Advanced planning and scheduling (APS) and enterprise resource planning (ERP) complement each other
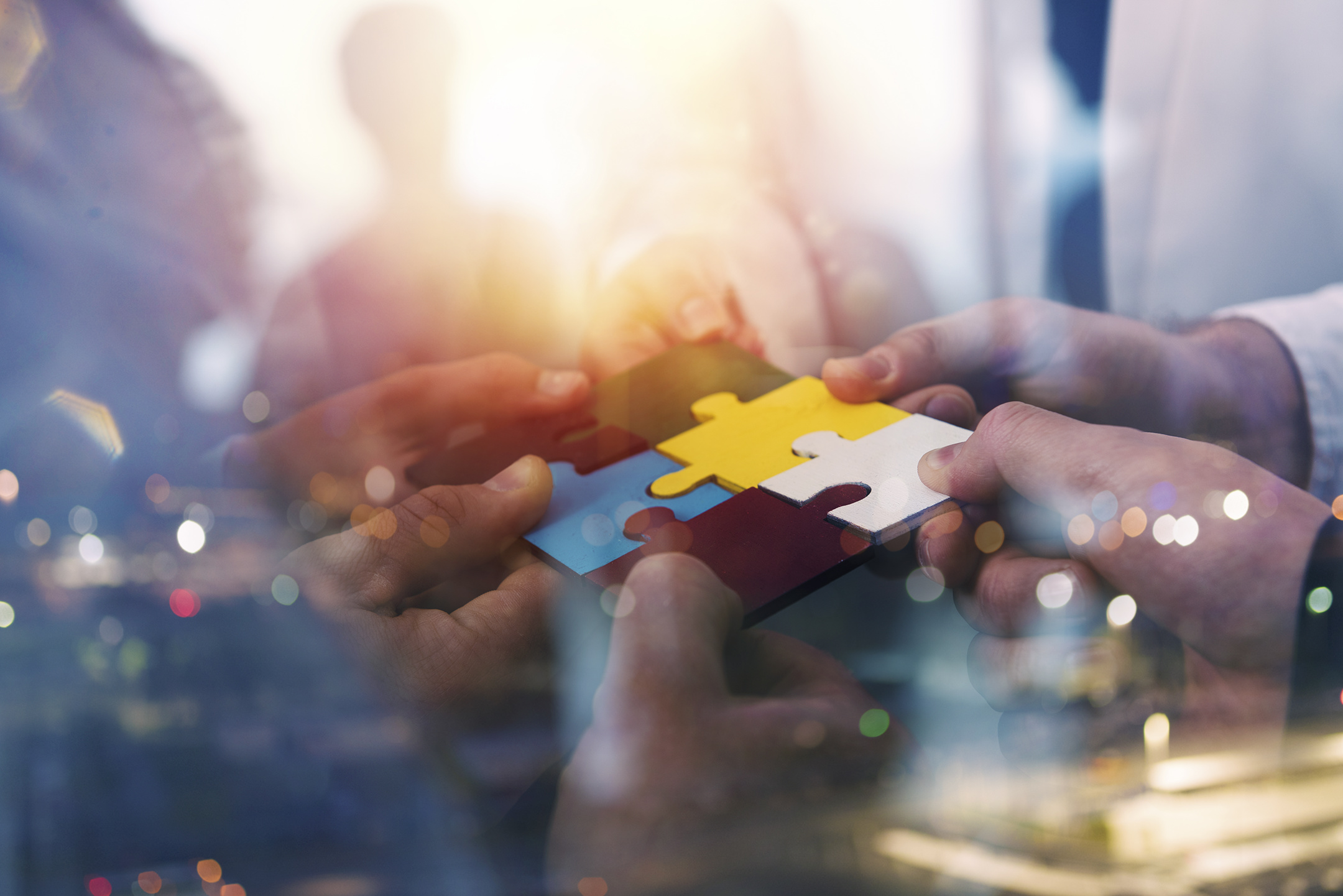
How is advanced planning and scheduling (APS) different from the planning and scheduling my company performs on our enterprise resource planning (ERP) system? Do we really need both systems? These are common questions among decision makers at manufacturing companies as they explore the ways in which digital tools could increase their efficiency and productivity – and therefore, their bottom line. A quick answer to the first question is that APS and ERP systems differ in terms of their functional purpose and points of focus, as well as the context in which their data is used.
To the second question, we say yes! APS and ERP systems are both needed if your company is to make the greatest gains possible from excellent production planning and production scheduling. Although some manufacturers make do with either ERP or APS for this functionality, it turns out that using the two systems in a complementary way makes each of them that much more valuable a resource.
Advanced planning and scheduling is a pillar of a comprehensive manufacturing operations management (MOM) system, and MOM and ERP systems represent two of the three key functional hubs within a manufacturing company’s data infrastructure (the third being product lifecycle management (PLM), which focuses on product creation and engineering data). Let’s explore the differences between ERP and APS systems, then outline how the two systems work together to bring the greatest benefit to your manufacturing floor.
Key differences in ERP and APS functionality
Generally, an enterprise resource planning system is the place in your digital ecosystem where business strategy and operations converge. MOM software, including APS, serves as the data infrastructure “bridge” between enterprise-level ERP information and the automation and control systems on the factory floor.
As a business-oriented system, ERP software manages most aspects of the business, integrating operations ranging from human resources to finances to purchasing and inventory. Planning and scheduling tasks in ERP are capacity-based and account for constraints only on a limited basis. Information generated by ERP software related to planning and scheduling includes:
- Production demand
- Master schedules
- Bills of materials (BOMs)
- Change orders
- Inventories
- Planned resources
Because its purpose is more closely related to production, advanced planning and scheduling software applies more directly to a company’s specific manufacturing operations. APS software uses advanced algorithms to ensure that the schedule is workable; that is, it effectively balances supply, demand and manufacturing capacity and accounts for constraints. The software is designed to dynamically update and recalculate scheduling variables as conditions change, such as a new order coming in or a production machine malfunctioning. APS also optimizes the schedule (and re-optimizes as conditions change). Optimization may be based on a selected strategic criterion: machine utilization, for example, or changeovers. The software is designed to improve productivity by:
- Minimizing inventory
- Removing production bottlenecks
- Reducing setup and changeover time
- Improving on-time delivery
One way to summarize the differences between APS and ERP is that ERP focuses on the business of manufacturing while APS focuses on the optimization of manufacturing operations.
APS and ERP complementary functionality
You may have noticed that the informationthat an ERP system generates is the data that is needed as input for the APS system to perform its optimization functions. This is the first aspect of the relationship between the two systems: ERP data feeds downstream to APS. The APS software receives and regroups this information to focus on manufacturing decisions such as rapid actions, detailed planning, forecasting, metric analysis, and ongoing adjustments.
The second aspect of the ERP and APS relationship flows in the opposite direction: data from the APS systems feeds upstream to the ERP system, where it serves as input to the many business operations (for example, human resources or finances) that the ERP manages.
This then is the complementary nature of APS and ERP systems: the enterprise resource planning system interacts with departments and systems across the enterprise, collecting data and providing it to other systems to use for their functional responsibilities. As one of those recipient systems, the advanced planning and scheduling system uses ERP data to perform capacity planning, materials requirement planning, and production scheduling. Data from APS is then collected by the ERP and distributed to systems across the enterprise that need this data for their functions.
Opcenter Advanced Planning and Scheduling
Siemens has designed our Opcenter Advanced Planning and Scheduling system to interact effectively and efficiently with ERP systems to maximize production efficiencies and minimize time to delivery. Capabilities of our APS software that help optimize planning and scheduling include:
- Rapid generation of achievable, efficient plans and schedules
- Close coordination of the entire supply chain to ensure production steps are executed on schedule
- Optimization tools that can prioritize a variety of criteria (for example, on-time delivery, machine utilization, or changeover frequency)
- Automated assessment of the impact of changes in quantity or delivery date
- Agile reoptimization in response to changing real-world conditions
Siemens customers that have implemented Opcenter Advanced Planning and Scheduling software have achieved significant reductions in inventory levels and waste while improving resource utilization and on-time delivery. We encourage you to explore Opcenter APS today