Growing capacity without expanding footprint [ARTICLE]
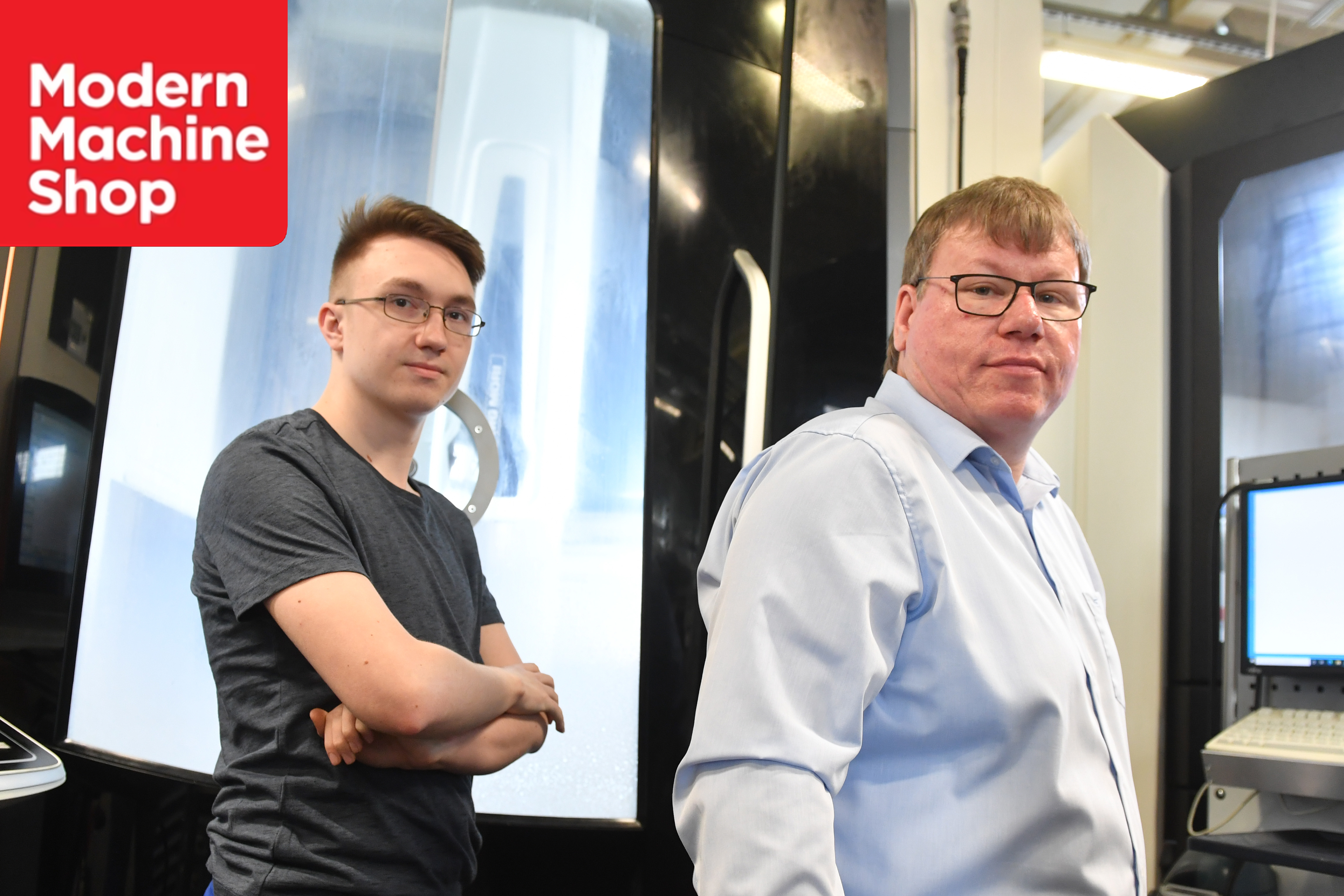
How do you grow your business when you can no longer physically expand your shop floor? This is the challenge that W.A. Pfeiffer, manufacturer of precision components for a wide variety of applications, was faced with. In a recent article titled “How this Job Shop Grew Capacity Without Expanding Footprint”, Modern Machine Shop talks about how this fairly small company with only 25 employees and 16 CNC machines was able to significantly increase throughput and compete globally through their mastery of digital production technologies.
To take on this challenge, W.A. Pfeiffer leveraged the digital manufacturing capabilities of Siemens Xcelerator to transform their job shop, starting with PLM. While PLM software is usually associated with managing product design data for design and engineering in large enterprises, it is playing an increasingly significant role in providing product and manufacturing information for process planning and execution on the shop floor, even for small part manufacturers such as W.A. Pfeiffer. They use Teamcenter to serve as the backbone of their entire digital manufacturing system. Company CEO Andreas Pfeiffer says, “The goal is to achieve higher production automation and end-to-end connectivity so that we can reduce set-up times and minimize throughput times.”

From there, all the design data is seamlessly exported into NX CAD/CAM, the shop’s system for CNC programming, which plays important roles in several ways:
- Comprehensive capabilities allow Pfeiffer to use one CAM system to program all their CNC machines (vs. multiple CAM systems for different machines or applications).
- The “digital twin” technology enables programmers to program in the context of the machine, generating intelligent toolpaths that can avoid obstacles.
- Modern and automated programming techniques enable Pfeiffer to speed up toolpath generation and standardize processes.
- Integrated CAD tools are used to prepare part geometry for machining and define the setup assembly (vs. using a standalone, disconnected CAD system).
- Associativity between the machining operations and 3D part geometry provides greater flexibility to implement design or process changes.
NX CAM software helps W.A. Pfeiffer improve productivity in both planning and production. CNC programmers can save time and reuse proven processes through automated programming techniques. NX’s advanced capabilities allow engineers to generate machine-specific NC programs using cloud-based postprocessing, and thanks to the G-code-driven simulation in NX, they can evaluate and optimize the processes before transferring them to production, saving setup time and increasing machine uptime. Pfeiffer was able to reduce cycle times by 25% while extending tool life by creating innovative high-speed machining strategies and optimizing toolpaths, resulting in fewer cutting passes.
Additionally, they use Opcenter APS for precise scheduling and Mcenter for tool management, CNC program management, and OEE analysis. The article concludes: “By using the digital manufacturing capabilities of Siemens Xcelerator, W.A. Pfeiffer transformed their operation, manufacturing high-quality products and continuously growing the business, despite the highly competitive global market. Customer and supplier relations have significantly advanced, and internal collaboration is better streamlined by using this suite of software solutions.”
You can read the full article at MMS online or in the PDF below.