What’s new in Opcenter X 2501
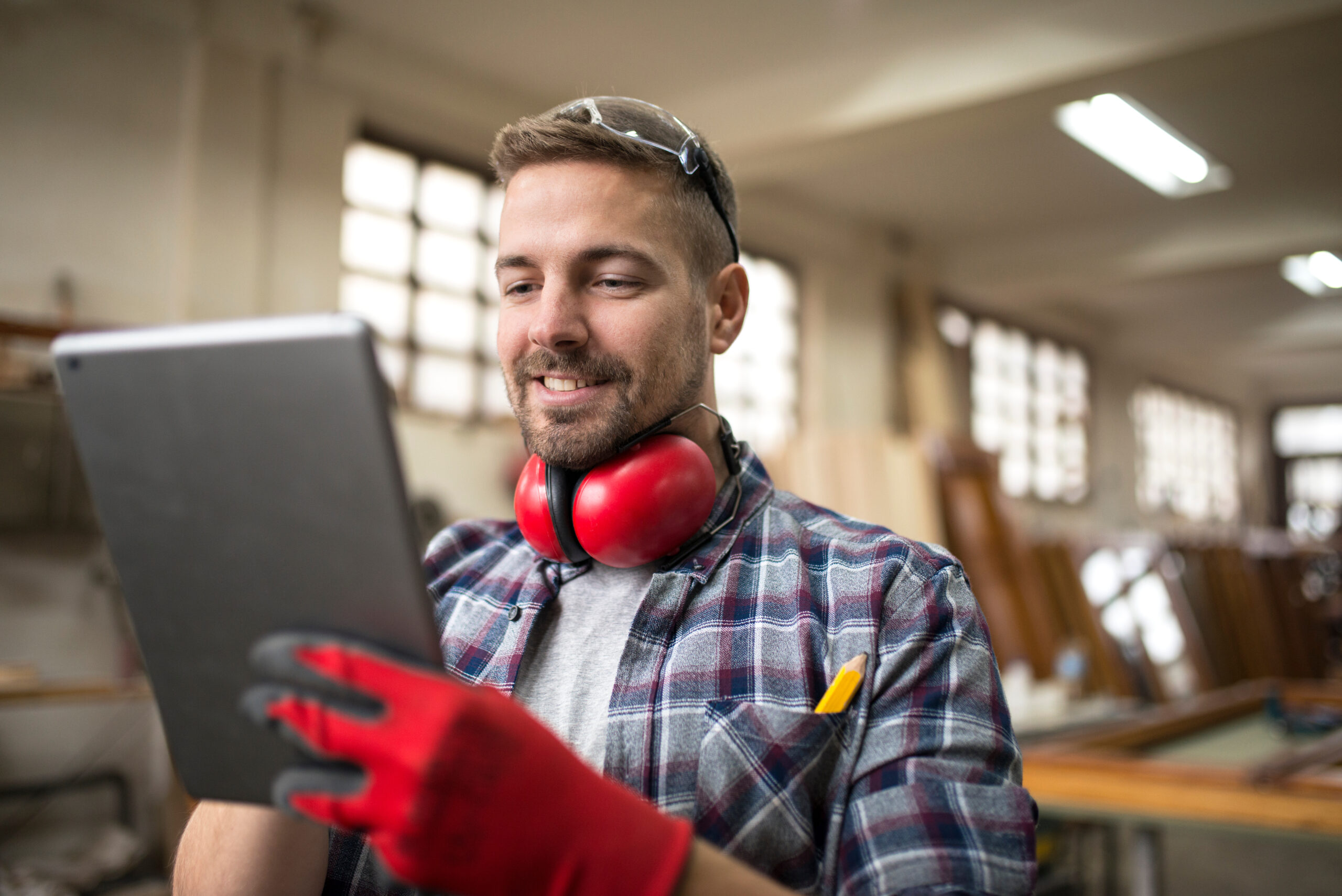
Opcenter X for scalable digital transformation
Summary
Siemens Digital Industries Software is pioneering modular MOM, enabling more manufacturers to take a stepwise approach to digital transformation. Built with cloud technologies and offered as software as a service (SaaS), using Opcenter™ X software, which is part of the Siemens Xcelerator business platform of software hardware and services, lowers the time and cost barriers for SMBs, enabling you to realize rapid return-on-investment (ROI) with modules that connect and adapt as your enterprise matures.
With Siemens as your MOM solution partner, you can be sure Opcenter X is built on a rich and deep knowledge base and the extensive capabilities of a leading software company. We listen to and learn from our customers, then innovate and capture best practices for every digital task. Then we apply best practices to accelerate time-to-value of our software.
With Siemens as your software partner, implementing modular MOM capabilities by using Opcenter X will bring about the manufacturing agility you need to thrive in your manufacturing space, both today and into the future.
MES capabilities
Order management enhancements
- Ability to define a Generic process. Generic process is a process that does not have a relation to a final product thus can be used for any production order.
- During process assignment stage a user can select from a list of either of the specific processes or the generic processes.
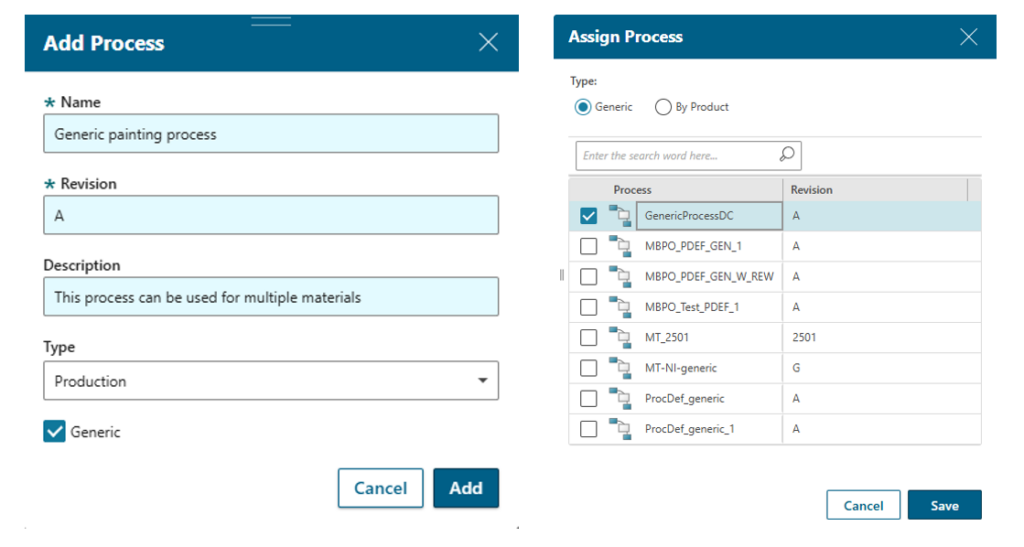
Audit Trail
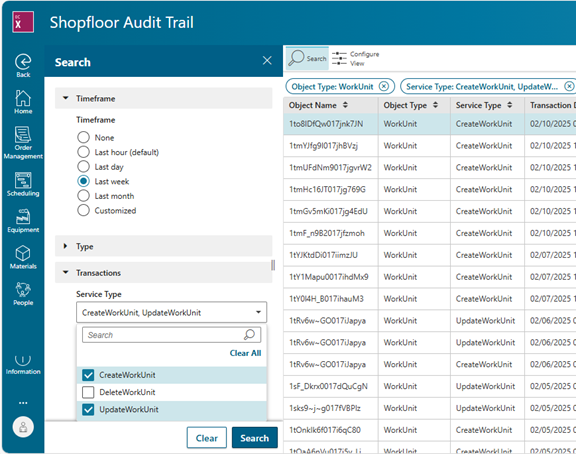
The Audit Trail module monitors a wide range of actions and transactions, making it essential to have flexible filtering options to efficiently manage and analyze the data. To enhance this functionality, the system now allows users to apply multiple filter criteria simultaneously, where applicable. This includes filters such as object type, user, and service type / action. With this improvement, users can select multiple filter options at once and view the results that match all of their selected criteria.
As the Audit Trail module displays several information for each record, users has now the ability to configure and save their own views according to the data they are interested in. The view configuration is stored separately for each user and is categorized by audit trail type (Modeling and Shopfloor). This architecture allows for maintaining separate personalization for each usage type and user, ensuring more effective management of visual preferences and settings.
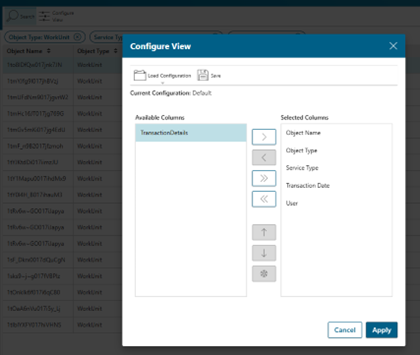
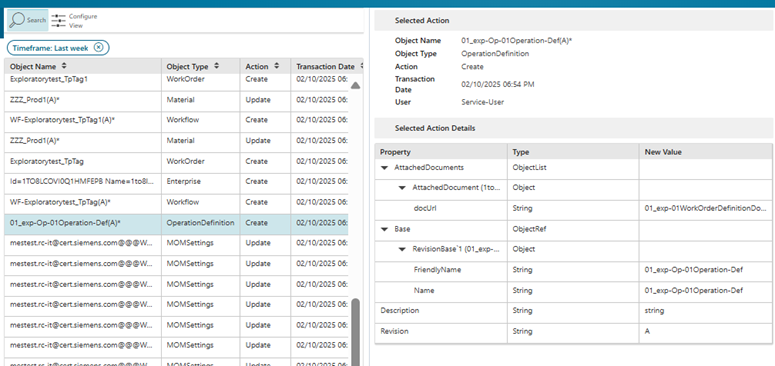
Actions performed on modeling objects can generate Audit Trail records with a nested structure. To facilitate the visualization of these actions, the Modeling Audit Trail user interface has been enhanced to display these records in a tree view format.
Resource management enhancements
As part of this new release, resource management has been enhanced with new features, including a resource usage task, a disassembly task, and the management of the state attribute on the resource administration page.
The resource usage task will enforce the use of the specified resource by the operator. Before performing any manufacturing activities, the operator must identify the resource they will use. During identification, the system checks for coherence between the resource and the specifications defined in the operation. These specifications may include a list of specific resources and/or a list of resource classes.
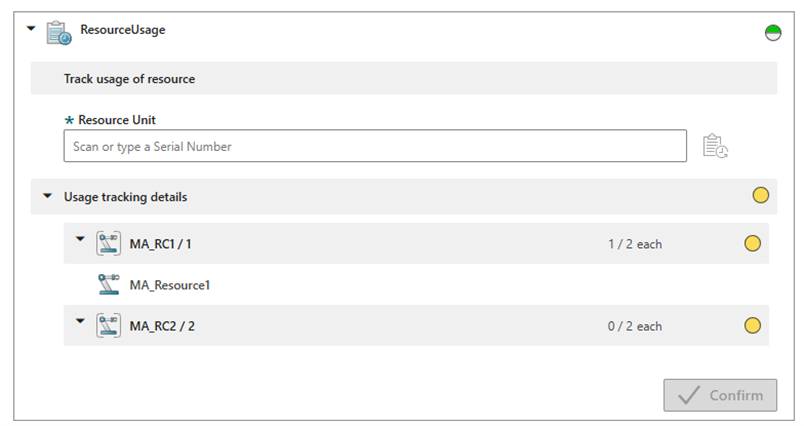
The disassembly task will require the operator to disassemble the specified resource. The operator must identify the resource specified at the operation level. If it matches, the resource will be disassembled, and the different components of the assembly will behave as independent entities.
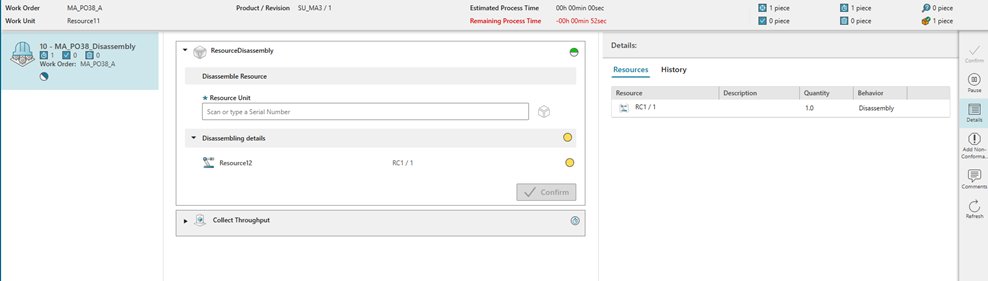
It is now possible to visualize and update the value of the state attributes configured for the resource. Through the state machine management application, designers can define the different states and transitions required by the manufacturing operations. Example of state machine could be for Calibration status, Sanetization or Cleaning status, that will be checked during the manufacturing steps.
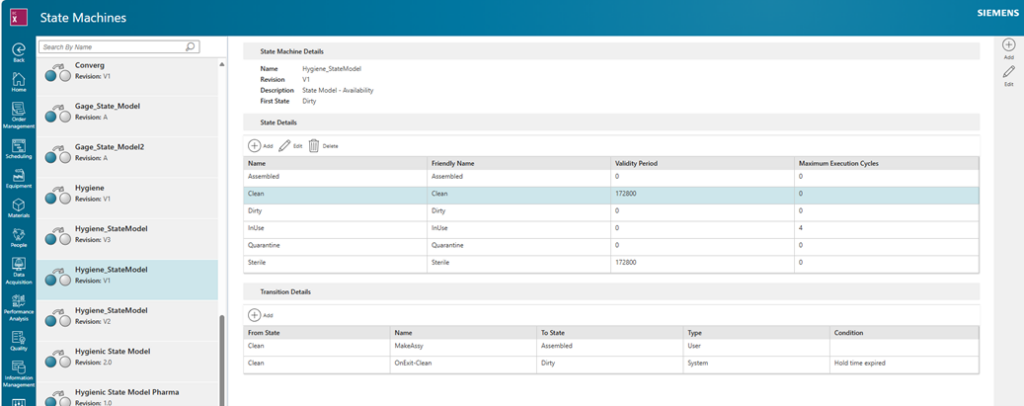
Adding the state machine to the resource classes allows the resource instance to have attributes controlled by the predefined state machine.
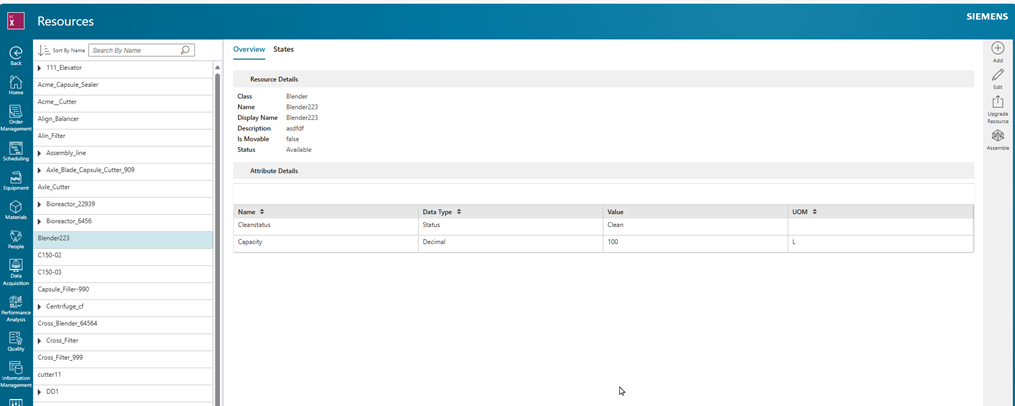
Operators now have the ability to visualize and update these attributes directly from the resource management application.
Quality capabilities
Inspection Plan enhancements
It is now possible to assign a gage group to an inspection step.
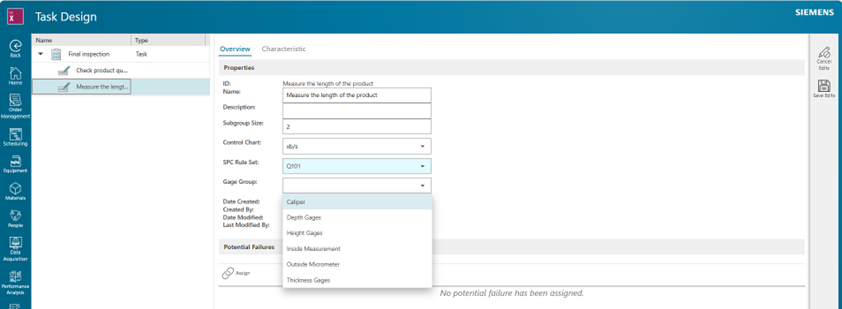
If the user now assigns a gage in the recording, only gages that belong to the gage group are offered.
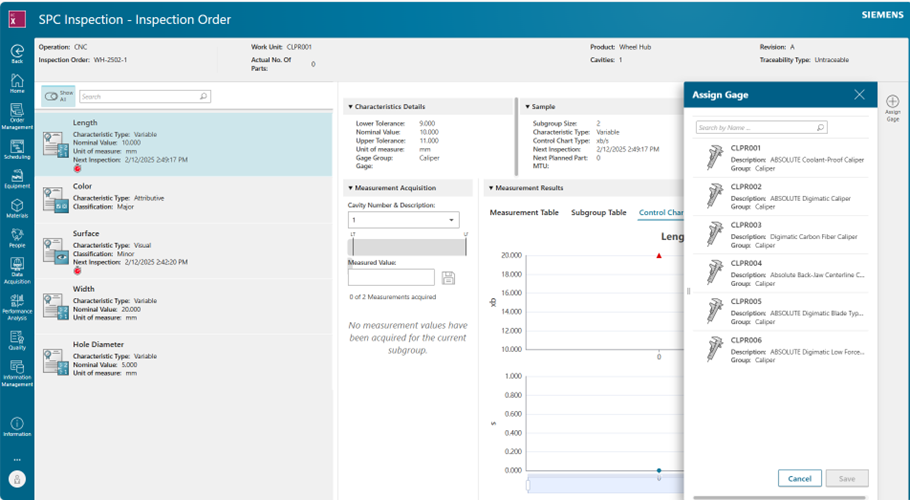
It is now also possible to add an image for a visual characteristic. If you then define the number of columns and rows, a grid can be placed over the image.
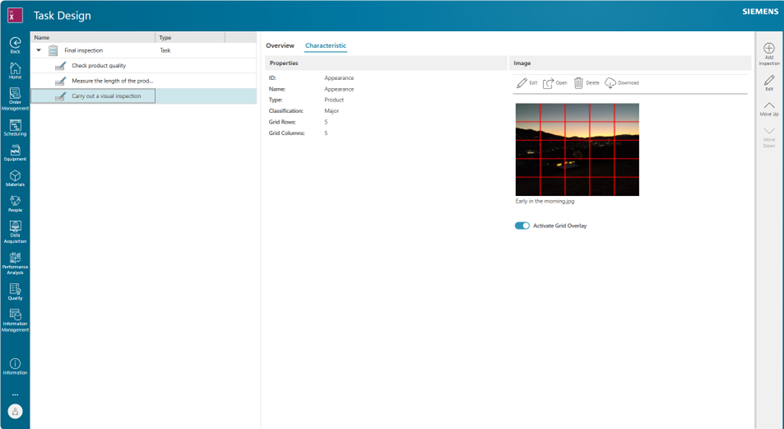
Defects can then be marked with a dot in the recording. The defects are then linked to the grid field in which the dots are located.
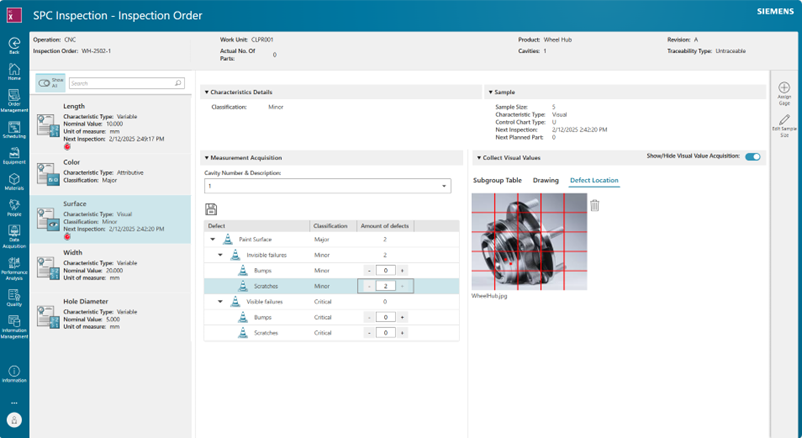
Easier handling of rework
When defining a process, it is now possible to identify certain process steps as rework. If a defect occurs at some point before a rework step in a process step, you now have the following option:
When entering a non-conformance for the defect, you can define at which process step rework is to be carried out:
– directly at the process step at which the non-conformance is created
– or at one of the subsequent process steps, if these have the type ‘Rework’.
SPC optimizations
It is now possible to forward measurement values to an external system. NATS messages are used for this purpose.
Process violations can now also be detected in attributive and visual characteristics. If you are interested in this, please take a look at our manual.
The inspection types initial, in-process and re-inspection, as well as final inspection, are now also supported in the data recording and can be specifically filtered there.
Non-conformance management optimizations
It is now possible to sent the most important data of a Non-conformance by NATS for reporting tasks. The data is used to enhance the existing Work Order Dashboard in the Visibility App.
Teamcenter Share is now connected to Opcenter X Quality for document exchange.
In the case of a non-conformance, it is now possible to assign responsibility without this person having to be assigned a specific action.
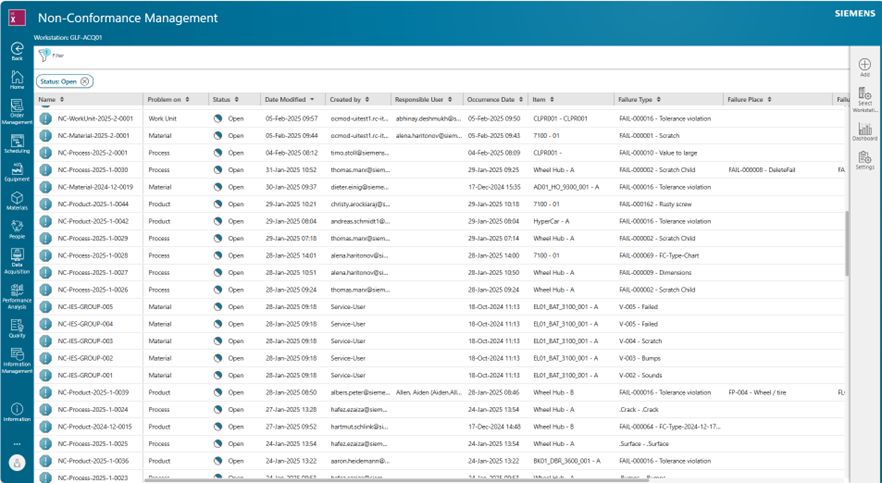
A description can be entered here. This information will also be used later by an AI component. The description is fixed for the non-conformance and exists exactly once.
In contrast to this, different people can enter different comments one after the other, which can then be read in a conversation.
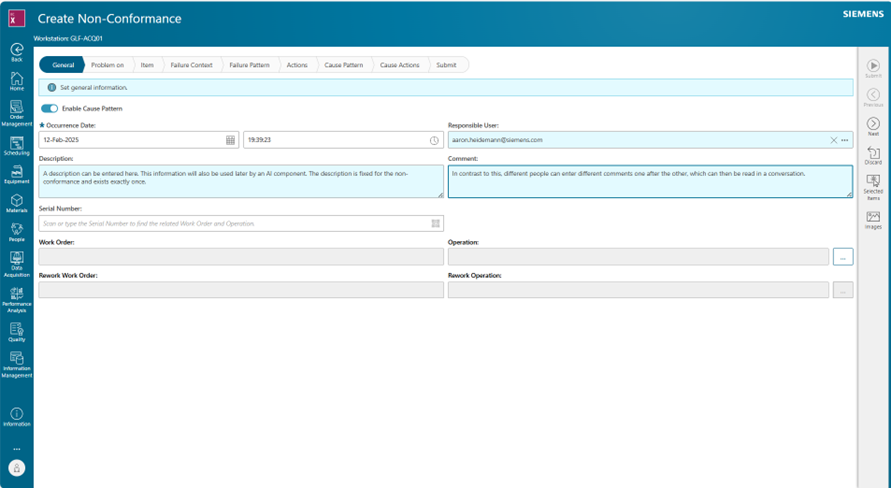
It is now possible to filter all NCs with a URL belonging to a specific work unit.
If a defect is to be documented with the help of photos, these photos can now be taken directly from the application – live.
Configurator capabilities
Adding business logic
Users can now view and edit methods with configurator’s model design. Upon opening a configurable object, the logic tab shows the defined methods. There is both a graphical view and a code view.
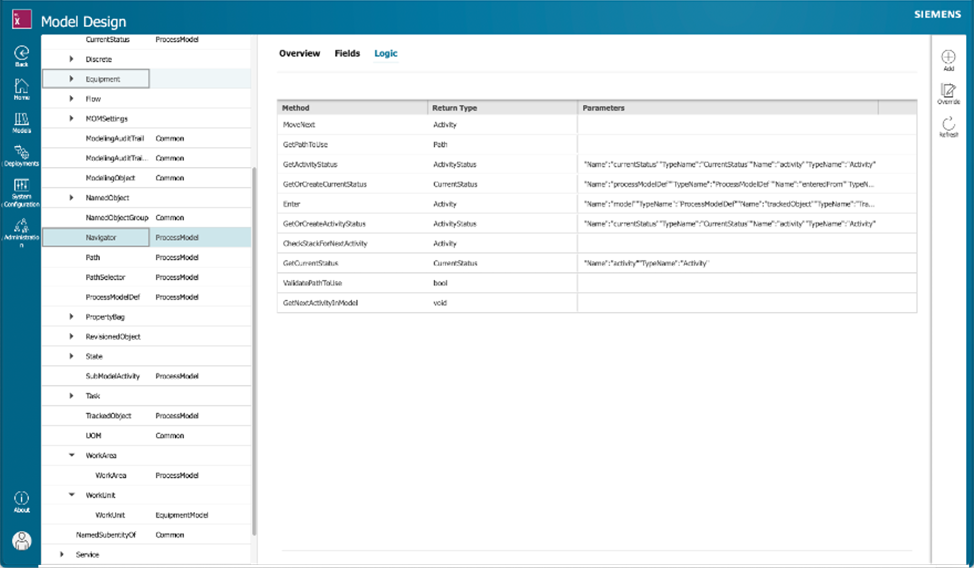
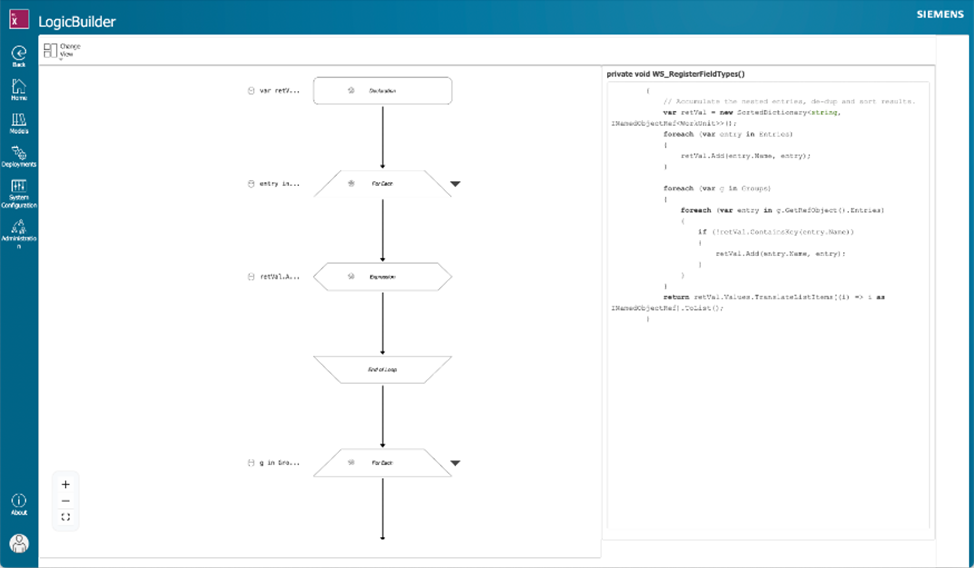
Managing secrets
Users can now add and manage secrets for particular applications of the development and production environments with the configurator’s deployment tile.
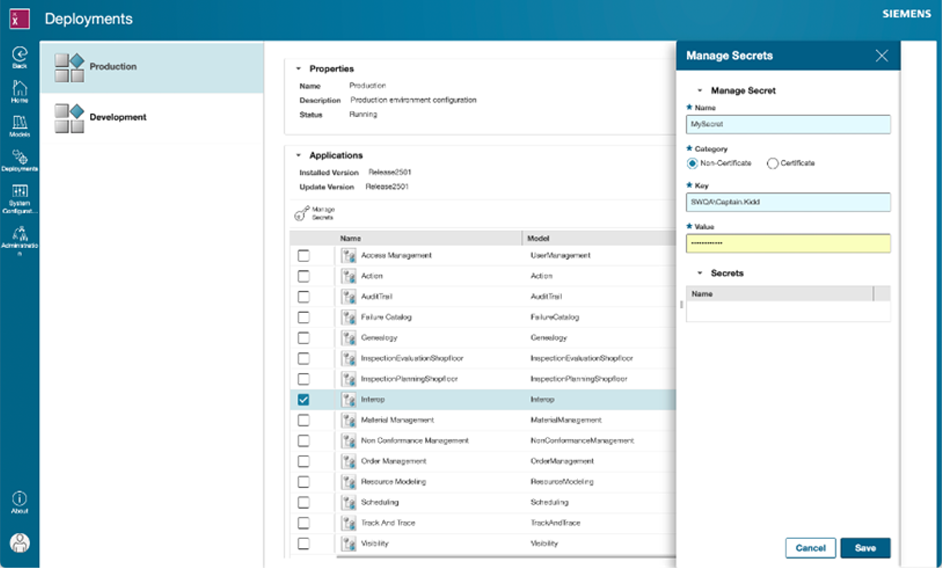
Resetting the development space
Users can now clear the development space and optionally delete the user’s private branch which clears all the changes that have not been pushed to the main branch.
Resetting the system configuration
Users can now reset the system configuration repository which includes the session timeout, allowed document types, model catalog, application catalog and can optionally delete the user’s private branch which clears all the changes that have not been pushed to the main branch.
Scheduling capabilities
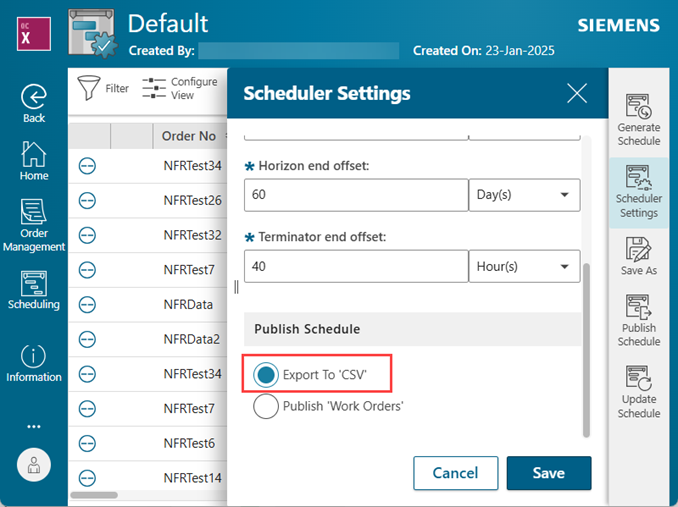
The default schedule can be exported as a comma-separated values (.csv) file for easy sharing or further analysis. It can be achieved by configuring the “Publish Schedule” settings, found under the “Scheduler Settings” feature. After this, the system will generate and save the schedule in a .csv format, allowing you to view it in applications like Excel.
The “Allocate Operation” feature allows planner to manually assign an operation to a specific resource at a chosen time. Operations can be allocated from the Gantt Chart or orders table. This gives you greater control over scheduling by enabling you to plan operations based on your priorities, resource availability, or specific requirements.
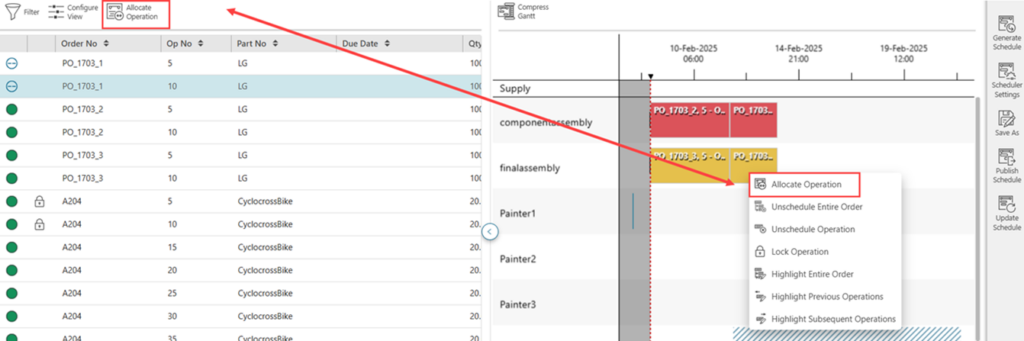
The Scheduling app now supports operations that are aborted in the Order Management app. When an operation is aborted, the not started scheduled operations are removed from the planning board. For in-progress operations, the actual end time will be the aborted time, shop floor status will be “aborted” and planning status will be “scheduled”.
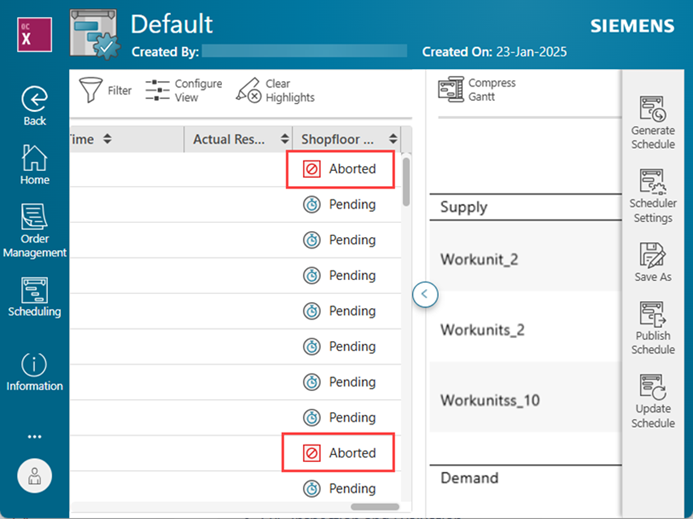
The configuration settings for generating a schedule, specifically the “Direction” and “Order By” field values, are now saved as global settings. This means that any changes made to these fields by a user will automatically apply to all users and all schedules across the system. With this update, users no longer need to configure these settings individually for each schedule, ensuring consistency and reducing repetitive setup efforts.
For operations with a short duration, the operation bar text will now always be visible on the Gantt Chart. If the available space within the operation bar is limited, the text may be truncated to fit appropriately. This shall ensure that users can quickly identify operations improving visibility.
Interoperability capabilities
Http connector management
Users can add and configure Http client connectors using new Interoperability Connector Management page. Http connectors can be used to call REST APIs of any Opcenter X apps or external REST APIs of external systems such as ERP.
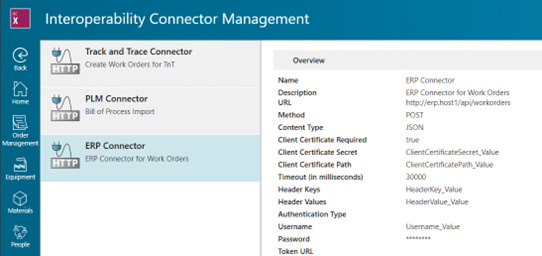
Kafka connector
Supports the publishing and consuming of Kafka messages from an external Kafka Broker.
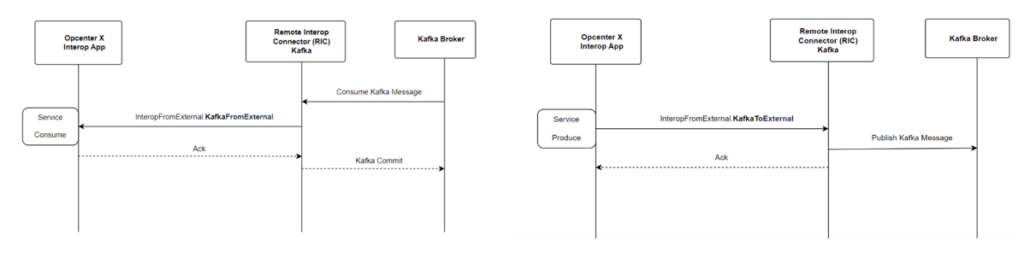
OPC UA connector
- Supports subscription to data changes
- Supports subscription to events
- Supports browsing of OPC UA nodes
- Supports fetching of OPC UA historical data
Improved organization of interoperability model
The integration examples are now organized under examples folder based on the type of connectors Eg. File, OPC UA etc.
Out of the box integrations are organized under the business areas they support. Eg. MES, Quality etc
Improved documentation
There is a dedicated page “How to Troubleshoot Interoperablity”. This is for troubleshooting issues that migth be encountered when building integration using Interop App.
The example integration walkthough has been improved and also includes example of offline/local testing of integrations.
If you are a decision-maker in an SMB in discrete industries and resonate with the challenges discussed, consider exploring Siemens’ new solution Opcenter X. It might just be the catalyst your company needs to leap into the future with confidence.
Try our product through our Trial page, or by requesting a demo.
