Siemens continues driving toward our vision to industrialize additive manufacturing
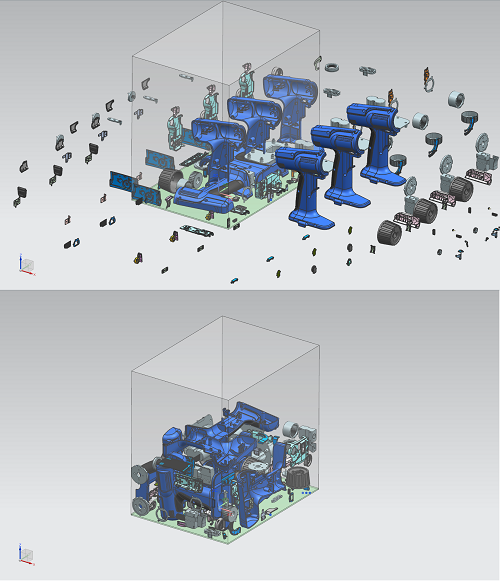
Today marks another major milestone in Siemens’ vision to industrialize additive manufacturing (AM).Siemens PLM publicly announced that we’re advancing 3D printing for industrial production with the creation of an HP-certified AM software module, Siemens NX AM for HP Multi Jet Fusion, available as part of the Siemens’ end-to-end design to production AM solution. The new module allows for the development and management of parts in a single software environment for HP 3D Printing solutions, avoidance of costly and time consuming data conversions and third-party tolls, and the improvement of overall design to finished part workflow efficiency. It also includes functionality for build tray preparation and 3D nesting of parts allowing optimization of the economics of a print session by nesting as many parts as possible into the build chamber.
The new software model will enable NX customers to combine design, optimization, simulation, preparation of print jobs, and inspection processes for HP Multi Jet Fusion 3D printed parts in a managed environment. NX users can now load multiple 3D part models auto nest and submit them (via integrated Materialise capabilities) to an HP 3D printer, all in a single NX environment and with a minimum of steps. The Siemens NX and HP Multi Jet Fusion integration also eliminates the need for data conversion between software applications or process steps and, in the future, is intended to allow unprecedented control, including material characteristics down to the individual voxel-level. This will result in the ability to print parts with variable textures, density, strength and friction, and thermal, electrical, and conductivity characteristics.
Watch the video, “Siemens NX AM for HP Multi Jet Fusion 3D printers – Advancing 3D printing for industrial production,” for a sneak peak at our newest module.
In the past year, we’ve talked a lot about shifting mindsets, overcoming barriers, and having the right tools and printing technologies to achieve the vision to industrialize AM. When we change mindsets and breakdown barriers — such as conventional thinking, uncontrolled workflows, and disconnect process chains — that are prohibiting organizations from incorporating AM into their mainstream product development and production operations, it unlocks tremendous business value. But we’re not all talk. Siemens PLM has made significant strides in one year to deliver on our vision.
In October 2016 we introduced a new comprehensive solution to unleash the full potential of the burgeoning additive manufacturing revolution. The solution is comprised of integrated design, simulation, digital manufacturing, data and process management software. The set of offerings helps companies fully leverage the benefits of the latest additive manufacturing technology.
At the time, I stated that in order to transition AM to an industrial production process, it must have digital integration between design, engineering, print preparation, production and automation, and include control and monitoring of machine performance. To accomplish this we combined Siemen’s NX software, Simcenter simulation software and test solutions, Teamcenter, and elements of our Manufacturing Operations Management (MOM) portfolio for manufacturing automation. Our integrated system uses smart product models without the need for data conversion between applications and processes giving users a more effective way to reimagine product design, re-engineer parts with increased strength/weigh ratios, apply advanced integrated simulation and analysis to predict design performance, prepare the print process for the selected device and manage the entire process from design to 3D printed finished part. Our system now drives the widest range of production 3D printing technologies.
In the past 12 months we’ve also delivered a baseline of eight new NX based Additive Manufacturing software modules. Our customers now have access to AM modules for AM design, lattice design, topology optimization, NASTRAN optimization, simulation, and printing–including build tray configuration, support structures and nesting (2D+3D). We’re working closely on many AM projects with NX customers to integrate modules designed for their businesses. To support the projects, we’ve launched significant AM training within Siemens PLM as demand continues.
In April 2017, we shared our plan to create a digital global part manufacturing collaboration platform designed to bring on-demand product design and 3D printing production to the AM industry. Siemens is developing a digital part manufacturing platform connecting all members of the global manufacturing community to maximize resource utilization, grow expertise and expand business opportunity. We are creating the platform because part buyers need to connect to qualified manufacturers offering the latest digital and industrial 3D printing technologies and expertise. At the same time, highly skilled manufacturers need to create a pipeline of job orders for next generation designs that lend themselves to industrial additive manufacturing. We have enjoyed overwhelming support from the industry to develop and grow the platform. Together with our AM partner ecosystem, we are revolutionizing what is possible.
The AM advancements made in the past 12 months are just the beginning. Stay tuned, as there are more innovative software solutions to be created and more part manufacturing platform partners to bring into the fold.
You can read the announcement press release here.
Siemens NX users can maximize the number of prints to be executed within the HP Multi Jet Fusion 3D printer build volume by loading multiple 3D part models into NX, and then auto nesting and submitting them (powered by integrated Materialise capabilities) directly to the HP 3D printer