Make parts, not files: reinventing part manufacturing [VIDEO]
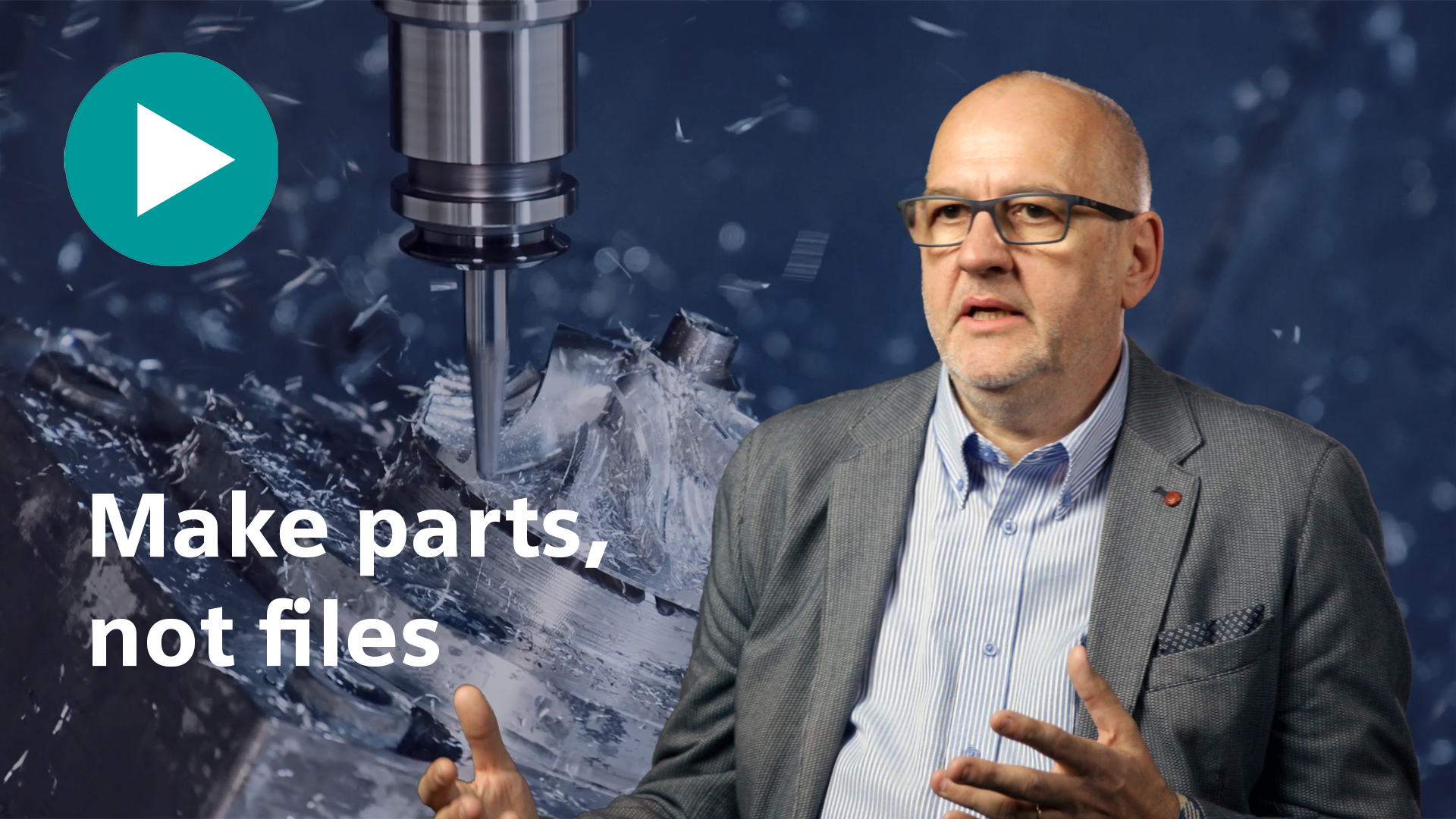
Part manufacturer’s success hinges on efficiency, precision, and flexibility — delivering high-quality parts on time while minimizing costs and adapting to evolving customer needs. To stay competitive, manufacturers are turning to next-generation technologies like artificial intelligence (AI), cloud platforms, and digital twin solutions, which help streamline processes, reduce errors, and enable smarter, more efficient operations. Armin Grunewald, Siemens Vice President Part Manufacturing Business Line, shares his insights into how these advanced technologies are enabling manufacturers to navigate complexity, embrace innovation, and deliver exceptional results.
Part manufacturers are at a crossroads today – workforce shortages, increasing complexity, competitive pressures, supply chain disruptions, and rising demands for quality and sustainability are reshaping the industry. These market challenges encourage manufacturers to rethink their traditional processes and adopt innovative solutions that can drive efficiency and resilience. Labor cost competition is now compounded by workforce shortages as an aging population retires, leaving a gap that must be filled by a younger, tech-savvy generation. “We need young, fresh engineers,” Grunewald explains, emphasizing the importance of tools designed for intuitive use. Siemens focus is on tailoring solutions to meet the diverse needs of operators, engineers, and NC programmers, creating a connected, user-friendly experience. This approach allows manufacturers to thrive in a landscape that demands adaptability and efficiency.
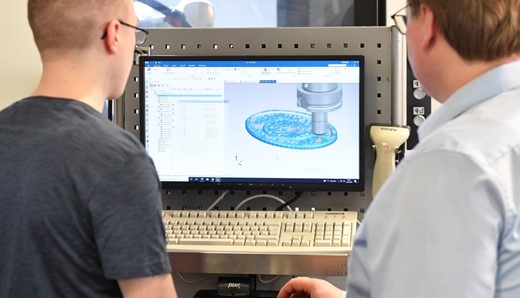
Reinventing part manufacturing with today’s market trends
Today’s trends like globalization, distributed supply chains, and heightened customer expectations force manufacturers to leverage digital solutions to dramatically accelerate the production of parts of any complexity to stay competitive. Siemens is at the forefront of this shift, offering integrated solutions that streamline processes, enhance collaboration, and drive productivity using the end-to-end NX for Manufacturing solution complemented by other advanced technologies like cloud and AI. To effectively manufacture new generations of components that the market needs today, new innovative technologies are necessary.
“We Siemens have a unique position. We have the software, the digital side of the digital twin and we have the physical side in the same house. So nobody else can connect a machine, a machine tool, a controller to the virtual world like we can.”
Armin Gruenewald, Vice President Part Manufacturing Business Line, Siemens Digital Industries Software
Decoding digital threads
The digital thread is essential for overcoming the complexity of modern manufacturing. By connecting data across the entire value chain, it ensures seamless integration from design to production. Grunewald explains how the digital thread isn’t just about data flow; it’s about optimizing the user experience. Whether it’s a shop floor operator or an engineer, every user interacts with tailored tools that streamline workflows. This holistic approach eliminates the silos that often slow down manufacturing, creating a cohesive and efficient ecosystem.
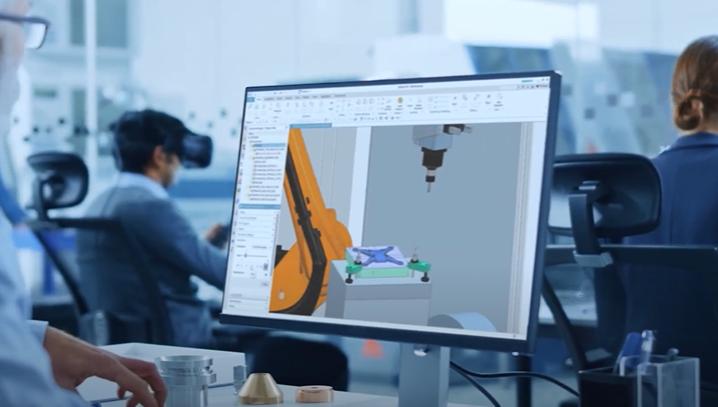
Innovating with industrial AI
Grunewald mentions how we use AI in our daily lives so why not using these technologies in engineering tools? AI is taking this evolution further, making NC programming smarter and more adaptive. Siemens integrates AI into engineering tools like NX CAM software to provide intelligent suggestions, predict costs, and remember user preferences.
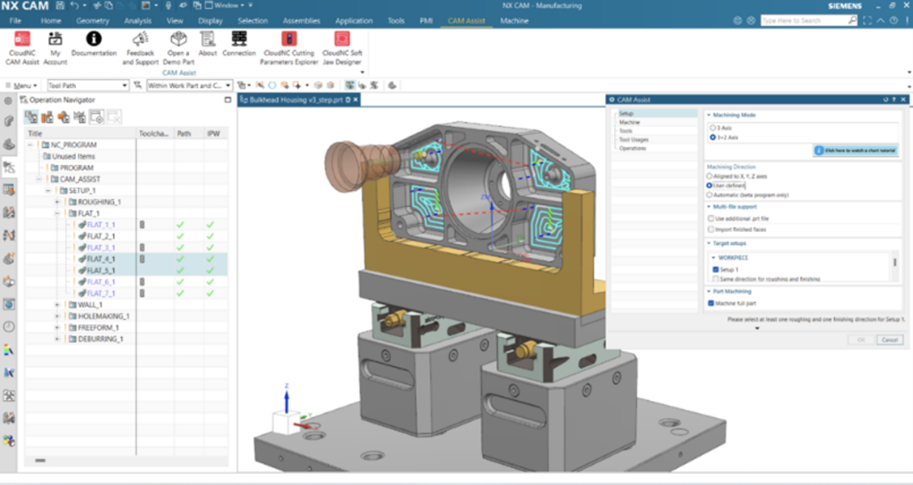
For example, Siemens is excited to recently introduce the integration of CloudNC’s CAM Assist solution, an AI-powered add-on, now available in Siemens NX CAM software. At the core of this partnership with CloudNC is the enhanced productivity AI brings to CNC programming. CAM Assist, helps automate the creation of 3 and 3+2 axis CNC, drastically cutting programming time from hours to minutes or seconds. AI CNC is especially important for industries like aerospace, automotive, and industrial machinery, where fast and accurate CNC programming is essential to maintaining tight production schedules and efficiency. As Grunewald explains, “AI and machine learning simplify processes and make tools smarter,” ensuring that manufacturers can adapt and excel in an increasingly competitive environment.
Simplifying manufacturing with the cloud
The cloud is also transforming how manufacturers collaborate and operate. By enabling access to data anytime, anywhere, the cloud fosters flexibility and responsiveness. It also facilitates seamless collaboration between suppliers and partners, ensuring that distributed teams can work together effortlessly. Beyond collaboration, the cloud simplifies application deployment and purchasing, allowing manufacturers to implement solutions faster and at scale. These capabilities are critical for adapting to the dynamic demands of today’s market.
For example, we are thrilled to recently introduce NX X Manufacturing, a powerful software-as-a-service (SaaS) solution, that combines industry-leading computer-aided design and manufacturing (CAD/CAM) with the flexibility, security, and scalability of cloud technologies. NX X Manufacturing offers three distinct product tiers including Standard, Advanced and Premium, each designed to address varying levels of part manufacturing complexity and specific production needs.
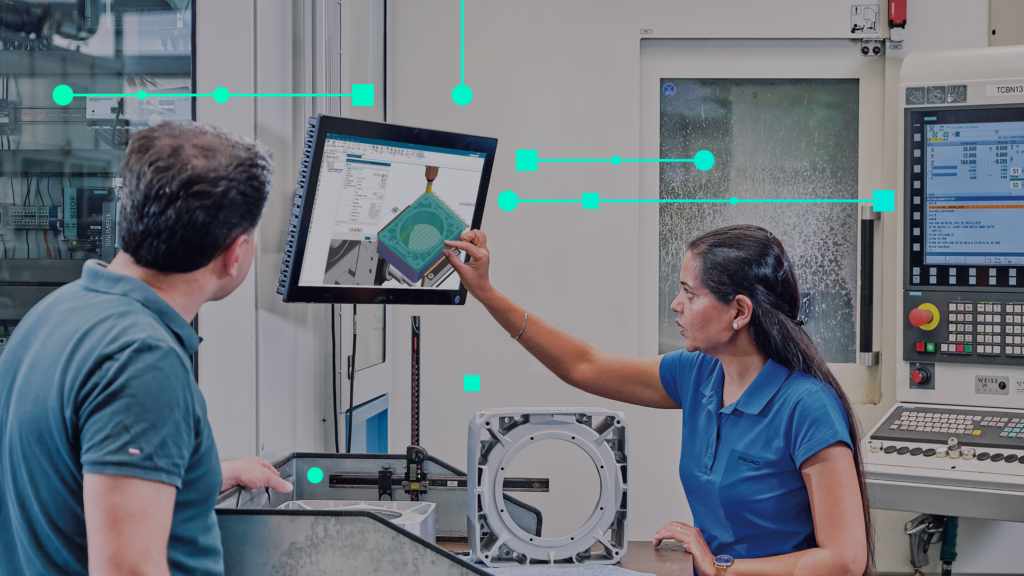
Discovering the most comprehensive digital twin
Siemens digital twin technology sets a new standard for integrating the virtual and physical worlds. By connecting machine tools with digital simulations, Siemens enables manufacturers to design and manufacture parts with unparalleled precision. This integration ensures that manufacturing processes align perfectly with machine capabilities, eliminating costly errors and reducing setup time. Grunewald proudly states, “We have the coolest digital twin on the planet,” reflecting Siemens unique ability to bridge the gap between design and production with advanced CAD/CAM capabilities.
The digital twin of the part model enables manufacturers to simulate the machining processes for optimization and error-free production on the shop floor. Using the comprehensive digital twin of the parts, resources and systems, you can drive highly efficient production processes while maintaining flexibility to quickly react to any necessary changes and eliminate disruptions to your process.
Through the combined power of digital threads, AI, cloud technologies, and the digital twin, Siemens is equipping manufacturers to overcome their most pressing challenges. These innovations are paving the way for a smarter, more sustainable future, ensuring that manufacturers can focus on what truly matters: making exceptional parts, not just files.