Ensuring Global Quality through Collaboration: 3 Areas to Watch
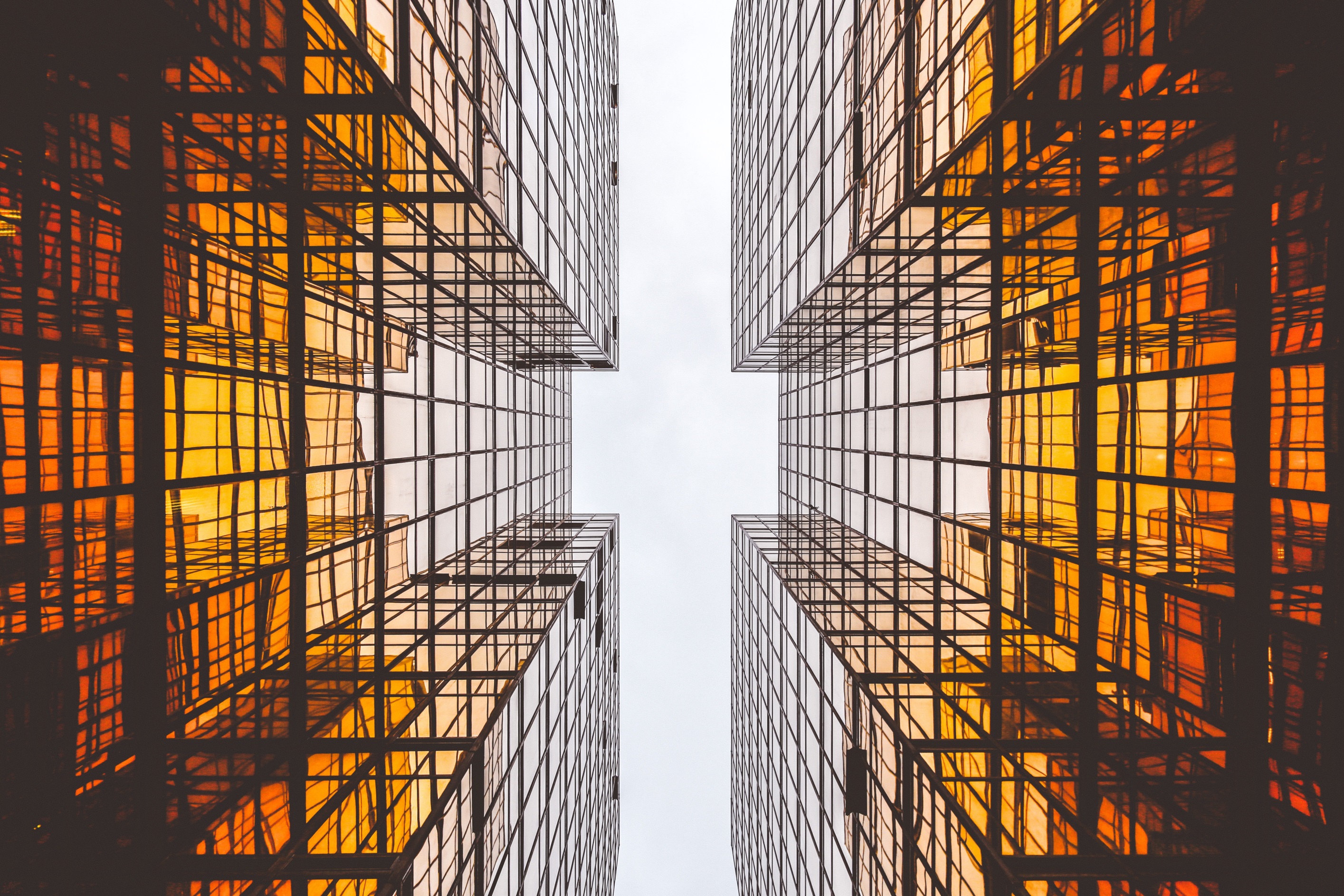
Today’s nuanced and networked manufacturing world spans the globe, yet wherever goods are produced and consumed, quality is an unforgiving expectation. Customers expect quality regardless of where a product has been manufactured and who has been involved, so brand owners need to ensure that quality expectations are being met and monitored by everyone in their supply chain, as well as everyone in their supply chain’s supply chain. The magnitude of this task has kept many an executive up at night. Quality failures all too often become a lead story in the business and consumer press.
Collaboration is at the core of global business. It makes sense to pay close attention to that process in relation to quality. Here are three areas that companies can focus on to help assure that global quality won’t become an issue in your morning news:
-
- Business relationships. Risk and compliance need to be managed across extended business relationships, yet often those relationships face close scrutiny only at their inception. Bad idea. Risk should be assessed over the life of a business relationship, so be sure that processes are in place to maintain an ongoing assessment of it. These risks will vary depending on the partner (e.g., geo-political and environmental factors can impact a partner depending on their place of business), and they should be considered accordingly. They also need the ongoing assessment of legal and regulatory issues in different markets, not just the market where you are based. Importantly, resolve issues as quickly as possible when they arise; all relationships will have difficulties to address from time to time. If they fester, they’ll become more problematic.
-
- Standards and testing organizations. Early engagement with testing and certification organizations is like a dose of preventative medicine: it helps avoid quality issues by ensuring that manufactured products meet international and domestic standards, as well as those that exist between specific trading partner nations. One consideration here: the earlier the involvement, the better. Think of collaborating with these groups in the design phase. One more: engage with standards and testing organizations based in the country or region where you are manufacturing.
-
- Technology. Strongly consider employing technologies that close the quality loop across all manufacturing facilities in your network. Quality Management Systems (QMS) can identify potential problems before they occur when integrated effectively as part of a closed-loop quality process proactively monitoring events across any enterprise source. Enterprise sources include supplier issues, manufacturing nonconformance, complaints, services, and audits—both locally and globally. Linking QMS with Manufacturing Execution Systems (MES) is a powerful strategy. Quality management systems that directly collaborate with MES and Manufacturing Intelligence ensure compliance with corporate and industry regulations, and enable quality programs such as lean and six sigma with the goal of continuously improving product quality and preventing adverse events. These applications that unify manufacturing, quality, and intelligence capabilities deliver a closed-loop approach to improving product and process quality.
The biggest message: use collaboration to prevent quality issues before they happen. This will save you a lot of sleepless nights.