5 key things you should consider when looking for a Product Data Management Solution
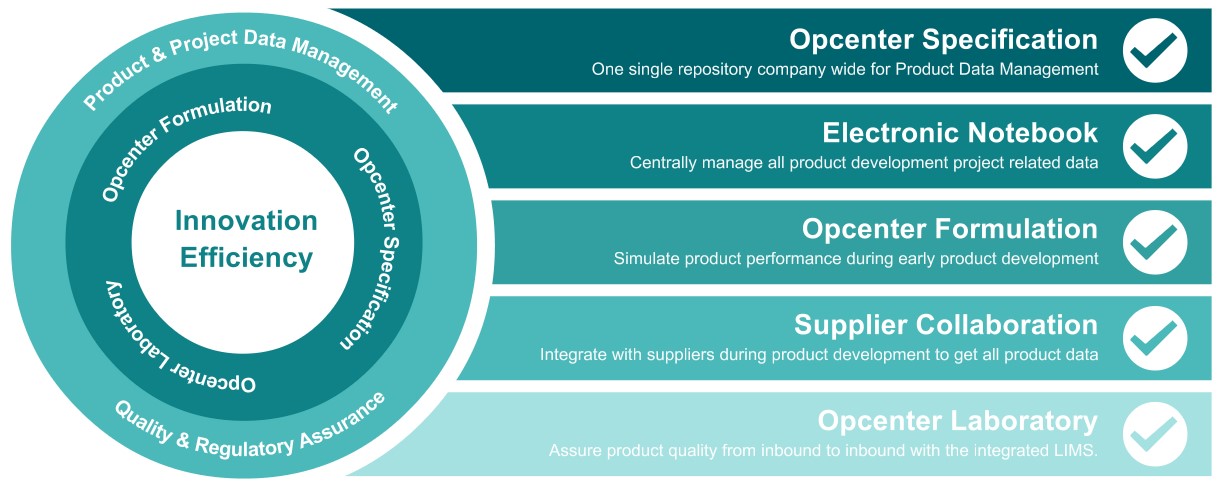
The drive for growth and increasing global competitive pressure are pushing companies throughout the process industry to put a strategic focus on continuous product innovation. These challenges have promoted the industrial Research and Development function to the center stage and leading edge, where it is fast becoming a key driver of a company’s commercial success.
As consumer demands are becoming more varied with product life-cycles getting shorter and regulatory compliance challenges growing in complexity, there is a tremendous pressure on processes and system infrastructures. In such complex world, mistakes are being made resulting in too many new product introduction failures, missed markets and unrealized growth opportunities.
As such, more and more business executives realize that there’s a pressing need to streamline their R&D processes, and look for a platform that allows an easy and consistent transfer of the final product designs to the affected manufacturing plants around the globe. Integration of R&D and Manufacturing is becoming a basic business requirement. Today, successful companies combine timely and insightful product innovation with a fast, global time-to-production and hence time-to-market.
A Product Data Management solution is a crucial component of the solution. Here are the 5 key things you should consider before making your final choice:
- Can I have an Integrated platform reaching beyond PDM?
- How will my PDM solution support me during my innovation process?
- How do I assure premium product quality from idea to shelf?
- Does the solution offer a full audit trail for traceability purposes – making it fully GMP compliant
- And last, but not least, is the solution easy to configure with little to no customization?
Why an Integrated Platform?
Product development and innovation within the CPG industries have many different facets, each with its own challenges to optimize and improve the overall process. It’s not only about a formula with different components that need to be combined in certain quantities. It’s also about primary packaging, a label, label artwork, ingredient declarations on a label, secondary packaging. Every single item like a formula, ingredient, label or artwork element are part of an overall larger process. As a company you would like this process to run as fast and efficient as possible.
Also, on top of that product development complexity, most goods and a growing share of services are ‘made in the world’, and not just produced in just one country. This adds complexity in terms of keeping everything aligned and synchronized.
Keeping all these aspects aligned and working together requires a solid integrated software platform across all elements to keep the product specifications up to date and assure product quality from inbound to outbound.
How it will support you during your innovation process?
An integrated platform allows you to improve the time to market by having all needed information in one central repository. That way, during product development through the Electronic Notebook, all product specifications are available during formula development. The formula workbench allows to create a digital twin of the product and simulate in a digital environment the impact on product performance of certain formula changes, on ingredient declarations, on claims, etc. It also allows you to evaluate, in real time, how a new formula complies with set targets. That way a company can quickly decide to proceed on real life trials with only a limited number of targeted formulas.
Embedding a LIMS component assures premium product quality from idea to shelf
Having a LIMS component not only allows you to organize the work in the lab in an efficient way, it also assures premium product quality.
The LIMS component supports the new product development process with different analysis on trials and assures the quality in production through at line and offline testing. That way the LIMS component can close the quality loop from idea to shelf during product development and from inbound to outbound once a new product goes in production. Raw materials can be analyzed upon delivery to assure that only good quality comes into the plant. Semi-finished & finished goods are analyzed to assure product quality throughout the production process and make sure that only good quality products are being shipped to the customer.
The LIMS component should have all functionalities needed to make that possible:
– A Lab Execution System (LES) to guide lab operators through the different steps of the standard operating procedure.
– A connection with instruments to register analysis results directly in the LIMS to avoid any typing errors. The Equipment Management functionality assures instruments are calibrated in time by scheduling service intervals and registering all interventions done.
– Have SQC rules embedded to pro-actively alert when analysis results start deviating. That way corrective action can be taken in time to avoid scrap or rework being produced
– Finally, monitor operator qualifications to assure that only skilled operators perform the required analysis and to have follow up trainings scheduled in time.
Offering a full audit trail and being fully GMP compliant
You need to ensure the solution has an audit trail registered to assure full traceability on all actions performed in the system. Changing statuses on a lifecycle will not only register the action, but also require a reason code to be entered. That way, the solution fully complies with all demands for Electronic Registration and Electronic Signature. Finally, access in the system can also be configured based upon Data Access Rights and Functional Access Rights linked to User Profiles.
Easy to configure with little to no customization
With an attractive look and feel, the user interface should be familiar and easy to work with for all users. Developed to also work on mobile devices, it provides support for multi touch and gestures – further extending the flexibility of the system. Because the solution is web services based and able to run on different web browsers, it is easy to maintain and access.
In brief, having One integrated platform for Specification Management, Formula Development, LIMS, Electronic Notebook and Supplier Collaboration:
- allows users to have all information on hand to accelerate the time to market for new product developments
- assures premium quality from idea to shelf, from inbound to outbound.
- is easy configurable and user friendly
- and provides an extended audit trail making it fully GMP compliant.
Siemens Opcenter RD&L solution is truly a best in class Data Management System for Formulated Products.
To realize innovation efficiency, Opcenter RD&L is a modular, integrated platform consisting of multiple components:
- Opcenter Specification, the core of the product data management offering a single repository company wide
- Opcenter Formulation where the digital twin of the formulated product comes to life and multiple simulations on different aspects can be run before taking a formula to real life trials
- Opcenter Laboratory, a full Laboratory Information Management System (LIMS) that allows you to closely link the quality parameters from the specification management system and realize the efficiency in the laboratory to support product development as well as at line and off line testing on the production floor.
Opcenter RD&L offers two additional components to further streamline organization and realize efficiency:
- With the Electronic Notebook all project related data can be stored in one central location with project plan milestones and tasks assigned to different people in the organization. Integrating this notebook within Opcenter RD&L allows you to use product data from the specification management component in a project, simulate formulations in the formula workbench, and launch real life trials with quality analysis in the LIMS – all linked to each other in the project hierarchy within the notebook.
- The External User portal enables the suppliers to be involved in the product data management. They can be requested to fill out the specifications of the materials they are supplying directly in Opcenter RD&L. This way, the customer can be certain that all needed product information is available in the system from the first time and they can avoid retyping information in their system. Also, wit the External user Portal, LIMS customers for service lab could enter the system to retrieve their analysis data and certificates of analysis directly from the system themselves.
To learn more about Opcenter RD&L, please visit our dedicated hub.
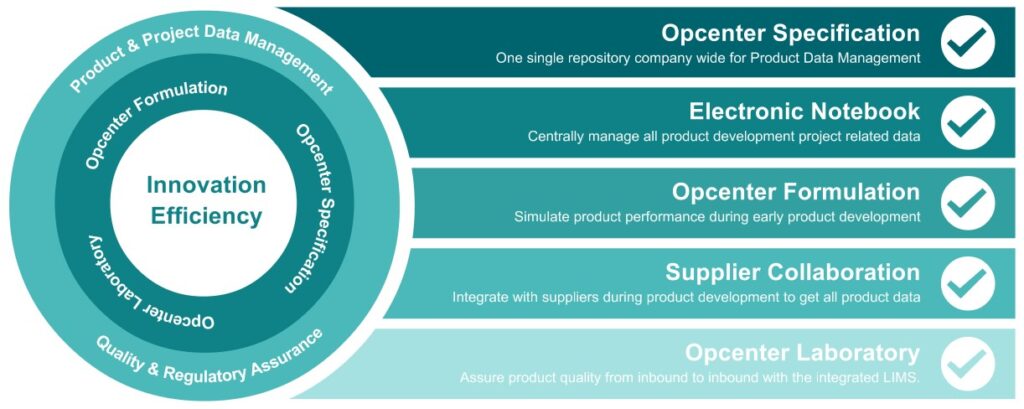