Optimizing Product Quality across the Entire Lifecycle
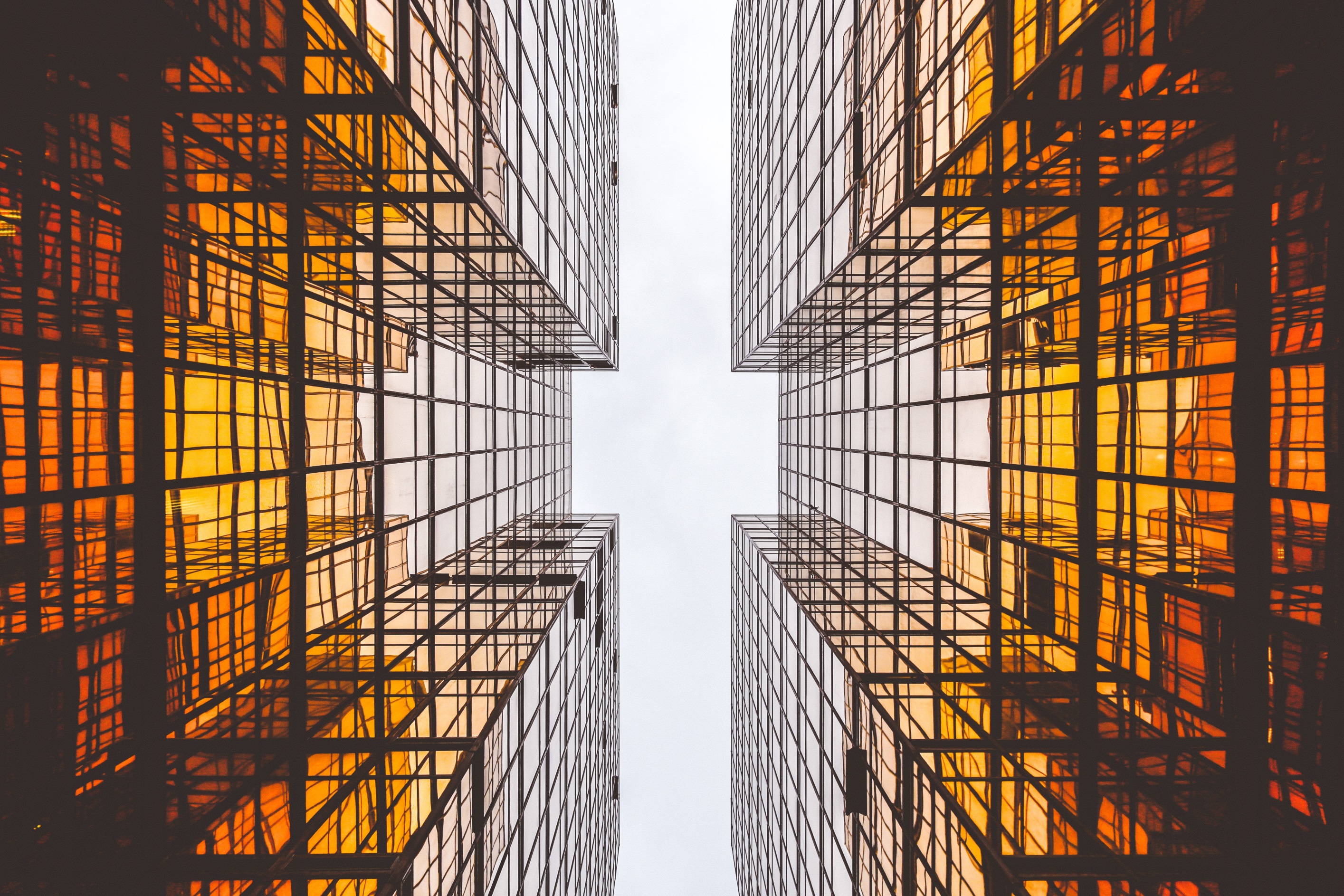
As we move from a regulatory focus on compliance to one of proactively addressing product quality, some manufacturers are already ahead of the curve. They have focused their culture from the top down on quality. With that culture, it is no surprise that their organizations behave differently. And so do the systems they use to support them.
These innovators are among the leaders in the adoption of state-of-the-art technology to enable quality-focused design and production. They are not only satisfying the expectations of their markets, but they are ready for the changing demands of regulatory agencies. These systems are proactively optimizing quality across the entire product lifecycle, not simply documenting the outcomes of particular processes in isolation. We call these “closed-loop quality systems” because they connect quality information from design to manufacturing to market use. Let’s list some examples of what a closed-loop quality system looks like:
-
- A closed-loop quality system provides production, quality and traceability management to optimize the processes involved in your product life cycle.
-
- It creates transparency in production processes, enabling rapid and effective intervention when deviations occur.
-
- It integrates with and compliments the existing enterprise resource planning (ERP) system and product lifecycle management (PLM) system to support risk management, providing immediate access to a company’s production and quality information. It also helps maintain a smooth flow of information and alignment of master data across functions.
-
- It provides real-time traceability to check product history and delivery information.
-
- It controls all corporate administration and production processes, as well those related to compliance, with codes of practice, laws and guidelines.
-
- It supports the phases of continuous improvement, such as the plan-do-check-act (PDCA) cycle, to promote consistent and sustainable improvement.
-
- The full range of quality methods and practices are supported in a unified, coordinated system, such as advanced product quality planning (APQP), control plans, audit management, failure modes and effects analysis (FMEA), inspection plan management (IPM), concern and complaint management (CCM), statistical process control (SPC) in-process inspection, warranty management, traceability management, incoming goods/outgoing goods inspection, and integrated workflow management.
-
- It facilitates Lean processes and waste reduction, reducing not only defects and quality costs, but also reducing process times
Today’s closed-loop quality systems are way beyond tools to achieve compliance. They are an integral part of improving product quality in a proactive way, coordinating all the moving parts related to a comprehensive quality program. And properly used in conjunction with ERP, PLM, and Manufacturing Operations Management (MOM), they improve quality not only of current products, but provide feedback into the next product lifecycle. And in the process, they create more efficient, profitable manufacturing enterprises.
Find out more about the leading closed-loop quality management system, the IBS QMS solutions from Siemens PLM Software. Download the brochure today.