Top 5 advanced CAM software capabilities every CNC programmer should know
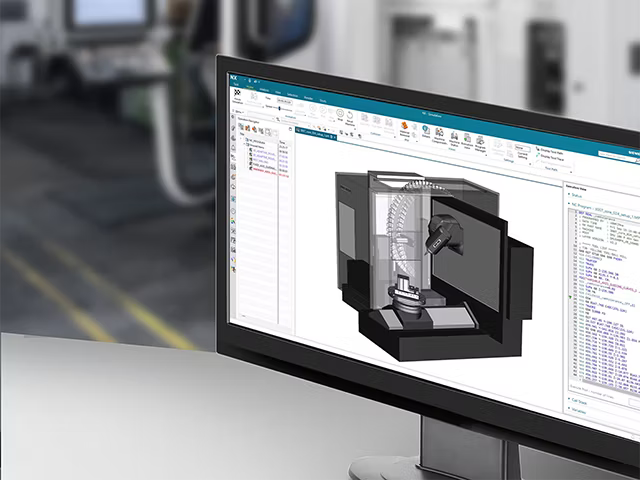
As a CNC programmer, you’re always looking for ways to work smarter, not harder. Yet, as machining becomes more complex, so do the challenges—optimizing toolpaths for efficiency, ensuring seamless post-processing across different machines, and programming complex geometries with precision. These obstacles can slow you down, increase the risk of errors, and impact overall productivity.
Advanced Computer-Aided Manufacturing (CAM) software can be a powerful ally in this pursuit, offering a range of capabilities that can dramatically improve your efficiency, precision, and productivity.
In this article, we’ll highlight the top five advanced CAM software features that every CNC programmer should know and utilize.
Top 5 advanced CAM software capabilities
1.) Multi-axis machining
One of the most significant advantages of modern CAM software is its ability to handle complex multi-axis machining. Your CAM software should be able to perform multi-axis machining to keep up with intricate part requirements and improve shop efficiency. While 3-axis machining is sufficient for many parts, 5-axis and beyond can offer significant benefits:
- Reduced setups: Multi-axis machines can often complete a part in a single setup, reducing handling time and potential errors from re-fixturing.
- Improved tool access: The additional rotary axes allow the tool to reach more part surfaces, enabling more complex geometries and reducing the need for specialized tooling.
- Superior surface finish: Multi-axis machining can provide a more consistent surface finish by maintaining optimal tool orientation relative to the part surface.
Advanced CAM software like Siemens NX CAM offers powerful multi-axis programming capabilities. NX CAM includes a range of 5-axis machining strategies, from simple swarf cutting to complex contour-following and geodesic machining. These strategies are supported by intelligent collision avoidance and machine simulation, ensuring safe and efficient multi-axis programs.
2.) Automated toolpath generation
Another key capability of advanced CAM is automated toolpath generation. Rather than manually creating every toolpath, CAM software can intelligently analyze part geometry and automatically generate efficient toolpaths.
Some examples of automated toolpath generation include:
- Feature-based machining: CAM software can recognize common part features like holes, pockets, and bosses, and automatically apply optimized machining strategies.
- Adaptive clearing: This technique automatically adjusts toolpaths to maintain a constant chip load, minimizing tool wear and maximizing material removal rates.
- High-speed machining: Advanced algorithms can create smooth, flowing toolpaths that take advantage of high-speed machine capabilities while maintaining tight tolerances.
Automating toolpath creation reduces programming time, improves tool life, and ensures consistent, high-quality results—helping CAM programmers and machinists work more efficiently.
3.) Integrated simulation
A critical aspect of any CNC program is ensuring that it will run safely and correctly on the target machine. Your CAM software should generate validated, production-ready programs to prevent costly errors and machine downtime.
Integrated simulation in CAM software plays a key role in validating CNC programs before machining. It helps part manufacturers detect errors, optimize toolpaths, and prevent collisions or part defects, ensuring smooth, efficient machining operations with confidence.
Advanced CAM software includes powerful simulation capabilities that allow programmers to virtually prove their programs before running them on real machines.
Some key simulation capabilities to look for include:
- Machine simulation: This shows how the actual machine components will move through space, detecting potential collisions between the tool, holder, and machine elements.
- Material removal verification: By simulating the actual cutting process, CAM software can verify that the program will produce the desired part geometry, catching any gouges or undercuts.
- G-code simulation: Advanced CAM systems can simulate the actual G-code that will run on the machine, providing the most accurate representation of the final program.
Explore Siemens NX CAM’s machining simulation to validate toolpaths at multiple levels and generate accurate, production-ready CNC programs.
4.) Postprocessing
To turn a CAM program into a machine-ready G-code, it must go through postprocessing. Every machine and control combination has its own unique G-code dialect, and the postprocessor is responsible for translating the CAM toolpaths into this specific format.
Advanced CAM software offers flexible and configurable postprocessing to handle a wide variety of machine and control types. Some key postprocessing capabilities include:
- Customizable output: Advanced postprocessors allow users to fine-tune the G-code output to match their specific machine requirements, such as preferred line numbers, comments, and safety blocks.
- Control-specific optimization: Postprocessors can take advantage of control-specific features and cycles to optimize the G-code program for faster and more efficient execution.
- Machine simulation integration: By linking the postprocessor with machine simulation, CAM software can provide G-code-level verification, ensuring that the post-processed output will run correctly on the target machine.
Siemens NX CAM offers a robust postprocessing environment with over 2,000 pre-configured postprocessors via Post Hub, a modern cloud-based platform for managing Digital Twins of machine tools. Its extensive library supports milling, turning, and multi-function machines from DMG MORI, Haas, Makino, Mazak, and Okuma. With Post Hub, users can easily access and deploy tailored postprocessors, streamlining the transition from CAM programming to real-world machining.
5.) CAD/CAM integration
Finally, one of the most powerful capabilities of advanced CAM software is its ability to integrate seamlessly with CAD software. By working directly with the native CAD model, CAM software can streamline the programming process and ensure that the machined part exactly matches the design intent.
Some key benefits of CAD/CAM integration include:
- Associativity: Changes made to the CAD model are automatically reflected in the CAM program, keeping the design and manufacturing data in sync.
- Feature recognition: CAM software can directly access CAD features and attributes, such as holes, pockets, and tolerances, to drive automated programming.
- Design for manufacturability: Integrated CAD/CAM allows for seamless communication between design and manufacturing teams, facilitating design optimization for more efficient production.
Siemens NX offers industry-leading CAD/CAM integration. NX CAM works directly with NX CAD models, as well as data from other major CAD systems. This integration allows for a seamless flow of information from design to manufacturing, reducing errors and accelerating the overall production process.
Unlock the power of advanced CAM software with Siemens NX CAM
As a CNC programmer, mastering these advanced CAM capabilities can help you take your skills and your shop’s productivity to the next level. Siemens NX CAM offers a comprehensive set of tools for multi-axis machining, automated programming, simulation, postprocessing, and CAD/CAM integration.
To learn more about NX CAM and its advanced capabilities, visit Siemens NX CAM. There you’ll find detailed information on NX CAM’s features and benefits, as well as case studies and testimonials from real-world users.
For a broader view of Siemens’ manufacturing solutions, check out the Siemens part manufacturing solution. Here you’ll see how NX CAM fits into a comprehensive digital manufacturing ecosystem, from CAD design to CNC machining to production planning and execution.
If you’re looking to dive even deeper into the world of advanced CAM and CNC automation, be sure to download our Ultimate Guide to Manufacturing with NX CAM. This comprehensive resource covers everything from CAD integration to machine simulation to postprocessing, providing valuable insights and best practices for maximizing your NX CAM investment.
Whether you’re a seasoned CNC veteran or just starting your programming journey, investing in advanced CAM software like Siemens NX can pay significant dividends. By leveraging these powerful capabilities and learning from resources like our Ultimate Guide, you can boost your efficiency, reduce errors, and deliver higher-quality parts faster than ever before. Start exploring the possibilities of advanced CAM today and take your CNC programming to new heights.
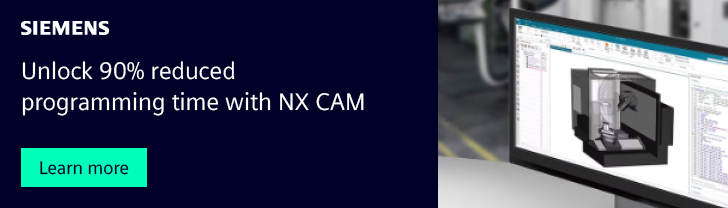
Frequently Asked Questions (FAQs)
Q. What is the best CAM software for CNC programming?
A: The best CAM software depends on your machining needs. Siemens NX CAM is a top choice for advanced CNC programming, offering powerful features like multi-axis machining, automated toolpath generation, real-time simulation, and seamless CAD/CAM integration.
Q. How does multi-axis machining improve CNC programming?
A: Multi-axis machining allows for greater tool movement and positioning, reducing setup times, improving surface finishes, and enabling complex part geometries. Advanced CAM software like Siemens NX CAM provides strategies for 5-axis and beyond, ensuring optimal toolpaths and collision avoidance.
Q. What are the benefits of automated toolpath generation in CAM software?
A: Automated toolpath generation saves time, reduces errors, and optimizes machining efficiency. Features like feature-based machining, adaptive clearing, and high-speed machining help CNC programmers streamline workflows while maintaining precision.
Q: Why is simulation important in CAM software?
A: Simulation helps verify toolpaths, detect potential collisions, and optimize machining strategies before running programs on a CNC machine. Siemens NX CAM offers machine simulation, material removal verification, and G-code simulation to prevent costly mistakes.
Q: How does CAD/CAM integration enhance manufacturing efficiency?
A: A fully integrated CAD/CAM system ensures design associativity, meaning any changes in the CAD model automatically update in the CAM environment. This reduces errors, speeds up programming, and improves collaboration between design and manufacturing teams.
Q: What industries benefit from Siemens NX CAM software?
A: Siemens NX CAM is widely used in aerospace, automotive, medical device manufacturing, and precision engineering due to its advanced machining capabilities and seamless CAD/CAM workflow.
Q: How can I learn more about Siemens NX CAM?
A: You can explore Siemens NX CAM’s full capabilities by visiting Siemens NX CAM or downloading our Ultimate Guide to Manufacturing with NX CAM for in-depth insights on advanced CNC programming.