Smart Digital R&D labs to boost innovation for automotive and discrete manufacturers
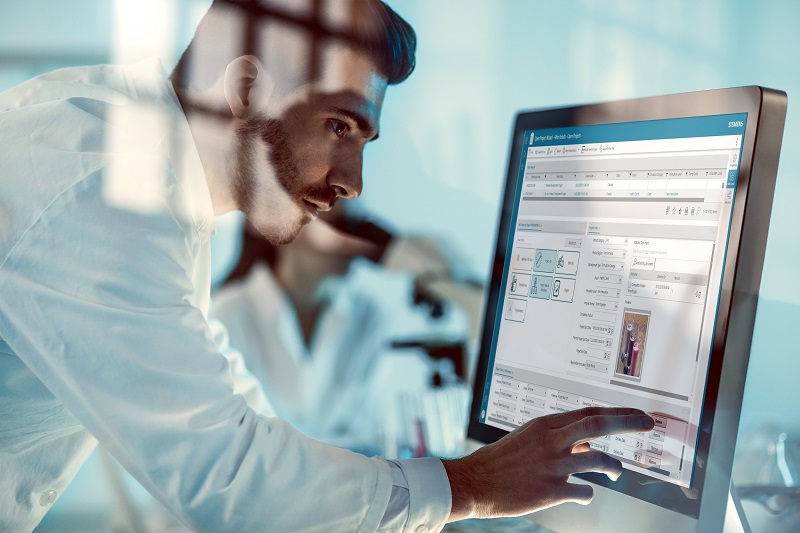
The Chemistry and Advanced Materials industry played a leading role in previous industrial revolutions. It has supported the innovations across industries that have transformed our societies and lives over the past 150 years. Current and next generation products like Electric Vehicles, drones, smart phones and tablets, flexible displays, high-speed internet, efficient integrated circuits etc., all depend heavily on chemistry and advanced materials research and laboratory activities across the supply chain. (Reference: World Economic Forum Digital Transformation Initiative report on Chemistry and Advanced Materials Industry[i])
As a case-in-point, the Automotive industry is going through mega themes of electrification, autonomous driving, connected vehicles and associated infrastructure / eco-system.
But there are underlying R&D efforts that are needed and ongoing for entire vehicle components and the value chain to support these mega themes. R&D efforts are in-way for new materials, chemicals and technologies across mechanical and electrical components that will be environmentally sustainable, efficient for electrification, robust for autonomous driving and secure to meet vehicle connectivity requirements.
As an example, properties of new materials and chemicals that are used to manufacture or treat different components (like seats, transmission modules, paint, window/door seals, braking systems, etc.) must be tested, say for lower noise requirement (due to electrification), durability, climatic conditions, corrosion, weathering, flammability, staining etc. (Reference: Automotive News, Material Science Revolution, How the industry’s researchers are looking for new vehicle ingredients [ii])
With electrification, the battery and fuel cells add their own complexity for R&D processes to achieve sustainable manufacturability and recyclability. R&D efforts require solid methodologies to test materials and properties, cell chemistry across the battery components (such as electrodes) to cell assembly to packing to module assembly and ultimately integrated with other components, like sensors, for optimized performance. There will be varying needs from the development of new materials with different properties and processing needs and requirements in cell manufacturing to battery assembly. When integrated further with other components or vehicle integration, testing requirements vary for the physical behavior of components and material properties in different conditions. Additional consideration should be given to standard testing of batteries for AC/DC voltage, energy storage and retention. All these activities are spread across multiple suppliers and OEMs.
This brings a high degree of complexity in performing pre-production testing and validation of raw materials (at source and on receipt), individual components, integrated in sub-systems and the entire vehicle. Complexity spreads across the entire supply chain where the new product innovations are developed, tested and integrated by different suppliers, groups and departments within an organization. During the R&D lifecycles, these tests are rigorous, and data shared with transparency and actionable insights are critical for shortening innovation cycles in bringing product and required process innovations to life.
Before reaching production readiness, managing test processes in lab environments where 100’s to 1000’s of formulations of materials are integrated with different assembly and sub-assemblies is a challenging endeavor and traditionally achieved in isolation with disparate systems and processes within an organization and across the value chain.
Digitalization of test and verification lab management enables a feedback loop with product engineering, manufacturing and quality engineering, production and end users. Data sharing across the value chain is of paramount importance for continuous improvements and accelerated innovation cycles.
Similar trends and the disconnected nature of the workings of R&D labs is common in Aerospace & Defense, Industrial Machinery and other discrete industries. Aerospace manufacturers have been at forefront in advanced materials research (like composites, heat resistant alloys, non-metal alloys) for several years. Composite core material – fibers, resins, pre-preg (or semi-processed materials), fillers and additives, adhesives etc., all require a mandatory testing at the source and on receipt for physical properties – with data transparency for closed-loop collaboration, but their laboratory processes and systems are traditionally managed in isolation with several ad hoc touch points with rest of processes and systems across the value chain. This is leading to inefficient, digitally disconnected and multitude of non-value add processes, hindering the pace of innovation.
So, how do we achieve digitalization that connects the traditionally disconnected processes and enables a true continuous feedback loop with entire supply chain of R&D laboratories with product lifecycle, manufacturing processes and subsequently, field inputs?
Irrespective of the industry, an integrated laboratory system that is open, flexible and seamlessly integrated into PLM processes and ultimately quality / manufacturing engineering and planning, production processes is the first step for Smart Digital R&D labs. This has been a common practice in process industries (like Food & Beverage, Chemicals etc.), where LIMS (Laboratory Information Management Systems) are tightly integrated into MES (Manufacturing Execution Systems), but for discrete industries this is in isolation and at varied level of maturity. This challenge in automotive and discrete industries is magnified with increasing complexity of supply chain dependencies, regulations and accelerated product innovations.
With an isolated LIMS or legacy systems, a traditional approach hinders the innovation pace that market and consumers are demanding in next generation products. Smart Digital R&D labs not only enable a digital thread of test and verification management, but also enforce data sharing across the value chain for continuous improvements to boost innovations.
Siemens Digital Industries Software is enabling Smart Digital R&D Labs with Opcenter Laboratory and with Xcelerator portfolio, we are supporting our customers today with tools and technologies to empower them for tomorrow.
Look for subsequent blogs in this series, for how Smart Digital R&D Labs support different industry challenges.
[i] http://reports.weforum.org/digital-transformation/wp-content/blogs.dir/94/mp/files/pages/files/170328-dti-chemistry-and-advanced-materials-industry-slideshare.pdf
[ii] https://www.autonews.com/technology/how-industrys-researchers-are-looking-new-vehicle-ingredients