What’s New in Teamcenter Quality 5.0
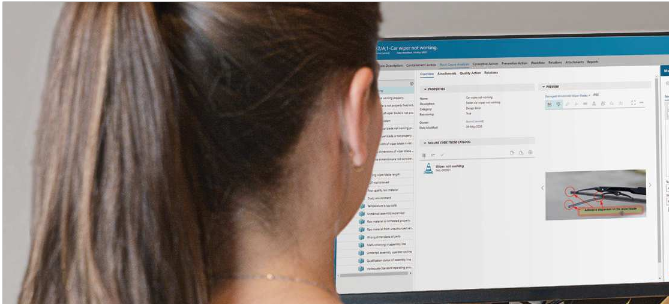
Delivering a holistic quality management solution for Teamcenter
We are excited to announce that the latest version of Teamcenter Quality.
The Teamcenter® Quality product family offers an enterprise-wide solution for capturing various quality issues, customer complaints and nonconformances. It provides a formal process to systematically investigate, analyze and resolve quality issues, streamlines the definition of measures to prevent recurrences, and reports the results in a clear and intuitive manner.
Teamcenter Quality 5.0 delivers the following benefits:
- Control all quality planning phases with clear visibility of customer deadlines
- Reduce time required to resolve problems and mitigate costly rework caused by repeating issues
- Enhanced root cause analysis methods based on engineering data improves user experience
- Traceability from planning through execution with central failure catalog and trigger change
- Issues are fully integrated in the problem solving and change management process flow
- Centralized action management for all quality processes increases transparency and allows consistent monitoring of all quality action types
Already using the Teamcenter Quality? See what’s new in version 5.0
Want to learn more? The Teamcenter Quality vision is to boost the operational excellence with native quality management aspects in NX, Teamcenter, and Opcenter Execution Platforms integrated with our common Closed Loop Manufacturing approach for Industry 4.0.
Teamcenter Quality product family is a set of features native on Teamcenter Active Workspace client, called APQP Program Management, FMEA, Control, and inspection Plan as well as problem-solving. Sharing the same database with other Teamcenter applications, Teamcenter Quality has the capability to integrate seamlessly to other areas of Design Engineering and Manufacturing Planning.
Find out more about Teamcenter Quality