Streamlining Processes and Boosting Efficiency: How Applied Composites Transformed Planning and Scheduling with Opcenter APS
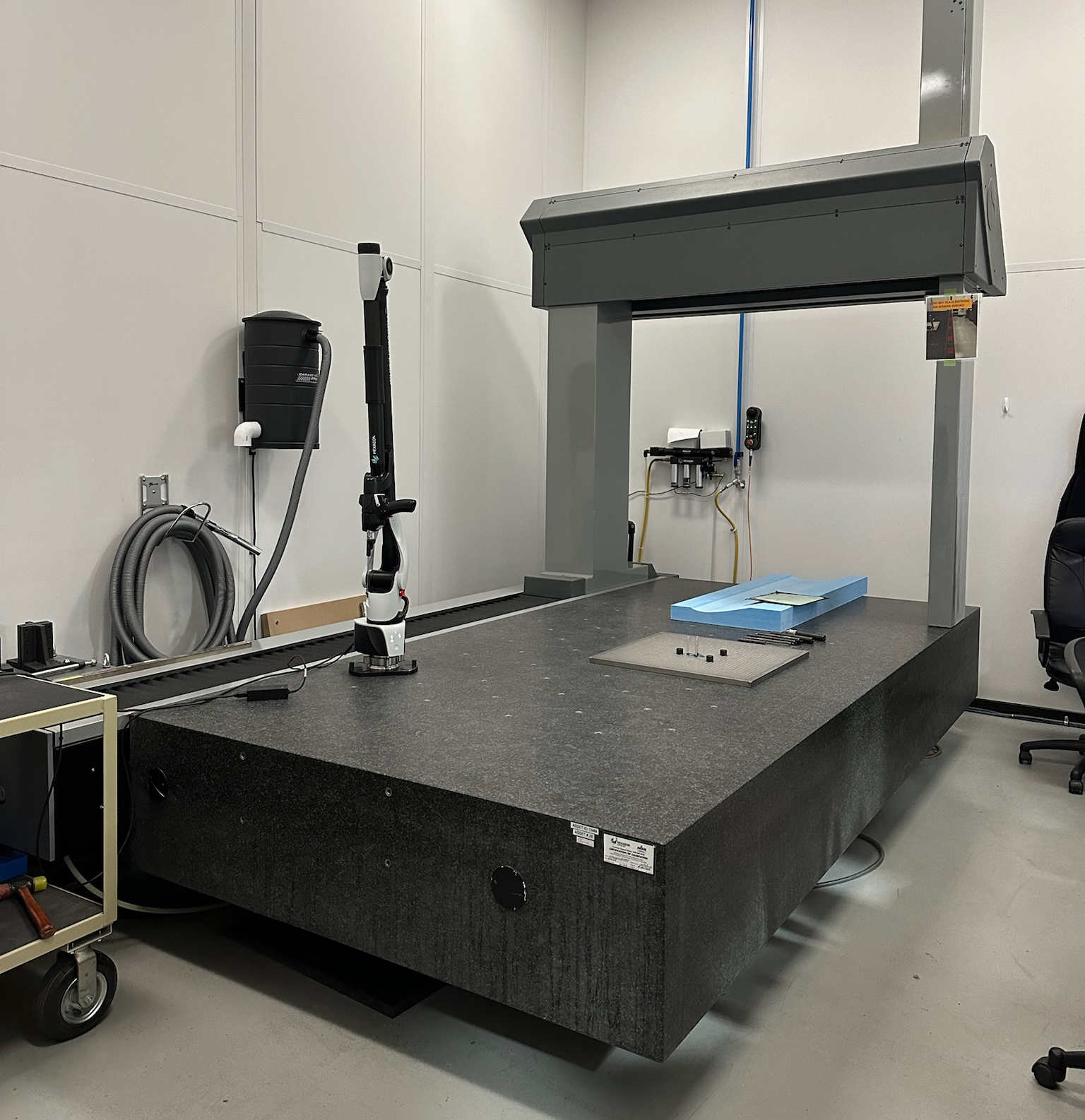
In today’s rapidly evolving aerospace and defense industries, efficient planning and scheduling are crucial for success. Applied Composites, a global leader in the composites industry, faced challenges as their business grew, impacting their overall processes. To overcome these hurdles, they turned to Lean Scheduling International (LSI), a Siemens Digital Industries Software partner, and implemented Opcenter™ APS. Let’s dive into how this software solution helped Applied Composites revolutionize their planning and scheduling operations.
The Challenges of Business Growth
As Applied Composites experienced growth, they encountered difficulties managing planning, scheduling, and overall processes. The expansion of their customer base and the subsequent increase in workload required more employees. Unfortunately, these compounding issues led to a disorganized work environment, causing stress among workers and even missing orders. The company struggled with material management, job scheduling, and ensuring they had enough employees to run available machines.
From Spreadsheets to Opcenter APS
To address these challenges, Applied Composites relied on spreadsheets and enterprise resource planning (ERP) software to create production reports and manage schedules. However, these tools had limitations, including a lack of visibility into material availability and an over-reliance on tribal knowledge from schedulers and shop floor supervisors. Recognizing the need for a more robust solution, Applied Composites collaborated with LSI and implemented Opcenter APS.
Overcoming Limitations and Improving Efficiency
Opcenter APS proved to be the game-changer Applied Composites needed. With the software’s ability to manage complex scheduling requirements and multiple constraints throughout the manufacturing process, the company could overcome their previous limitations.
Configuration and Constraint Consideration
By configuring models that considered all constraints, from materials to tooling and operator capabilities, they could create schedules based on the plant’s true capacity rather than estimates. This allowed for more accurate planning and improved scheduling processes. Previously, creating a schedule involved hours of manual work, leveraging knowledge and data from multiple sources. With Opcenter APS, scheduling decisions became automated, saving time and effort. Scheduling is now a matter of minutes rather than hours.
Enhanced Visibility and Accuracy
Opcenter APS offered Applied Composites newfound visibility into their operations. Workers could easily track the progress of orders in the plant, enabling them to inform customers of actual lead times compared to standard lead times. This increased transparency helped identify potential issues downstream and ensured smoother operations. Moreover, the ability to set accurate material demand dates and schedules was a game-changer for the company.
Conclusion
Thanks to Siemens and Lean Scheduling International, today Applied Composites has reached impressive improvements and achieves on-time delivery on average 96 to 98 percent of the time.
Additional Resources
Read more in the Applied Composites case study