The Impetus for Paperless Manufacturing
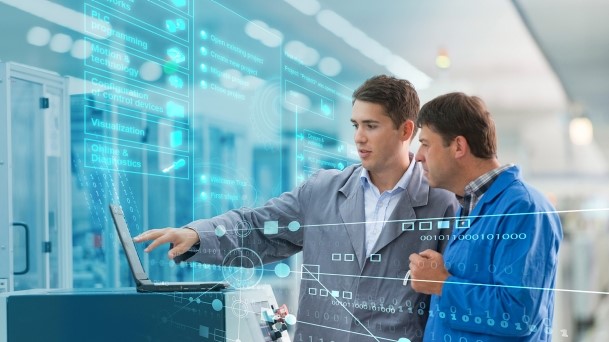
Manufacturers in virtually all industry sectors have been made less efficient by paper-based processes. The problem with paper is manifold:
- From a documentation perspective,the opportunity for errors is a magnitude greater than with automated processes. Studies show that even when paper-based records are executed with accuracy greater than 99.5 percent—not a strong likelihood in the real manufacturing world—documentation errors for a company will still accumulate to tens of thousands. On the other hand, today’s paperless manufacturing systems have zero documentation errors.
- From a quality perspective,manual, paper-based systems cannot adequately prevent errors at each and every step of operations. Consider all the steps involved in manufacturing operations:
- Are the machines qualified?
- Is the procedure correct?
- Have the operators been trained?
- Has all relevant data been collected?
Answering these questions strains the credulity of the effectiveness of paper-based systems. In fact, manufacturers that have relied on paper have had quality issues so problematic that severe regulatory demands have been passed to limit the damaging effects.
- From a cost perspective,paper-based processes add overhead (e.g., materials, labor) and non-value time across operations. With the errors introduced from the reasons above, waste increases, and yields are reduced. All of this results in additional expense.
- From a time perspective, errors and rework increase production time. This latency can slow product development and launch. Being slow to market not only impacts customer experience and expectation, but introduces additional competitive threats by manufacturers who have automated manufacturing operations.
Small wonder, then, that manufacturers are increasingly looking to paperless manufacturing as a strategic imperative. These systems address the above issues by automatically controlling operations across the enterprise. They ensure that operators and machines are right for the application and properly certified, material issue is controlled in real time, all pertinent data is captured in real time, and procedures are enforced at the point of execution. The result is more predictable manufacturing, and that means fewer non-conformance issues, less scrap and rework, and more consistent product quality. It also means, importantly, that brands are less exposed to risk.