have a small or even no IT department and also limited capability to sustain fixed costs.
[11:17] Bettina Pruemper: Okay, Giulia, but which are the specific needs for these small and medium-sized customers and how can a manufacturing operations management solution address them?
[11:28] Giulia Piovano: Well, SMB customers need a MOM solution able to support the rapid deployment to reduce the services time and total costs of the project. They need also flexible contracts with, for example, subscription licenses model, cloud support, also, in order to reduce the upfront cost of hardware. The MOM system needs to provide the core functionalities out of the box, limiting the project risk due to customization and using standard technologies. And finally, flexible user interface including the support of mobile devices. At Siemens, we promote the rapid implementation methodology. Basically, a template based on Opcenter that provides both technical and functional advantages like, for example, the rapid installation and configuration, some integration pre-configured with the ERP system, the scheduler system, and so on, and out of the box reports. In addition, some Opcenter modules are available as a service on cloud, like our offering to perform business intelligence and monitor manufacturing performances.
[12:45] Bettina Pruemper: All right. So, unfortunately, we are already at the end of today’s episode. In the second part of this podcast episode, Marco Cassani will describe Robopac’s case study in greater detail. So, we will not only talk about the challenges but also how they implemented the factory of the future with Siemens. But for today, thank you, Giulia and Ian, for joining this discussion on digital transformation for industrial machinery. We are really looking forward to the second part of the podcast episode.
[13:18] Giulia Piovano: Thanks to you, Bettina, was a pleasure.
[13:21] Ian Hadden: I agree. Thank you. And of course, thank you to our listeners. If you enjoyed it and want to stay up to date with the latest digital industry stories, click the subscribe button and leave us a review and rating.
[13:32] Bettina Pruemper: Also, for further information, you can visit us online at siemens.com and use the contact section to reach out to us. This is the Voice Of Smart Digital Manufacturing, and I hope you will join us again for our next podcast episode.
What you’ll learn in this episode:
- Key trends driving the need for digitalization in the industrial machinery industry (02:44)
- The role of data in automation of industrial machines (06:22)
- The application of hyper-automation in the manufacturing process (07:18)
- Machine usage optimization using Opcenter (09:00)
- The state of global competition and the role that digitalization is playing (10:04)
- How Manufacturing Operations Management (MOM) helps small and medium business enterprises (11:21)
Meet the experts
Ian Hadden is the Solution Director for the Industrial Machinery at Siemens. Ian has worked with Siemens in the integration space as a Solution Architect for Teamcenter and in the Digital Manufacturing Space for over 10 years.
Connect with Ian on LinkedIn
Giulia Piovano is a Industry Manager at Siemens, with a special focus on Industrial Machinery, A&D, and heavy equipment. Giulia been working at Siemens for 10 years. She previously served as a Service Manager for Siemens’ A&D customers.
Connect with Giulia on LinkedIn
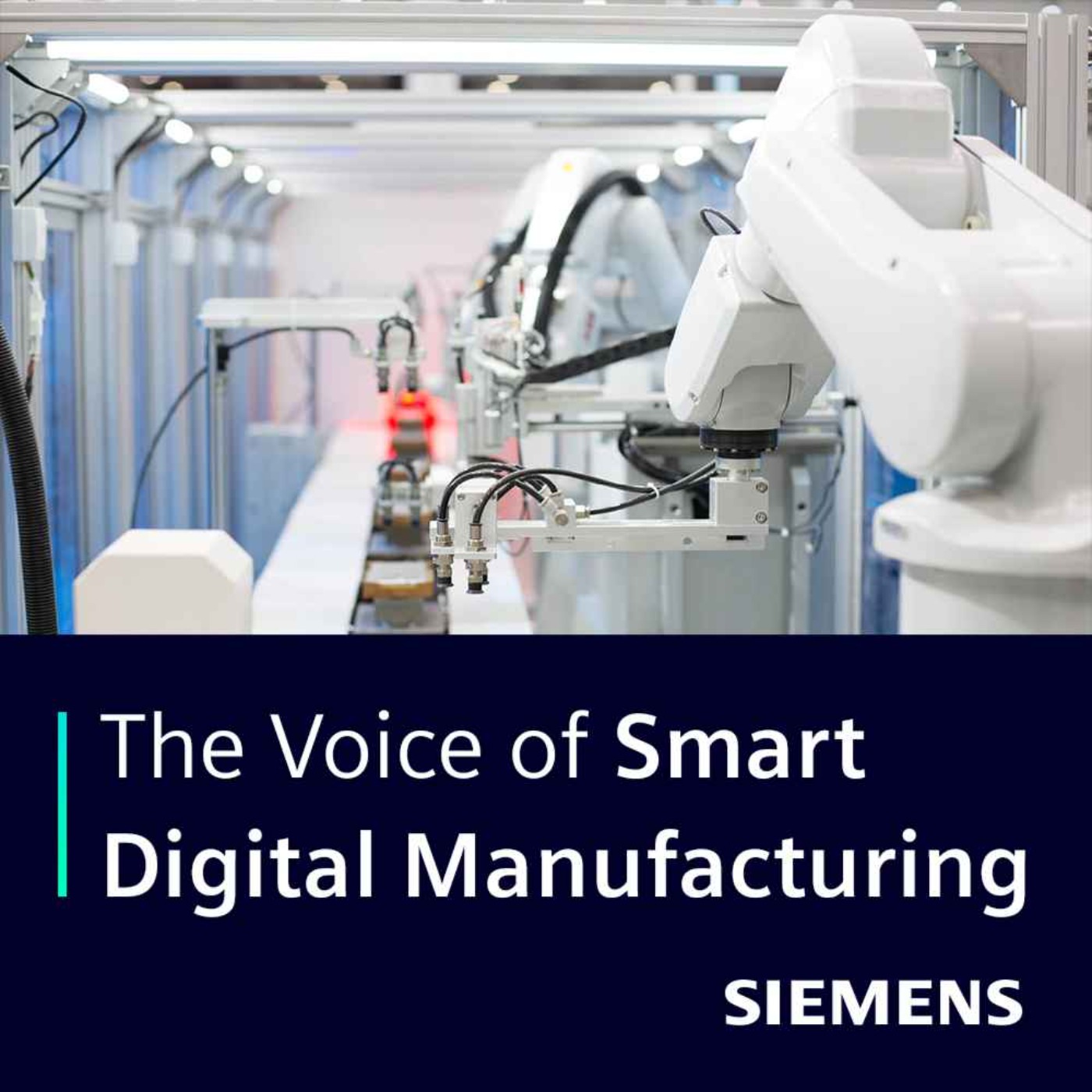
The Voice of Smart Digital Manufacturing Podcast
The Voice of Smart Digital Manufacturing is a podcast dedicated to the industries of tomorrow. Throughout 10 episodes, we will invite industry experts to share their experiences on how Siemens enables industry manufacturers – from Medical to Electronics – to become leaders, by leveraging the digital infrastructure to accelerate growth and innovation to market while lowering the cost. This series will shine a light on the road ahead for industries that are willing to embrace change brought on by digital transformation. Hosted on Acast. See acast.com/privacy for more information.