Data integration to connect IT with OT is key to scale digitalization
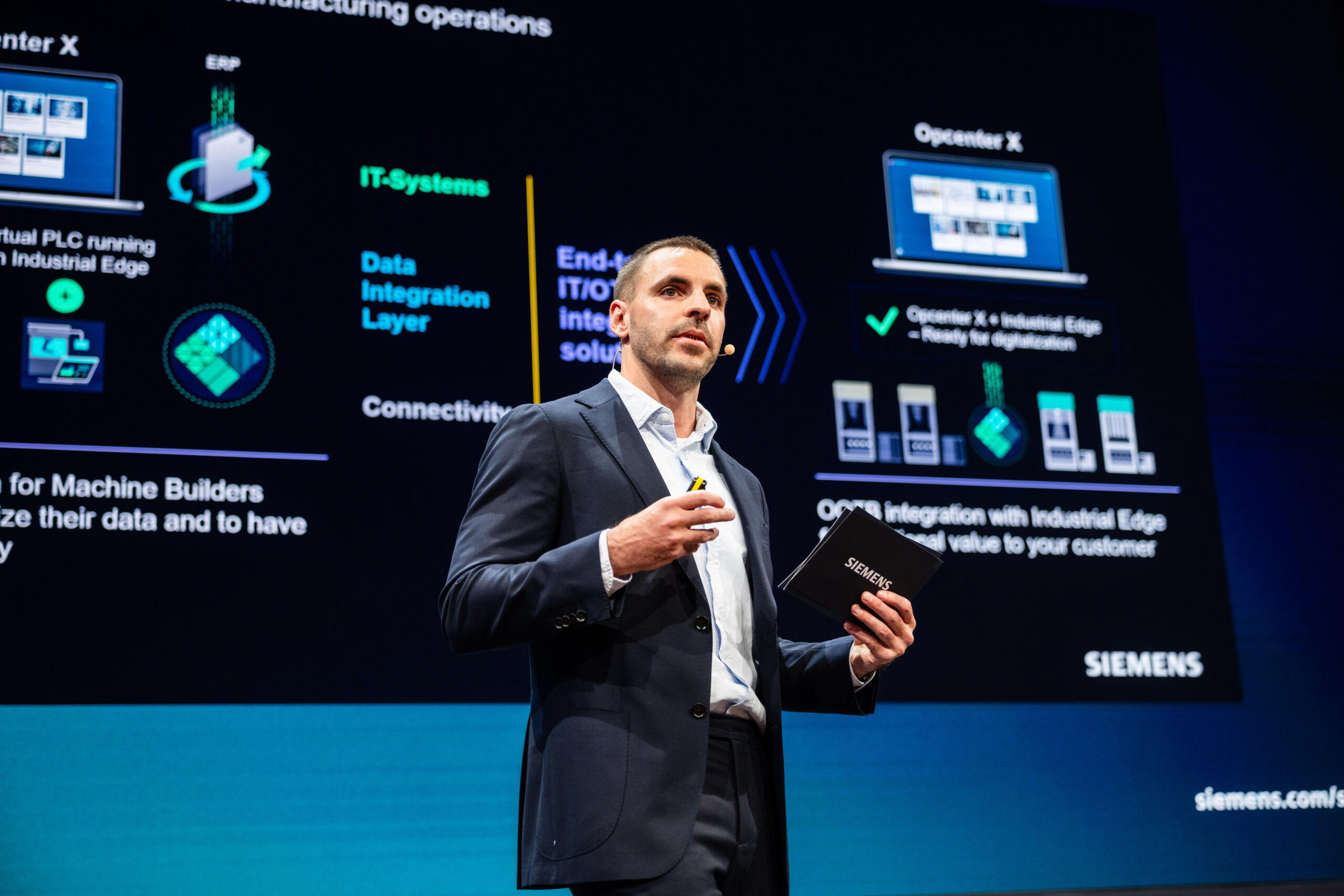
Improving data integration from both IT and OT sources is a significant challenge for companies, system integrators, and machine builders. In this presentation, we will explore the implementation of data integration and discuss the potential technologies that can meet the requirements for successful digitalization. We will showcase a practical use case using Industrial Edge and the MES system Opcenter X.
Unfortunately, 67% of people have incomplete IT-OT integration projects, and only 70% of all projects actually achieve their goal of enhancing production and driving improvement. This is a considerable problem. Why does this happen? It is because the challenge of integration lies in working together closely and having a comprehensive portfolio and common strategy in place.
One of the challenges we face is optimizing operations. How do we improve our production processes? Another important aspect is competitiveness and sustainability. To achieve these goals, it is crucial for people to collaborate and embrace digitalization, making our products more efficient and environmentally friendly.
This collaboration involves both people and technology, with data playing a central role. Without access to data, it is impossible to make meaningful improvements. For example, without data, we cannot identify areas where we are producing excessive carbon emissions. This integration effort involves engaging employees, technicians, and technology users.
So, what do we offer as a solution? Connectivity is at the heart of our offering. We provide the means for seamless data exchange and communication.
To acquire the necessary data, connectivity to IoT systems and other relevant sources is essential. This connectivity forms the foundation of the data integration layer, which serves as the tool to bring together OT, data, and IoT systems. Siemens offers a comprehensive portfolio that includes the data integration layer, facilitating seamless connections between products and systems, including cloud-based instances.
However, a crucial question arises: how do we transform this data into meaningful information? Often, there is a lack of context between operations and the data generated by machines. This lack of understanding can lead to ineffective planning and execution, resulting in potential delays and compromised product quality.
Merely collecting machine data is not sufficient; it is equally important to contextualize it. Without a direct connection to manufacturing operations, achieving optimal performance on the shop floor becomes challenging.
Today, we are excited to introduce Opcenter X, a cutting-edge MES system that operates entirely in the cloud. Launched in April of this year, Opcenter X is a software-as-a-service (SaaS) solution, meaning you don’t have to worry about managing operations – we take care of that for you. By integrating Opcenter X with Industrial Edge, we can achieve real-time visibility, enabling quick decision-making and production optimization.
Opcenter X is a truly modular system, offering a range of modules that not only ensure smooth operation but also continuously improve production processes. Our cloud-based Opcenter X MES system encompasses typical MES functions, as well as quality execution and advanced planning and scheduling capabilities.
This comprehensive software-as-a-service solution leverages the Industrial Edge technology to seamlessly integrate IT and OT systems. It addresses the complexities that arise from the three layers of connectivity, data integration, and IT systems. With Opcenter X, you can achieve a seamless and efficient IT-OT integration.
This game-changing integration not only benefits machine builders but also their customers and manufacturing companies. By leveraging this out-of-the-box integration, they can benefit from pre-designed the end-to-end visibility and its important data contextualization. This eliminates the need for expensive service implementation, as the data from the machines can be directly contextualized.
To summarize the advanced technology of Opcenter X and its value in production facilities: Opcenter X is designed to simplify, optimize, and enhance manufacturing processes with a modular and cloud-based solution. It offers secure access from any location while upholding the highest security standards. By trusting Siemens with software operations, updates, and maintenance, you can focus on your business and innovation. All operations are handled by us, making the software user-friendly and easy to use.
We can quickly deploy it because it is a cloud-based solution, which significantly reduces implementation time due to its modular nature. You can begin with a small scale and expand as you progress on your journey. Opcenter X is not just a tool for streamlining and managing your production, but also a partner that can evolve alongside you during your digital transformation journey.
Ready to take your manufacturing operations to the next level? Learn more about Opcenter X and how it can transform your business by contacting Siemens today.
Try our product through our Trial page, or by requesting a demo.