Features or Direct Modeling- Which is Better for Mold and Tool Design?
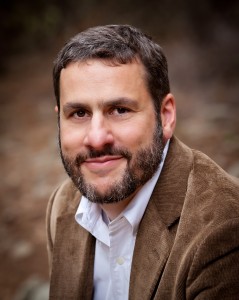
This blog post has been licensed for hosting by Siemens PLM. The concepts, ideas and positions of this post have been developed independently by Industry Analyst Chad Jackson of Lifecycle Insights. © LC Insights LLC
Do you remember when 3D solid modeling hit the market? I guess it started a little over 15 years ago. You had parameters that would drive changes in features that would, in turn, manipulate product geometry. Drawings updated automatically. It was pretty amazing at the time.
Now, do you remember when the movement came to mold and tool design? The picture painted back then was equally amazing. Apply some global shrinkage or other tweaks, subtract the product geometry to create the cavity and crack that mold. Presto: you were done.
Only, it didn’t quite work out that way. The tweaks were always a good bit more complicated than that. Many other manufacturability issues had to be taken into account. It was an improvement. Absolutely. But it wasn’t magic like the way it was painted.
Fast forward to today, and findings from the 3D Collaboration and Interoperability study show that 75% of respondents use 3D models to design mold and tooling. But when it comes to actually designing molds and tooling, which is better? Feature-based history approaches or direct modeling? Let’s discuss.
The Ease and Freedom of Direct Modeling
Let’s start with the easy argument. If something needs to be tweaked, either with product or tooling geometry, why should you have to create a feature to do it? Once you start creating features, you start creating interrelationships and constraints that can lead to feature failures. And those can add sorts of delays into your process.
Direct modeling offers an easy way to make changes to any geometry. You just select it and push, pull, drag, rotate or otherwise tweak it with some controls. Those changes aren’t remembered. They aren’t codified. They don’t create interrelationships. Make the change and move on. There are certainly advantages to that in today’s short schedule world.
The Automation of Feature-Based History
However, designing mold and die tooling isn’t all clean sheet, start from scratch work. In fact, a good part of it is highly repeatable, especially if you’re trying to apply some lessons learned to the effort. That goes for cooling lines, ejector pins, mold bases and more. Why would you want to size and tweak all of those for every single project when the rules about fitting them to your tooling is already well known?
Well, that’s where features and the history-based approach to building models is beneficial. They are intelligent in that interrelationships and external references let a feature-based model react intelligently to new inputs. All that sizing work can be automated dramatically. And that, too, is advantageous in today’s short schedule world.
Which is Best?
I have to admit at this point that this question hints at a false conclusion. One that is pretty prevalent in the industry today. And that false conclusion is that you have to choose one modeling approach or the other. So my advice is simple.
Don’t compromise. Don’t settle.
Carefully investigate CAD software applications to answer a very specific question: can you use feature-based history and direct modeling approaches at the same time? You will, of course, find almost every CAD software application today offers both of these capabilities. However, they are often offered in separate modes, between which you switch. The problem is that sometimes, you need the intelligence of reference-based feature history modeling while you are dragging mold and die geometry around. As you drag the mold block surface to increase its size, the mold base, cooling lines and ejector pins should move with it. And that’s just one example. Plenty more exist.
Summary and Conclusion
Let’s recap.
- Findings from the 3D Collaboration and Interoperability study show us that 75% of organizations are using 3D models to design mold and tooling.
- Direct modeling approaches enable quick and easy changes to mold and tooling geometry without the need to create features, and the failure inducing interrelationships that come with them.
- Feature-based history approaches enable automation for highly repeatable tasks such as running cooling lines, placing ejector pins and sizing mold bases.
- Both modeling approaches are highly applicable to mold and die design.
- Don’t compromise. Don’t settle. Carefully investigate CAD software applications to answer a very specific question: can you use feature-based history and direct modeling approaches at the same time?
That’s my take. What do you think? Sound off and let us know how these two modeling approaches fit in with mold and die design.
Take care. Talk soon. And thanks for reading.
About the Author
Chad Jackson is the President and Principal Analyst of Lifecycle Insights, a research and advisory firm that assesses the business impact of software applications and systems on engineering organizations. Chad has more than 15 years of experience with CAD, CAE, PDM, PLM and related technologies as part of the analyst community and software industry. Due to his industry knowledge and thought leadership, Chad is a sought-after expert, author and speaker that has advised, published and presented dozens of times domestically and internationally.